The advent of shale-gas production onshore North America, the resulting overhang of gas supplies, and the downward pressure on gas prices have led operators to consider the possibilities of liquid-natural-gas (LNG) liquefaction plants for the export of LNG from coastal locations to international markets. Several proposals for onshore liquefaction relate to the conversion of existing LNG regasification sites. The paper assesses the technology implications of migrating LNG floating production, storage, and offloading (FPSO) concepts to inshore service.
Market Context
The energy markets have seen a remarkable evolution in gas developments driven by a number of factors including the relative abundance of this energy resource and its global availability, flexibility in use, and low carbon number. According to the International Energy Agency (IEA), gas will increase its share of the global energy mix from 21% in 2009 to 25% by 2035.
Against this backdrop, the shale-gas revolution in North America has already led to gas self-sufficiency, with North America poised to be a net exporter by 2016. According to the IEA, the introduction of horizontal drilling, hydrofracturing, and resource targeting technologies has led to a 27% increase in natural-gas production, from 2005 levels to 23 Tcf in 2011 (Fig. 1). A further increase of 44% from this 2011 level is foreseen by 2040. US natural-gas production has outpaced growth in demand by a ratio of 2:1 since 2005, leading to downward pressure on natural-gas prices.
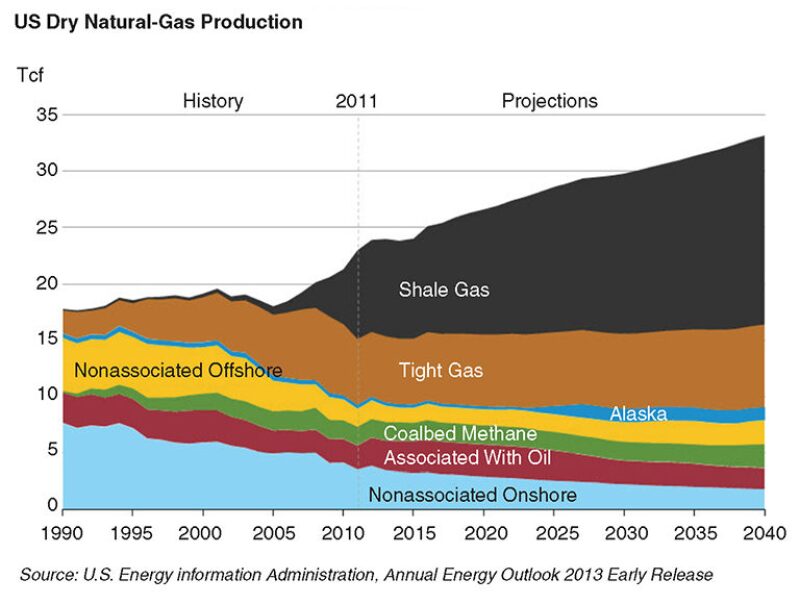
These factors have prompted owners of existing LNG regasification terminals to sense a shift in the demand/supply balance, and to seek approval to install liquefaction facilities for export of LNG. By the end of May 2012, 15 applications had been submitted to the US Department of Energy for export authorization, amounting to a staggering 145 million t/a of capacity.
The sweet spot for floating liquefaction units lies precisely in the greenfield phase of the LNG-export scenario. For greenfield developments, the atshore or inshore deployment of floating LNG (FLNG) can offer interesting advantages over its onshore counterpart. These include potential for faster permitting, a faster construction schedule, and significant potentials for standardization and redeployment.
Concept
The concept envisages the liquefaction unit along with feed-gas pretreatment installed on a barge or on the deck of a ship-shaped vessel located atshore or inshore coastal waters. The Gulf of Mexico coastline and offshore British Columbia are typically contemplated locations for FLNG facilities. Feed gas will be sourced from these pipeline grids, which will transport shale gas after undergoing appropriate treatment (gas conditioning, dehydration, and dewpointing) at intermediate gathering locations.
The supply of feed gas to the FLNG unit will require a spur line from the pipeline grid. The feed gas will be compliant with pipeline transportation specifications, which vary somewhat from transporter to transporter. In practice, the composition of the gas will vary through the operational life of the pipeline grid, depending on aggregate composition of gas from the contributing gas fields or resource plays. However, the carbon dioxide (CO2) and hydrogen sulfide (H2S)/sulfur content, the water dewpoint, and the hydrocarbon-liquids content in particular are expected to be constrained to within the specification limits set by the pipeline transporter.
There are two feasible development concepts that may be considered for deployment of the FLNG unit, driven by nearshore bathymetry and metocean environment factors. In the first of these, shown in Fig. 2, the FLNG unit is moored at shore or portside in protected waters against a jetty/wharf accessible from the shore facilities by a connecting trestle. In this configuration, the incoming spur line from the grid is routed on the trestle and connects to the topside of the FLNG unit. The jetty also serves to moor the LNG trade carrier as it visits to receive its LNG cargo.
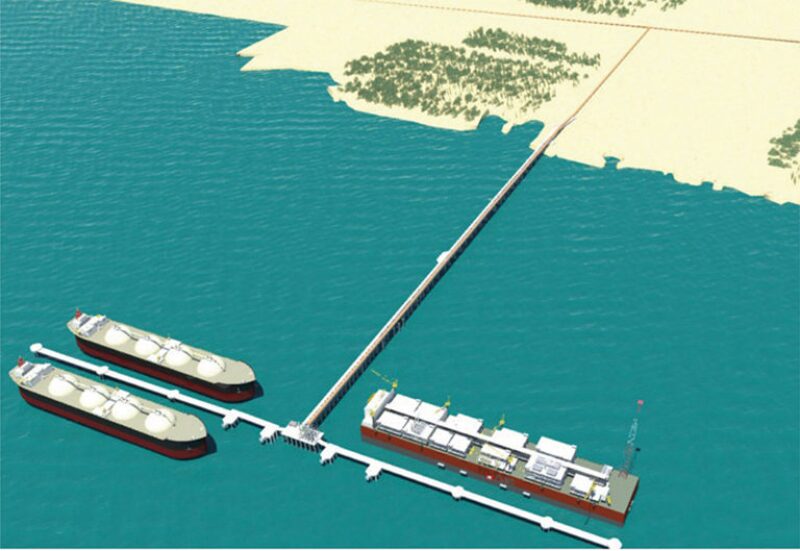
In the second concept, the FLNG unit is located in inshore waters, but 3 to 5 miles from shore. Several reasons could drive selection of this configuration, including poor or unstable bathymetry at the shore line, which then requires significant dredging operations to cut and maintain the channel for arriving LNG carriers, and to provide the 15-m keel-clearance depth required at the jetty location. In case jetty construction is ruled out, a variation to the inshore option is a site-moored FLNG vessel, with product offloading to LNG trade carriers in a side-by-side configuration by use of mechanical loading arms (Fig. 3 above).
The severity of the metocean characteristics will determine the choice of the floating substructure for each option. At the atshore location, the selection of a barge could be a feasible option. The barge would support the topside processing facilities and will also integrate the storage tanks required for the LNG, liquefied petroleum gas (LPG), and condensate.
In the inshore scenarios, the choice for the floating substructure is likely to be a ship-shaped vessel, recognizing the more arduous metocean conditions expected, and the need to manage vessel motions to ensure that topside systems are able to operate within permissible envelopes.
Topside Processing
Topside processing consists of feed-gas preparation followed by LNG liquefaction. The extraction of LPG and condensate is to an extent integrated with the precooling steps associated with the liquefaction step, depending on the generic configuration of the process. The tighter the integration, the more efficient the LNG scheme.
The topside systems are typically located on a plated deck platform approximately 3.5 m above the vessel deck. The storage tanks for LNG, LPG, and condensate are located below deck. The living quarters are located near the bow of the FPSO upwind of hazardous areas.
Feed-Gas Preparation. The acid-gas-removal unit (AGRU), the dehydration unit, the mercury-removal unit, and the natural-gas-liquids (NGL)/condensate fractionation are core elements of the feed-gas preparation section. The AGRU-absorber and the NGL-fractionation systems must be designed to perform satisfactorily under vessel motions. Among other specifications, the feed gas must be treated to remove CO2 down to 50 ppm, and water specification leaving the dehydration unit needs to achieve a maximum of 1 ppm. Shale gas, when delivered by a transporter through the pipeline grid, will have its CO2, moisture, and hydrocarbon- dewpoint levels adjusted to conform to the prescribed pipeline specifications.
Liquefaction Technologies. The core of the processing system is the LNG liquefaction block, for which there are several candidate technologies, most of which are proprietary offerings. Several alternative liquefaction cycles are available. The front-end engineering and design methods appear to have demonstrated that there are no “show stoppers” from a technology standpoint for the first field application of an FLNG unit. Nevertheless, as might be expected, these evaluations have been specific to the metocean environments and development-field parameters applicable to the respective deployments. What is increasingly evident is that technology selection for LNG liquefaction is also driven by the design capacity of the FLNG unit.
For a discussion of the influence of design capacity on the choice of technology, please see the complete paper.
Liquefaction-Technology Selection. It is clear that selection of the right technology for North American FLNG applications will depend on a number of factors. Capacity of the liquefaction plant is a key determinant of choice of liquefaction cycle, along with the efficiency and specific power consumption. In addition to these, several other criteria are also important in selecting the right technology (please see the complete paper for more details).
The choice of liquefaction capacity, and any phased buildup to the ultimate capacity, will be driven by commercial considerations. Once this commercial envelope is determined, then the choice of the number of trains, and the technology selection, can commence. As with an onshore installation, it is important to recognize the influence of economies of scale, given that costs of the jetty, the hull, and product storage represent fixed and near-constant cost elements at any capacity point. Following this logic, higher capacity levels are desirable, as long as this does not imply a divergence from contemporary design experience. Given the more benign metocean environments anticipated in inshore waters at locations of interest in North America, it is feasible to consider capacities at or near 3.6 million t/a as representing the top end of the capacity envelope. If the capacity is configured as multiple trains, then availability risk is reduced because of the smaller sizes of equipment, and the more-predictable influence of motions on system performance.
On the other end of the scale, lower-end capacities can also be considered, incorporating technologies more suitable to small-scale and midscale applications. Capacities as low as 0.5 million t/a may be considered for monetization of pipeline-grid gas.
Storage and Offloading
Proven proprietary tank configurations are illustrated in Fig. 4. Tanks with storage spheres extending above deck are less suitable for deployment at LNG process facilities. Membrane-type containment tanks, in the context of LNG FPSO applications, have a propensity for sloshing because of vessel motion. Sloshing can generate high dynamic loads and impact pressures, which can impair the containment system, the hull, and the pump tower in the tank. The prismatic tanks are inherently superior to the membrane-type tanks with respect to sloshing of the LNG in partially filled tanks. However, the anticipated low-to-moderate severity of motion at either the atshore or onshore locations reduces sloshing in membrane tanks as a risk issue. In addition, the proprietors of the membrane containment technology have now developed a design that addresses the sloshing issue by adopting a twin-row arrangement.
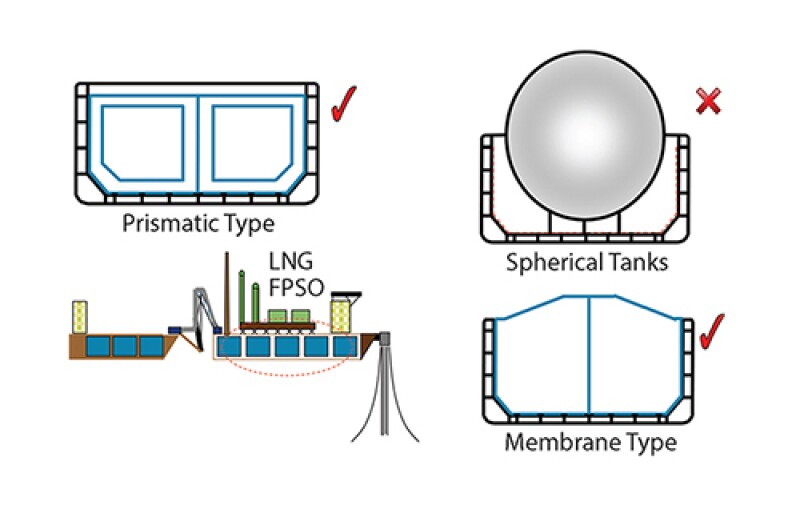
LNG offloading from the FLNG unit will be accomplished with jetty-installed mechanical loading arms, which have been in use at onshore terminal jetty heads for several decades. These loading arms are suitable for significant wave heights of 2.5 m, which should ordinarily provide a high availability for loading at the atshore location.
Pathfinding Economics
Preliminary economics have been carried out for an FLNG deployment where a 460-MMscf/D gas feed rate will produce approximately 3.0 million t/a of LNG. Industry figures suggest FLNG capital expenditures (CAPEX) range from USD 700 to more than USD 1,000 per t/a LNG capacity. Trestle/jetty costs are notionally estimated at USD 150 million and spur line from grid at USD 20 million, respectively. On this basis, the outlay on the FLNG vessel, topside, spur line, and export jetty is expected to be approximately USD 3 billion (at the top end of the FLNG CAPEX range). LNG shipment rates assumed for conventional trade carriers are based on current rates, and typical tolling rate is assumed for regasification terminals (required for LNG vaporization and delivery to the European grid). For a detailed presentation of these economics studies, please see the complete paper.
This article, written by JPT Technology Editor Chris Carpenter, contains highlights of paper OTC 24091, “Development Options for North American LNG Export: The Merits of Inshore-Deployed FLNG for Liquefaction of Onshore Shale Gas and Examination of Principal Technology Drivers,” by Joe Verghese, WorleyParsons Europe, and Nancy Ballout, WorleyParsons Houston, prepared for the 2013 Offshore Technology Conference, Houston, 6–9 May. The paper has not been peer reviewed. Copyright 2013 Offshore Technology Conference. Reproduced by permission.