Automated real-time torque-and-drag (RT-T&D) analysis compares real-time measurements with evergreen models to monitor and manage downhole wellbore friction, improving drilling performance and safety. Enabling RT-T&D modeling with contextual well data, rig-state detection, and RT-interval event filters poses significant challenges. The complete paper presents a solution that integrates a physics-based T&D stiff/soft string model with a real-time drilling (RTD) analytics system using a custom-built extract, transform, and load (ETL) translator and digital-transformation applications to automate the T&D modeling work flow.
Methodology
A T&D representational state transfer (REST) application program interface (API) was integrated with an RTD analytics system capable of receiving and processing both real-time (hookload, torque, and rig-state) and digitized (drillstring and casing components, trajectory profiles, and mud-property) well data across multiple platforms. This strategy consists of four parts:
- Digital transformation apps, ETL, and translator
- Physics-based stiff/soft string T&D model API
- Pre-existing data infrastructure
- RTD analytics system
The data-flow architecture reveals a flexible design in the sense that it can accommodate different types of T&D models or any other physics-based REST API models (e.g., drillstring buckling or drilling hydraulics) and can be accessed offline for prejob/post-job planning.
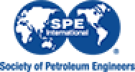