In January of 2020, Corterra Energy, an independent exploration and energy production company with operations in the Midcontinent region of Oklahoma, approached Upwing Energy to analyze some of their unconventional wells to better understand the effect of Upwing’s Subsurface Compressor System™ (SCS) on production and recoverable reserves.
The analysis was conducted with the Upwing Enhanced Production Simulator (ESP), a proprietary in-house analysis tool, which takes in consideration the reservoir characteristics, the SCS operational envelop, the wellbore dynamics and the topside equipment. The tool has been developed and validated over the course of five well trials, including the company’s most recent trial in Riverside Petroleum’s New Albany unconventional shale well with a 5,000-foot horizontal wellbore. The reservoir characteristics of the Riverside Petroleum well are very similar to the selected Corterra wells analyzed below.
The Production and Recovery Challenges of Unconventional Shale Wells
In general, the estimated ultimate recovery of the original gas in place from unconventional horizontal and multi-staged fractured wells is approximately 15 to 20 percent. In addition, the production of these wells is known to drop by 75 to 90 percent in the first few years of the life of the well. Liquid loading in the horizontal section of the well and in the formation have been identified as the major causes of the declining production rates and limited ultimate recovery. It is common practice to install an artificial lift system, such as a gas lift or plunger system to produce these wells, however doing so, only brings the liquids in the vertical wellbore to the surface. The liquids in the horizontal wellbore continue to put backpressure on the reservoir.
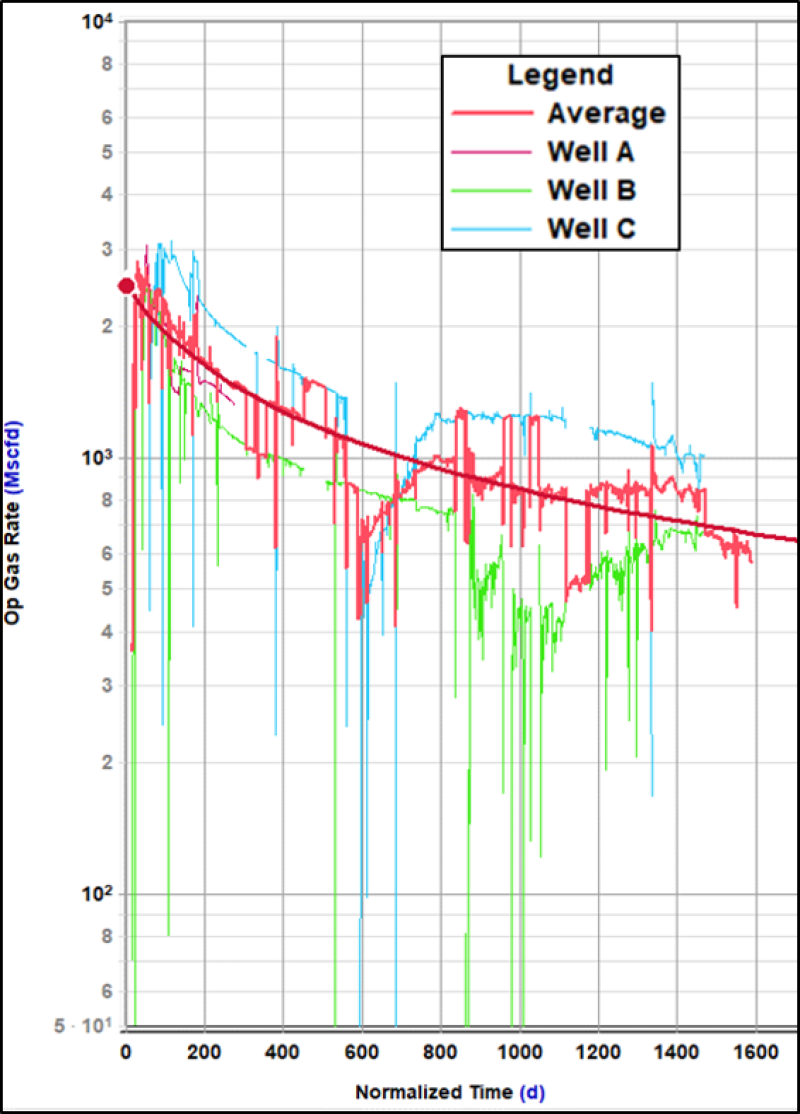
There are many studies published regarding liquid loading in vertical wells. Two commonly quoted liquid loading models were developed by Turner et al. (1969) and Coleman et al. (1991). However, these have proven not to be applicable to horizontal liquid-rich wells. Another study by the University of Tulsa demonstrated the significance of gas velocity in carrying liquids, and characterized flow regimes under different velocities, identifying 20 feet per second as being the critical gas velocity needed to effectively carry liquids along a horizontal well.
The Effect of Subsurface Compression on Liquid Loading
Upwing’s SCS can uniquely solve the combined issues of liquids in the horizontal section of the well and liquids in the formation. Operation of the SCS in a gas well creates a low-pressure zone at the compressor inlet at the bottom of the wellbore, thus lowering the bottom hole well pressure. This drawdown in the wellbore actively induces more gas flow from the formation to the wellbore. With higher gas flow rates and lower bottom hole flowing pressures, the increase in the velocity (e.g. 14 feet per second or above) of the gas stream carries more liquids out of the wellbore, thus removing liquids from the vertical and horizontal sections of the well. Decreasing back pressure from liquid loading results in increased gas production, which in turn accelerates liquid unloading and prevents vapor condensation when exiting the compressor.
In the case of the trial with Riverside Petroleum, to ensure deliquification, a velocity of 29 feet per second was selected as the design point for the compressor and wellbore geometry. The trial resulted in a 62% increase in gas production and a 50% increase in liquid production.
The Corterra Well Simulation Results
Because the characteristics of the reservoir and the completions are similar for all three of the Corterra Energy wells analyzed, the effects of the SCS on production and reserves are similar. The results of Well B are shown below.
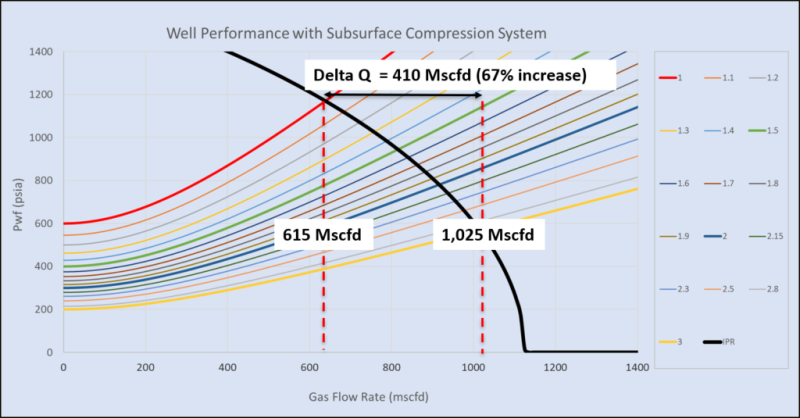
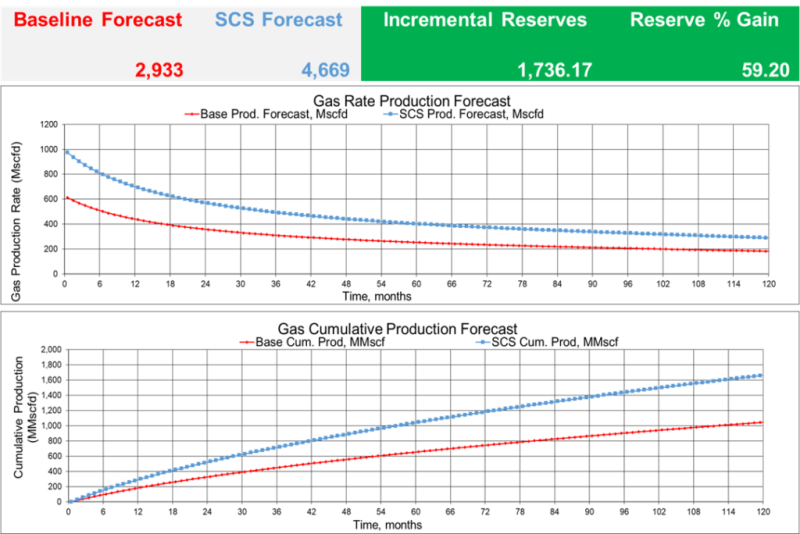
The Topology of the Upwing Subsurface Compressor System (SCS)
The downhole components of the SCS embrace a novel and reliable architecture that eliminates the primary failure points of conventional electric submersible pumps (ESPs). The SCS consists of two main components- a high-speed (50,000 RPM) hermetically sealed permanent magnet motor with magnetic bearings and a hybrid wet gas compressor. These two components are coupled by a magnetic coupling that conveys torque from the hermetically sealed motor to the compressor with no mechanical shaft or seals, so there is no need for a motor protector to isolate the motor from downhole fluids. This “protector-less” architecture eliminates a frequent point of vulnerability for conventional downhole artificial lift systems. A sensorless wide-frequency variable speed drive at the surface controls the motor at high speeds.
About Upwing Energy
Upwing Energy, Inc. (“Upwing”), headquartered in Cerritos, Calif., provides the most reliable, available and retrievable artificial lift technology that increases the production and recovery of hydrocarbons from conventional and unconventional wells. The company is an innovative offshoot of parent company Calnetix Technologies, which is a recognized leader in high-speed rotating systems for a wide variety of industries. For more information, please visit www.upwingenergy.com.
About Corterra Energy
Founded in 2016 and led by industry veterans, Corterra Energy, LLC is an independent exploration and energy production company headquartered in Tulsa, Oklahoma with operations in the Midcontinent region of Oklahoma. For more information, please visit www.corterraenergy.com.
