For oil and gas operators today, remaining competitive means drilling longer laterals with less downtime, while creating the best possible balance of cost efficiencies. Casing flotation devices can help operators achieve these goals as they are engineered to reduce costs and increase efficiencies by ensuring casing reaches the bottom.
In the Appalachian Basin, Northeast Natural Energy (NNE) was challenged to land 17,000 feet of casing in a horizontal gas well with a 9,000-foot lateral while maximizing operational and cost efficiencies.
Running casing to depth in long lateral sections is complex due to excessive drag forces. While conventional casing flotation can reduce drag by creating an air chamber above the float collar that reduces sliding friction by approximately 50 percent, they shatter in large pieces. This creates debris which results in losing a significant portion of pay zone at the toe of the well.
However, by utilizing Nine Energy Service’s Breakthru™ casing flotation device, NNE eliminated the need for a debris trap and shortened the shoe track of the well. NNE gained an additional 20 feet of pay zone without extending lateral length, translating to an estimated incremental gas recovery of $120,000 in addition to improved drilling and completion cost efficiencies.

Over 99% Percent Total Depth Success Rate
Nine’s Breakthru casing flotation device uses an engineered material barrier that disintegrates into small sand-like particles after activation that are then easily circulated out through sleeves, toe valves and float equipment. This effectively eliminates the need for a debris trap, fluid flushes or extra trips to retrieve device pieces, reducing cost and maximizing recovery.
The device also greatly reduces the weight of the casing, which enables the string to reach total depth every time. And, eliminating the two premium thread connections required for conventional flotation subs lowers costs and further improves well economics.
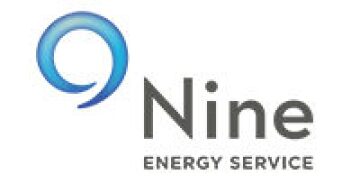