Historically, invert-emulsion drilling fluids are the preferred system for drilling offshore Cameroon. However, with a regulatory environment moving toward zero discharge, associated costs are rising. Therefore, an operator planning to drill in this environment investigated high-performance water-based-mud (HPWBM) system alternatives. HPWBM systems offer the potential advantage of offshore discharge of drilled cuttings and effluents (owing to the absence of oil contamination) and lowered waste-management costs. Experience in the field demonstrated that the selected drilling fluid met expectations by achieving the required drilling performance and high shale stabilization with zero environmental impact.
Introduction
Drilling with an overbalanced pressure is a common operational technique used to prevent formation fluids or gas from entering the wellbore, thereby minimizing the risk of well kick and blowout. However, overbalanced drilling can cause drilling fluid to invade the formation, resulting in formation damage, differential sticking, and sloughing if the formation consists of highly reactive clay and shale. To avoid these consequences, invert-emulsion drilling fluids have always been preferable for drilling highly reactive clays and shale formations.
The HPWBM system is formulated with a concept of total inhibition. Unlike a conventional water-based-mud system, designed chemical additives are used explicitly in the formulation to achieve desired drilling characteristics that are similar to those of invert-emulsion mud. The key features of HPWBM systems include high shale stability, clay and cuttings inhibition, rate-of-penetration (ROP) enhancement, minimized bit balling and accretion, torque and drag reduction, and environmental compliance.
A complementary benefit of its aqueous base is that HPWBM captures the growing need for more-environmentally-friendly drilling fluids. During the past 10 years, more-stringent regulations on drilling-waste disposal have been implemented worldwide. The industry anticipates that the zero discharge of oil-contaminated drilling wastes will soon be the global standard. By switching from invert-emulsion drilling fluids (oil/synthetic-based mud) to an HPWBM system, operators can achieve substantial cost savings on waste management and logistics. These savings result from the use of on-site, offshore discharge allowed by an absence of oil contamination.
Field Background
Fig. 1 above displays the location of the BaF field in the Douala basin offshore Cameroon. The operator has been drilling a number of wells in these fields, most of which were development wells. According to the operator’s drilling campaign, three offset wells were drilled with synthetic-based muds (SBMs) and five wells were drilled with HPWBMs in the BaF field. Our reference offset well (Offset Well 3) was the last SBM well, drilled in late 2005.
Operator’s Selection Criteria for HPWBM
On the basis of the historical data of the offset well, approximately 1933 t of oil-contaminated drill cuttings and 37,834 bbl of waste water were generated from drilling with SBM. With past SBM practice, the operator obtained environmental permits that allowed the discharge of untreated synthetic-based wastes from the platforms directly into the ocean. However, there is a strong anticipation that the Cameroonian government will begin placing stronger restrictions on ocean discharges of SBM and oil-contaminated cuttings. If the regulatory agency leans toward a zero-discharge limit, the operator will be liable for the transfer of oil-contaminated drill cuttings to land for any further treatment.
The secondary consideration was that the operator had already used the HPWBM system for shale inhibition onshore in the Peruvian jungle and in Colombia, Cameroon, and Gabon. The system showed success in achieving high shale inhibition, preventing clay and cuttings hydration, and reducing bit balling. The operation was successful, without any hole-related problems. Therefore, when the operator planned to drill the next offshore development well in BaF field, they selected the HPWBM with a saturated NaCl system as an alternative to traditional SBM. This transition has been taking place since 2011.
HPWBM Design
The shale formation is known to act as a semipermeable (selective) membrane because the clay-rich matrix hinders the movement of some solutes. The selectivity of the shale membrane increases with decreasing shale permeability. Therefore, the design of the HPWBM formulation is aimed to form in-situ, effective sealing under downhole conditions, improving the efficiency of the semipermeable membrane. In this work, the HPWBM components contributing to shale stability were sealing polymer, aluminum complex, and NaCl brine. Because of its extremely small particle size, a nanosized polymer sealant provides a mechanical plug for shale pore throats and shale microfractures, while the aluminum complex chemically precipitates inside the pore throats and shale matrix because of the change in pH or the interaction with multivalent cations in the formation. A coprecipitation of polymer sealant and aluminum complex forms a good membrane sealing that imposes a water flow from the wellbore to the formation side. In addition, the HPWBM formulation used the NaCl brine to lower water activity of mud and increase the osmostic gradient, causing the fluid to flow from inside the pore to the wellbore. An increase in membrane efficiency and osmotic pressure differential of the HPWBM led to a significant reduction in the pore-pressure transmission.
One of the technical challenges involving water-based muds is control of the hydration of reactive clays. Clays consist of negatively charged aluminosilicate layers kept together by cations. Clay hydration begins with a surface hydration (a bonding between water molecules and oxygen on clay surface) and ionic hydration (the hydration of interlayer cations with surrounding shells of water molecules). The ability to adsorb water between the layers results in strong repulsive forces and interlayer expansion (swelling). Severe clay hydration and dispersion in water-based mud can lead to poor fluid rheological properties. In the HPWBM formulation, an environmentally acceptable water-soluble clay-hydration suppressant was used in conjunction with monovalent salt (in this case NaCl) to reduce the swelling and dispersion of highly reactive clays by a cation-exchange mechanism. A similar chemical inhibition approach can also be applied to drill-cuttings inhibition.
Drilling Performance Evaluation: Offset vs. HPWBM Test Wells
Offset-Well Review. Well 3 is a J-type directional well. There were two sections (12¼-in. and 8½-in.) drilled with SBM. The 12¼-in. section drilled with 1.25-specific gravity (SG) SBM was the directional drilling, with a final inclination of 68° and an average ROP of 17.5 m/h. The following section (8½-in.) was drilled with 1.16-SG SBM, with an average ROP of 11 m/hr and a final inclination of 90°; then, the 7-in. slotted liner was run to total depth with a gas lift completion. The well’s true vertical depth was 700 m.
Test Wells: HPWBM Achievements. The operator performed a 1-year campaign to evaluate the HPWBM system for offshore drilling from March 2011 to March 2012. Five wells were drilled with the HPWBM system in the BaF field. Here, the performance of HPWBM in the last three wells (6, 7, and 8) is evaluated. In these three test wells, the HPWBM system was employed in the 12¼-in.- and 8½-in.-hole sections.
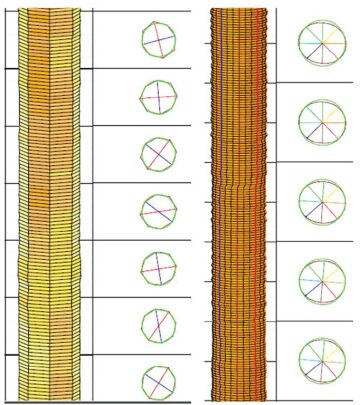
In Well 6, operator review indicated that the 12¼-in.-hole section drilled with the 1.35- to 1.4-SG HPWBM provides a good ROP of 14.6 m/h. The section total depth was achieved in 2 days with no back reaming. Electric logging with a six-arm caliper (Fig. 2) shows no washout, with an average of 12¼‑in. mean internal diameter. Both casing and cementing operations were completed without any issues. Similar findings were also observed in the 8½-in. section drilled with 1.25- to 1.30-SG HPWBM.
The section daily mud report of Well 7 indicated that the cuttings appeared to be very dry and remained integrated. This finding suggests superior clay- and cuttings-inhibition performance of the HPWBM. Additionally, the report indicated that a good hole condition existed when performed back to bottom. As noted in the report, the hole was circulated clean and was confirmed stable by the flow check before tripping out without any noticeable drag.
At the end of Well 7, the 63 m3 of a 1.24-SG HPWBM was transferred for reuse to drill the next well (Well 8). In that well, recycled mud was reconditioned with additives, mainly to increase mud weight to 1.40 SG, and then combined with the freshly formed HPWBM in the active pit. The results show that the HPWBM still maintains desirable rheological properties. The ability to reuse or recycle the HPWBM system provides an added benefit of reducing drilling-mud cost for the operator. The operator was able to decrease the total operational cost by a range of 13 to 30% from the planned budget by use of the HPWBM system. Furthermore, because the HPWBM is an environmentally compliant fluid, the spent mud and drill cuttings can be discharged directly and do not require further drilling-waste treatment.
Conclusions
After the 1-year campaign, well recaps indicated that the HPWBM proved to be an excellent alternative to the invert-emulsion mud for the BaF field. The system delivered high drilling performance and optimum characteristics such as shale stability and clay and cuttings inhibition as well as a high ROP. The operator experienced no wellbore problems. From an environmental perspective, because of the absence of oil contamination, the system eliminated the rig costs associating with drilling-waste management.
This article, written by JPT Technology Editor Chris Carpenter, contains highlights of paper SPE 163502, “High-Performance Water-Based Drilling Fluids: An Environmentally Friendly Fluid System Achieving Superior Shale Stabilization While Meeting Discharge Requirement Offshore Cameroon,” by Anuradee Witthayapanyanon, SPE, Baker Hughes; Jerome Leleux, SPE, Julien Vuillemet, Ronan Morvan, and Andre Pomian, Perenco; and Alain Denax and Ronald Bland, SPE, Baker Hughes, prepared for the 2013 SPE/IADC Drilling Conference and Exhibition, Amsterdam, 5–7 March. The paper has not been peer reviewed.