Several enhanced-oil-recovery (EOR) techniques (thermal methods in particular) are currently available to achieve higher recovery factors in heavy-oil fields. However, some technologies, such as downhole electrical heating (DHEH), have been improved recently, allowing enhancement of production and therefore improvement of the recovery factor with relatively low investment cost in comparison with the high costs involved in the implementation of thermal technologies. To increase the production of a heavy-oil reservoir offshore Congo, a study of DHEH applications has been carried out with encouraging results.
Introduction
The Zatchi Marine field, operated by Eni Congo in partnership with Total Congo, is located approximately 25 km from the Congolese coast (Fig. 1). It is a multilayered sand reservoir with five oil-bearing levels (A through E). In particular, Level B is a 30-m-thick sand characterized by a large accumulation of heavy and highly viscous oil with the presence of both a bottom and a gas cap and very low reservoir pressure. Water depth ranges from 55 to 57 m, and there is an areal extension of approximately 34 km2.
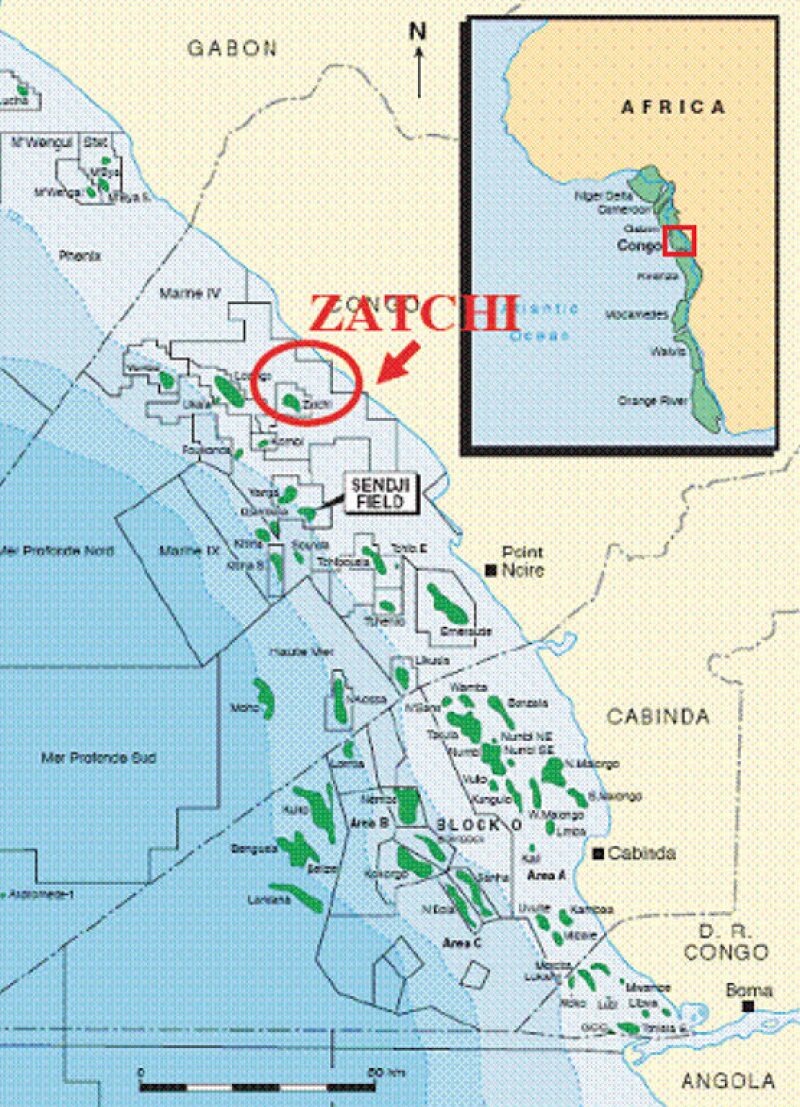
The development of the Zatchi B reservoir has always been an extreme challenge. Since the development of the field, six wells have been drilled and only three have been put into production, with sometimes unsatisfying results because of the severe problems of gas coning and cresting. An important improvement was achieved in 2008 with the drilling and completion of Well ZAM-408 ML, the first successful multilateral well ever drilled in West Africa and the first Technology Advancement of Multilaterals Level 6 technology applied in the Congo basin.
Following this important achievement and the growing interest in the various EOR techniques and development scenarios, a dedicated study was conducted by Eni to evaluate and assess the most suitable integrated technology applicable to the Zatchi B reservoir.
Reservoir simulations showed that among the different EOR techniques, thermal methods could enhance the recovery factor from this reservoir significantly. However, because the study is considering an offshore field (producing from a platform with very limited space and available power supply), and taking into account the heterogeneous reservoir environment, thermal methods were deemed to be too costly, with a high risk and a long-term implementation. Therefore, another technique was taken into consideration: cold production assisted by a DHEH system, which represents the edge between cold and hot production. DHEH allows production enhancement and thus improvement of recovery factor, with significantly lower investment costs when compared with those typically associated with the implementation of thermal technologies such as steam injection. This technology uses a three-phase system designed to provide a defined wattage according to the different applications and type of cables. The heater section is set downhole and is connected to the surface with a power cable. It generates heat to the near-wellbore region, decreasing viscosity and friction and, consequently, increasing oil mobility.
Reservoir
Zatchi B is a shallow reservoir [approximately 400-m true vertical depth (TVD)], characterized by a good porosity (greater than 30% in sandy facies) and permeability (in some areas higher than 1 darcy). Production started in 1988 and continues today from four levels (B through E). To date, almost all oil production has come from the C, D, and E layers through conventional development.
In 2006, the pilot project ZAM-408 ML began to evaluate the potential for multilateral technology in such reservoirs, and the well was drilled in 2007. Significantly important achievements have been reached with this well, which is still in production today: increased production, improved pump efficiency, and reduced gas-coning effect.
Given the successful results of Well ZAM-408 ML and considering the huge oil accumulation within the Zatchi B reservoir, the operator decided to explore alternative solutions in order to exploit the potential of this layer. Therefore, in 2009, a dedicated EOR study for Zatchi B was conducted and led to the execution of the DHEH pilot on a new well, ZAM 409. This well was designed as a horizontal well with 500 m of drain. The well design was quite challenging, considering the shallow target (400-m TVD) and the fact that an electrical submersible pump (ESP) had to be deployed.
The simulations showed that the DHEH cable will increase the temperature of the surrounding fluid and that the heat transferred will increase production as a function of reducing the viscosity and allowing the fluid to flow better. In addition to the improved flow conditions and as a result of the reduced viscosity, bottomhole heating has been reported to produce several benefits, such as less friction inside the production tubing above the pump. This allows the pump to work more efficiently, with lower backpressure. Case studies have demonstrated that formation heating stimulates the mobility of oil by the thermal expansion experienced by gaseous phases of crude. The heated oil liberates dissolved gases in the solution. This process forms a layer of gas that, when heated, will expand, pushing the fluid upward. Likewise, water, when present in a limited amount in the reservoir, will be converted to steam, which in turn expands and increases bottomhole pressure, also acting as a pushing agent.
It is important to note that flow rates have a significant impact on the temperature obtained. Oil that is static will absorb thermal energy, as opposed to oil that is moving away from the heat source. As a result, the higher the flow rate, the lower the amount of heat that is absorbed, and thus there is a smaller impact on production. The balance between heat input and oil produced is delicate.
Completion Design
The completion architecture was designed to accommodate the heater cable in the tail pipe deployed across the whole horizontal section. The tubing-string size was designed to be 3½ in. An ESP was designed to be set in a tangent section of the well. To monitor the temperature along the well (but especially across the horizontal section) and to carefully evaluate the increase in temperature caused by the startup of the heater, a downhole-temperature-sensing (DTS) system was deployed all along the well. To run and support the heater cable and DTS system in the openhole section, both were deployed and clamped to a tail pipe attached below the ESP. Special clamps and a midjoint have been designed and deployed along the depth of the completion. A chemical-injection mandrel (for antiemulsion and antiparaffinic purposes during production) and a tubing-retrievable, surface-controlled, subsurface safety valve were also part of the completion architecture.
A special tubing hanger and bonnet with additional passages have been designed for the specific project (Fig. 2).
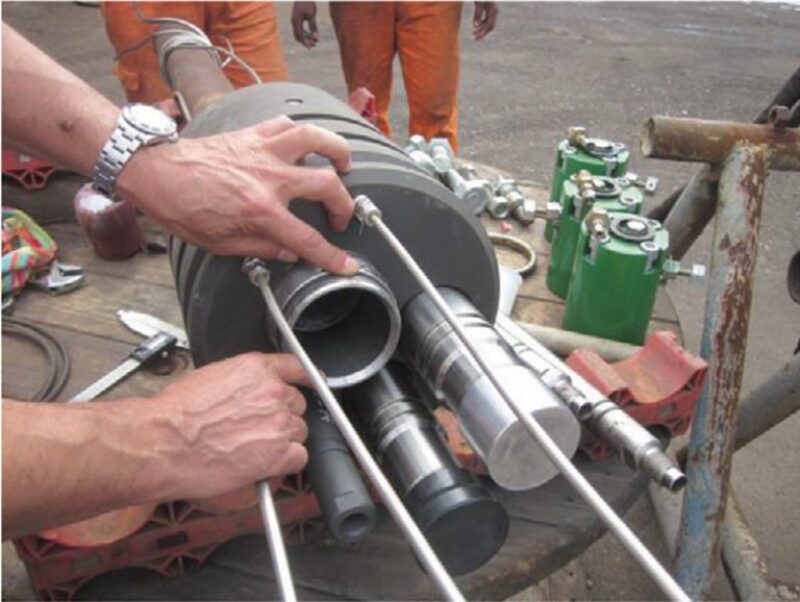
The total duration of the completion was 21 days. After the well cleanup and after a period of cold production, the downhole heater was switched on. The temperature rose to approximately 80°C uniformly along the whole horizontal drain in approximately 1 week. As a first result, the ESP performance improved, and the well is currently being monitored in order to evaluate the long-term benefits in terms of recovery.
For full details about the completion operation, please see the complete paper.
Lessons Learned
From an operational standpoint, many issues had to be faced with the splicing of the DTS fiber-optic cable, representing one of the weak points of the system. During equipment transportation on the rig, the connection between the DTS cable and tester box was damaged and the DTS specialist had to spend several hours correcting the problem.
While running the DTS system and the heater at the splice section, both splices slipped off with very low applied stress and had to be remade at the rigsite. Furthermore, DTS-system splicing requires the use of sulfuric acid and, during the run in hole of the 1⅔-in. tail pipe at 538-m measured depth, the high-temperature section of the DTS cable and the standard encapsulated DTS inline splice was broken. A delay of approximately 24 hours in restoring the splice (fusion splice) occurred because acid had to arrive at the rigsite from Pointe-Noire, Republic of the Congo. Furthermore, the conditions at the rigsite were not appropriate for a fusion splice (considering a limited space that was not clean enough for a very delicate operation).
One mitigation method is to limit the number of splices as much as possible (for example, only one section for the optical fiber, instead of two sections with different dimensions and ratings), and, in any case, it is necessary to know the maximum allowable tension that can be applied to the fiber-optic cable (to be included in the technical specifications). Even though the bottom-end 1⅔-in. tail pipe was strongly centralized, difficulties in passing through the hanger at 519-m depth were recorded. Several attempts to pass were made, but without success. Only when tubing was pulled up and rotated 90–180° was there a successful pass through the hanger section. Once free, the tubing was then reoriented to the original position. This operation had to be repeated several times, but no major problems were encountered. While running the completion string, all the electrical tests for the heater, the ESP cable, and the measurements on the DTS optical fiber were positive.
The major issue encountered during completion operations was related to a negative test registered while measuring the insulation resistance (IR) on the ESP cable immediately before startup of the pump. The IR during all the run-in-hole operations and after tree installation was higher than 1 GΩ, while before starting the ESP, it was measured at 15 kΩ (i.e., grounded). To find where the power-cable section was damaged, it was necessary to retrieve the completion and test the ESP power cable over its length until the ESP assembly was at surface. Finally, the damage was found to be at the -motor-lead-extension (MLE) cable insulation. The MLE cable and seal section were changed, and, because of the suspicion that the cable was damaged while passing a high dogleg-severity section, the ESP assembly was installed 60 m higher than the previous depth.
This article, written by JPT Technology Editor Chris Carpenter, contains highlights of paper IPTC 16858, “Downhole Electrical Heating for Heavy-Oil Enhanced Recovery: A Successful Application Offshore Congo,” by F. Bottazzi, C. Repetto, E. Tita, and G. Maugeri, Eni, prepared for the 2013 International Petroleum Technology Conference, Beijing, 26–28 March. The paper has not been peer reviewed.