Today, the industry faces tremendous challenges related to safety, efficiency, sustainability, and socioenvironmental responsibility. At every stage, well-construction projects must be concerned about those aspects to establish measurable barriers for preventing issues. Therefore, drilling and completion fluids are critical for achieving project goals and ensuring operations are executed as planned.
Drilling and completion fluid selection is a complex process in which addressing future downhole conditions for predicting potential problems is vital to eliminating nonproductive time. Conventional deep high-pressure/high-temperature wells in South sub-Andean Bolivia or unconventional long horizontal wells in Argentina are pushing drilling-fluid design to its limits with regard to keeping equivalent circulating density (ECD) as low as possible while preventing formation damage. Paper SPE 211539 describes several successful applications of low ECD organophilic clay-free inverted emulsion fluid in reaching project goals in challenging environments.
On the other hand, constant monitoring of drilling-fluid properties also is necessary. Fluid properties must be monitored so additives can be adjusted to prevent problems. Even though conventional monitoring relies on humans for performing periodic tests, recent technology developments offer a solution for complex drilling operations by allowing continuous real-time monitoring of drilling-fluid properties using sensors and artificial intelligence, as fully described in paper SPE 212443.
Finally, discussion of drilling and completion fluids must mention solids-control equipment. Ensuring that fluid properties are within acceptable ranges without discarding valuable additives is the main objective of any solids-control-equipment arrangement. Things become more complicated when working with low-density drilling fluids, where a comprehensive understanding of solids-removal techniques and their customization for a particular application requires research and laboratory-scale trials, which are rare in the literature. Paper SPE 212470 provides relevant and novel information through a full-scale test program for solids-control-equipment efficiency optimization focused on treating low-density muds.
This Month’s Technical Papers
Low-ECD Inverted Emulsion Fluid Shows Superior Performance
Method Provides Real-Time Anomaly Detection for Drilling-Fluid Properties
Light-Density Hollow-Glass-Beads Drilling Fluid Achieves High Solids-Control Efficiency
Recommended Additional Reading
SPE 211509 High-Fluid-Loss Squeeze and Reticulated Foam Lost-Circulation Material Plugs 40,000-Micron Laboratory Simulated Fracture/Vug Opening by Sharath Savari, Halliburton, et al.
SPE 214171 Using Cerium Oxide (6.0 SG) as Weighting Material in HT/HP Drilling Fluidsby Gholam Reza Soori, Cahya Mata Oiltools, et al.
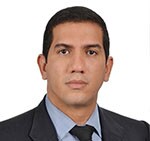
Víctor Soriano, SPE, is a senior well engineer working as a well construction manager at YPFB Chaco. He has more than 16 years of experience in complex onshore drilling, completions, and well-intervention operations. Soriano holds a BS degree in petroleum engineering from Universidad Nacional de Ingenieria, Peru, and an MS degree in petroleum engineering from the University of Oklahoma. He is currently pursuing his PhD degree in engineering at Pontificia Universidad Católica del Peru. Soriano is a registered professional engineer in Peru; a technical reviewer for several journals, including SPE Drilling & Completions; and a judge in the DrillBotics competition. He can be reached at victor.soriano@ypfbchaco.com.bo.