Every drilling engineer’s dream would be to deliver more complex well profiles and smoother, more consistent boreholes in less time—ideally in a single run—eliminating the need to trip out of hole. The problem is that conventional positive displacement motors (PDMs) and rotary steerable systems (RSS) both exhibit limitations in different drilling scenarios.
Industry Challenges and Needs
Downhole motors, for example, are capable of delivering reliable, very high dogleg well profiles. However, because the drillpipe alternates between rotating and sliding, rates of penetration (ROPs) are low and hole quality is tortuous, increasing the potential for stuck pipe.
On the other hand, fully rotating RSS deliver smoother wellbores at higher ROPs than PDMs, reducing drilling time by as much as 50%. However, the maximum build rate of a typical RSS is only 6 to 8 deg/100 ft, and much lower while drilling soft formations, enlarged holes, or hard interbedded stringers at high angles to the wellbore. For well profiles with high build rates, an RSS may be used for the vertical and lateral sections while motors must be used between the kickoff and landing points. This requires at least three bottomhole assemblies (BHAs) and multiple trips out of hole.
To reduce risks while saving rig time and costs, drillers would prefer the hole quality and performance of an RSS combined with the high dogleg capability and steering assurance of a PDM.
To meet operators’ growing needs both in unconventional shales and difficult formations, Schlumberger developed the PowerDrive Archer high build-rate RSS. In a single run, the technology can deliver well profiles previously possible only with motors. By improving borehole quality and reducing tortuosity, it minimizes the risk of stuck pipe and facilitates the deployment of casing, sleeves, and completion equipment (Fig. 1 above). It can perform openhole sidetracks and drill deeper before kickoff than other RSS, maximizing reservoir exposure and increasing potential production.
Description, Development, and Deployment
The high build-rate RSS represents a breakthrough in steering control. The RSS has been in use since the late 1990s. However, it could not deliver the 8-to-12-deg/100-ft build rates necessary for typical well profiles in unconventional shale plays. Due initially to rapid increases in shale drilling, Schlumberger began development in 2007 of a new RSS aimed at roughly doubling the maximum build rate of previous tools.
The new system is a hybrid, combining proven technology from push-the-bit and point-the-bit RSS (Fig. 2). In a conventional push-the-bit RSS, external pads push against the borehole wall, forcing the bit in the desired direction. The conventional steerable motor uses an external bend and the point-the-bit RSS uses an internal bend that misaligns the tool relative to the borehole axis. Combining the two systems provides much higher dogleg capability than either one alone. The new RSS consists of a reliable electronic control unit and mechanical steering unit. All external components rotate fully with the drillstring. In steering mode, electronics hold a rotary valve geostationary, diverting about 4% to 5% of the mud flow to a set of internal pads, which push on the inside of a stabilizer sleeve instead of the borehole wall. The sleeve is hinged on a universal joint, which pivots and points the bit in the desired direction. The degree of deflection is controlled by a mechanical strike ring, and held electronically in a constant direction for as long as necessary.
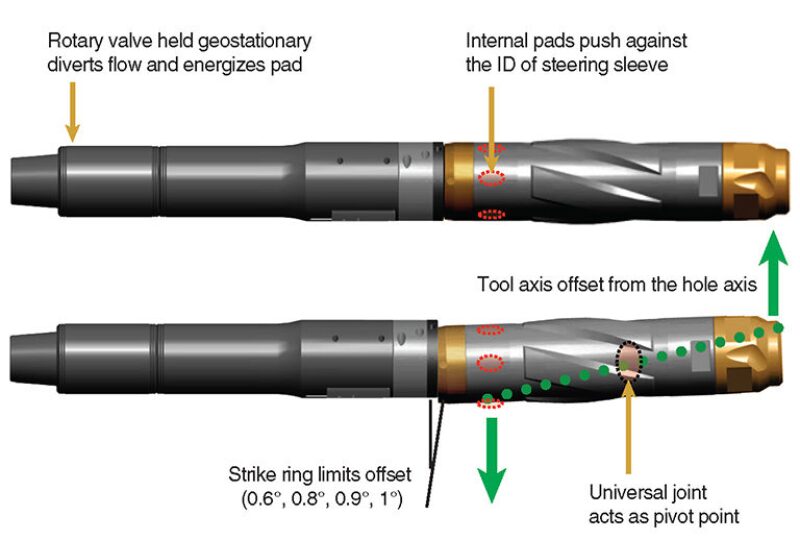
Field trials began in 2008 and underwent two stages of testing. Initially, field tests focused on delivering higher build rates than before. However, subsequent testing was necessary when it became clear that the hybrid steering system required specialized bits and fatigue management for BHAs rotating through much higher doglegs. The hybrid RSS had to be treated not simply as a “tool,” but as an engineered “system” of bits and BHA design, or it could not ensure consistent reliability and optimum performance in different formations and hole conditions.
Using the Smith Bits IDEAS integrated drillbit design platform, engineers simulate bit behavior as part of the system—drillstring, BHA, and RSS—under a variety of actual drilling conditions. Engineered bits designed for the high build-rate RSS can also be optimized to improve ROP and durability in specific applications and fields. To avoid twisting off or wearing out BHAs as they rotate through aggressive curves, a finite element analysis and a detailed strain-based fatigue study were performed to predict the run life of all components under high build rates. A unique fatigue management system tracks the actual build rate in real time and compares it with a fatigue model, thereby reducing risk and extending BHA life.
During field trials, the new RSS delivered build rates as high as 17 deg/100 ft in some cases. After 4 years, 6,000 hr and 138,000 ft of drilling, and testing and validation in 100 wells in North America, Africa, Asia, and the Middle East, the system was officially commercialized in March 2011.
Applications and Case Studies
Primary applications for the new RSS technology include wells that require higher quality holes along with build rates comparable to downhole motors, such as horizontal wells in unconventional reservoirs, and wells that require greater dogleg assurance than other RSS can provide, such as openhole sidetracks or unconsolidated formations. It can also be used to redesign well profiles by reducing inclination through unstable formations in the shallower section and pushing the kickoff deeper, thereby minimizing drilling risks and costs. Because well profiles can be delivered in a single run, operators also reduce health, safety, and environmental risks associated with equipment handling and multiple trips out of hole.
Case study: Unconventional shale reservoirs in the US. Cimarex Energy had drilled four horizontal wells in the Woodford shale using PDMs. To reduce wellbore tortuosity and save time, the operator used the fully rotating, high build-rate RSS to drill the 8.75-in. curve with an 8-deg/100-ft dogleg severity and the 4,353-ft lateral to total depth (TD) in a single run. Tortuosity reduced by 20%, ROP increased by 80%, and the company saved a total of 10 days compared with motors. An operator in the Eagle Ford shale increased ROP by 85%. A Cotton Valley operator reduced drilling time from 8 to 4 days, and a Marcellus operator increased ROP by 170%.
Case study: Deepwater field, unconsolidated sands in Asia. An operator in Asia drilling multilateral wells in a deepwater field with a conventional RSS was unable to maintain long horizontal well trajectories in geological “drop zones” because of extremely unconsolidated sands. Directional sidetracks or motors were necessary to reach TD. Using engineered bits and specially designed BHAs, the new hybrid RSS successfully drilled six laterals with complete directional control within 1 to 2 m of the reservoir boundary, even at ROPs of 1,000 ft/hr. The operator saved 4 days and USD 4.5 million. For the first time, the operator was also able to perform efficient openhole sidetracks to target bypassed attic oil, potentially adding production worth several million dollars.
Case study: Well profile redesign in the Middle East. An operator in the Middle East had planned to kick off from vertical in the 12.25-in. section. However, that would require drilling at an inclination through an unstable zone. By choosing the high build-rate RSS, drillers redesigned the well to reduce the angle through the 12.25-in. section, push the kickoff deeper, and deliver a higher dogleg in the 8.5-in. section. The operator drilled the first well at a conservative build rate of 7.6 deg/100 ft for 846 ft, reaching TD in 25.8 drilling hrs. The second well achieved a more aggressive 11.2 deg/100 ft for 742 ft in the 8.5‑in. section, reaching TD in a single run in 15 hours. Shortening the 8.5‑in. section saved almost 700 ft of liner, 2.5 days of rig time, and approximately USD 125,000.
Case study: Complex well profile offshore Thailand. To increase production in its Bualuang field, Salamander Energy needed to drill a complex directional plan with a longer than usual horizontal section. Because of shallow kickoffs, high doglegs, and soft formations, previous wells had used PDMs. However, torque and drag modeling of the current profile showed that after 2000 m measured depth, no slackoff weight would be available to slide the motor to achieve the build rate required to hit the target. To improve hole quality, reduce friction, and achieve the necessary dogleg severity, Salamander deployed the new hybrid RSS with a multifunction logging-while-drilling tool. Drillers built inclination from 13 to 90 deg while turning from 124 to 355 deg, landed as planned 1.5 m below the upper reservoir boundary, and drilled to TD in a single run while increasing ROP by 50%.
Future Plans
The high build-rate RSS drills 8⅜-in. to 8¾-in. hole. Currently, development and field testing are under way for tools for additional hole sizes, each of which have different requirements.
For more information, please go to www.slb.com/archer.