This paper shows how automation reduces invisible lost time and allows drillers to focus on other activities while repetitive tasks are controlled by software. An automated drilling-control system using advanced modeling of well conditions in the North Sea helped the rig save up to 10% of rig time per well through safeguarding and optimizing manual operations and automating repetitive activities such as tripping, pipe filling, connections, and pump startup.
Introduction
To explain why the real-time model-based automated system deployed on the rig was capable of saving up to 10% of rig time, the following factors must be considered:
- The effect that time and temperature have on drilling-fluid properties and thereby why conventional operations must be kept at a conservative level compared with automated operations tuned to current downhole conditions
- The reduction of invisible lost time and the realization of faster, smoother drilling operations with fewer unplanned drilling events, obtained through shorter connection times, automated pump startups and shutdowns, automated friction tests, and active (automated) safeguards and safety triggers that assist drillers during manual operations
- The human factors and team efforts to optimize operations further wherever possible
Drilling Fluid
Some of the main functions of the drilling fluid are to cool the drill bit; transport drill cuttings out of the wellbore; and maintain downhole pressures to avoid fluid influx or formation collapse, prevent fluid losses, and avoid formation fracturing.
Weighting material is added to the drilling fluid to adjust its density and thereby control downhole hydrostatic pressure. In order to keep the weighting materials and drill cuttings suspended in the drilling fluid whenever fluid circulation is stopped, drilling fluids also incorporate polymers or gelling materials. The drilling fluid is formulated to turn into a gel state within only a few seconds of fluid circulation stopping, after which the gel structure strengthens with time.
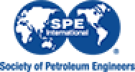