Oil wells can produce large volumes of oil, gas, water, and dubious data. For example, a recent study of data from 40 wells found that the measure of the weight on the bit (WOB) was off by 18% in the average well.
The big problem was that 69% of the time this key measure of the force applied while drilling was not recalibrated when the weight of the drillstring was increased as pipe was added, which is known as WOB zeroing.
Past technical papers on data quality focused on how data were measured, not on whether drillers were regularly zeroing, said Adam Neufeldt, a research engineer at Pason.
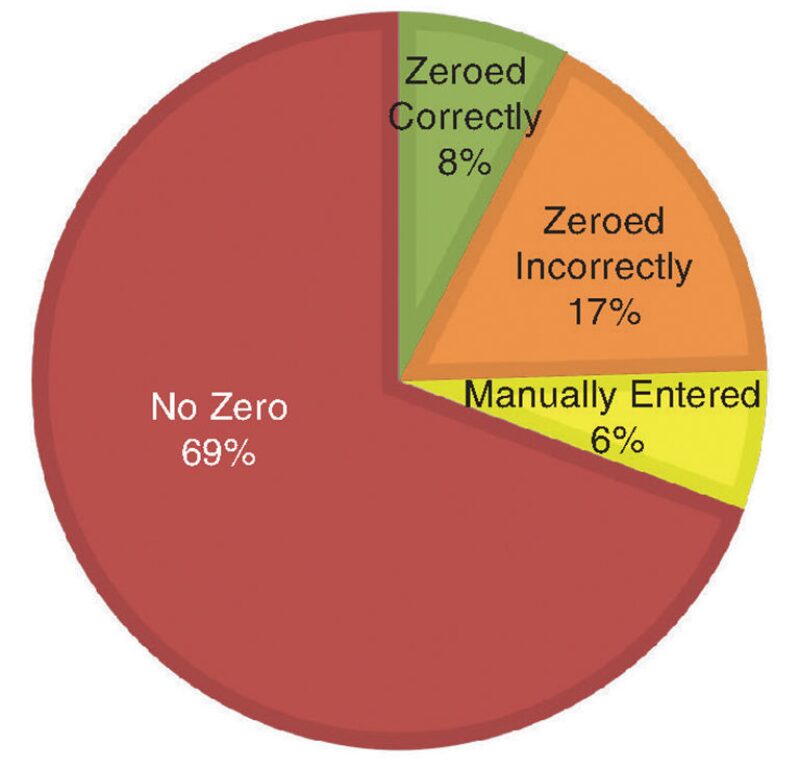
He delivered a paper (SPE 189636) at the recent IADC/SPE Drilling Conference where multiple papers were generated about the industry’s growing use of data for analysis and control, including some questioning data quality, which could undercut the value of analytics and automation.
The demand for better-quality data is rising as operators and service companies build systems to gather and analyze real-time drilling numbers. Representatives of Anadarko, Nabors Drilling, and Occidental all presented papers at the conference describing how they are expanding their ability to gather and analyze more drilling data faster to improve drilling performance.
“We have reached the tipping point on the use of this data,” Matt Isbell, drilling optimization advisor for Hess, said during a presentation at the drilling conference about the Operators Group on Data Quality, which was formed a couple of years ago to address the problem (SPE 189626).
“The errors are significant and there are huge consequences,” said John de Wardt, president of De Wardt & Co., who is leading an industry effort to create a roadmap for drilling automation systems development. He is working with Southwest Research Institute to develop a validation system to verify sensors and systems for drilling measurement.
The Pason paper looking at WOB data shined a light on the central role played by drillers. Errors in the drilling data recorder were likely caused by drillers failing to push the button on the recorder to zero the measure.
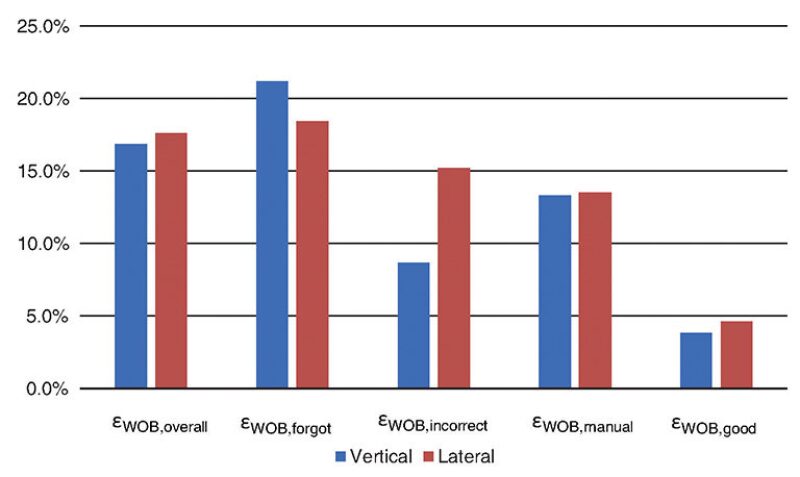
Several experts interviewed said that if an operation was progressing smoothly, the driller would likely keep an eye on the data but not feel a need to do the update, allowing the error to grow.
The study found a similar error rate in the estimates of the differential pressure that measures the force of the fluid flow driving the mud motor, which, like WOB, is used to measure the mechanical energy applied by the drill bit. Failure to regularly zero the differential pressure was a major source of error as well.
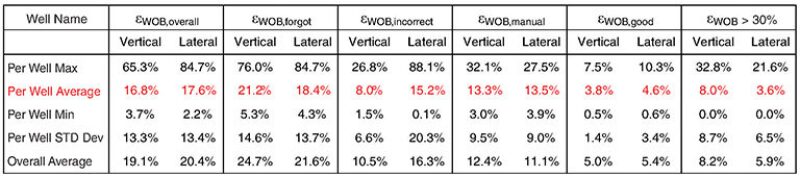
“The actual action of performing weight on bit and differential pressure zeroing does take time out of the work flow,” said Stephen Lai, manager of drilling systems group at Pason, a large maker of drilling data recorders. He said that “in terms of drilling speed, there may be a conscious decision not to do it on every stand if they are comfortable with what is going on.”
In well sections where WOB is a concern, Lai said zeroing “is more likely to be done in a disciplined manner.”
While the driller’s focus may be on other, more pressing matters, for those analyzing the data a number drifting off from accurate is a maddening error to fix. And bad data undercut the value of digital drilling controls.
“It is a really simple workflow. It just makes sense to automate. It is repetitive,” Lai said. Pason is developing software for its recorders that will automatically do this calculation after each stand of pipe is added using a new algorithm that also ensures the measurements are consistently made under the correct conditions. It plans to field test it later this year.
The fact that a driller failing to update a data recorder is a concern worthy of a technical paper and a software development project is an indication of how the growing use of data is changing the industry as leading-edge companies inject data and digital systems into the drilling process.
It used to be that the operator’s representative on the rig would tell the driller, “There is your bit, go run it, and do your best. This is a vastly different thing,” said Fred Dupriest, a Texas A&M University professor known for his work on driving drilling efficiency while at ExxonMobil.
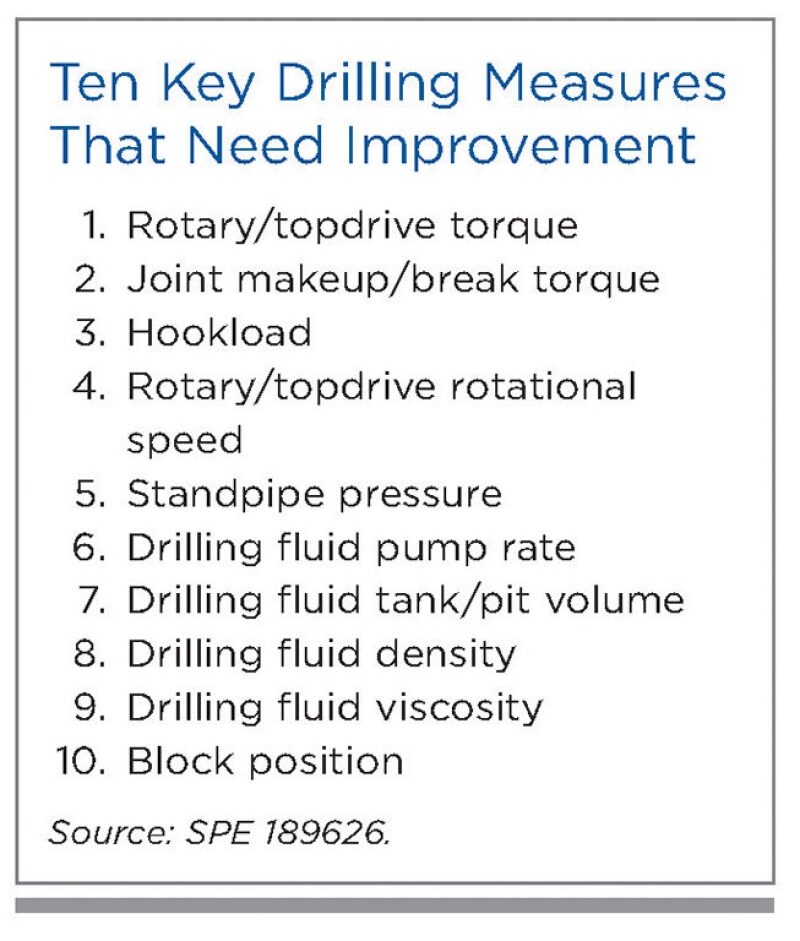
Based on his experience, he believes it is possible to deliver a large return on a significant investment in improved drilling techniques. But it requires a deep understanding of the physics and supporting data, as well as an answer to the question, “how does it make money?”
The flood of data and analysis will likely deliver a better understanding of drilling, but some early wins are needed.
“The real challenge right now is that a lot of people are spending a lot of money,” Dupriest said. “If the industry doesn’t start creating more actual value from analytics, they will stop spending that money, and the analytics industry will go away. You can point to a handful of companies that have a vision around this, but they are not adequate to create the size of market needed to sustain growth in analytics. I wouldn’t question the value, but the industry still does.”
Data Origins
The value of data-driven drilling analysis depends on the quality of the inputs.
“A real problem with data analytics is it is only as good as the data that is there,” said Michael Behounek, a senior drilling advisor for Apache, who was the lead author on the paper for the drilling data quality group. One of their challenges is persuading the industry to be more skeptical about its data.
“Unfortunately, now it is blind trust. They have no way of checking it. Once you have received a data set it is too late,” Behounek said, adding, “Today with all the data we get on a chart we assume it is right. There is probably some inaccuracy.”
There are easily observed errors, such as a sensor failure, but a lot of it is not so obvious. Some readings drift. The cause can range from sensors aging in a harsh environment to failing to zero the WOB.
Others are accurate readings from different points of view, like instant replays of a big moment in a televised sports game that offer different impressions of what happened depending on the angle and distance of the camera recording it. Most often, the WOB is measured at the deadline anchor, which moors the line to the drilling rig. It is not going to deliver the same weight as a sensor just below the topdrive.
Numbers also vary based on what is going on at the time. If a directional driller shifts from drilling ahead to sliding to change the well path, that will alter the WOB. “One of the biggest data quality issues may be the time stamp on the data,” Isbell said.
Anadarko’s project to quickly build a real-time drilling monitoring system (SPE 189595) encountered data streams lacking the tag identifying the well the data had come from, said Dingzhou Cao, staff data scientist for advanced analytics and emerging technologies at Anadarko.
Like Anadarko, the early adopters building these systems are putting a lot of energy into data quality. One large independent oil company told Jim Wicklund, managing director for energy research at Credit Suisse, “We are managing data we are not yet applying.”
The paper from the drilling data quality group highlighted 10 basic parameters needed for drilling control. Several are needed to consistently calculate WOB, particularly the hookload—the weight of the string of pipe used for drilling.
The weight of the string when it is off the bottom minus the weight when in contact with the rock face is a rough indication of the force applied during drilling. It is certainly not the only measure—the mud pump flow rate has a significant impact on the actual WOB—but can summarize the challenges faced by those looking for cost-effective, real-time measures to improve performance.
Computers running algorithms cannot deal with a range of data points for key measures such as the hookload and, while humans are better at dealing with ambiguity than machines, they would benefit from accurate measures.
“People on rigs have been dealing with ambiguity for all these years. We need to know what the hookload is,” Isbell said.
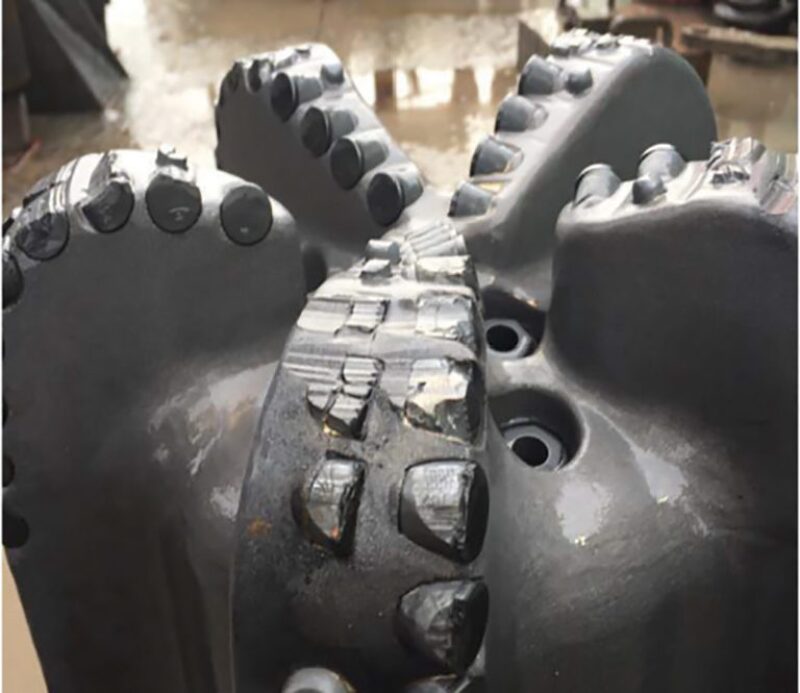
Data Accuracy
It is hard to argue against more accurate data, but there are plenty of questions about the cost of collecting it. Some operators who have asked service companies for data-gathering changes have been told, “That is going to be a higher cost and that is not in our contract,” Isbell said.
Better data are not going to be free. There are costs associated with change, from the time spent calibrating sensors to the expense of installing better instruments in strategic locations. While that investment can create a flow of data that can be used to improve performance using analytics and digital controls, those returns are harder to measure.
Behounek said they need to convince the industry that better data will be a “positive impact, not a cost impact.”
Changing how measurements are done will be a significant political challenge because exploration and production operations are so splintered. Operators pay the bills, but they depend on drillers to create the hole, with supplies and services from others, all of which have turf to defend.
Adding to the difficulty of getting comparable numbers is the fact that larger operators work with multiple contractors with varying types of rigs and ways of doing things. Even rigs operated by the same contractor likely include different components, potentially yielding different numbers.
The drilling data quality group is working on developing contracts with standard language setting out the data quality required, and ultimately wants industry standards on data quality. The group wants to ensure that no matter whose equipment and software is used, consistent measures are generated for analysis and digital controls. “We are trying to tell people we do not want multiple standards,” Behounek said.
Doing so will require agreements on which data are needed and how they should be collected. Automation and analytics require data that are reliable enough to allow comparisons over time and among wells, which is “better or at least appropriate data,” Isbell said.
“You could become over-prescriptive and with that comes cost,” he said. The group is working on developing an industry consensus to avoid a costly proliferation of data rules as each company goes its own way.
Based on papers at the drilling conference on how to better measure the WOB, they will need to balance the cost with the physics to get a good enough measure.
For example, hookload measurements are commonly made at the deadline anchor, which moors the drillstring to the deck of the drilling rig. This widely used method can lead to small errors that can stack up to a greater than 10% error compared to measures at the drillstring, according to the drilling data quality paper. Measurements made near the topdrive are more accurate but there is the added cost of the equipment needed to do it.
Those using the most common formula for measuring WOB—the weight of the drillstring when not drilling minus the weight when drilling—might find that the error is not significant.
“The absolute value of the hookload can be off by 30,000 lb, but the WOB is still right if the on-bottom and off-bottom hookload are both off by the same 30,000 lb, and that’s usually the case,” Dupriest said. “Systems like the autodriller don’t try to maintain constant hookload, they maintain constant differential hookload.”
But Dupriest acknowledges that while that formula is a useful approximation, the actual force applied by the bit is reduced by a variety of downhole factors including friction, long horizontal wellbores, and the makeup and flow of the drilling fluid.
“The actual WOB is not what the difference in hookload would suggest. It’s also complicated because as we increase WOB, the percentage loss increases,” Dupriest said.
A paper (SPE 189601) describing these factors in detail and offering formulas that could “substantially reduce” errors in weight on bit measurement was presented by Karl Erik Thoresen, senior development advisor at corporate R&D, NOV. It described WOB as “one of the most important controllable variables of the drilling process. Still, it is quite rare and very difficult to measure directly.”
Using its Novos system to automate zeroing, NOV has been gathering data from a test rig in Navasota, near Houston, equipped with sensors at the topdrive and downhole to get more accurate, calibrated measures of pressure and WOB to fine tune its WOB method, he said.
Pason opted for a simple approach that will automatically zero the WOB number after nearly every stand, reducing the average WOB error on those stands zeroed to less than 5%. It comes with the limits that come with surface measures. But by using software to automate the process, they are working to eliminate some of the variables by ensuring the measurement is done under consistent conditions to eliminate factors that can alter the WOB calculation, like whether the pumps are on and the drillstring is rotating.
“There is a need for accuracy with a pragmatic consideration of the cost. You cannot have a super-expensive rig in the field,” Lai said.
For Further Reading
SPE 189636 An Algorithm to Automatically Zero Weight on Bit and Differential Pressure and Resulting Improvements in Data Quality by A. Neufeldt, S. Lai, S. Kristjansson, Pason Systems.
SPE 189601 Improving Surface WOB Accuracy by Å. Kyllingstad, NOV, and K.E. Thoresen, NOV/NTNU.
SPE 189626 Operators’ Group, Rig Contractors, and OEM/Service Company Work to Solve Rig Data Quality Issues by M. Behounek, Apache Corp.; D. Nguyen, ConocoPhillips; S. Halloran, Ensign Energy Services; and M. Isbell, Hess Corp. et al.
SPE 189595 Rapid Development of Real-Time Drilling Analytics System by D. Cao, C. Loesel, and S. Paranji, Anadarko Petroleum Corporation.