George P. Mitchell died on 26 July 2013 at the age of 94. He left behind a multifaceted legacy that testified to his entrepreneurship, philanthropy, and love of country. Within the oil and gas community, this legacy focused on his work to prove up the Barnett shale unconventional gas resource, which established him as the “Father of the Shale Gas Revolution.” Through his vision, perseverance, and commitment, the knowledge base and application of existing and new technologies not only revolutionized the search for shale gas, but also carried over into tight oil and gas reservoirs, changing the global outlook for both.
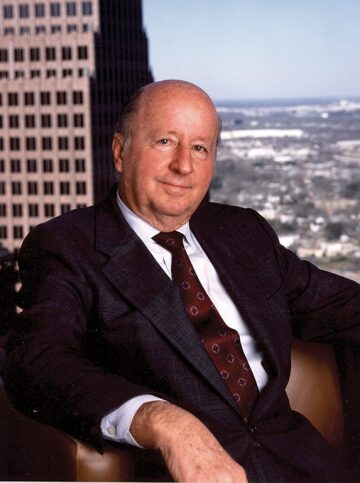
Beginnings: Getting Into the Gas Business
George Mitchell entered the oil and gas industry through the encouragement and tutelage of his older brother Johnny. After graduating from Texas A&M University in 1940, earning a degree in petroleum engineering with an emphasis in geology, Mitchell served in the Army Corps of Engineers during World War II. He began working with his brother on oil prospects while still a member of the Army Corps. He and Johnny established their first company, Oil Drilling Inc., in the late 1940s, with George generating drilling prospects and his brother finding investors.
Ellison Miles, an acquaintance of George’s from his time at A&M, started a drilling company in north Texas after leaving the Army. He and business associate, John A. Jackson, became aware of the potential for a large stratigraphic gas accumulation in Pennsylvanian-age Atoka conglomerates in the Fort Worth basin of Texas and communicated their thoughts to George. Oil Drilling put together the necessary money and took their first lease in the Fort Worth basin, a 3,000-acre tract in southwest Wise County.
In 1952, George Mitchell’s journey to the Barnett began with the drilling of the first well on this lease, the D.J. Hughes No. 1. The well encountered multiple members of productive conglomerates and was completed as a shut-in gas well. According to Kutchin (2001), within 90 days of this discovery, Oil Drilling acquired 300,000 acres in the north Texas area. Subsequent test and re-entry of previously plugged wells confirmed the significance of the find.
Oil Drilling, however, was faced with several obstacles at this point, the most significant of which was a market for the gas. Since the early days of drilling in the area, Lone Star Gas Company had dominated gas gathering and marketing in north Texas, transporting it to the Dallas area. The problem with this dominance stemmed from the fact that operators had little choice but to sell their gas at Lone Star’s terms, which included marginal pricing and seasonal takes. Few, if any, operators in the north Texas area during the ’40s and ’50s would drill for gas. However, if gas was all they encountered it was sometimes better to sell something for a return even if it was for only a portion of the year rather than plugging the well. Mitchell, however, was not looking for oil and understood that to make this new play commercial he had to have year-round sales under a guaranteed contract. This was an insight at a time many in industry were flaring associated gas.
Mitchell immediately set out to break Lone Star’s stranglehold on the north Texas gas market. In 1955, he was successful in negotiating a very favorable contract with Natural Gas Pipeline (NGPL) for their Chicago market (Fig. 1). Terms of the agreement provided a take-or-pay provision, loans to begin development drilling in the play, a term of 20 years from commencement of sales from a dedicated area, and a price of 13 cents/Mcf of gas, which was substantially higher than the existing local market. Oil Drilling would be responsible for delivering pipeline-quality gas to a gathering system to be built by NGPL and tied into their trunk line in Oklahoma. This major line moved gas from the Hugoton/Panhandle fields of Kansas, Oklahoma, and Texas to the Chicago market, where gas was used during the winter months and injected into storage fields during the rest of the year.
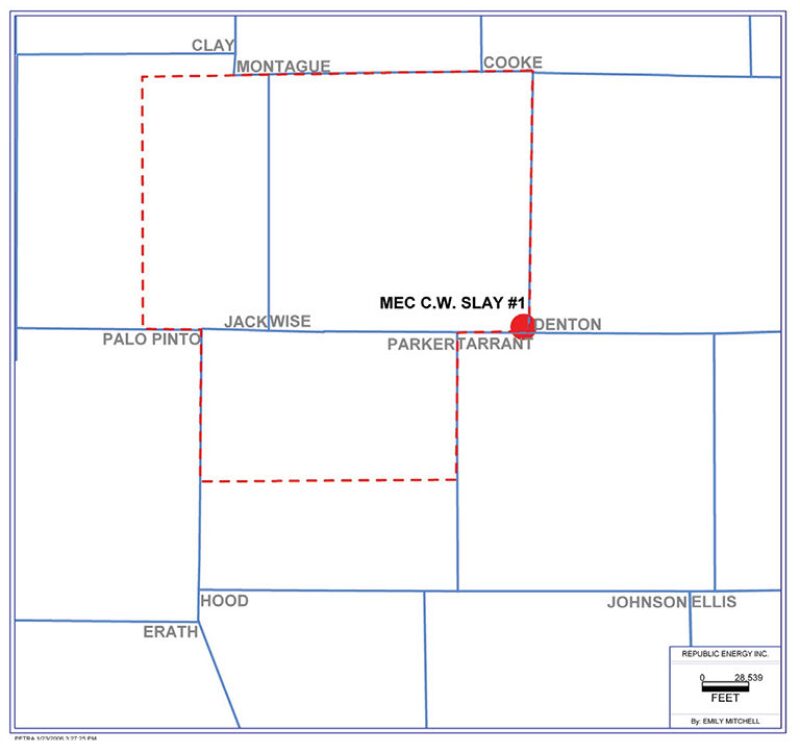
The pipeline-quality gas provision forced the company to get involved in the gas-processing business, as the majority of the gas developed in the contract area at that time was 1,300 BTU (liquids-rich), and natural gas liquids (NGLs) needed to be stripped to meet pipeline specifications of 1,000 to 1,100 BTU.
This entry of the company into gas processing proved beneficial over the years since the original plant constructed for processing the gas would recover 50 to 60 bbl of NGLs per MMcf of produced gas. Allowing for shrinkage of the gas stream, processing was still quite profitable.
Prior to the first sale of gas through the contract on 17 December 1957, Oil Drilling changed its name to Christie, Mitchell & Mitchell to reflect H. Merlyn Christie’s involvement in the company. The sale of this first gas established the end date of the contract as 17 December 1977. Over the next 35 years the company experienced a number of name changes and entered into contract extensions and renegotiations, but maintained a continuous drilling program in the Atoka conglomerates.
Mitchell’s Rising Use of Fracture Stimulation
In 1972, the company name changed to Mitchell Energy & Development Corp. (MEDC) and was listed on the American Stock Exchange. The development side of the company involved real estate and the building of The Woodlands, a master-planned new town located north of downtown Houston. A public offering proved beneficial for the cash requirements necessary for these two diverse entities and still allowed George Mitchell to retain control of the company with 70% of the voting stock. This controlling interest proved crucial for his future efforts to prove up the Barnett shale gas resource.
Over the years Mitchell applied fracture stimulations to most of the north Texas conglomerate wells to improve rates, ultimate recoveries, and well economics, but most of these early fracture jobs were relatively small.
In 1979 the company pumped the largest massive hydraulic fracture stimulation on record at the time in an attempt to improve the commerciality of its North Personville field in Limestone County, Texas. The treatment was a gelled water fracture consisting of 1 million gal of fluid and 2.8 million lb of sand. It resulted in a twofold increase in the well’s production rate and ushered in a new era for the company as a whole.
While North Personville became one of the company’s largest production centers, second only to north Texas, this stimulation opened up a new niche, which was unconventional, tight-gas reservoirs.
Building Up the Barnett
In 1981, Mitchell drilled the discovery well for the Newark East Barnett shale (NEBS) gas field, the C.W. Slay No.1. Originally planned as a Caddo limestone and Atoka conglomerate test, the well was deepened at George Mitchell’s insistence to evaluate a possible Viola limestone (Ordovician-age) extension to an existing field in the area. When the Viola proved tight, Mitchell requested a test of the overlying Mississippian-age Barnett shale (Fig. 2). The initial test after acidizing was insignificant and the well was shut-in for evaluation.
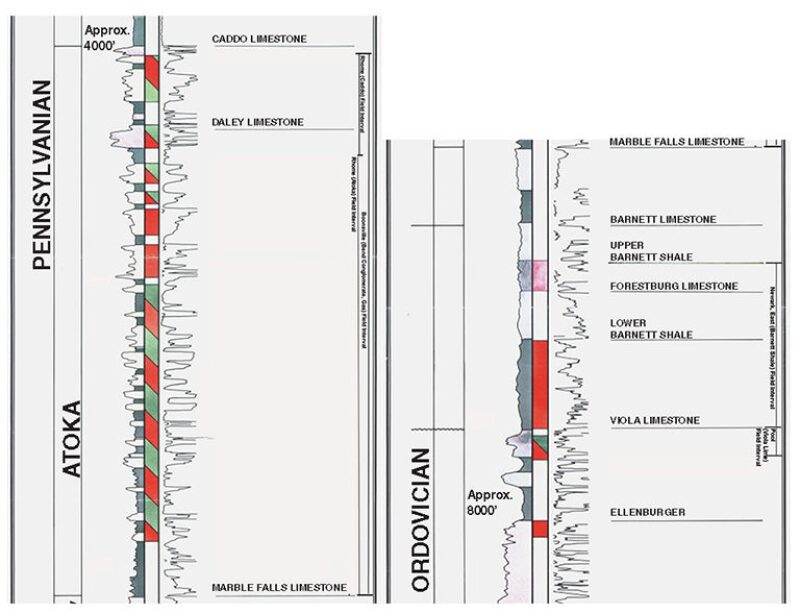
By mid-1981 MEDC began rebuilding its north Texas team, which had suffered losses of geological and engineering staff to competitors and through retirements. Mitchell began organizing the team he would lead over the next 20 years to evaluate and prove up the NEBS as a world-class gas field and to change the global gas picture.
The C.W. Slay No. 1 well was stimulated in the lower Barnett in September 1981 with a 250-ft theoretical fracture half-length (TFHL) treatment. The well tested gas at ~250 Mcf/D, an insufficient rate to justify a connection by NGPL. Wells not accepted by the gatherer either had to be shut-in or connected using company funds. Mitchell paid the cost and the well was connected to sales in June 1982. The Barnett’s initial production coincided with negotiations between MEDC and NGPL to improve the gathering system in the contract area to drop line pressures.
During the previous 25 years, MEDC extensively developed the Atoka conglomerates in the contract area, generally forming 352-acre pooled units to HBP (held by production) most of its 350,000-acre leasehold. Many of these wells reached advanced stages of pressure depletion and were unable to produce against line pressures without the aid of company-installed single-well compression. These individual compressors greatly increased manpower requirements and operations cost. The system needed to be upgraded with line looping and increased gathering-system compression.
NGPL indicated a willingness to make the system upgrades if MEDC could show a minimum of 5 years of drilling potential to meet the contract obligations. Mitchell requested an in-house study of drilling prospects within the contract area, not only to determine the 5-year outlook, but also to obtain an estimate of the remaining life of the existing conglomerate play. This study was executed by MEDC geology and reservoir engineering, and the results indicated that there were sufficient prospects for the 5-year period and probably for an additional 5 years beyond that.
By 1992, however, the company would have a difficult time finding and drilling enough commercial wells to replace yearly production and to build its reserve base, and that would lead to difficulty meeting contractual volume requirements.
Mitchell Energy Barnett Shale Team: Acknowledging Its Members’ AccomplishmentThe Mitchell Energy Barnett Shale Team received the 2013 Spirit of ECC Award at the 2013 Engineering & Construction Contracting (ECC) Association Conference, held mid-September in Palm Desert, California. In 1981, the late George P. Mitchell assembled a team of geologists, engineers, and other critical groups, to find a commercially viable way to extract natural gas trapped in the north Texas Barnett shale formation. At the time, few people expected this endeavor to succeed, and none could have imagined the energy revolution this team would begin to unleash 17 years later. The thought leadership, entrepreneurial spirit, and perseverance the Mitchell Energy Barnett Shale Team demonstrated over those 17 years is at the heart of what the Spirit of ECC Award represents. It took tremendous teamwork to overcome the uncertainties and setbacks encountered in working on a new technology development project for that period of time. A diverse group of 62 people were at the core of this project, with no doubt many others contributing to the team’s ultimate success. These team members have not received the acclaim they deserve for what they accomplished. The award and the following published list are opportunities to acknowledge their achievement.
|
The Barnett and Mitchell’s Team
George Mitchell then issued his challenge: “We have 10 years to find a replacement for the north Texas revenue stream.”
It made obvious sense to look where the company was already producing. The company had an advantageous gas contract, a large HBP land position, pipeline infrastructure, a gas-processing plant, and a staff already working the area. The north Texas region was responsible for a large portion of the company’s revenue stream and assets and, therefore, the company’s future depended on finding a replacement for the conglomerate production. Mitchell was assured that everyone involved understood the critical nature of the situation and would find the necessary replacement.
This initial challenge led to the beginning of the Barnett team, which over time grew to include professionals from many specialties.
At that point no one in the company knew what the replacement would be, but due to the recent test in the C.W. Slay well, the Barnett shale was one of the likely candidates. Over the next decade, the list of candidates grew to include 10 possibilities. The general feeling was that the replacement would not be a single objective, but rather a multitude of objectives.
The effort began with MEDC exploration and development geology assessing available sources of information. Some of the shallow prospects on the early list could be evaluated using existing well data and incorporating additional science as new development wells were drilled. That was not the case for the Barnett shale and some of the deeper prospects, however, since most of the deeper wells in the basin were old and had inadequate well logs. In fact, to save money, even some of the newer wells that used modern logging programs had the porosity tool turned off while crossing the Barnett shale. The absence of good gamma-ray and porosity logs in wells significantly hampered regional mapping and evaluation.
When management was informed about the lack of a good database, it was decided that standalone exploratory wells were not feasible. On the other hand, exploratory deepenings of selected development wells could be used as long as development reserves would carry the total well cost. Those deepenings would build the necessary database, and would test stimulation techniques and evaluate their results.
During the same time period, members of the team were reviewing publications on the north Texas area as well as the published results from the Gas Research Institute/US Department of Energy (GRI/DOE) Eastern Gas Shale Project. One of the main takeaways from the GRI/DOE project was that gas shales needed to have open natural fracture networks for gas storage and permeability.
The team then initiated a detailed structural anaylsis for the deep section within the MEDC contract area. Shallow wells were utilized to map the base of the Atoka to see if it might highlight areas where faults, flexure zones, and four-way structures could be identified since those were all regimes where natural fracturing would be expected. The areas of interest were then researched to determine whether seismic data was available or needed to be acquired.
Seismic data was obtained, wells were deepened, cores were taken, and a Barnett database began to be built on the shale’s organic richness, thermal maturity, structural complexity, source-rock thickness, and petrophysical parameters.
From 1982 through 1986, 41 wells were deepened, with MEDC engineering testing 30 and establishing production on 21 (Fig. 3). Those wells provided initial insight into gas productivity and thermal-maturity requirements.
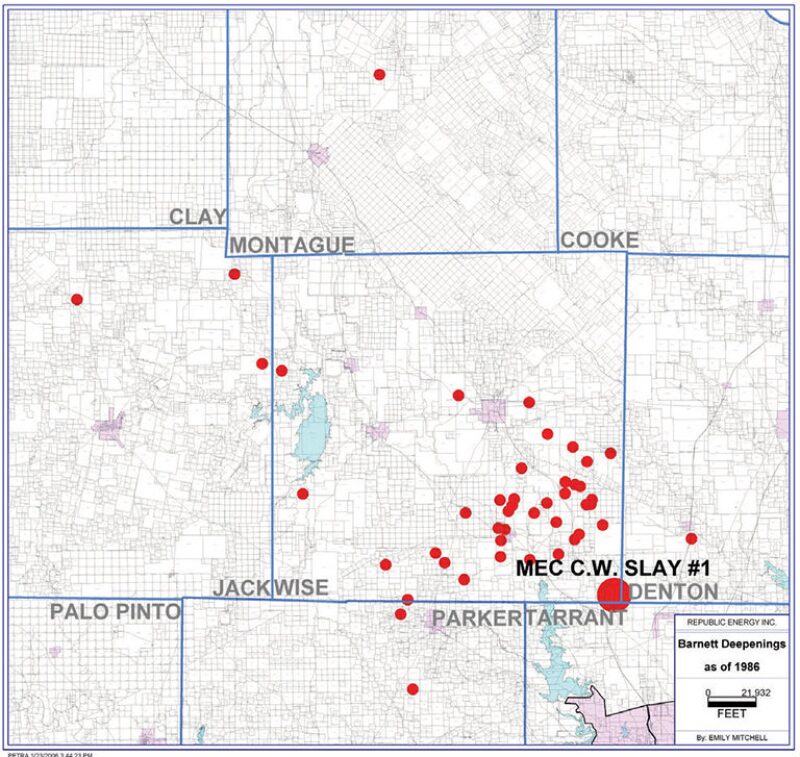
However, one of the more significant realizations dealt with natural fracturing. In structural areas, the Barnett was frequently heavily fractured, but the fractures were completely cemented with white calcite (Fig. 4). In addition, the mineralization associated with the healing process adversely affected matrix porosities and resulted in higher fracture gradients than observed in structurally quiet areas. Cores provided the means to measure rock porosity and correlate that to the log porosities. Although core evaluations indicated average values of 3.7% porosity (average log values of 13.5% from density response using a 2.71 grain density), the majority of the porosity in the rock was not visible.
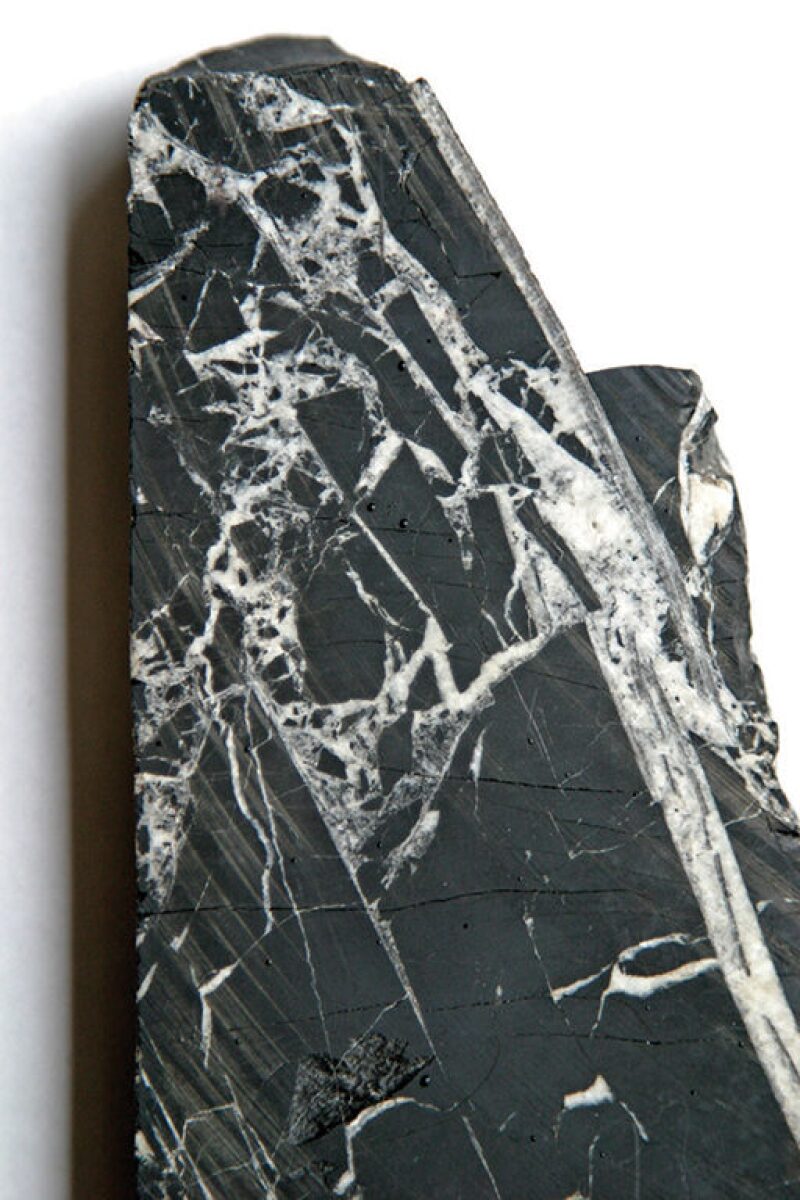
It was not until 2007, when the Bureau of Economic Geology in Austin, Texas, applied argon ion milling to the sample-preparation process, that the source of the porosity was identified. Resolution then was so enhanced that nano-pores could be seen throughout the organic material in thermally mature rocks and the connectivity of these pores was the source of the matrix permeability.
Proving Through Stimulation Experimentation
As early as 1986, Mitchell had established, in the case of the Barnett, that natural fractures were not a contributor to production, which was determined to be completely dependent on the amount of source rock contacted through induced fracturing and the ability to achieve a large pressure differential between the matrix and the fracture. That conclusion was in direct conflict with the prevailing models at the time. This knowledge was obtained through cores, pressure analysis, and stimulation experimentation.
In the evaluation of the 30 test wells, MEDC geology was able to identify gas-mature areas, and MEDC engineering experimented with varying types and sizes of stimulations. Initially foam fractures were pumped. But the need for longer fracture wings caused the TFHL to exceed the capacity of the fluid to carry the large volumes of sand used. Engineering was, therefore, forced to go with nitrogen-assisted gel fractures.
By the end of 1986, the company had pumped fracture stimulations with TFHL designs as long as 1,500 ft. In many of these wells, as the fracture lengths were increased, there was a commensurate increase in initial rates (Fig. 5). The 1,500‑ft design frequently yielded initial gas rates of 900 Mcf/D to 1,100 Mcf/D, so the company decided to standardize on this size and monitor production and develop decline curve and economic models.
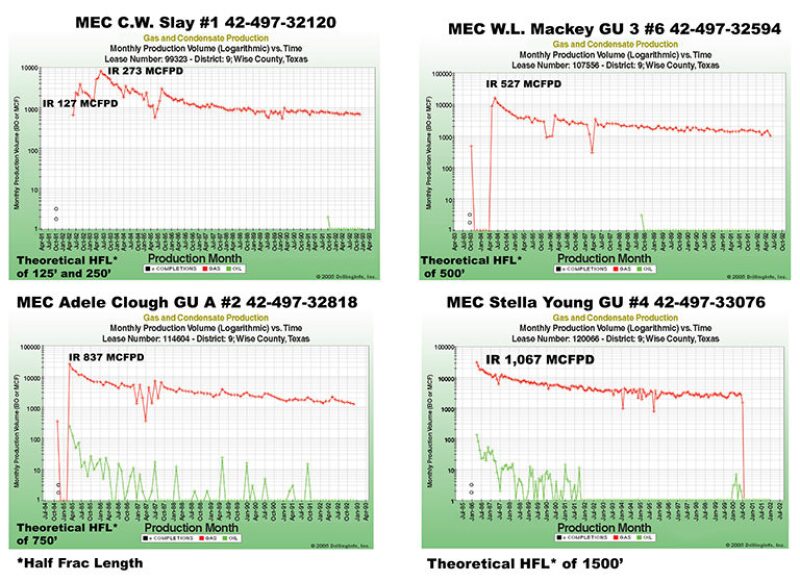
Since no productive analogs could be identified, extended production histories were required to determine estimated ultimate recoveries (EURs). Initially after a well was stimulated and brought on production, a minimal amount of reserves would be attributed to it, and when production surpassed that booking, the reserves would be revised upward.
By mid-1987, there was ample production history for the identification of a potential development area of 15 sq miles (Fig. 6). Completions within this area utilizing a 1,500-ft TFHL stimulation gave repeatable results. Outside this area, the results were mixed, but MEDC engineering believed by tweaking the fracture stimulations they could increase the size of the development area.
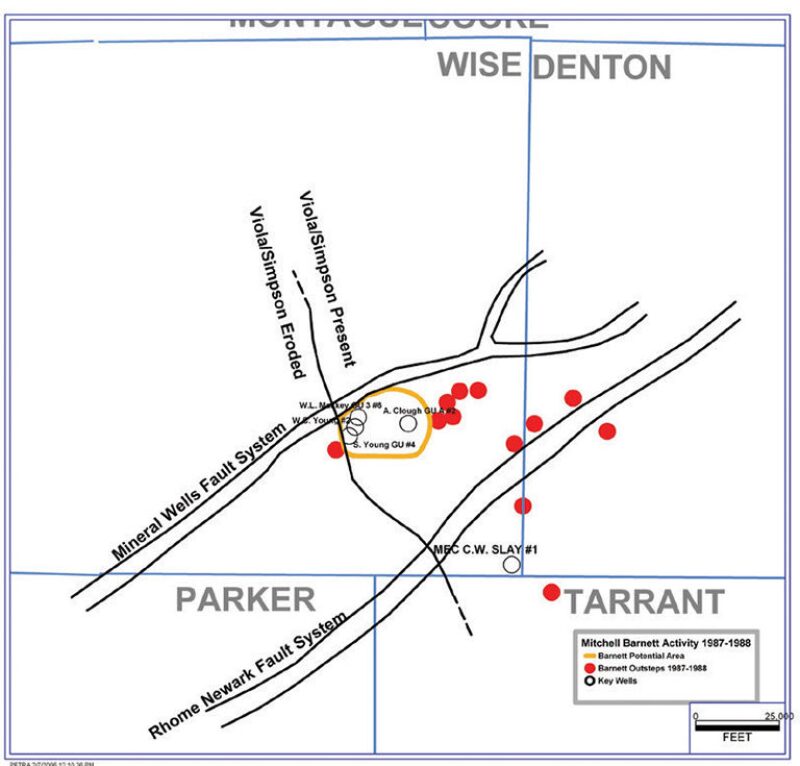
A sufficient number of wells and production histories existed by 1989 so MEDC reservoir engineering could begin working on models to establish some guidelines. The data suggested that a well with an initial gas rate of 900 to 1,200 Mcf/D might be expected to produce approximately 1.0 Bcf during a 25-year life. The consensus at the time was that a 1.0-Bcf recovery per well would meet MEDC’s corporate economic criteria with expected product pricing.
However, the economic models suggested the program would not be able to stand much geologic or mechanical risk. The only way to improve the economics was to increase initial rates/EURs or decrease cost.
Expanding Barnett Acreage
MEDC exploration began expanding the prospective area for the Barnett in 1985, but it was not until late 1986 or early 1987 before cash flow and test results provided the encouragement to get serious about leasing new areas. One of the prime areas was east of the NGPL contract area in Denton County. Company management decided if commercial Barnett production could be established then a deal could be struck with NGPL to take the gas.
MEDC’s land department began aggressively acquiring leases in the western part of the county. Engineering began working with the fracture-treatment designs and gradually increased the number of areas where, by tweaking the design on the 1,500-ft TFHL, repeatable results could be obtained.
The company’s engineering department efforts proved very successful, and, by late 1997, a Barnett core area was established consisting of 115 contiguous sq miles (Fig. 7). The geology team members identified and mapped two major fault systems crossing the southeast corner of Wise County. The ’97 core area was limited on the north and south by these faults and on the west by the Viola limestone pinchout, where the Barnett directly overlays the fractured Ellenburger.
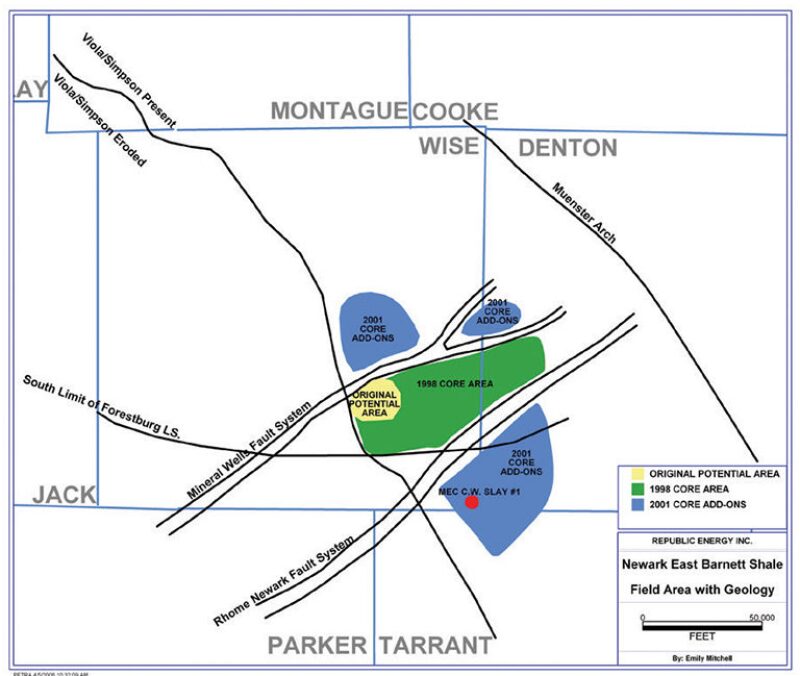
To the east, the core area extended into Denton County, where an agreement had been reached with NGPL whereby Mitchell would lay the gathering system from the wells in the county to the contract area and NGPL would pay contract price. This arrangement proved very beneficial to the eastward expansion of the play.
Over the years, attempts were made to expand west, north, and south, but all these attempts were unsuccessful and with time the team began to understand that the failure had nothing to do with the maturity, quality, or pressure gradient of the Barnett. This understanding, however, came about primarily as a result of a business decision.
Focus, Focus, Focus on the Barnett
In 1995 Mitchell Energy negotiated a contract buyout with NGPL. It provided a cash injection to the company as well as other positive benefits, but moved all the gas previously sold under the contract to spot pricing. That meant that the gas price was hit with an immediate reduction of about a dollar per Mcf. George Mitchell supported this buyout for myriad reasons, but the end result was it forced the Barnett team to expedite reducing costs and/or increasing reserves.
The Barnett achieved satisfactory economics to support a development program within the expanding core area by 1992, and in 1994 replaced the Bend conglomerate as the primary source of new gas for Mitchell in the north Texas area, comprising 71% of the program that year.
With the contract buyout and spot pricing, however, the program essentially became a breakeven proposition based on single-well economics. Corporate economics were now used to justify maintaining the program, since the majority of the gas was rich in NGLs and being processed through the company-owned plant. Corporate economics made the play generally competitive with other drilling programs in the company.
The team recognized that swings in product pricing could reduce the corporate economics advantage, so other measures had to be taken. Over the years, drilling and completions cost had seen reductions, and decline curve models had provided for the needed average gas reserves of 1.0 Bcf for a 25-year effective life. Still, more needed to be done, and the completions engineers began to look for ways to significantly reduce fracturing cost, the single largest portion of the drilling authorization for expenditure.
Ultimately, they proposed the use of the slickwater design developed by UPR for the Cotton Valley sandstone objective at Carthage field, east Texas. Initial estimates indicated treatment cost could be reduced to as little as 20% of the existing gel-stimulation cost. Engineering pumped the first of these in May 1997. With time and slight modifications, in September 1998 they were adopted as light sand fractures (LSFs) for universal application in the Barnett.
During the experimental phase of these new treatments the team developed a much better understanding of the problems with fracture containment. Poor stimulation efficiency due to weak or absent barriers was determined to be the primary obstacle in making commercial wells in the gas-mature areas, if well cost and product pricing were held constant. In many cases, water volume could be significantly increased at a low cost to overcome the absence of an upper barrier. In fact, the upper Barnett section could now be added to the completion at a reasonable cost where it had never been commercial with expensive gel treatments.
The addition of the upper Barnett resulted in average EURs of 1.25 Bcf of gas per well in the core area. In addition to the improved economics and better understanding of stimulation containment, the field began to see positive interference in old Barnett completions as a result of a nearby new well’s LSF.
Gaining Fracture Insight
In the early 1990s, Mitchell performed a significant amount of investigation into induced-fracture orientations and as a result established that this direction was generally in the N54E- to N60E-degree range. Wells stimulated near one another that were not lined up in this orientation rarely saw any indication of interference. Wells that were lined up in that direction saw interference and it was generally negative.
With the application of the LSF in new wells, the Mitchell team almost immediately began seeing well interference in nearby old gel-fractured completions, regardless of orientation. This was initially concerning, but the team found that greater than 90% of the interfered wells came back after clean-up at better rates than before being hit.
In time, it was determined that this major change in interference resulted from the fact that the induced-fracture network from low-viscosity water was significantly more complex with greater extents perpendicular to induced-fracture direction than were seen in gel fractures. That was attributed to the ability of the low-viscosity water to get into north-to-northwest-oriented natural healed fractures and, as a result of the changing stress field behind the advancing fracture, break the bond and open them to fracture-fluid entry. These opened natural fractures and secondary induced fractures parallel to the primary induced-fracture wings resulted in geometries that would reach out and touch the much more linear gel-fractured networks.
With time, it became apparent that the improvement seen in the old wells did not negatively impact the EURs in the new wells. This revelation then led to the re-stimulation of all the old gel-fractured wells with LSFs, resulting in significant per-well, low-cost reserve increases and higher estimated recovery efficiencies in developed areas (Fig. 8).
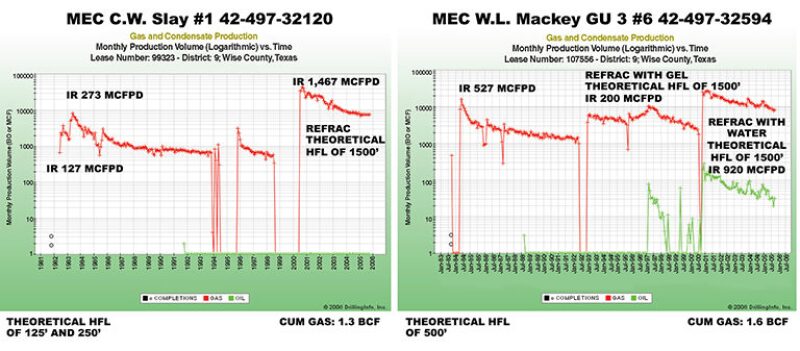
The above improvements to cost and reserves were important. However, the lessons learned on containment barriers and fracture efficiencies provided the impetus to reevaluate the areas north and south of the bounding faults of the 1997 core area. As previously mentioned, by increasing the volumes of the LSF in these two areas, the effects of weak or absent upper containment barriers could be overcome. By 2001, three additional noncontiguous core areas were proved up, increasing Mitchell’s total Barnett development area to approximately 250 sq miles (Fig. 9).
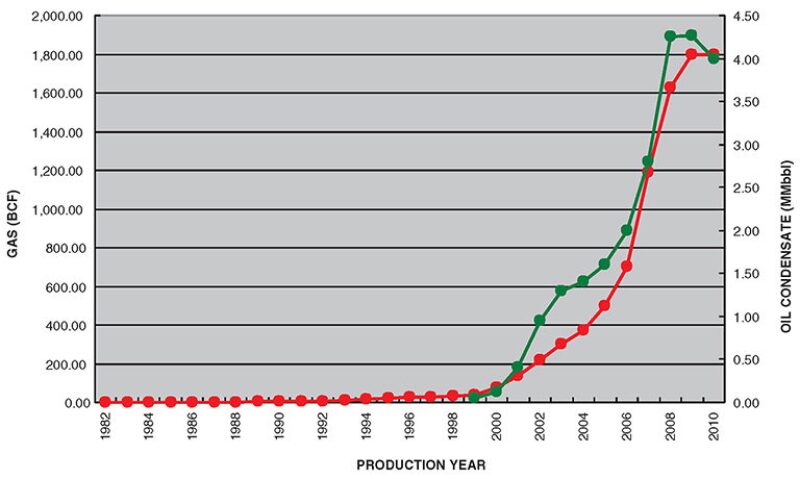
Lack of a lower fracture containment barrier was much easier to identify but more difficult to overcome since breaking through a weak Viola limestone or directly into the Ellenburger west of the Viola erosional limit generally resulted in production of formation waters and the resultant inability to get higher pressure differentials in the fracture network. In most Barnett producers, stimulation-fluid recovery is generally less than 30%. Therefore, a well exceeding this can be judged to have had poor fracture containment/efficiency and to have broken into the underlying Ellenburger (or in some instances a limited extent wet Viola interval). Mitchell attempted to modify treatment design in those areas to improve fracture containment, but had limited success.
Experiments With Horizontal Wells
Mitchell had joined with GRI/DOE in 1991 to drill a horizontal test well in the Barnett to evaluate the commercial application of the technique in a shale well. The well proved to be non-commercial after a single induced gel fracture in the uncemented portion of the cased lateral.
However, after several years of monitoring the well, the team believed that horizontals might be utilized in areas with poor or absent bottom fracture containment and recommended drilling two horizontals—one perpendicular to induced-fracture direction, and one parallel. The wells were drilled in 1998 in a noncommercial Barnett area. Both were initially stimulated with volumes commensurate to a vertical well. The completions indicated the perpendicular lateral to be superior to the parallel well and were deemed to be mechanical successes, in that the stimulation stayed in zone, but commercial failures, in that the limited treatment volumes were insufficient to establish the necessary EUR to pay the well out. The team’s belief was that with additional tweaking larger stimulations could be used in horizontals, probably in conjunction with more treatments, and large areas of mature-gas Barnett with poor lower containment could thereby be proven.
Unfortunately, additional horizontal testing was put on hold while the company evaluated strategic alternatives for improving stockholder value or, in laymen’s terms, investigating the possibility of a sale or merger.
The Merger With Devon Energy
With improving product prices, the company began ramping up drilling and re-stimulation operations within the 250-sq-mile core development area and increasing the capacity of its gas plant to handle the subsequent tremendous production increases (Fig. 9). Leasing efforts were expanded to include portions of three counties (Johnson, Tarrant, and Parker) to the south of the existing core, which the team had identified as having excellent Barnett potential. That in turn improved the company’s bottom line and its attractiveness to others.
Over a 17-year period, Mitchell successfully proved the Barnett shale source rock to be a viable and commercial play and then moved to enhance its value through the application of new and existing technology, ramping up production, and acquiring significant additional acreage positions in prospective areas.
In August 2001, a merger with Devon Energy was announced, with the official closing at the end of January 2002.
Mitchell’s Legacy
Based on George Mitchell’s 50-year commitment to building a company and, as part of that, an asset base in the Fort Worth basin, he had uniquely positioned his company to recognize, evaluate, and prove the Barnett shale resource play—a play that not only had a profound effect on the United States’ energy supply at a critical time, but also resulted in a complete reevaluation of the world’s hydrocarbon energy supplies.
He has been referred to as “The Father of Fracturing.” However, that is not accurate. Fracturing was originally proposed and utilized by others in the 1940s, expanded upon by many more over time, and used by thousands before George Mitchell applied the process to the first Barnett shale well.
His achievement dealt with the following: building of a knowledge base for shale production that went well beyond the source-rock database existing in 1981, developing an exploratory model that did not require open natural fracture networks, recognizing the importance of fracture barriers to successful shale completions, and applying new and existing technologies to a shale to make it commercial.
If George Mitchell is to receive a title for his achievements, it should be “The Father of the Shale Gas Revolution.”
Even this does not say it all, since so much of what he initiated has carried over to shale oil as well as tight oil and gas reservoirs.
References
Kutchin, J.W., How Mitchell Energy & Development Corp. Got Its Start and How It Grew, Universal-Publishers.com, 2nd Edition, 2001; pp 183–224.
Steward, D.B., The Barnett Shale Play—Phoenix of the Fort Worth Basin: A History, The Fort Worth Geological Society and The North Texas Geological Society, Spring 2007; pp 12–195.
![]() | Dan Steward, consulting geologist with Republic Energy in Dallas, Texas, served as a member of the Barnett shale team during his tenure at Mitchell Energy (1981–2001). During this 20-year period, he held a number of positions within the company management, but in one capacity or another was always involved with the Barnett shale play. Other employers throughout Steward’s 46-year career include Ames Oil & Gas, Dresser Magcobar, and Shell Oil Company. He earned his BS degree in geology from the University of Houston. After Mitchell Energy’s merger with Devon in 2002, Steward joined Republic Energy and continued his involvement with the Barnett shale through its activities. This partnership has allowed him to apply the understanding of organic shales he acquired from experience with the Barnett to other shales across North America. In 2005, George P. Mitchell asked Steward to write a history of the evolution of the Barnett play. This history was published by The Fort Worth Geological Society and The North Texas Geological Society in 2007. Titled The Barnett Shale Play—Phoenix of the Fort Worth Basin: A History, it forms the source of the material used in the accompanying article, “George P. Mitchell and the Barnett Shale.” Steward also received the American Association of Petroleum Geologists 2007 Explorer of the Year award for his role in establishing the Barnett as one of the largest producing gas fields in the country and the model for shale resource plays worldwide. |