The Tunu giant gas field is in the Mahakam region of the South China Sea. Because of the maturity of the field, the producing layer has moved from the deep zone of consolidated sand into the shallow zone of unconsolidated sand. Hydrocarbon production from the shallow zone is unmanageable without primary sand control downhole. In this paper, a new type of sand-consolidation low-viscous binding material, based on a combination of inorganic and organic components, is presented.
Introduction
Tunu produces almost 40% of total gas production in the Mahakam region.
×
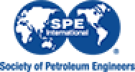
Continue Reading with SPE Membership
SPE Members: Please sign in at the top of the page for access to this member-exclusive content. If you are not a member and you find JPT content valuable, we encourage you to become a part of the SPE member community to gain full access.