Downhole drilling dynamics tools assist in understanding the downhole environment, providing a meaningful avenue for additional forms of optimization. Memory-mode logging tools, which can be run in various sizes of carrier subs to allow placement in several positions in the bottomhole assembly (BHA) or drillstring, provide a reasonably inexpensive opportunity for collecting downhole run data. This data, which includes rotations per minute (RPM), three-axis vibration, and temperature, among other variables, can then be analyzed post-run to develop a solution specific to the problems occurring. If drilling dysfunctions such as stick/slip or whirl exist, BHA configuration or drilling parameters can be adjusted accordingly to optimize performance and reduce well delivery costs.
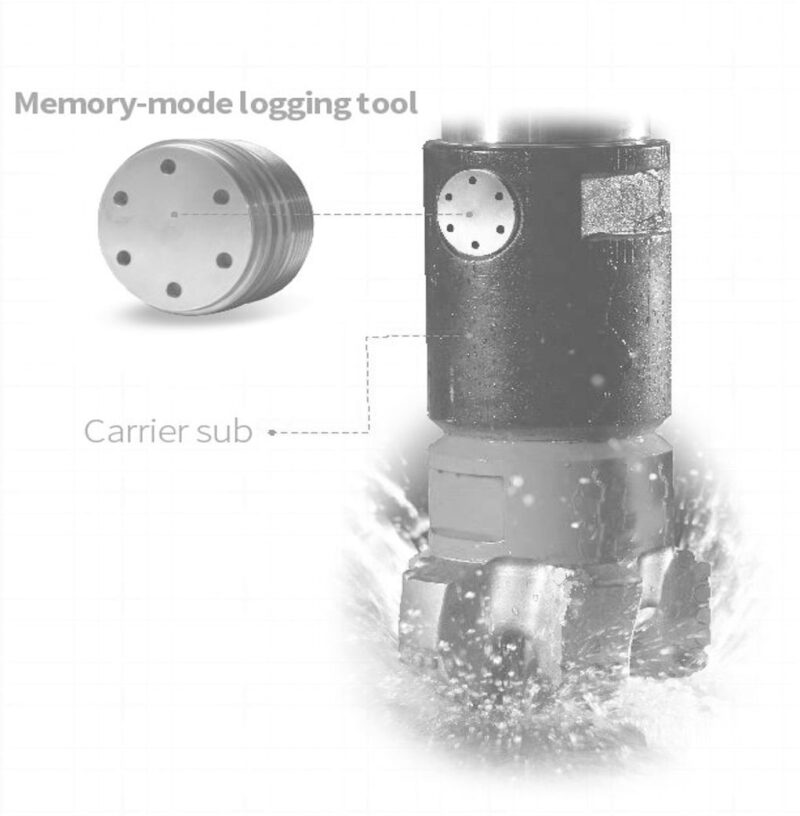
Using Downhole Data Analysis To Help Optimize Bit Selection
Downhole data could also reveal critical information about bit performance, and some memory-mode tools were invented precisely to help gather data that could help bit designers identify weaknesses in the design and improve them. A bit, for example, might not be perfectly tailored to a formation due to unforeseen lithological conditions, or there may be a need for a specific cutter layout to increase rate of penetration (ROP) in a particular section. While many times such considerations will have been dealt with ahead of drilling, there is often no way to account for the unknown.
In bit design there is a clear need for iterative product development, with each successive bit (and related cutter technologies) building upon the strengths and compensating for the weaknesses of their predecessors. By better understanding the downhole environment and how new, more challenging well types and paths impact performance, engineers will be able to develop more effective bit designs in the future.
Software and Downhole Tools: Overcoming the Limitations of Drill Bit Selection
When drill bit selection cannot fully deal with stick/slip or bit upgrades increase well costs too much, algorithmic software may be a worthy complement. One such drilling performance application uses automated vibration dampening to mitigate torsional vibration and reduce stick/slip oscillations during drilling operations. The software is activated on demand by the driller and prevents the fundamental frequency of torsional vibration from manifesting and becoming an excitation source for the drillstring. When using this software, the driller is shown the degree of stick/slip on his/her screen, and if the severity reaches a critical point, the system’s auto-tuning feature will enable the speed controller to provide optimal damping to mitigate stick/slip occurrences.
This approach overcomes the more traditional methods which usually require the driller to identify stick/slip occurrences and then manually manipulate the weight on bit (WOB) and RPM setpoints to overcome them. As with many improvements in the modern oil field, the software option seeks to overcome the limitations and inconsistencies of manual processes—a driller cannot accurately quantify stick/slip severity across a period while simultaneously optimizing drilling parameters. In addition, manual outcomes rely on individual driller skills, including how quickly he/she reacts to the drilling dysfunctions.
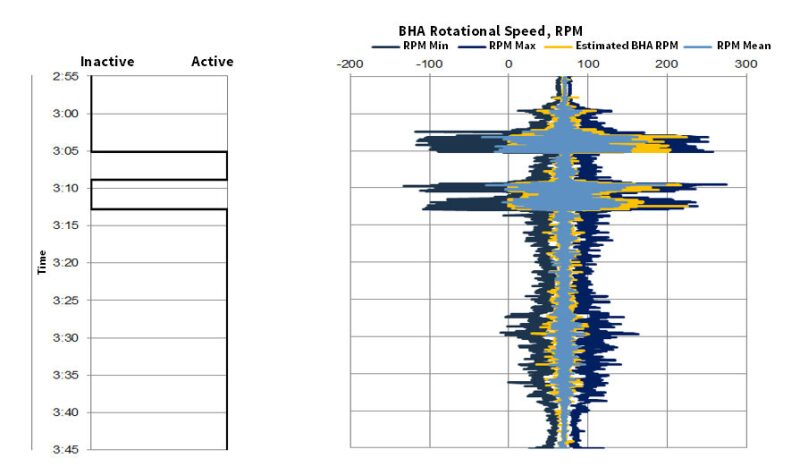
On the downhole side, tools can also be used to offset the limitations of drill bit design. One such tool can be placed above the measurement while drilling (MWD) or nonmagnetic portion of the BHA to prevent torque from shooting up the drillstring, helping to establish stable parameters. Drill bit design might incorporate torque arrestors and other similar features to keep vibration down and protect the drill bit, but such additions can cause ROP to suffer; this tool eliminates this concern and allows for more aggressive bit designs to be used. The possibility of cutter-induced stick/slip, which can occur in between other types of stick/slip, also presents a challenge, as it often cannot be overcome by conventional methods. The downhole tool takes this into account and, by design, allows the driller to expand the operational window of the drill bit to increase ROP without incurring stick/slip-related vibrations. It also attempts to provide steadier load when friction causes the WOB feed to become erratic.
While both the software- and tool-based solutions are viable, the major considerations in the current economic climate are cost and efficiency. It has generally been accepted that with the software option, the rental day rate is significantly lower than with a downhole tool, and using software eliminates the risk of equipment damage while downhole, lost-in-hole events, etc. The driller should weigh the options and determine an appropriate solution to meet the needs. Ultimately, the additional technology cannot, and should not, replace sound engineering practices in bit design, but rather should augment the performance of a well-designed bit/BHA.
Using downhole tools and technologies that complement good bit selection can help optimize drilling performance and reduce costs. Understanding the impact of all interrelated products and technologies and acting to optimize how they work together will make performance improvements across categories more pronounced. This will only become more important as the industry continues to seek efficiency and cost-effectiveness, and the need for profitability drives new development of integrated, automated systems.
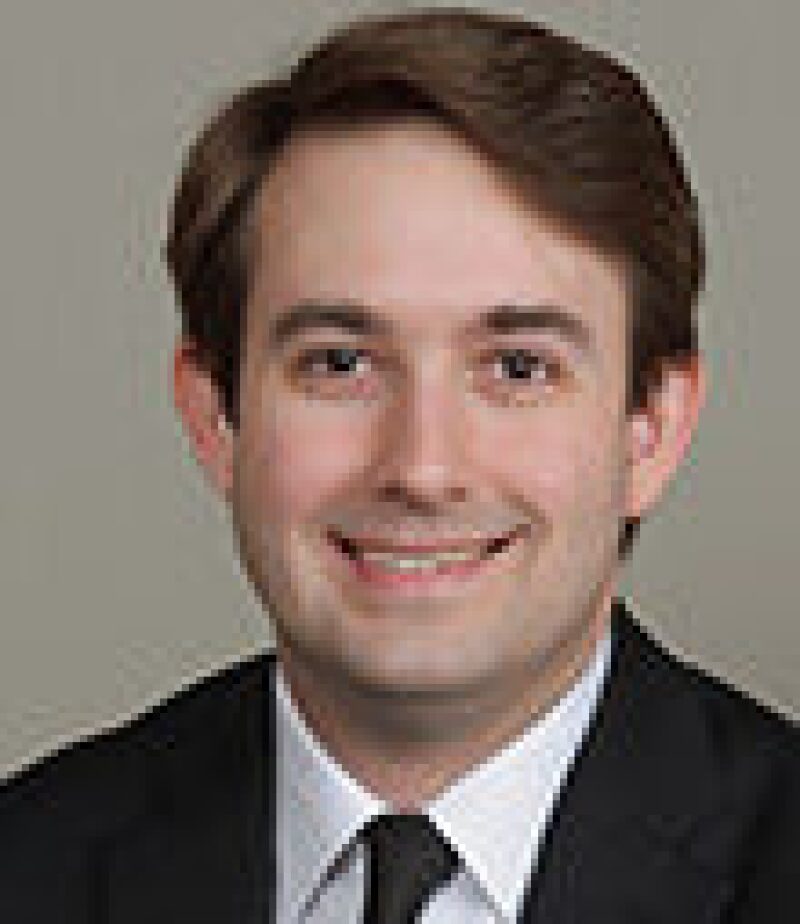
Stephen Forrester has worked at National Oilwell Varco (NOV) as a marketing/technical communications writer since 2014. His editorial interests at the company have largely centered on using surface and downhole data analytics to drive drilling optimization and closed-loop automation, though he is currently expanding his knowledge of additional product lines and technologies. Before joining NOV, Forrester worked at the oil and gas division of Lloyd’s Register as a technical editor of compliance inspection reports on subsea blow out preventors and related pressure-control equipment. He holds BA and MA degrees in English from the University of Houston and has been an SPE member for 2 years.