As a professional scientific discipline, Human Factors Engineering (HFE) is the study of designing equipment and machinery for use by humans. The field comprises a number of technical disciplines that bring specialist knowledge, skills, and techniques to mitigate risks associated with human errors in a number of safety critical industries. Many industries such as aviation and nuclear power have improved process safety by using approaches drawn from this field.
The Society of Petroleum Engineers (SPE) has recently formed the Human Factors Technical Section to build a community of interested parties to identify how this discipline can be broadly applied in the oil and gas industry. The objective is to identify human factors that need to be managed and controlled to help reduce the potential for major incidents. Aside from designing safer equipment and improving safety culture through training and operating procedures, human factors engineering concerns carrying out projects with a special focus on human interaction. Identifying processes in accordance with individuals’ physical capabilities and limitations, as well as decision-making strategies in safety critical situations, serves as a platform to further enhance safe operations.
Identifying the Factors
In July, the SPE held a 2-day summit in Houston with the goal of creating a common understanding of the challenges associated with the broader application of human factors in the oil and gas industry. “We set out to identify opportunities to improve how we consider human factors in the oil and gas industry,” said Ford Brett, chief executive officer of PetroSkills.
The summit resulted in a white paper discussing topics and needs associated with human factors in the oil and gas industry. The paper outlines 10 general human factors risks as follows:
- Leadership and culture
- Perception of risk and decision making
- Communication of risk
- Human factors in design
- Individual and team capacity
- Commercial and contractual environment
- Collaborative and distributed team working
- Workload transition
- Assurance of safety critical human activities
- Investigation and learning from incidents
While none of these risk areas stand as independent, each of these needs attention to improve safety assurance, and the demand is on the oil and gas industry to retain the confidence of society at large. Certain factors such as attitudes, competence, and skills and behaviors of frontline operators, can interfere with consistent, reliable human performance. By looking at the overall process of resource development, the group intends to focus on its various components to alleviate potential failures resulting from human-induced errors.
Human factors issues can, on occasion, be engineered out by ‘pure’ technical solutions (Fig. 1). “Airbags and antilock brakes are examples of these in the auto industry where need for human ‘reaction time’ or ‘decision making’ can be mitigated by technology. But pure technical solutions are rare to solve process problems, human decision making, situational awareness, and limitations and capabilities of workers,” Brett said.
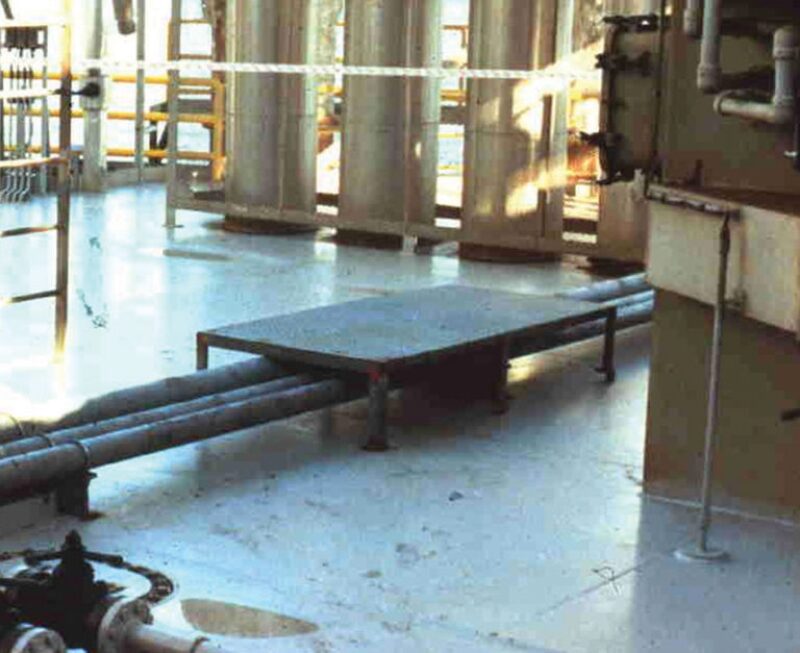
To Err is Human
Regardless of advances in design, people make mistakes. “Humans are not perfect,” said Andrew Dingee, a consultant at BP/Contractor SEMS and chair of the technical section.
Improving risk recognition and decision making is a major area of focus for the human factors working group. From senior executives to frontline personnel, decisions are consistently made of “what to do next.” According to the group’s report, all levels of decision making can be safety critical. Strategic decisions influence the overall condition for safety while those on the frontline have a direct effect on the course of action.
The report defines decision making as involving an entire process including awareness of the situation; making projections; planning courses of action; and, choosing which one to take. It also links decision making to risk perception, which can be influenced by the level of control an individual feels he or she has over a safety situation.
Understanding how groups can influence the decision-making process is also important. Diversity and experience can alleviate problems associated with decision making by one individual. Situations also have a direct influence in the process. Time pressure, poor and/or ambiguous presentation of information can also result in poor decision making.
Designing for Use, Against Errors
“Ultimately, the industry needs error management,” Dingee said. “We need a culture that accepts that humans are not perfect.” From a design perspective, the role of HFE is to develop facilities that can retain full functionality in spite of the potential for human-induced errors. “When mistakes are made, the error is caught and mitigated, and the process continues,” Dingee said.
In many cases, thorough investigations show that deficiency in design or implementation of the interface between people and technology often contributes to the loss of human performance (Fig. 2). To alleviate problems associated with design-induced errors, the technical section calls for critical systems to be designed taking into account the possibility of human error.
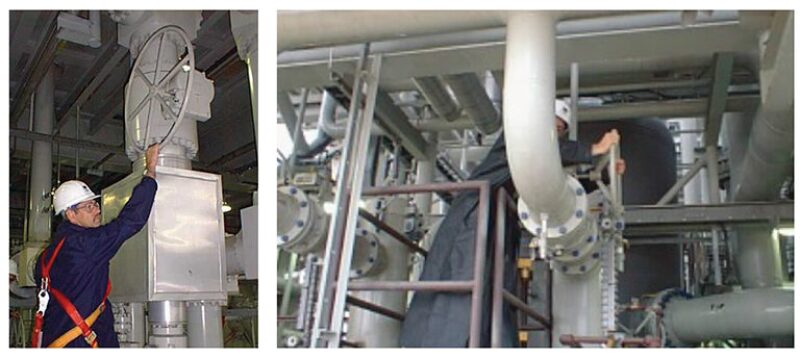
Oil and gas facilities are safer now than before, and the goal of the technical section is not to reinvent the wheel. The ongoing discussion has evolved around looking at what is currently being done; what is not being done; and, what can the oil and gas industry learn from other high hazard industries, such as aviation and nuclear power.
Crew resource management (CRM) is a major focus of the technical section; although this has improved risk mitigation in the airline industry, it presents certain challenges within oil and gas.
CRM provides very clear and deliberate understanding and analysis of each individual’s role under all operating circumstances including crisis situations. The roles are well defined and developed through a practiced understanding. Standardization in the airline industry provides benefits to this level of decision making that is not readily available within the oil and gas industry. “Every gas plant is different,” Brett said. “Drilling and production are dynamic operations, and the design and process of a specific development will change from early to late in the life cycle of resource development.”
Learning from past mistakes is an important topic for the discussion on human factors. What is described by many as a “blame culture,” the industry currently operates on the assumption that most mistakes can be reduced to human error. A closer focus on human factors is a means to provide better designs and improved process management to create systems that continue to rely on human control and yet do not completely disrupt when errors are introduced. “We are losing out on learning from the near misses,” Dingee said. Close observation and better reportage of incidents could help drive the human factors initiative in the upstream oil and gas industry.
Looking Ahead
Process safety management and human factors are broad components. By organizing a community of technical specialists, the Human Factors Technical Section will examine the possibility of adopting methods and views that have aided other industries outside of the oil and gas industry. The attention is on finding elements that are currently applied in oil and gas, but perhaps not as broadly as they could be applied. “We want to understand what we know and what we do not know to determine the best areas for further research,” Brett said.
As an industry, the upstream oil and gas industry will continue to improve over time. “It is very clear that there are a number of things we can do immediately to improve the way we work,” Brett added.The technical section plans to meet its goals by identifying the low hanging fruit within HFE. Other contributions will include further systematizing the way teams work within the industry and optimizing decision-making processes, especially in emergency situations.
According to Dingee, standardization of human factors aggregation is an important need within the industry. From one company to the next, implementation of this discipline may appear misaligned. “We want to develop a solid foundation within SPE that provides some basic definitions for human factors issues within the industry, and to formulate basic philosophies to start addressing these in the workplace,” he said.
The technical section is in its early phase, and the group’s knowledge gathering has identified several areas to focus on for specific solutions. “We want to bring the right people together to accelerate that conversation to essentially move the industry to the future faster,” Brett said.
Visit www.spe.org/network/technicalsections to learn more about the Human Factors Technical Section.
HFE in Major Capital Projects
The life cycle of major capital projects in the oil and gas industry can span over several years. For a major operator, the goal of HFE is to focus on the application of human factors knowledge to the design and construction of systems. Ensuring that facilities are built in a way that optimizes the human contribution to production can minimize the potential for design-induced risks to health, personal or process safety, and environmental performance.
According to the International Association of Oil and Gas Producers (OGP) Recommended Practice RP 454 “Human Factors Engineering in Projects” (2011), the process involves five stages as follows:
- HFE screening
- HFE design analysis
- HFE design validation
- HFE support to startup
- Operational feedback
The objective of this practice is to identify unusual HFE risks or opportunities very early in the project life cycle, ideally before front-end engineering.
The overall nature of HFE design requirements is twofold. According to RP 454, prescriptive and goal-oriented requirements need to be addressed in fundamentally different ways(Fig. 3).
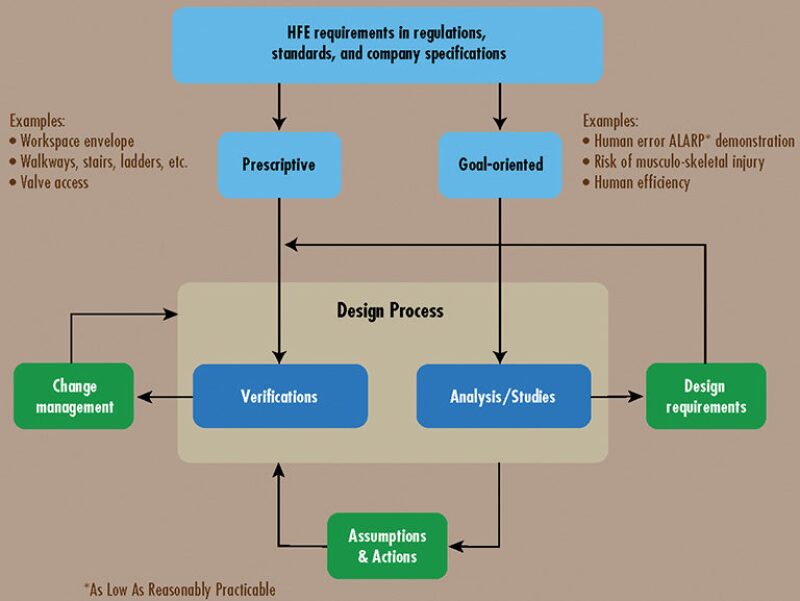
Prescriptive requirements, such as technical specifications, optimal positioning of valves, or the sizing and location of access platforms, and other design features, are typically met through compliance with existing technical standards. In contrast, goal-oriented requirements mandate a particular achievement such as bringing human error to an acceptable level during valve operation or ensuring that maintenance activities are carried out within specific time limits. These design requirements call for analysis using structured tools and methods to develop a solution that meets the goal. Goal-oriented design requirements can demand more resources to develop suitable technical solutions.
For Further Reading
SPE 156736 Lessons Learned Applying Human Factors Engineering in Capital Projects by Alfred Seet and Ron McLeod, Shell.
The Human Factor, Process Safety and Culture White Paper. SPE Human Factors Technical Section.
Report No. 454. Human Factors Engineering in Projects. International Association of Oil and Gas Producers. www.ogp.org.uk/pubs/454.pdf.
Report No. 460. Cognitive Issues Associated With Process Safety and Environmental Incidents. International Association of Oil and Gas Producers. www.ogp.org.uk/pubs/460.pdf.