The installation of flowlines in ever-deeper and -more-remote areas requires specific technologies for precommissioning. Coiled tubing can be a solution; however, offshore precommissioning can require coiled tubing to be deployed several times for durations sometimes exceeding a month and requires larger diameters. Therefore, a campaign was initiated to characterize the behavior of coiled tubing under combined plastic and elastic fatigue. In addition, an innovative bend-stiffener design was developed to control the stress levels in the coiled tubing at the hang-off location.
Introduction
Precommissioning is a critical part of flowline installation and operation.
×
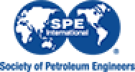
Continue Reading with SPE Membership
SPE Members: Please sign in at the top of the page for access to this member-exclusive content. If you are not a member and you find JPT content valuable, we encourage you to become a part of the SPE member community to gain full access.