The number of subsea wells has increased steadily to more than 5,500 by the end of 2012. Unfortunately, because of their location in deep water, interventions in subsea wells have typically required drilling rigs, and operators have been reluctant to perform interventions on these wells. Cost-effective riserless light well interventions (RLWIs) are crucial if subsea operators are to realize the full potential of 50% oil recovery (or more) from their subsea fields.
Introduction
Traditionally, subsea intervention has required a deepwater drilling rig to be freed from the drilling schedule and mobilized to the subsea wellsite. Then, a riser is connected to the subsea well, allowing electric-line, coiled-tubing, or heavier pipe-conveyed interventions. These types of operations are challenging to schedule, time consuming, and costly and can have high risk. With this combination of factors, operators often decide that costs and potential risks of an intervention to improve production are too high and choose to forgo this work on an adequately producing well with no operational problems. Thus, recovery factors in subsea wells are much lower compared with recovery rates of dry-tree, platform-based wells.
RLWI
RLWI is run from smaller, dynamically positioned light-well-intervention vessels instead of large workover ships. RLWI reduces costs and improves scheduling flexibility, thereby reducing barriers to performing subsurface well interventions and helping subsea operators improve recovery rates.
The key to the low cost of RLWI is that the subsea well-control package (or “subsea stack”) is deployed subsea as a single lift. Once landed on the subsea tree, wireline tools are deployed in a subsea lubricator through open water from the vessel down to the subsea stack. The electric line runs through the open water rather than inside a riser from the surface. On top of the lubricator pipe, a pressure-control head is connected to avoid spills. Fig. 1 shows the combination of technology and services used to perform an RLWI.
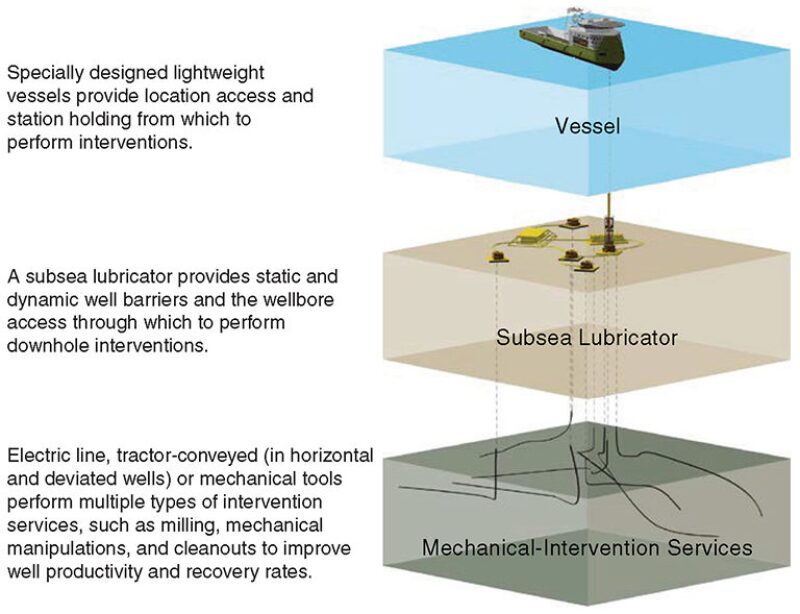
In addition to eliminating rig-rental costs, mobilization and rig up/down is faster, and thus the intervention process naturally has less nonproductive time. The ease of operations and light weight of the equipment provide a further cost savings because fewer people are needed. One intervention study showed that RLWI was accomplished at 50% of the cost of conventional interventions.
In 2000, Statoil decided a new solution for subsea/subsurface interventions was needed and began exploring RLWI. As the technology started to be used regularly and the benefits became obvious, Statoil challenged service providers to develop the technology and capability further. Some service providers accepted the challenge and began developing a new set of tools that allow rigless and riserless running. Since then, more than 2,000 RLWI operations have been performed with excellent results. For a discussion of three case studies involving RLWI, please see the complete paper.
Types of Interventions Performed by Use of RLWI
Over the last few years, new technology has greatly expanded the scope of work that can be performed on electric line. Thus, far more than running production-logging tools or perforating can be accomplished with RLWI. These additional operations include milling, clean-out (Fig. 2), and surveillance services.
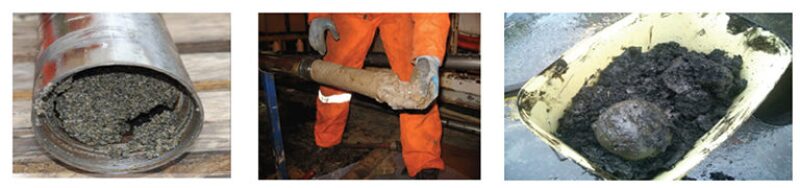
New Technology Solves Old Problems
Setting Plugs and Bridge Points Without Explosives. The new mechanical stroker tool is designed to provide a force of up to 33,000 lbf by means of a bidirectional hydraulic actuator. Where even higher forces are required, plugs can be set with the add-on electric/hydraulic setting tool. This provides a force of up to 55,000 lbf and eliminates the need for explosives. To set or pull the plug, special tools and adapters are mounted on the actuator piston. Operations are managed and monitored from the surface and initiated once the setting tool has positioned and anchored itself. The ability to perform high-precision interventions and to do so in a nearly nonintrusive manner, eliminating the need to kill the well, is critical in many offshore scenarios.
Retrieving a Bridge Plug Obstructed With Debris. A pulling tool has been modified to overcome a specific problem in which debris collects on top of the fishing neck of a downhole bridge plug. Running on electric line and using a specially modified nozzle, the electric-line suction cleaning tool enters the fishing neck of the device. The suction from the tool removes the debris and lets the pulling tool engage fully. The mechanical stroker tool then engages the anchors and pulls the plug in a single run.
Well-Cutting Services Without Use of Explosives. A new well cutter was introduced in 2012 that provides an efficient, nonexplosive option for cutting drillpipe, liner, tubing, and casing. This is especially important when simultaneous operations are being conducted and it is difficult to shut down the rig for the radio silence required when using explosive cutters. The tool uses a rotating head to grind the pipe incrementally, which helps prevent shavings and allows the pipe to be cut in compression, a major advantage over current centrifugal knife-cutting technology. With the smooth/beveled surface the cutter produces, a polishing trip with drillpipe may be eliminated, again saving rig time and increasing operating efficiency.
Surface Readouts Provide Real-Time Feedback. Previously, there was only one-way communication to the tool. Now, real-time data from the tool on the conditions and operations downhole are possible. This allows confirmation that the planned activities have occurred.
RLWI Operations Proved Safe in 89% of Subsea Wells. With the recent world record of performing RLWI on electric line at a water depth of 1216 m (nearly 4,000 ft), RLWI operations have proved safe to perform in 89% of subsea wells worldwide and in 85% of Brazilian subsea wells.
Cable-Simulation Software Mitigates Concerns About the Effect of the Current in Open Water. During riserless offshore well interventions, the intervention electric line is exposed to the currents in the open water between the ship and the subsea lubricator system; these currents can occur in different directions and magnitudes at different depths.
The forces that act upon the electric line will, through the internal forces in the cable, effectively act as an upward lifting force on the tool string inside the well, which may require modification of the toolstring (e.g., add a tractor to pull the tools in the well). However, simulation software has been developed to model the current forces and ensure safe operations.
A typical offshore electric-line cable is used for the stimulations, and the simulations are based on a discretized model of the electric line. The electric line is divided into N cylindrical sections of constant mass and variable length. From basic dynamics, a second-order differential equation in 3N variables can be derived. This is equivalent to a first-order system in 6N variables. In looking for an equilibrium solution for the system, one can use the overdamped case. This leads to a reduction to a first-order differential equation in 3N variables. When solving the equations, with a standard Runge-Kutta method, the shape of the electric line and the internal forces along the entire electric line can be calculated. The force terms in the equations come from the drag forces induced by the current on each electric-line section, and from the gravity, buoyancy, and internal forces in the electric line. The drag force is estimated by use of the crossflow principle.
Given a current profile and the water density as a function of depth, the internal forces of the electric line and the upward force, exerted by the electric line at the top of the lubricator, can be calculated. The hydrodynamic forces acting on the cable are estimated with the crossflow principle, and the simulation model seeks only the final steady-state equilibrium, with no attempt to include the time history. Thus, the software can help in planning well-intervention jobs, such that the upward force at the wellhead and the wire-line tensions remain within a safe envelope.
Additional Benefits of RLWI vs. Conventional Intervention
There are many additional benefits of using RLWI over conventional intervention. These include inherently safer operations (because of the light weight of the equipment, fewer people and lifts are needed), a smaller physical footprint, a smaller carbon footprint, and faster mobilization.
Because there is no riser back to the surface, there is no pathway for hydrocarbons to migrate to the surface in an uncontrolled incident, such as occurred in the Deepwater Horizon disaster. This provides a safer work platform above the well and avoids the need for surface flaring and hydrocarbon management on the back deck. During uncontrolled situations, one needs only to cut the electric line and not the pipe. In addition, if a blowout occurs, it is easier to control and shut in with RLWI than with conventional blowout-preventer sealing against pipe. In both cases, RLWI provides a more-robust and certain solution to shutting in an uncontrolled well.
The Norwegian Petroleum Safety Authority, in conjunction with Statoil, performed a study of injuries that occurred during workovers and drilling from 1992 to 2012. With the onset of electric-line and RLWI operations and the abandonment of snubbing operations, the number of injuries began to decline in 2000. This sharp downward trend continued as mechanical electric-line services were introduced to the marketplace and the frequency of use increased (Fig. 3).
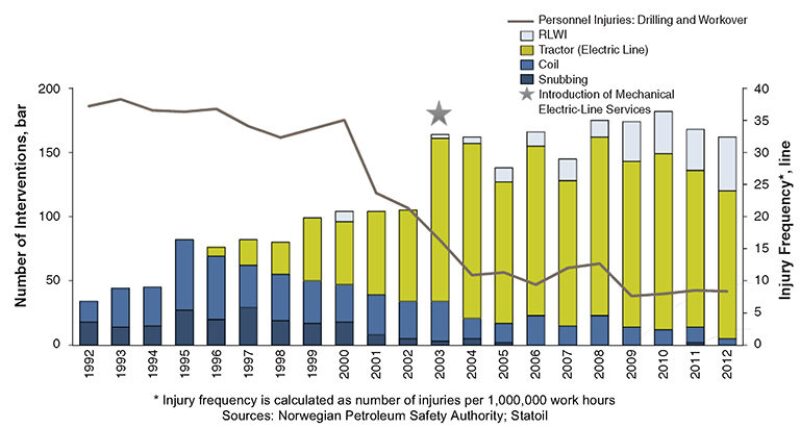
This article, written by JPT Technology Editor Chris Carpenter, contains highlights of paper OTC 24367, “Improved Recovery Rate in Brownfield Subsea Wells Using Riserless Light Well Intervention,” by O.E. Karlsen, SPE, B. Morrison, SPE, and P. Maciel, SPE, Welltec, prepared for the 2013 Offshore Technology Conference Brasil, Rio de Janeiro, 29–31 October. The paper has not been peer reviewed.