The Society of Petroleum Engineers (SPE) technical report, Getting to Zero and Beyond: The Path Forward, sets the stage for continuing the discussion across the industry of the essential actions the industry must undertake to attain and sustain zero harm. The report is a compilation of discussions from various SPE sessions and expands on those discussions to identify and evaluate actions that may aid the industry by exploring current thinking and views; incorporating experiences and learnings from other industries that are mature in the application of human factors; and suggesting the next steps that will enable the oil and gas industry to meet an expectation of zero harm.
Introduction
The goal of health, safety, and environment (HSE) programs and departments is to eliminate incidents that produce harm whether to people, the environment, or property. But somehow the industry has settled into a comfort zone, a zone that tolerates incident occurrence and satisfaction with incremental improvement.
Phrases such as “you should have seen the way it was before” or “but we are better than we were” are heard and somehow enable us to accept that what we are doing is sufficient, good, and OK.
Industry safety statistics were the subject of an analysis conducted using International Association of Oil & Gas Producers (IOGP) member company annual safety data. The findings showed that in the period from 2014 to 2016, the lost-time injury frequency and total recordable injury frequency both posted an incremental decrease (Fig. 1). However, during the same period, the fatal accident rate showed an increase (Fig. 2).
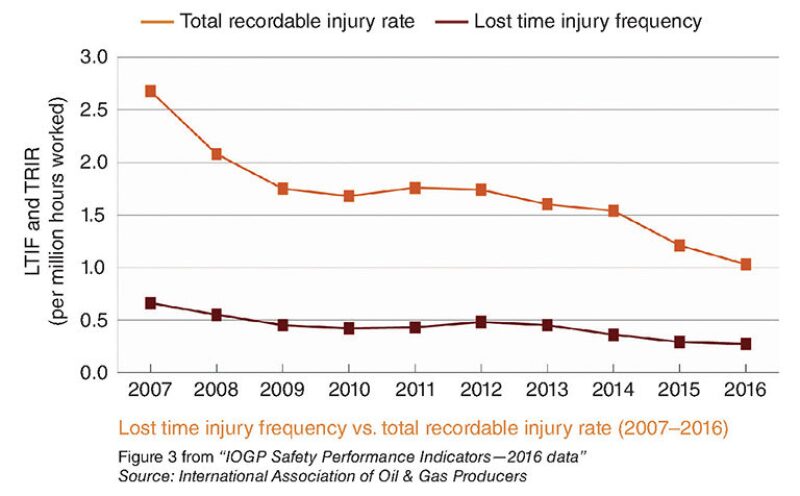
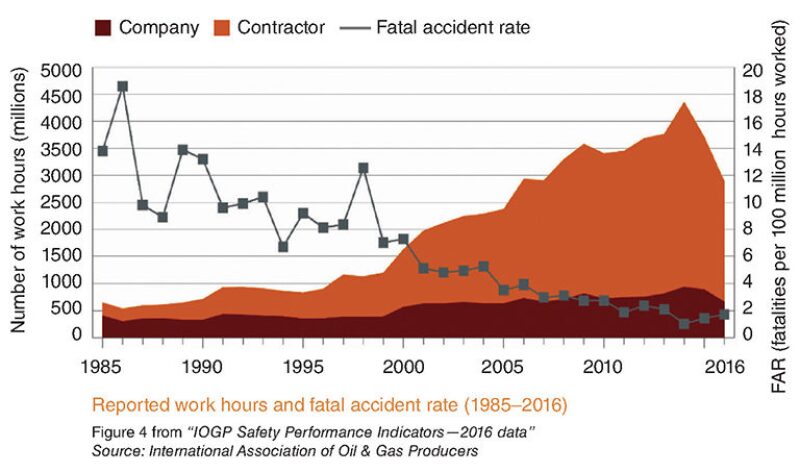
In June, IOGP released its annual Safety Performance Indicators for 2017. Although the 2017 statistics illustrate an improvement in the number of fatalities, the number of fatal incidents increased in 2017 (IOGP 2018).
Most striking is the realization that the top three causes of fatal incidents that occur in the global upstream oil and gas industry have remained the same since IOGP first began collecting the data in 2010. Fundamentally, fatalities are occurring despite the industry implementing traditional HSE efforts such as IOGP’s Life-Saving Rules, management systems, training programs, and targeted injury campaigns. What needs to occur is to challenge the current mindset, the ingrained culture. What if we could reject this incremental mindset and make the leap to be satisfied only when we are attaining and sustaining zero harm?
That is exactly what a group of SPE members did. They united, starting in 2010, to change industry thinking—to challenge incremental HSE performance improvement, and to create “zero thinking,” not as the end or long game, but as the starting point to defining HSE performance. Their work and efforts have culminated into a recently issued SPE technical report titled Getting to Zero and Beyond: The Path Forward.
The technical report points in the direction that gives us specific steps that we, as the oil and gas industry, can undertake to shift our industry into “high reliability organizations (HROs),” focused on the expectation of zero harm to drive decision making, our operations, and our definition of performance. Our current incremental thinking is giving us limiting breakthrough. “Zero and Beyond” is a breakthrough, and it matters. And best of all, we now know how to do it.
Beginning the Journey
The journey to develop the report and recommendations began in 2010 and 2011 when SPE hosted a Forum Series titled “Getting to Zero—An Incident-Free Workplace: How Do We Get There?” These two sessions used the voice and experience of 133 participants representing 92 organizations and 16 countries to frame a baseline. This baseline, while it said our present incremental thinking needed to shift to one of zero thinking, recognized the greatest impediment to do so was ourselves, our industry. Specifically, within the next few years, the industry would need to:
- Change the behavior of senior leaders
- Become a learning industry, following what other industries have done
- Eliminate the reaction to blame the individual and increase self-reporting
- Make leading indicators intrinsic, rather than elusive
- Begin to apply human factors
Then, in 2015 and 2016, SPE hosted a follow-up series, where more than 750 participants from numerous disciplines and organizations joined global sessions that were held jointly in-person and virtually in North America, South America, the Middle East, Asia, and Europe. In the 5 years since the first session, it was evident the thinking had changed; 70% of the participants believed zero harm was possible, and 20% believed it may be possible. Further, participants said “human factors” was essential to achieve zero harm. However, it was acknowledged that across the industry, there was insufficient alignment on what human factors is and how it should be applied. Participants also identified that there was misalignment and confusion on the expectation of zero harm. Overwhelming the message was: “We believe it is achievable, but we need to better understand how to achieve it.”
The original team of SPE members listened and, 2 years in the making, the “how to” has been published. Here are the highlights of how the industry can achieve zero incidents, zero harm, and zero impact.
Pathway for the Industry
Revise our vision of zero and establish a culture that supports the expectation of zero harm. If with our present thinking we are plateauing or only experiencing incremental improvement, then new thinking is required if we are going to accomplish anything different.
We are a data-driven industry and, in the case of HSE performance, our dependence on data and analysis is proving to be insufficient to drive breakthrough change. The insidious side of data is that because it is explainable it tends to be recognized as acceptable. Unfortunately, whatever is acceptable does not have the motivational power to desire or drive change. Further, because of our data-driven nature, we can never have enough; we are always looking for more data, more analysis. Data and analysis become the end game when, in fact, the real end game, doing no harm (zero), should be our true focus.
Hence, we need to be more culture-based, not data-based. As an industry, we need to change our culture to one that embraces zero harm as an expectation. This will be transformative. It will change our thinking, and changed thinking will change outcomes.
Perhaps one of our biggest obstacles is defining what zero harm means. Not everyone believes zero harm is attainable, and maybe that is because we have not yet landed on a working definition for our industry.
Defining zero harm as a goal implies that we can set incremental HSE performance targets; it acknowledges that our operations will harm today. A goal of zero suggests an unattainable numerical target of perfection. Rather, we need to think of zero harm as an expectation in each and every moment, and that it is an attainable expectation today, not a future goal for the industry. This may seem like a subtle shift in thinking, but the difference between the two is the difference between focusing on future improvement and focusing on HSE in the moment. This shift is imperative to eliminate incidents.
This is the culture shift that must occur: not accepting underlying conditions, behaviors, or gaps in systems that can lead to harm. Our present industry culture unfortunately accepts harm, because our data/analytical purist mindset cannot envision a time when no harm might occur. It is not the outcome per se that defines zero harm, it is the expectation. And interestingly, changing the thinking to expect zero will get us closer to achieving the outcome of zero harm than if not expecting it.
Learn from industries more mature in human factors. Half of our industry’s efforts to manage HSE performance are limited to the use of management systems, procedures, audits, and/or lagging indicators. Many have yet to consider how leading indicators, culture, leadership, or human factors impact HSE performance. To understand and implement these resources it is not necessary to chart new territory. There is much to be learned from industries that model, such as the nuclear, aviation, and aerospace industries. They have one important thing in common: they appreciate that risks can be managed/eliminated once you recognize that you must look holistically into how humans engage with equipment, with systems, and with each other.
We have examples in our industry. One company is focusing on the underlying organizational and system aspects to enable it to achieve a step change, not just incremental change in HSE performance (Fig. 3).
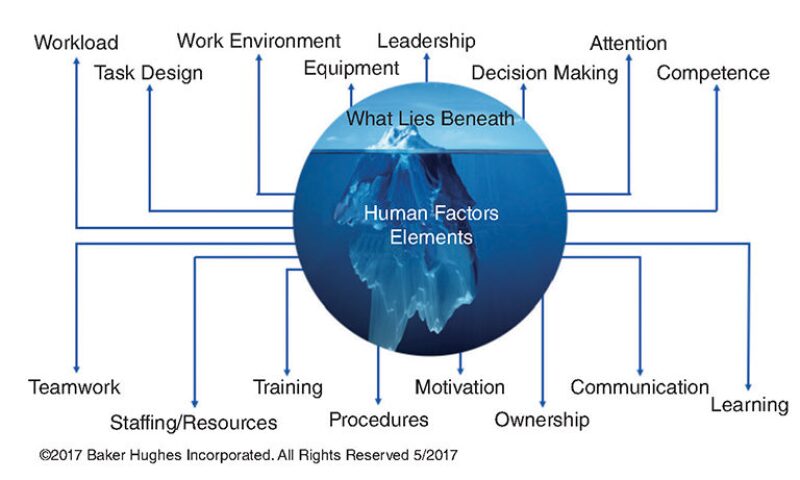
Once we have a common understanding of human factors, we can begin to drive a consistent industry culture and standardize a set of leading indicators that measure the degree to which human factors are being used within the industry.
De-emphasize injury rates and other lagging performance indicators and utilize more leading indicators to focus on safeguarding and risk reduction. Only 11% of our industry is using leading indicators (SPE Technical Reports Committee 2018). Such rear-view thinking will never allow us to focus on what eliminates incidents.
Optimize collaboration across companies and crews. Our industry is made up of a complex supply chain, all interrelated and all needing to interface seamlessly. We must collaborate to drive for standardization of management systems, practices, standards, and use of human factors principles that will drive shared learning and common solutions. We can be competitive and collaborative.
Establish a no-risk-to-sharing culture across companies and the industry. As an industry, we do not effectively share lessons. But we should. We must remove barriers to open sharing of lessons learned. There is no use sanitizing the message to the point of uselessness. We must create an environment where incident information can be shared across boundaries without fear of unnecessary regulatory reaction and burden, misunderstanding, and mistrust by the public as well as frivolous and counterproductive litigation. HRO industries have done it—why are we not?
Work hand-in-hand with regulators on risk-management strategies. Regulators have a crucial role to play. We must collaborate with regulators so a joint focus can be appropriately placed on major hazard risk. The evidence exists that where industry and regulator genuinely co-own the challenge, there is more effective action and less bureaucracy to managing the risk. For our industry, there is room to improve collaboration.
Opportunities for Individuals
As professionals in the industry, it begins with us and our leadership in the organizations where we work. As an individual starting place, look to see where you and your organization are against three key elements.
Interdependent culture. There are some very keen criteria envisioned in DuPont’s Bradley HSE culture curve (Fig. 4). To be interdependent means to genuinely look out for everyone, to avoid reliance on the comfortable feeling that everything is managed, to work cooperatively, and, interestingly, to have an expectation of zero harm (not a vision or target of zero). This is the optimal cultural stage setter for immersing oneself in human factors and HRO thinking.
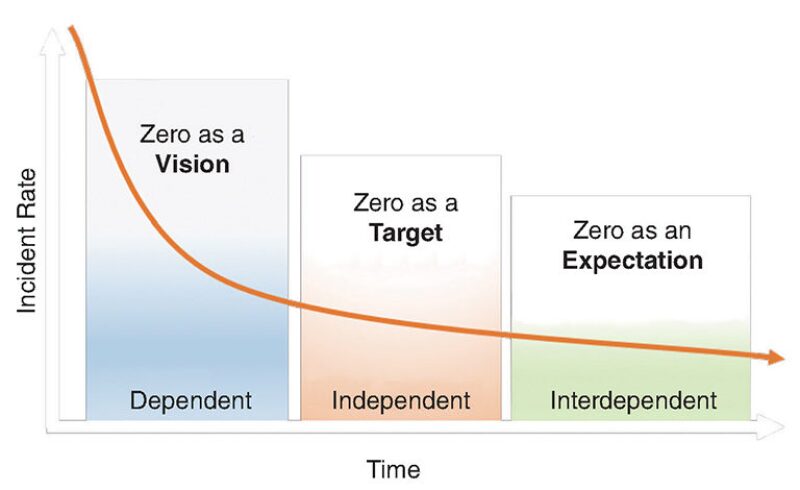
Operational ownership. This means equipping and empowering employees and the organization (not only those in HSE) to look out for each other, intervene in unsafe acts or conditions, be proactively engaged to identify and mitigate risks, and willingly implement and use controls and processes.
Sustainable HSE leadership. This is where HROs separate themselves from the pack: a willingness to look within an organization—its systems and processes—for gaps that create error-producing conditions that in themselves are at the heart, the precursors, of why incidents happen. Then correcting the gaps with a no-blame culture. The objective is to achieve an organizational culture dedicated to the pursuit of true (often pre-emptive) root cause, not what we typically label as root cause.
Summary
Our present plateau of HSE performance and the present time trajectory to get to zero is too long and should not be acceptable to our industry. We listened and our industry colleagues said we are ready for zero, just show us how to get there. Remarkably, it can be as simple as changing our thinking. “Getting to Zero” is being driven by the expectation that our actions, our work, our purpose is to have zero harm. Getting to zero equals an industry-driven expectation of zero harm.
References
Harris, W. and Hinton, J. 2017. What Lies Beneath: An Aspect of Human Performance That’s Driving Institutional Change. Presented at the 23rd Annual Human Performance Root Cause Trending Conference, Toronto, Ontario, 12–14 June.
Hinton, J., Glencross, C., Zamora, T., Knode, T., Dingee, A. 2018. Getting to Zero and Beyond. Presented at SPE International Conference on Health, Safety, Environment and Social Responsibility, Abu Dhabi, UAE, 16–18 April. SPE 190485.
IOGP Report No. 2017s, Safety Performance Indicators 2017 data. June 2018.
SPE Technical Report Committee. 2018. Getting to Zero and Beyond: The Path Forward. SPE Technical Report SPE-191770-TR. Society of Petroleum Engineers, Richardson, Texas (March).
Walker, K., Hawkes, C., Poore, W., Carvalho, M. 2018. Industry Safety Data, What Is It Telling Us?. Presented at SPE International Conference on Health, Safety, Environment and Social Responsibility, Abu Dhabi, UAE, 16–18 April. SPE 190545.
![]() | J. Jack Hinton is chief HSE officer for BHGE. Before joining Baker Hughes in 2005, Hinton was a dean and professor at the Kazakhstan Institute of Management, Economics, and Strategic Research for 2 years. He previously spent 26 years at Texaco serving in leadership roles that included director of HSE and vice president of international petroleum. Hinton currently sits on the management committee of the IOGP, is a member of the Kazakh-British Technical University Business School Advisory Board, sits on the Board of the Center for Offshore Safety, and serves as chairman of the Board of Advisors for the Southwest Center for Occupational and Environmental Health. He is a member of the SPE HSSE-SR Advisory Committee, serving as chair of its Safety Subcommittee. He holds a doctorate of public health degree in occupational health and an MS degree in environmental science, both from the University of Texas, and a BS degree in biology and chemistry from Trevecca Nazarene University. |