To accelerate learning, an operator deployed a real-time, closed-loop downhole automation system (DHAS) in conjunction with wired drillpipe in the 8¾-in.-hole section. The operator also used downhole memory tools in the 5⅞-in. lateral section to collect downhole drilling parameters and vibration data. The optimization process drew upon key elements from lean manufacturing concepts.
×
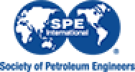
Continue Reading with SPE Membership
SPE Members: Please sign in at the top of the page for access to this member-exclusive content. If you are not a member and you find JPT content valuable, we encourage you to become a part of the SPE member community to gain full access.