This study investigates oil-production mechanisms from the matrix into the fracture by simulating two laboratory experiments as well as several field-scale studies and evaluates the potential of using carbon dioxide (CO2) huff ’n’ puff to enhance oil recovery in unconventional liquid reservoirs (ULRs) with nanodarcy-range matrix permeability and complex natural-fracture networks. This study explores the mechanisms contributing to oil recovery with numerical modeling of experimental work and investigates the effects of various parameters on oil recovery.
Introduction
CO2 injection has been recognized as one of the more important and successfully applied enhanced-oil-recovery (EOR) processes in the US since the start of the first commercial CO2-injection project in 1972. Statistics show that, out of the 153 active CO2 EOR projects worldwide, 139 of them are in the US. CO2 flooding is the only EOR method in the US that has been consistent and economical since the drop in oil prices in the 1980s. One of the main advantages of CO2 injection is that CO2 can achieve miscibility with the resident hydrocarbon when minimum miscibility pressure (MMP) is attained.
Although CO2 flooding has demonstrated the potential of increasing oil production in conventional reservoirs, if this EOR process were to be applied to ULRs, the oil-recovery mechanism could not be considered the same as that during a conventional CO2 flooding because of the differences in reservoir petrophysical properties, fluid-phase behavior, and the fundamental mass-transfer mechanisms.
In general, diffusion during gas injection has been recognized as a critical mechanism that affects the oil recovery in fractured reservoirs. If the diffusive flow in the matrix is being neglected during simulation, the calculated result will underestimate productivity.
Furthermore, complex fracture geometry has been proposed for hydraulic fracturing because of the intersection between hydraulic fractures and in-situ natural fractures.
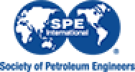