Saudi Aramco says its Manifa field is an example of how it is combining its technology and innovation capabilities to develop one of the most challenging megaprojects in the history of the company.
Measuring approximately 45 km in length and 18 km in width, the Manifa field in Saudi Arabia is considered the fifth largest oil field in the world. It was discovered in 1957 with first sustained production in 1964. By 1977, 17 wells had been drilled, mostly offshore. Because of poor demand, the field was mothballed in 1984. But in 2006, a grassroots field redevelopment plan kicked off with major capital spending, and drilling and development started in 2010. The field was successfully put back into production in April 2013, three months ahead of schedule, and the field achieved 500,000 BOPD by July 2013.
By the time the field reaches its full potential at the end of the year, the Manifa field will have the capacity to produce 900,000 BOPD of Arabian heavy crude, 90 MMscf/D of gas, and 65,000 B/D of condensate. The project consists of 42 km of causeways, 3 km of bridges, 27 drilling islands, 13 offshore platforms, 15 onshore drilling islands, water supply wells, injection facilities, multiple pipelines, and a 420-MW heat and electricity plant.
Shifting Strategy
As Saudi Aramco aims to push forward from its traditional role as a buyer and consumer of technology to an enabler and creator of new technologies—its new global technology and R&D strategy—the company has introduced several technologies during the development of Manifa.
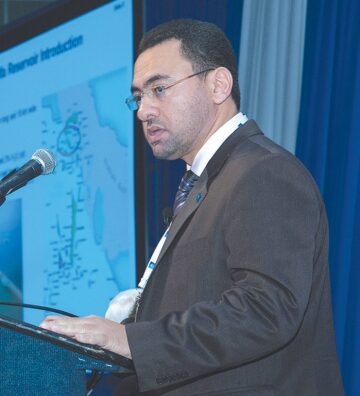
The Manifa crude oil increment has been a monumental achievement in the company’s history in terms of production, technology, and manpower, said Shadi Hanbzazah, supervisor at the Manifa production engineering unit. Saudi Aramco combined onshore and offshore development and a causeway in a single project. Water depths are between 4m and 6m. To adequately cover operations in the field, 27 man-made islands were developed and connected by a causeway. “The field development strategy was aimed to transform the field from being 70% offshore field development to 70% onshore field development through the creation of 27 man-made islands, each the size of 10 soccer fields, connected with 41 km of causeway while 13 offshore platforms were installed for the field’s deeper water locations,” said Hanbzazah.
The field’s geography in the shallow waters of the Arabian Gulf’s fragile ecology required unique, environmentally friendly access solutions involving a novel causeway design linking drilling islands. “We collaborated with both local and international academic institutions to optimize the design of the Manifa causeway,” said Khaled A. Al-Buraik, vice president of engineering and development at Saudi Aramco. “The Arabian Gulf was studied taking into account numerous environmental considerations to minimize traffic in shallow waters and allow natural marine growth. The design mapped and considered coral reef formations and the habitats of marine life.”
Although a major driver for the causeway concept for the Manifa development was to improve project economics, carefully placing the artificial islands on the Gulf also helped ensure a minimum environmental footprint. As a result, the Manifa field became the largest extended-reach hydrocarbon producer project in the world. “Thus, Manifa contains the largest number of extended-reach wells (ERWs) as two-thirds of the wells in the field are ERWs by industry standards, some with a total depth of 37,000 ft, departing beyond 26,000 ft from surface locations,” said Hanbzazah.
The Manifa reservoir has five main reservoir layers. Two of these reservoirs targeted for development contain both heavy oil and relatively lighter crude. “Generally, Manifa crude is quite heavy and sour with API gravity of 29°, 14% H2S in gas, and 3% in oil,” said Hanbzazah.
Production opportunities exist in the presence of formation heterogeneity and a heavy oil layer between the aquifer and the zones above it. “The reservoir has relatively low permeability, randomly distributed baffle zones of mud-lean packstones, and variable shallow marine carbonate facies consisting of carbonate grainstones, some with calcite cementation and minor dolomitization,” he said.
During the development phase of the project, Saudi Aramco developed tailor-made technologies for the field. Five patents were filed, some of which could have international application, according to Saudi Aramco.
Apart from well placement of the long horizontal single and dual lateral wells, another challenge was effective stimulation. In Manifa’s barefoot injector and producer completions, even relatively shallow drilling-induced near-wellbore damage can substantially impede the flow or injectivity. Acid stimulation was required to remove drilling-induced reservoir damage from the overbalanced water-based mud, which uses calcium carbonate as weighting material.
Meeting the Challenges
Another issue the development team faced was the viscosity of the heavy crude layer, which affects the ability of the natural water drive to energize the flow of oil from below. Therefore, peripheral power water injection above the viscous layer was planned for the field to provide pressure maintenance and efficient sweep of hydrocarbons to the producers, said Hanbzazah.
With heavy oil in place, the challenge was to place the horizontal injector well paths in mobile fluid layers as close as possible above the nonproducible heavy oil interface to ensure meeting injection rate targets, thereby providing an optimal sweep of the lighter crude and minimizing bypassed oil, he said.
A Game Changer
One key technology deployed was coiled tubing (CT). Two records were achieved during the development of Manifa. “The records set while achieving a well’s intervention objectives include attaining the deepest CT reach for rigless well intervention at 29,897 ft (9.11 km) measured depth in an extended-reach openhole horizontal power injector well using a CT tractor,” said Hanbzazah. “Also, the first application of real-time logging enabled through a wired motor head assembly via the tractor.”
The intervention objectives were to acid stimulate an open hole completed relatively deep in the reservoir with a total depth of 29,897 ft and an openhole length of 6,697 ft using 2-in. CT with an openhole tractor to perform injectivity/falloff test and to conduct real-time logging for evaluating the reservoir’s injectivity profile. “It was very challenging especially with the depth of the wells,” he said.
Several techniques were applied to extend the lateral extension of CT into the open hole for effective stimulation treatment or to evaluate the effectiveness of the treatment. These techniques include the use of friction reducers or organic solvents to reduce encountered friction and the application of external forces, such as tractors and vibrators. A key challenge was the lack of depth when running holes. “We also faced challenges reaching the required depth as the CT sometimes locked up at shallower depth compared to the required, which was a real challenge,” Hanbzazah said.
Fiber-optic coiled tubing provided the best CT intervention option available. The fiber optic acts as a source of telemetry from downhole tools to the surface in real time, and as a source of temperature measurement known as distributed temperature sensing.
Tools at the downhole end of the CT consist of a bottomhole temperature gauge and a bottomhole pressure gauge for measuring the inside and outside pressure of the CT. A casing collar locator was used for depth correlation and gamma ray for both depth correlation and lateral identification. “Often, a tension and compression sub is included for measuring bottomhole CT tension and compression forces,” Hanbzazah said.
“Technology helped us in cost saving during the development. The plan was to drill 100 to 200 wells in Manifa. Using these technologies enhanced the field’s production and reduced the number of wells for developing the field,” he said.