In the fifth installment of the Society of Petroleum Engineers’ Project, Facilities, and Construction Expanding Facilities Knowledge series, Kenneth Arnold, senior technical advisor with WorleyParsons, asked, “Are you a professional engineer?” According to Arnold, being a professional engineer requires more than merely applying the science and knowledge of engineering to defined tasks.
Engineering culture is largely a safety culture. Hazards exist in all oil and gas facilities. He said facilities design should be carried out in a way that protects individuals from common mistakes. “We have to assume that people will make a mistake and protect them from themselves,” he added.
Statistical Analysis
API RP 13C is the recommended practice for analysis, design, installation, and testing of basic surface safety systems for offshore production platforms. The rule provides the groundwork for a generic hazard analysis. “Process upsets cause bad things to happen,” Arnold said. Many facilities use an event tree analysis (Fig. 1). “It does not matter who designed the facilities, hazards remain the same,” he added. The purpose of analyzing hazards is to identify which sources can lead to a problem such an injury or an oil spill.
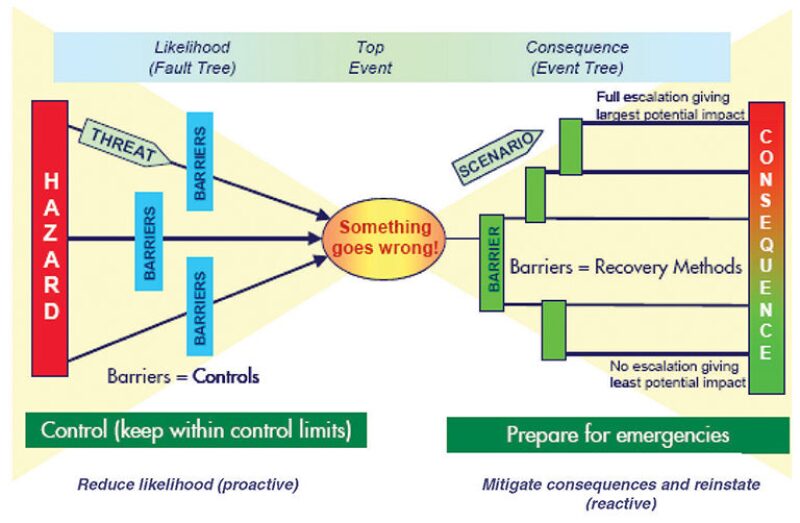
Specific problems such as overpressure, leaks, fire tubes, excessive temperatures, and inflow exceeding outflow each have to be identified and protected against. Typical components used in offshore applications function in the same manner regardless of application. The challenge is to look at each piece of equipment to determine what kind of process upset can occur. “You then must decide how to control these events, how to set up sensors that serve to prevent these events,” Arnold said.
A proper hazard analysis can be used to determine what devices are needed for each specific facility. According to Arnold, simply complying with API 13C does not guarantee a safe facility. “The idea that, if you put the right shut-ins in place, a facility is safe, is far from the truth,” he said. Arnold pointed out that in one 10-year period in the early 1990s in the Gulf of Mexico, all cases that were reportable as a fire or explosion were caused by events that had nothing to do with the process safety outlined in API 14C. “Compliance is step one, but it doesn’t give you a safe facility,” he said.
The primary benefits of hazard tree analysis include providing concise documentation that is easy to audit. It can minimize subjective decisions, and it provides consistent results in production facilities.
Safe Facilities
“A facility designed with a safety shutdown system is not necessarily ‘safe,’” Arnold said. He cited API RP 14J. “If you are a facilities engineer anywhere in the world and you have not read 14J, you are not prepared to do your job.” The document is an overall analysis of all the other processes engineers need to consider when designing a facility.
Many sources of hazards have nothing to do with the way the process is designed. Escape paths, electrical systems, firefighting systems, and insulation on piping can each contribute to hazardous conditions. Simple things like mixing fuel, air, and an ignition source need to be considered when designing a platform. “We need to separate our fuel sources from our ignition sources as much as we can,” he said. “We can’t separate fuel and ignition sources totally, but we can try and minimize the occurrence of them being together as best we can.”
Facilities are designed with an appropriate level of devices and redundancies to reduce the risk of occurrence of those sources and conditions that can be anticipated by sensing change in process conditions. Although much more is required if the overall probability of any one change leading to a hazard is to be acceptable. Improved maintenance, operating procedures, testing, and drills all contribute to improving a facility’s overall safety.
The principles outlined by API 14J require engineers to design for safety by properly containing hydrocarbons and preventing ignition. Electrical systems should be properly designed, and the structure should be designed to prevent fire escalation while also providing for personnel protection and proper escape routes.
Human Factors
Human factors engineering (HFE) is a specialized discipline. The science is devoted to ensuring consideration of people in the design based on capabilities, limitations, culture, experience, and motivations. “We have to think about the human element in what we are designing,” Arnold said. “We are getting better at understanding what human factors entail,” he added.
“We need to understand what people can do, what they cannot do, and what they will do,” he said.
HFE is often equated to ergonomics. While ergonomics is part of HFE, it is not everything. Looking at controls, alarms, personnel selection, training, and understanding job tasks is also part of HFE (Fig. 2). “You want people to naturally do the right thing when they are under stress, when they have inadequate information, or even when they have conflicting information,” Arnold said. “They need to understand the information they are seeing.”
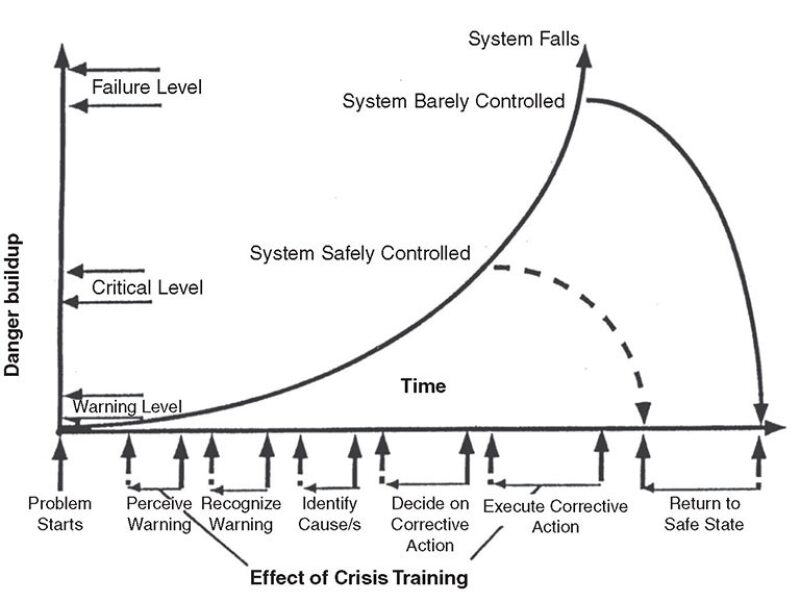
HFE is devoted to promoting safe and efficient person/machine performance and to reducing human error. Operating procedures are devised to offer clear directives on how to carry out specific tasks; although, human error can render procedures obsolete.
With HFE, facilities design is carried out with consideration of a variety of human factors to prevent errors in a time of crisis. “Just because there is a procedure in place, we owe it to the operators to do a better job in our design,” Arnold said.