Sidetracking, the long-proven technique of setting a whipstock to exit an original wellbore to tap an alternate production zone or bypass a downhole obstruction, is relying on digital technology to enhance performance in increasingly challenging formations and complex well trajectories.
Combined with advances in whipstock and milling technologies, the digital component is enabling operators to plan and conduct sidetracking operations with greater flexibility, precision, and efficiency—important objectives considering the variety of scenarios where the procedure is used. In open holes where toolstring failures have occurred, whipstocks, often are set to sidetrack around a lost bottomhole assembly (BHA) to recover the drilling program.
In cased holes experiencing reservoir depletion, a whipstock system can perform a slot recovery, drilling ahead to a different part of the reservoir using as much of the original wellbore structure as possible. Sidetracking also enables slot recovery on offshore platforms, which are restricted by the number of well slots from which to drill. In tight unconventional reservoirs, whipstocks are set to sidetrack and build long laterals from a vertical wellbore. Multilateral wells, common in regions where surface infrastructure is restricted, feature as many as eight wells sidetracked from a single mother wellbore.
To meet the realities of 21st century hydrocarbon recovery, optimized tool design, robust materials, and pre-planning regimens that use the latest simulation and visualization software are now essential. The recently launched TrackMaster Select modular whipstock sidetracking system provides full-gauge windows for casing exit operations. The system features a single-piece mill engineered with an optimized cutting structure, replacing the random crushed carbide cutters with a cutting structure forged into the tool body. The structure incorporates individual cylindrical cutting inserts brazed onto the blade. The forged body design eliminates the welding process, putting far less heat into the tool and increasing mill fatigue life by about 30%.
The result is a stronger, faster, and more reliable sidetracking system that can perform challenging milling jobs involving heavy casing, high chrome content, and longer milling times in a single run. The modular system, which enables applications for single or multiple casing exits, openhole sidetracking for offshore extended windows and multilateral wells, was used to successfully perform a single-trip dual-casing exit operation in a carbonate field in the Middle East.
Digital Solutions for Planning, Modeling
The whipstock sidetracking system works in concert with the IDEAS integrated dynamic design and analysis platform, which provides 4D, time-based simulations that capture the entire drillstring and wellbore geometry to ensure precise modeling of cutting interfaces for drilling rock and milling metal. Whipstock retrievability is improved with an optimized hook slot location, while the new mill design preserves the thickness at the top of the whipstock for greater reliability.
The design and analysis platform offers a suite of solid mechanics and programs that reveal bit-to-rock and mill-to-metal interactions in a virtual environmental for real-time customization. Collaboration with the customer establishes baseline performance and goals and incorporates modeling from a variety of tools, including motors, mills, and pipe cuttings. Cutting interface data are attained from scrape and insert indentation tests conducted in the materials mechanics labs. Models are validated using theoretical calculations and commercial finite element packages. Pre-job planning with the platform has been shown to minimize doglegs and predict consistent well trajectory with 97–98% accuracy compared to actual results.
The whipstock sidetracking system is also supported by the DrillPlan coherent well construction planning solution, which enables optimization of the BHA model window geometry, and performs following string pass-through and milling simulations, along with bending stress and downhole dynamics analysis.
The planning solution integrates into one platform, three software services—the i-DRILL integrated dynamic system analysis service, which uses predictive modeling to minimize vibration and slip/stick and optimize BHA performance; the WhipSim whipstock simulation software to model the milling operation and window geometry and the Runner drillstring analysis program, which provides a model for analyzing surface parameters, torque-and-drag and settings operations for anchors and shear bolt activation, and real-time analysis of modeled vs. actual parameters. The comprehensive service maximizes overall well planning and provides the ability to make adjustments during the operation to ensure the exit widow expedites passage of the BHA.
Sidetracking Through Dual Casing
In 2017, Kuwait Oil Company (KOC) collaborated with Schlumberger to successfully plan, model, and deploy the modular whipstock sidetracking system as part of a slot recovery operation in the Raudhatain carbonate field of northern Kuwait. Sidetracking in the field is commonly used to improve production in old wells. Formation analysis, BHA analysis casing and centralizer placements, wellbore inclination, dogleg severity, and orientation are critical for ensuring a successful sidetracking job.
In this case, the operator needed to sidetrack through dual casing in an existing wellbore in a challenging, high-shock carbonate environment. Carbonate formations can be very damaging to mill systems, especially in situations with dual casing. Key objectives were to mill a high-quality, full-gauge window and exit two strings of casing with minimal shock and vibration in one trip. Window quality was especially critical for enabling subsequent BHAs to pass through without incurring costly and risky tripping operations.
The job involved sidetracking the existing wellbore drilled with 9 5/8-in. and 13 3/8-in. casing strings. During the planning phase, the BHA was modeled using a finite-element analysis (FEA)-based modeling system and the whipstock simulation software. The mill operation and cutting structure were modeled using the IDEAS platform to determine the configuration that would generate the least amount of vibration.
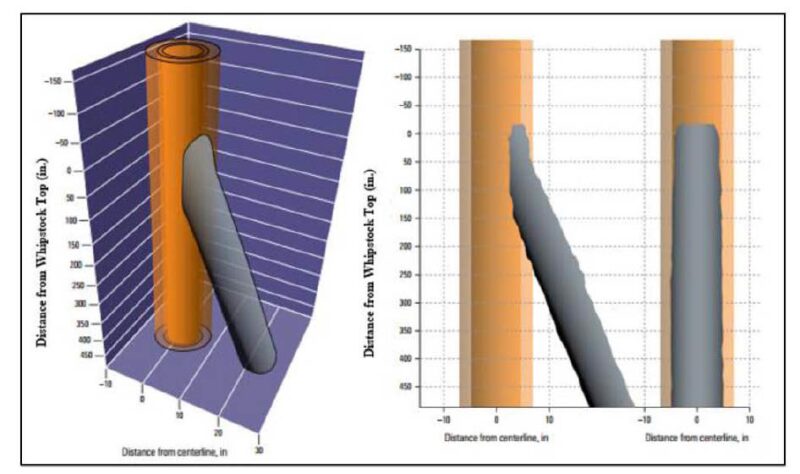
During the planning phase, several issues were evaluated, including the feasibility of using a bi-mill vs. a tri-mill BHA. The bi-mill BHA was eventually selected to mill the two casing strings at the whipstock setting depth. Placement of the centralizers and casing collars along the length of the casing at the kickoff point was analyzed to ensure the centralizers or casing collars were not inadvertently milled. The dimensions of the whipstock slide and mill position during the milling operators also were considered. Torque-and-drag was modeled before the job to verify that sufficient weight was available to shear the shear bolt. These analyses enabled the engineers to finalize a reliable parameter road map. The whipstock setting depth was determined by studying the exact points where the lead mill initiated the cut at each casing string.
The whipstock simulation software, which calculates dogleg severity for a liner or BHA pass-through as well as the stresses of the BHA, was used to check the bending moments, ensuring that the completion strings were not impacted by the dogleg across the whipstock. Engineers also reviewed the total cuttings volume generated from the milling operation. Cuttings were collected from the ditch magnets periodically throughout the operation so that the quality of the window could be evaluated by comparing the total volume of metal cuttings with the volume simulated using the whipstock simulation software.
Collaboration between the two companies ensured the challenging sidetracking job met the operator’s objectives efficiently and safely. For an operation that typically would be accomplished in two or three runs, the whipstock sidetracking system, enhanced with proactive planning, and modeling and simulation technologies, successfully performed the complex dual-casing sidetrack in a single run, significantly reducing time and cost. Planning using the design and analysis platform and whipstock simulation software were key to mitigating BHA shock loading. The project enhanced KOC’s confidence in the FEA platform’s ability to accurately identify the basis of damaging vibrations, paving the way to implement the approach in subsequent wells.