Earlier this year, one of the founders of Fervo Energy announced that the geothermal innovator had reached its “Mitchell moment.”
Jack Norbeck, chief technology officer for Fervo, likened a test where it used a pair of fractured wells to create water hot enough to generate electricity to the time when Mitchell Energy adopted slickwater fracturing to economically extract large amounts of gas from the ultratight rock in the Barnett Formation.
“We have derisked all those core challenges, we reached the Mitchell Energy moment for geothermal,” Norbeck said.
By doing all that and supplying 3.5 MW of electricity to the local grid that powers Google facilities, he announced that the firm’s enhanced geothermal system (EGS), had reached the highest level of technical readiness.
Now comes the hard part—proving that technical triumph can be turned into something really big.
The Mitchell moment in 1997 is remembered because it led to a series of innovations that allowed hydraulic fracturing and horizontal drilling to add enough oil and gas production to move global markets.
What has been learned about fracturing in the decades since allowed oil industry veterans at Fervo to effectively use those tools to do what others had failed to accomplish—create high-volume EGS capable of generating power.
One big difference between the moments is that Houston-based Fervo’s next step looks like a leap compared to Mitchell’s.
After Mitchell’s moment, no innovation was required to sell shale gas from the Barnett or find the oilfield services needed to develop and produce it. Plus, it could learn from the many other companies working in tight rock plays.
Its moment was the culmination of years of innovations by oil and service companies who continued finding ways to build on that advance. The endless arguments over who can claim credit for the innovations behind the Mitchell moment are evidence of the size of that support network.
Today, Fervo’s efforts are also supported by the oil industry’s service sector and supply chain.
Oil company Devon Energy, drilling contractor Helmerich & Payne, and pressure-pumping specialist Liberty Energy are among its early backers. And Fervo is benefiting from the government-funded research and site-evaluation work at the Utah Frontier Observatory for Research in Geothermal Energy (FORGE) site, which is the key site for geothermal testing funded by the US Department of Energy (DOE).
But unlike Mitchell, the path to commercial success will require Fervo and others to show they can create large operations to convert the heat they harvest into a cost-competitive commodity in a fast‑changing, highly competitive industry.
Sage Geosystems recently was added to the short list of geothermal startups with big projects, signing a deal with Meta to build a 150-MW plant somewhere east of the Rockies. Also high on the list is Eavor whose first commercial project will use its closed-loop heating technology for home heating and electric generation in Germany.
Fervo is feeling the pressure to get to the market fast.
By 2026, it plans to generate 70 MW of power at its Cape Station project to fulfill contracts for customers in California. By 2028 it plans to reach 400 MW.
In 3 years, the plan to grow from two wells and 3.5 MW to a large field development with enough wells to support 400 MW of production will test the knowledge, experience, and the reaction times of an experienced team using oil industry methods, services, and supplies to do something quite different.
And they need to execute all of that well enough to convince investors and lenders to back further developments.
When Norbeck describes what Fervo is doing, it doesn’t sound hard.
“Scaling up to 400 MW does not require building something that is 100 times bigger or more complex, it is actually just replicating what has already been done 100 times,” he said.
Fervo began drilling and fracturing wells for the water-heating system last year. By July the company had completed 12 wells and ordered the turbines and generators needed to convert that hot water into power for sale beginning in 2026, Norbeck said.
The pace of the work is part of the company culture.
“We are really focused on accelerating the learning curve,” said Christian Gradl, vice president of operations for Fervo, during a panel discussion at this year’s Offshore Technology Conference (OTC).
They are learning as they go, aided by a fast‑growing flood of data from actual enhanced geothermal development.
“We are right at the inflection point. We are going from one or two examples to a large number of them,” said Mark McClure, the CEO of ResFrac, whose fracture software and consulting services are being used to create geothermal models to help guide the effort.
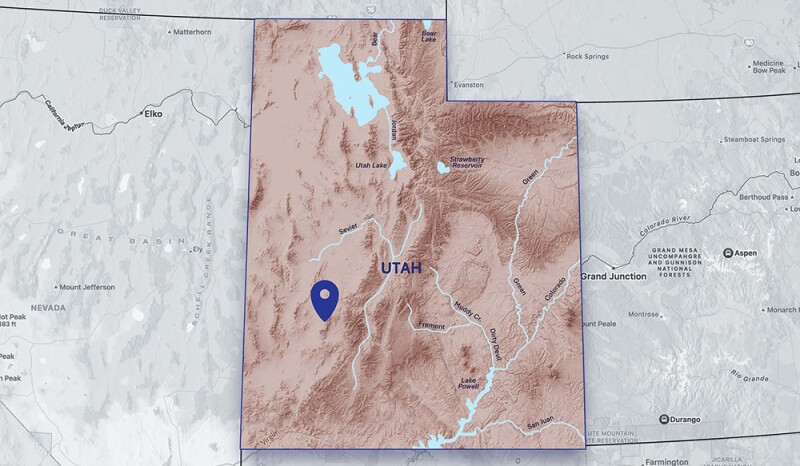
Think Fast
As Fervo’s team contemplates the meaning of the new information streaming in, it must also move quickly.
“We need to continue making progress to meet contractual obligations. There is not a lot of time to stop and do lookbacks.” Norbeck said.
At the Stanford Geothermal Workshop held at California’s Stanford University he also said this: “The pathway to scale is straightforward and requires no new technology leaps. With no significant technical risks remaining, the focus now must be on consistency, replicability, and cost reduction.”
The company’s plan is based on the belief that the risks of building a first-of-its kind commercial-scale plant on a tight schedule are far outweighed by the rewards.
“For those who deploy early, the opportunities grow,” Norbeck said.
Those opportunities include more chances to improve the process, lower costs, and identify growth opportunities. The thinking behind that strategy was laid out in a paper by Tim Latimer, Fervo’s CEO and cofounder, at the 2017 Stanford workshop.
Based on a study of the evolution of the shale oil and gas sector over time, he predicted that it would become possible to “accelerate the development of commercially viable EGS resources in the near term.”
At this stage, the success of the Cape Station project is like proving up an oil discovery.
Norbeck would not say what they expect to spend on it, but this greenfield development could easily consume much of the $420 million Fervo has raised from investors and grants. These are funds earmarked for work demonstrating that a large-scale enhanced geothermal project can become a successful venture.
Continued private support is critical because geothermal isn’t getting the billions of dollars in federal funding for commercialization that is going to low-carbon technologies such as carbon storage or direct air capture (Fig. 1).
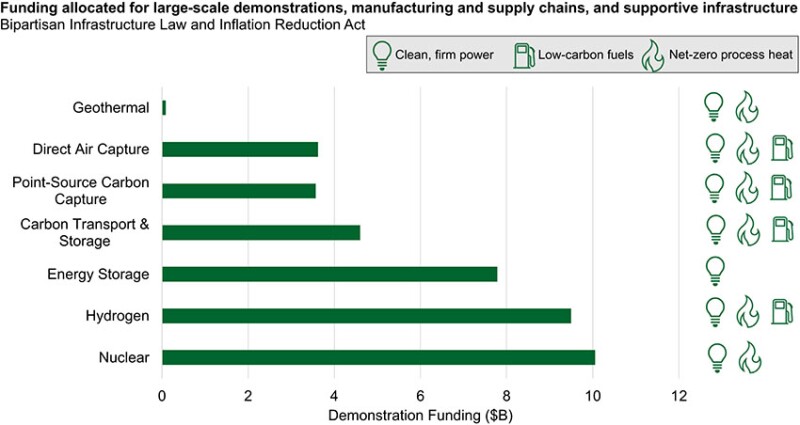
“Funding is a problem, particularly in the early parts prior to proving the (geothermal) resource,” said Ajit Menon, vice president, geothermal at Baker Hughes, during the OTC panel. He added, “Investors are not keen to come in until you have proven the resource.”
Oil to Geothermal
The most obvious signs of rapid learning in geothermal are the reports of much faster drilling through granite and other hard rocks based on advanced drilling techniques developed by oil and gas drillers.
During the Stanford workshop, Fervo reported it had reduced the time needed to drill a well from 59 days for a well with a 3,000‑ft lateral at Project Red to 20 days for a deeper, well with a 5,000-ft lateral at Cape Station.
The next step is 15-day wells, he said, adding that faster drilling has lowered the cost per foot drilled from $1,000 to $350.
In addition to drilling faster, Fervo has also reduced the downtime and costs by cutting the number of drill bits needed per lateral to two.
This is significant because it lowers the total cost of the wells, which represent about half the budget of an enhanced geothermal development. The other half pays for the power plant and related surface facilities.
A 2022 report by a researcher at the National Renewable Energy Laboratory (NREL) concluded that the well cost savings from faster drilling are a lot lower than the days saved would suggest, because the total well cost includes fixed expenses “such as the time and material costs associated with casing and cementing.”
When Fervo engineers talk about well costs, they don’t sound so fixed.
For example, they found it’s possible to live without high-cost, high-temperature drilling and fracturing hardware because the fluid pumped during those jobs reduced the heat to levels found within the upper limits of equipment used in conventional wells.
Still in the long run—which, in geothermal is measured in decades—the value of the system performance will far exceed the value of cutting the drilling cost by 40 days.
As with oil and gas, subsurface engineering and execution are both very important, and their value over the life of a project is harder to quantify than drilling performance.
“Our view is the challenge with geothermal is not the drilling technology. The oil and gas industry knows how to drill,” said Cindy Taff, founder and CEO at Houston-based Sage Geosystems, which developed a different approach to injecting water into fractured reservoirs.
The former drilling vice president for unconventional well operations at Shell says the measure of success will be an integrated system that reliably delivers kilowatts of power at a competitive cost.
“The key things are the thermodynamics of getting heat out of the rock efficiently, getting heat to the surface without expending a lot of energy, and converting heat to electricity efficiently,” said Taff.
In short, she said the goal is simple: “We are concentrating on making geothermal more cost effective.”
Subsurface Thinking
Nobody at Fervo disagrees with Taff’s message about the importance of engineering the operation above and below the ground.
Norbeck laid out several key engineering challenges that alter the cost per kilowatt of a project.
First is the amount of energy delivered per well based on the flow rate per day and the temperature of the produced water.
Flow rate is a function of how much is injected and the percentage of the injected water reaching production wells. At Cape Station, Fervo is significantly increasing the injection rate by going to wider casing—roughly double the diameter at Project Red—and longer laterals to push more fluid through more fractures.
The produced water temperature is affected by well depth and the local temperature gradient. At Cape Station the wells are 2,100 ft deeper than at Project Red, in a formation where the temperature rises about 4°F per 100 ft of depth.
Higher temperature water increases the efficiency of the generators used for geothermal, known as Organic Rankine Cycle units (ORC). The equipment is designed to extract the maximum amount of power from water heated to around 400°F.
Different sorts of generators are needed because the energy conversion efficiency at that temperature is about one-third of the average conventional power plants with 600°F steam. If they could drill geothermal wells deep enough, companies could produce water this hot.
The problem is that it’s now not possible since such temperatures would destroy the downhole equipment that’s available today.
Another critical cost is the energy required to pump water down the injection well, through the fractures, and back up the production well.
These “parasitic loads” lower the net power output. The pumping energy expended is a function of the pipe friction plus the pressure drop while flowing through the fracture network.
Fervo is working to limit the parasitic energy loss, which Norbeck said is between 10% and 20% of the total power produced. Others have pegged it at around the middle of that range.
At Cape Station, wider casing is significantly reducing the pipe friction.
But there are tradeoffs to going bigger. The longer laterals used to increase the fluid pumped adds some pipe friction. The wider well spacing used at Cape Station—Norbeck declined to say how wide—increases the pressure drop.
“The parasitic load is directly related to well spacing—and the efficiency of the stimulation,” Norbeck said.
A good geothermal fracturing job delivers
- Evenly spaced flow paths.
- Large enough fractures to efficiently heat a large volume of water.
- Fracture networks that avoid exceptionally large fractures able to divert much of the water resulting in thermal short circuiting.
Cindy Taff, founder and CEO at Sage Geosystems, added that another goal is to create fracture networks that direct a high percentage of the injected water to producing wells. In shale, a lot of water in fractured formations leaks off to parts unknown.
The third critical engineering challenge is creating a stable, long-lasting heating system. Well spacing matters in this instance. Flow paths from the injection to the production well need to be long enough to reduce the risk of cooling the surrounding formation. Some cooling is normal, but it can grow to the point where it causes a premature thermal breakthrough.
“You want to design well spacing such that you do not see too much temperature drawdown” over a lifespan of up to 30 years, Norbeck said.
Other long-term questions raised by sessions at the Stanford workshop included heat-related damage to proppant and cement over time. There are high-temperature options available, but their higher cost will be a tough sell to companies that need to drive well costs down.
As with oil and gas, the goal is to create a large, fractured surface area. In geothermal this measures the contact area where hot rock meets injected water—called the thermal front.
“Surface area dominates long-term performance,” Norbeck said. He provided a rule of thumb, suggesting that 10 to 20 million ft2 of total surface area per well is required.
Spacing and Stacking
Concentrated multilevel development is something Fervo expects to use to reduce costs above and below the surface.
Norbeck described a tank-style development with enough wells to reach their 100-MW and 400‑MW targets.
He declined to offer further details, saying the number of wells, the spacing, and target rates for daily production were proprietary.
Those numbers may also be subject to what is learned along the way about maximizing subsurface system performance.
Norbeck said the average production well—which represents about half the wells—will produce from 50,000 to 100,000 B/D of water heated to around 400°F. While Gradl put the target rate around 75,000 B/D, the process is aimed at finding ways to do better.
They need to create a subsurface system where the flow and energy content of the water matches up with the specifications of the power‑generating system.
Data gathered by drilling, fracturing, and injection tests is offering an early measure of their decisions on how to space and stack wells to maximize the flow from well to well and minimize resistance along the way.
Fervo is using ResFrac’s software to integrate data and evaluate its spacing and frac designs. Like Fervo, ResFrac CEO McClure is not offering specifics other than to say: “For spacing and stacking decisions for EGS: Yes, this is going to be very important. Probably even more important for EGS than shale, where it’s already important.”
Bigger Pads
One surprise for Fervo is the savings it can realize from bigger well-pad designs that concentrate more wells and generating capacity around the wellheads. This is a break from how things work in traditional geothermal.
“In geothermal, when you look at a lot of maps there is a spider web of pipelines from the central plant to all the injection and production wells,” Norbeck said.
By locating standard modular turbines and generators at the pad sites, they can eliminate much of that web.
The turbines and generating equipment orderedthis spring from Turboden will allow Fervo to add capacity as it adds geothermal production at a pad site. The initial order is for three organic Rankine cycle generators with six turbines.
This can grow as the startup company adds capacity with production of water and power concentrated on the pads.
Norbeck said such a move could significantly lower the cost of future growth. And that raises the question of how dense can this development get?
The answer is a reminder that using oil business expertise for fractured geothermal requires resetting one’s point of view.
Well-to-well frac hits can be a damaging problem in oil and gas by causing extreme water production which is an indication that a well is failing. In geothermal, frac hits and high water production are goals.
Early tank development in oil and gas is associated with some disastrous results where too many wells drained overlapping pockets of oil and gas. The result was a deadly combination of high well costs and less-productive wells with high water cuts.
EGS engineers are working in granitic rocks where oil and gas are not likely—and would be a problem it were around. But they need to maximize the amount of produced water using the lowest number of wells, and space and fracture them in ways that ensure dependable heating for decades.
This presents major modeling challenges to identify the factors that could lead to excessive cooling over time, such as tightly spaced wells or large fractures that cause “short circuits” that draw water from smaller fractures that heat water more efficiently.
Cooling rock can have unexpected consequences that are not all bad. Analysis by McClure related to testing at the nearby FORGE project suggested that limited cooling causing the rock to shrink a bit can expand fractures for greater production.
But too much cooling introduces a risk of short circuiting as large fractures grow by capturing the water from other nearby ones, resulting in insufficient heating.
In its first year, Norbeck said Fervo did not see signs of any such trouble. But it is early.
Based on the evolution of shale technology, there will be surprises.
Recently Fervo has run across examples of casing deformation downhole, which Norbeck said they are investigating.
Casing damage has long been a problem in fractured shale wells. This is particularly true in areas near tectonically sensitive areas around mountains, such as the FORGE site. Damage can be caused by interactions among the force of drilling and pressure pumping, stresses related to the area’s geology, and movements between nearby rock faces.
As Fervo moves to scale up production, most others in this young field are trying to win support to field test their methods.
Government support for geothermal includes researchers like Koenraad Beckers, who describes his job as geothermal research engineer at the NREL, as doing “tech-economic simulations to get a sense of what will it take to create competitive projects.”
NREL is looking to quantify how deep, how hot, how many wells, and how much fractured surface area is needed to build successful injected geothermal power operations. Longer term it is looking for ways to limit thermal decline and prevent fractures from short circuiting.
“We are at the stage of doing our demonstration projects. There is much we do not know yet,” said Beckers.
For engineers this is good news. McClure predicted that enhanced geothermal could “open up decades of new questions.”
For Further Reading
42nd Workshop on Geothermal Reservoir Engineering Stanford, Use of the Experience Curve To Understand Economics for At‑Scale EGS Projects by Tim Latimer, Stanford Graduate School of Business; Peter Meier, Geo‑Energie Suisse AG.
2022 Geothermal Rising Conference, 2022 GETEM Geothermal Drilling Cost Curve by Jody C. Robins, Jody C. Robins, Devon Kesseli, National Renewable Energy Laboratory, et al.
Pathways to Commercial Liftoff: Next‑Generation Geothermal Powerby Doug Blankenship, Charles Gertler, Mohamed Kamaludeen, Michael O’Connor, and Sean Porse, US Department of Energy.