Fueled by a culture of innovation, hydraulic fracturing has transformed the energy landscape from inside North America out. But achieving that paradigm shift took years of improving subsurface understanding, technology development, and fine-tuning the completions practice through trial and error.
Authors from Liberty Oilfield Services set out to document this evolution in SPE 194345 as they took a deep dive into fracturing history. Their paper traces the advancements in fracturing study and deployment from its earliest days to the present.
Fracturing first took place in 1947 and has grown exponentially in uptake over the past 2 decades. The result has been the shale revolution, which has catapulted the US to at or near the top of the world in both crude oil and natural gas production.
Between 2000—just after fracturing pioneer Mitchell Energy began commercial shale production—and 2018, yearly US dry gas production went to 83 Bcf/D from 53 Bcf/D while US crude output climbed to just under 11 million B/D from 5.8 million B/D, according to data from the US Energy Information Administration. Once largely dependent on imports, the country has become a net gas exporter and oil exports are reaching new heights.
During that same period, increased fracturing intensity and a better knowledge of the subsurface complexities associated with the completions practice resulted in North American pressure pumping horsepower rising tenfold, yearly frac stage count growing twentyfold, and proppant mass pumped jumping fortyfold.
Since the turn of the millennium, “the difference has really become that we bring the frac down to the hydrocarbon molecule in the rock,” said Leen Weijers, vice president of engineering at Liberty Oilfield Services, at the recent SPE Hydraulic Fracturing Technology Conference in The Woodlands, Texas. “We do that with multistage horizontal wells and a focus on complexity, creating a plumbing system that is two miles long and maybe half-a-mile-wide and maybe 500 ft in height.”
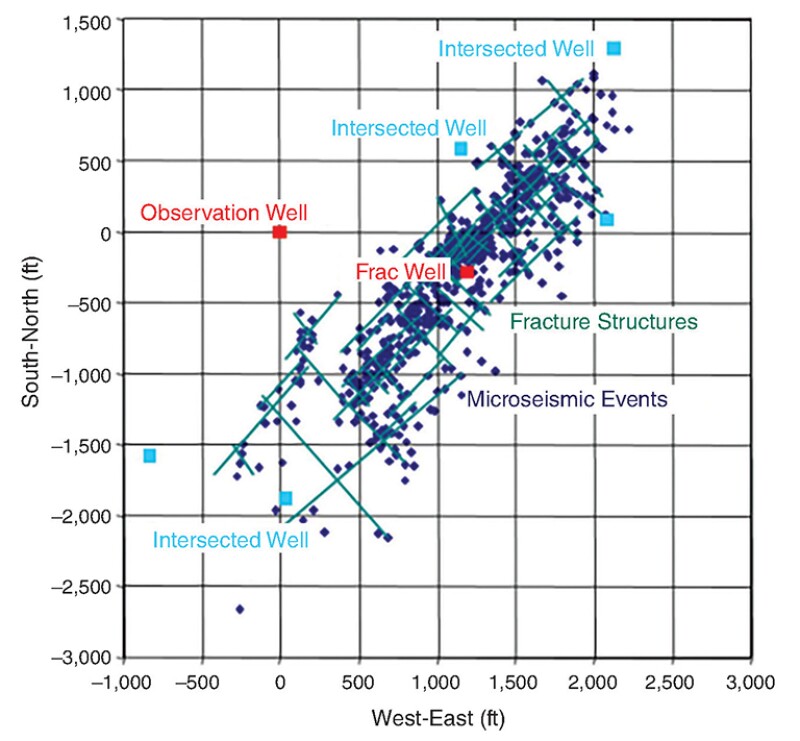
Background: Mineral Rights, Fracture Study
Weijers et al. first noted the importance of private mineral ownership in spurring unconventional development in the US. Mineral owners can develop, borrow against, or sell their land, meaning they have a direct stake in the high-risk, high-reward mineral development game. As the industry became more aware of the gas and oil recovery potential from shale, small independents began scooping up acreage, benefitting from their familiarity with the communities in which they operated or planned to operate.
A major step forward in understanding the subsurface impact of hydraulic fracturing, Weijers et al. said, came with the realization by Warpinski et al. (1991) that fractures are complex, with dozens of parallel fractures growing simultaneously during a job in a narrow, 20–40 ft‑wide zone. This dispelled the previous belief that simple bi-wing fractures extended from the wellbore, stimulating further study of fracture growth.
Fracture diagnostic tools such as tiltmeter fracture mapping and microseismic mapping were subsequently developed, providing fracture dimensions used to feed fracture propagation models, which improved fracture design. Work by Fisher et al. (2002) for the first time showed a widely complex fracture system with multidirectional fractures, creating a one-mile-long, 1,200-ft‑wide area that the authors called the fracture “fairway.”
Outsize Fracturing Treatments
In the meantime, operator experimentation with low-proppant slickwater fracs eventually led to Mitchell Energy “cracking the code” for commercial shale gas development in the Barnett Shale of north Texas, Weijers et al. said. Devon Energy acquired Mitchell Energy in 2002, combining the complex fracture strategy with multistage fracture treatments in horizontal wells.
Shale operators have since focused on creating larger, denser fracture fairways, though a recent trend toward capital discipline may be contributing to a moderation of some of the larger numbers below:
- Laterals lengthen to reach more rock and hydrocarbons. For example, in the Utica Shale of the Appalachia region, lateral lengths almost doubled to 8,628 ft during 2011–17, according to DrillingInfo data. In the Williston Basin, the average lateral now stretches more than 2 miles with a limited surface footprint thanks in part to North Dakota setting the standard drill spacing unit at 1,280 acres.
- Proppant and fluid volumes grow to new heights. During 2010–17, average proppant mass spiked to 1,600 lbs/ft from 500 lbs/ft, and fluid volumes increased to 33 bbl/ft from 13 bbl/ft. Operators are shattering basin records, Weijers et al. noted, with some wells taking in a proppant mass equivalent to a 100-car unit train, surpassing 20 million lbs/well. This has come with the increased use of high-viscosity friction reducers.
- Stage count and intensity boom. The average stage count has risen to 40 stages/well, with average stage spacing dropping to 200 ft/stage in 2017 from 350 ft/stage in 2010.
- Pump rates take off. The rate per lateral foot increased to 0.42 bpm/ft in 2017 from 0.16 bpm/ft in 2010 in an effort to improve diversion, accompanied by a rapid increase in frac fleet horsepower.
Not only is much more proppant being used in treatments, but the type of proppant has changed over the years. Operators have gone from using resin-coated sands and ceramics to lower-cost sands mined locally in-basin, a trend that began in the Permian, where operator Pioneer Natural Resources, for example, now has its own mines. Mesh size preference has moved to 40/70 mesh and then even smaller to more than 100 mesh.
Service firms have also become more skilled at repeated staging, which involves targeting fracture treatments at certain subsections of a lateral. Ball-and-sleeve tools enabled firms to shut access to a recently treated interval and move to the next stage. Aided by other wireline innovations, plug-and-perf tools have served as an efficient solution as multiwell pads became the norm.
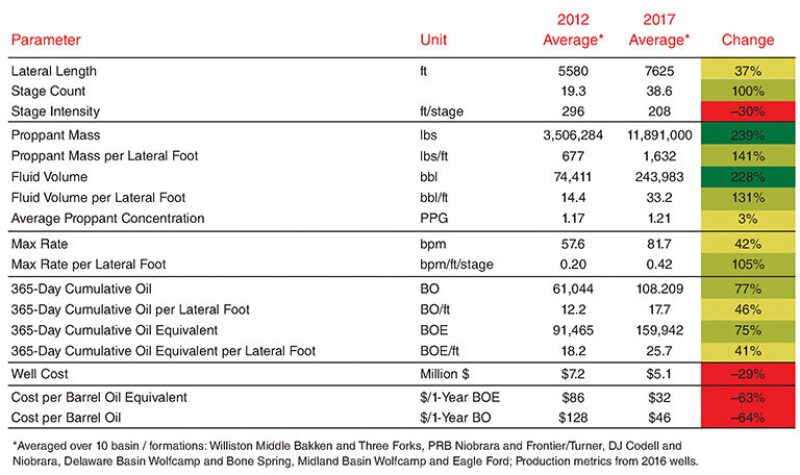
Efficiency Cuts Costs
While frac intensity has spiked and horizontal wellbores continue to stretch farther and farther, oilfield service firms and operators have managed to slash drilling and completions (D&C) costs to levels well-below those of earlier this decade, necessitated in part by the commodity price downturn of 2014–16. The downward shift in cost has helped sustain shale production as operators take a more conservative financial approach and prioritize free cash flow generation.
During the downturn, operators tweaked designs to incorporate cheaper sand and lower gel loadings with cheaper fluid systems. The impact on D&C spending was dramatic. Citing data from Coras Research, Weijers et al. noted that average well costs in four major US liquids-rich basins fell to $5.1 million in 2017 from $7.2 million in 2012. The average cost per barrel of oil produced—meaning all D&C costs for barrels in the first year of production—was just $46/bbl in 2017, compared with $128/bbl in 2012.
New fracturing strategies have been informed, in large part, by learnings taken from free-flowing data in the US. Much of D&C data reported by operators to state regulators are made public, allowing for firms to apply multi-variate analysis in their effort to find better ways to drill, complete, and produce their wells.
But perhaps the most basic way to control costs is to maintain uptime, which has been a primary directive to service companies by their operator clients since the downturn. The typical frac crew in the US spends about 25% of its time pumping, with some spending up to half their time pumping, Weijers et al. said.
Pumping companies are shedding downtime by ensuring equipment redundancies, which includes storing parts that are known to fail in a warehouse trailer; posting extra horsepower, blenders, and other critical equipment near the site; and furnishing blenders with a second discharge pump.
Reducing equipment degradation also has become a point of focus given the injection of high quantities of abrasive proppants alongside high-rate and slickwater jobs. Pumping companies, for example, are employing pressure monitoring to boost fluid-end life expectancy and provide targeted and timely valve and seat replacements.
With these changes for the better come even more room for growth, as operators and service companies continually raise the ceiling as to what can be accomplished with unconventional development and production.
The next set of challenges center on dealing with more crowded basins, interwell communication, and production declines while maintaining capital discipline given perpetually unpredictable commodity prices.
For a more complete picture of the evolution of hydraulic fracturing, read SPE 194345 by Weijers et al.