Standalone-sand-screen (SAS) completion, especially in horizontal gas wells with high potential for sand production, typically suffers from premature failure caused by sand erosion resulting from high velocity in the annulus near the heel section. This paper describes the work conducted to understand in detail and quantify the erosion risks to SAS completions in horizontal gas wells and to pursue a proof-of-concept assessment of using swelling-elastomer packers to segmentize the flow in the annulus as a means of reducing erosion risks near the heel.
Introduction
During the production phase, decreasing pore pressure will cause a concentration of stresses around the wellbore and perforations, leading to failure of the rock and subsequent transportation of sand particles from the wellbore to the sand-control-equipment interface (e.g., sand screens and gravel pack). In scenarios when downhole sand control is no longer effective, the produced sand will be transported to the surface, leading to other issues such as sand deposition in pipelines and erosion of surface flowlines and equipment.
In gas-dominant systems, as gas is produced from the bottom of the hole to the surface, the volume of gas increases with decreasing pressure, resulting in a significant increase in gas velocity in surface flowlines and equipment, from approximately 1 m/s at the heel section downhole to more than 10 m/s in surface flowlines. Compared with liquid-dominant systems, the relatively low viscosity and density of the gas will cause the sand present in the gas flow to easily escape from the bulk fluid-flow stream and affect surfaces at high velocities, thereby posing significantly higher erosion risks.
It is important to ensure that any downhole sand control applied in gas-dominant systems is reliable, with features that reasonably reduce the risk of premature failure. In the case of SAS completion, most authors and researchers have concluded that screen erosion is by far the most common failure mechanism. It has also been noted that annular flow plays a significant role in the erosion and failure of sand screens in horizontal gas wells.
Despite these technical challenges, application of SASs, as opposed to gravel packs, in horizontal openhole completions has the potential to significantly reduce capital expenditure, expedite well development, and improve productivity (skin). With these factors as the motivation, a proof-of-concept project involving experimental and computational-fluid-dynamics (CFD) models was conducted to assess and develop a methodology to use swellable packers to reduce annular-flow velocity, thus reducing the erosion risk on SAS completions.
Proof-of-Concept Experimental and CFD Work Programs
Sand-Erosion-Model Development. An experimental program was conducted to develop a CFD suberosion model for the specific sand-screen materials and sand-particle-size-distribution (PSD) combination.
A cylindrical sample is placed in a wind-tunnel apparatus, as shown in Fig. 1, and is impacted by air/sand flow for a specified time. Surface profiles of the cylindrical sample before and after the erosion experiment were measured with purpose-built equipment consisting of a stepper motor to rotate the sample at a specified resolution and a gauge head to measure the profile of the cylinder sample with resolution of ±3 μm. The difference between the profiles before and after the erosion experiment for a given cylinder angle is determined. From the obtained experimental results, CFD simulations are conducted to provide impact-angle correction for particles with low Stokes numbers.
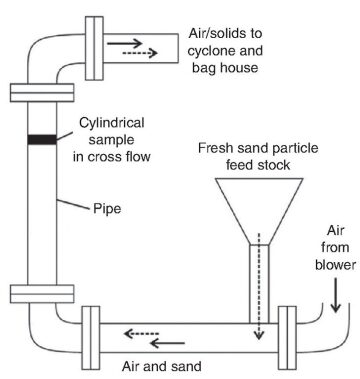
Several experiments were also conducted to validate and assess the accuracy of the developed erosion model in predicting material loss of sand-screen coupons. Erosion experiments involving coarse particles on a rectangular screen coupon were conducted with the same apparatus as shown in Fig. 1, with the cylindrical sample substituted by the screen coupon or by the perforated plate similar to the shroud material of the SAS. The depth of material loss for each sample was determined on the basis of surface-profile measurements of the sample before and after erosion experiments by use of a coordinate measurement machine (CMM). The CMM has the ability to provide an accurate measurement with an uncertainty of ±1 μm and spatial repeatability of ±5 μm.
The experimental setup for the 1-m screen section uses similar blower, sand-feeder, and bag-house systems as those in the apparatus shown in Fig. 1, with modifications to incorporate annulus/base-pipe flow sections in a horizontal configuration. The test section consists of a 1-m SAS with a concentric ring attached around the annulus near the middle section of the screen to divert the flow toward the screen (Fig. 2 above). Air and sand with the same particle-size distribution as the cylinder-in-pipe experiments were passed through the wind tunnel. A qualitative comparison with the paint-erosion method and a quantitative comparison of the erosion rate predicted by CFD with experimental results were conducted (results are shown in Fig. 3). Further details regarding the paint-erosion technique are given elsewhere, while a similar technique and apparatus were used to measure the material loss on the screen.
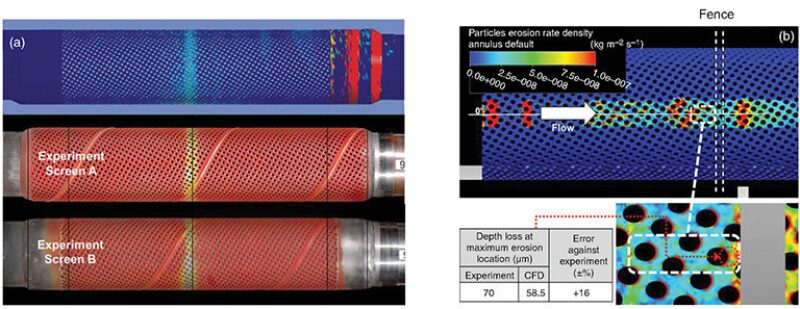
In summary, the developed CFD suberosion model has shown excellent agreement with experimental validation, with nominal accuracy of approximately ±1% and ±16% at the point of maximum erosion for the perforated-plate and 1-m-SAS experiments, respectively.
Enhancement of Erosion Model at Elevated Temperature and Sand Concentration. The erosion model developed at room temperature and dilute sand concentration was then enhanced to incorporate the effect of an elevated temperature and high sand concentration through a series of experimental campaigns. In the elevated-temperature-erosion experiments, a setup similar to that shown in Fig. 1 was used. The sample holder was modified and fitted with electrical heating elements to heat rectangular samples to the desired temperatures. Erosion experiments of selected materials were conducted up to 120°C, and the ratio of erosion rates at room and elevated temperatures was then computed. The trend of decreasing erosion rate with increasing temperature up to approximately 200°C has been observed by other investigators for erosion because of direct impingement of solid particles on other stainless- and carbon-steel materials.
To assess the effect of high sand concentration, an erosion experiment in a water-/sand-flow rig was conducted (results are shown in Fig. 4). It can be seen that the erosion rate increases linearly with increasing sand, loading up to 1% vol/vol concentration before converging to a plateau at approximately 5% vol/vol concentration. This effect is believed to be caused by the increasing prominence of particle/particle interaction with higher sand concentration.
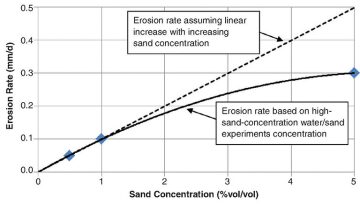
Sand-Screen-Failure Condition. To establish the conditions at which the sand screen was significantly damaged and considered failed, progressive-erosion experiments on selected sand-screen coupons were conducted with the same apparatus, methodology, and sand PSD (coarse sand) for the sample-in-pipe experiments. In these experiments, however, the condition of the filter media was observed and recorded after a specified amount of sand had passed through the wind tunnel. Once an opening of approximately 300 μm was observed in the central hole, the depth loss of the shroud was measured. These data are then used to correlate the condition at which the filter medium was deemed to have failed with the amount of material loss on the shroud in CFD modeling, because explicit erosion modeling of wire-mesh-type filter media is too complex and requires substantial additional computing resources.
CFD Simulation of Gas Flow in Horizontal SAS Completion. A CFD modeling campaign was conducted to better understand the gas-flow profile in horizontal SAS completions. The main aim of this work was to assess the effect of flow-segmentizer distance in reducing the annular flow velocity in 8½-in.-wellbore and 5½-in.-base-pipe configurations. Qualitatively, the simulation work shows that the use of flow segmentizers along the horizontal completion will create flow of gas from the base pipe back to the annulus downstream of the segmentizer, consistent with other previous work. However, the quantity of gas flowing back to the annulus is dependent on three major factors: base-pipe gas velocity, sand-screen permeability, and the distance between segmentizers.
Parametric CFD-simulation studies were conducted in order to establish quantitative estimates of gas flow along the length of the horizontal completion for different segmentizer distances, gas flow rates, and screen permeabilities. Results obtained from these simulations are then integrated with the findings from erosion-model development and enhancement, and screen-failure-condition experiments, to develop a tool to optimize flow-segmentizer placement in a horizontal-gas-well completion. An example application is given in the following section.
Case Study
The developed engineering tool can help determine the optimized location of segmentizers (and the distance between them) along a horizontal gas well to limit annular velocity and, subsequently, erosion risk on sand screens. The critical inputs required are completion geometries [e.g., wellbore diameter (assuming open and uniform annulus along the openhole section), SAS outer diameter, base-pipe inner diameter, and horizontal-well length], reservoir and gas properties, and the range of expected gas-production rates throughout the well’s life. Several assumptions are also employed in the design stage, such as sand loading, flow distribution of gas from the formation entering into the wellbore, and the homogeneity of the formation sand.
A sensitivity study for a 1,000-ft horizontal gas well was conducted to demonstrate the use of this optimization tool. The gas production was varied from 30 to 40 MMscf/D, with sand loading varying from 10 to 50 lbm/MMscf. For simplicity, it is assumed that the flow of gas entering the wellbore has an 80:20 distribution. That is, 80% of the gas enters the wellbore in the first 500 ft from the heel, and 20% in the last 500 ft from the toe. Critical velocity for screen erosion used in this case study is estimated on the basis of sand-loading rate, expected field life, gas-production rate, and reservoir temperature.
A pilot installation of this openhole-SAS-completion concept with close similarities to the case study just described was conducted successfully in 2012 in one of five horizontal wells in the K field, located 200 km offshore east Malaysia. From the core analysis conducted, the amount of sand particles less than 45 μm was in the range of 23–68% by weight. The uniformity coefficient and sorting coefficient are greater than 5 and 10, respectively, which conventionally would have led to the selection of openhole-gravel-pack (OHGP) completion.
Comparison between openhole SAS with segmentizers and OHGP wells within the same reservoir and with similar permeability showed that the pilot well has experienced the same gas production with 33% lower drawdown compared with OHGP, translating to a 50% higher productivity index. Additionally, the openhole SAS completion, with its relatively simple and faster installation, led to cost savings of approximately USD 1 million. To date, continuous monitoring of the pilot well shows that it has been able to deliver a higher gas rate than the production target consistently.
This article, written by JPT Technology Editor Chris Carpenter, contains highlights of paper OTC 25019, “Reduced Erosion of Standalone-Sand-Screen Completion With Flow Segmentizers,” by M.S.A. Zamberi and S.N.A. Shaffee, Petronas Group Technical Solutions; M. Jadid, Z. Johar, and I. Ismail, Petronas Carigali; and C.Y. Wong and C.B. Solnordal, CSIRO, prepared for the 2014 Offshore Technology Conference Asia, Kuala Lumpur, 25–28 March. The paper has not been peer reviewed. Copyright 2014 Offshore Technology Conference. Reproduced by permission.