A high-pressure/high-temperature (HP/HT) exploration field in Block PM on the northern side of the Malay basin, Malaysia, is notorious for a steeply rising pressure ramp, narrow drilling-operation window (only 0.5 to 0.6 lbm/gal in the 14¾ and 9½-in. sections), and interbedded sand/coal and shale formations. Block PM is still in the exploration-and-appraisal stage; therefore, petrophysical information is limited. Well SBD-2 was the second attempt to reach and cross the F and H sands. Formation-pressure-while-drilling (FPWD) and managed-pressure-drilling (MPD) technologies were applied to drill this well. FPWD provided a direct pressure measurement while drilling to set the lower boundary, and formation-integrity tests (FITs) with MPD provided the upper boundary.
Introduction
The SB field has a relatively high temperature gradient and abnormal-pressure regimes. Challenges in this HP/HT environment include a reduced kick tolerance, narrow drilling margin, higher drilling-fluid densities, high temperature (limitations in formation-evaluation equipment), wellbore ballooning, and availability of personnel experienced in HP/HT drilling.
Well SBD-2 had been considered undrillable because of its very narrow safe-drilling margin. The previous attempt to drill through the F and H reservoir sands, Well SBD-1, suffered an influx from the formation that exceeded kick tolerance and compromised the fracture gradient, resulting in total fluid losses. Well SBD-1 failed to reach total depth (TD) despite the use of an MPD system—200 m shy of the geologic target. Well SBD-2 was drilled only 50 m away from Well SBD-1. Given the close proximity, there were offset pressure data for planning Well SBD-2 down to a depth of X240 m, but beyond this depth it would be exploratory drilling. Given the uncertainties that would be encountered drilling past X240 m, the engineering team sought best practices and technologies that would provide the greatest chance of success drilling into such a tight margin at high temperature.
The 8½×9½-in. reservoir section would use an automated MPD system to mitigate drilling risk complemented by an FPWD tool in the drilling bottomhole assembly (BHA) to provide direct pressure measurements. The MPD system was used for early kick detection (EKD), FITs, dynamic flow checks, and constant-bottomhole-pressure (CBHP) control for a safe mud-weight window that was expected to be less than 0.9 lbm/gal. The high mud weight needed to drill this formation resulted in a high equivalent circulating density (ECD) throughout the section, requiring the MPD system to maintain a static condition between 0.2 and 0.4 lbm/gal. The FPWD tool would provide pressure data to establish the lower limit for the MPD fingerprint tests, and to serve as calibration points for the pore-pressure model. The objective in this 8½×9½-in. section was to maintain overbalance in the narrow window between pore pressure and fracture gradient. These tight drilling margins required use of an automated MPD system with software capable of predicting temperature effects and annular-pressure behavior during any well-control situation.
MPD Overview
The International Association of Drilling Contractors Subcommittee on Underbalanced and Managed Pressure Drilling has made the following formal definition of MPD. MPD is an adaptive drilling process used to control the annular pressure profile precisely throughout the wellbore. The objectives are to ascertain the downhole-pressure environmental limits and to manage the annular hydraulic-pressure profile accordingly. MPD is intended to avoid continuous influx of formation fluids to the surface. Any flow incidental to the operation will be contained safely by use of an appropriate process.
- The MPD process uses a collection of tools and techniques that may mitigate the risks and costs associated with drilling wells that have narrow downhole-environmental limits by managing the annular hydraulic-pressure profile proactively.
- MPD may include control of backpressure, fluid density, fluid rheology, annular-fluid level, circulating friction, and hole geometry or combinations thereof.
- MPD may enable faster corrective action to deal with observed pressure variations. The ability to control annular pressures dynamically facilitates drilling of what might otherwise be economically unattainable prospects.
Not in the formal definition but implied is that this drilling method uses a single-phase drilling fluid treated to produce minimal flowing frictional pressure losses. MPD helps manage the problems of massive losses associated with drilling fractured and karstic carbonate reservoirs. It also manages ECD when drilling extended-reach wells and wells with narrow margins between formation breakdown and well kicks.
The MPD system used in Well SBD-2 included an automated-control-and-data-acquisition system that monitored and controlled the annular pressure. The primary objective of this process is to control the bottomhole pressure (BHP) at a fixed point in the open hole, keeping the BHP within an acceptable range to prevent influx, borehole instability, ballooning, breathing, and mud loss. The MPD system includes an automated control system, bypass line, choke manifold, dynamic relief choke, backpressure pump, Coriolis flowmeter, control cabin, and all necessary surface piping and isolation valves to connect the MPD equipment to the rig equipment (Fig. 1) and rotating control device (RCD) (Fig. 2).
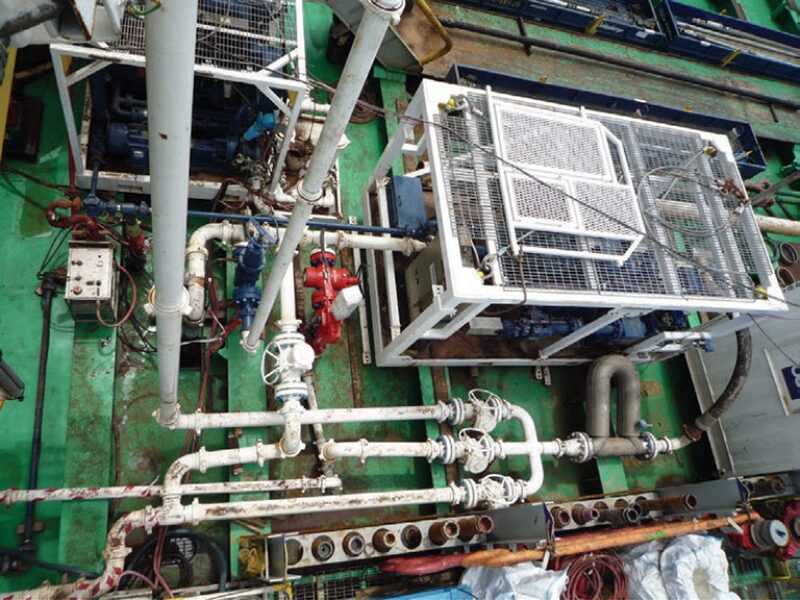
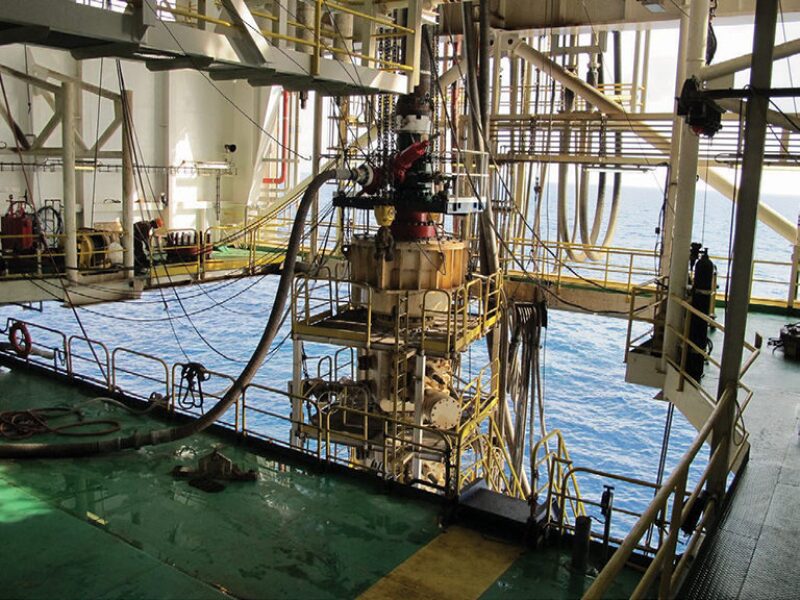
FPWD Overview
The FPWD tool provides direct real-time measurement of formation pressure and mobility. The 30-ft-long FPWD tool has an integral stabilizer that houses the measurement section (Fig. 3). The tool is a probe-type formation tester, similar in design and operation to conventional wireline formation testers. In operation, the measurement probe is brought to the desired test depth at neutral drillstring weight, the BHA is kept stationary while the pretest is conducted (approximately 10 minutes of total stationary time), and the measurement is transmitted to surface.
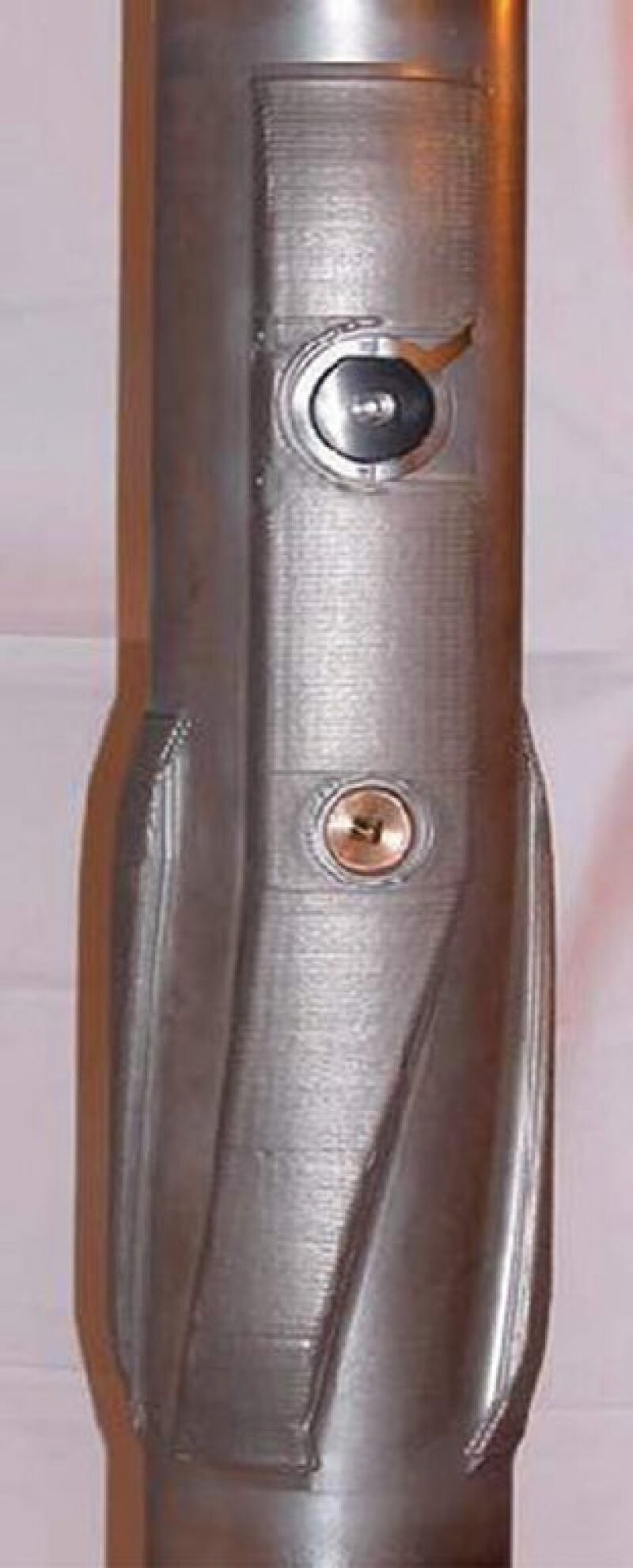
A challenge with FPWD tools is controlling the pretest to provide the correct rate and volume to yield a stable pressure. For FPWD pretests, a downlink command is sent to the measurement-while-drilling tool and forwarded to the FPWD tool. This command carries instructions regarding which pretest sequence to carry out. Depending on the sequence called for, the parameters of the pretest may be either fixed or downhole variable. Fixed pretests will adjust the rate, volume, and time for the pretest sequence and are chosen on the basis of anticipated formation mobility. Uncertainties in formation mobility can provide a risk to the use of fixed-mode pretests, but the ability to control the rate and volume directly can be useful in difficult testing conditions. Time-optimized pretests (downhole variable) will vary rate and volume intelligently downhole, independent of surface control, to achieve a stable pressure within the 5 minutes allotted for measurement. This pretest type is designed to overcome limitations of mud-pulse telemetry used to control logging-while-drilling (LWD) tools. Time-optimized pretests provide a much better chance of obtaining a valid measurement on the first pretest attempt, given their ability to vary the rate and volume; however, the flexibility to control rate and volume directly with a fixed-mode pretest can bring value. In Well SBD-2, a combination of fixed and time-optimized pretests was used in the testing program.
Taking pretests for drilling applications, such as pore-pressure calibration, can be challenging given the very dynamic nature of the wellbore and near-wellbore formation shortly after drilling. Challenges include the inability to make a seal because of a lack of mudcake, supercharging that can lead to nonrepresentative formation pressures, and continuous invasion and secondary supercharging from mud circulation during the pretest.
Kick and Loss Detection
The low kick tolerance and consequent loss of SBD-1 indicated that a key challenge for SBD-2 was kick tolerance. Engineering analysis before drilling indicated a kick tolerance of 55 bbl in the 8½×14¾-in. section, 15 bbl in the 10½×12¼-in. section, and only 10 bbl in the 8½×9½-in. section. Precise and early kick detection was vital to prevent influx volumes that could compromise open formations or the lowermost casing shoe. Integrating EKD into the MPD system allowed precise measurements of inflow through stroke counters and outflow with a Coriolis flowmeter. Small deviations were identified through an alarm system to alert the team to any changes beyond noise, to prevent false alarms. In total, the system identified two kick events and five loss events throughout the drilling of Well SBD-2. An unexpected high pressure was recorded at test point X590 m. Therefore, the test was repeated 30 hours later with a pressure recorded within 1.5 psi of the original measured pressure, providing further confidence in the FPWD result (Fig. 4). With knowledge of this high pore pressure, the MPD fingerprint tests proceeded without going below 18.2 lbm/gal, eliminating any chance of formation-fluid influx.

Pore-Pressure Prediction
Given the failure of Well SBD-1 to reach TD, an effort that relied primarily on MPD alone, the approach used for Well SBD-2 could be considered all-inclusive in that a variety of disciplines supplied data that were used by the drilling team to develop a representation of occurrences downhole. It was envisioned that such an approach could overcome shortcomings that could be inherent in a single standalone approach. Examples of data used to understand pore pressure and wellbore behavior while drilling include:
- A geomechanics predrill study
- Real-time monitoring through the pore-pressure mud-logging team by use of cuttings, drill gas, and flow-rate change
- Wireline formation-pressure measurements throughout the upper well sections
- LWD measurements for pore-pressure-trend analysis (e.g., resistivity)
- FPWD with LWD in the 8½×9½‑in. section
- Real-time hydraulics modeling to understand the ECD behavior given the temperature, pressure, and fluid properties
- Look-ahead seismic to match synthetic-seismic models and tie to velocity horizons
- Dynamic fingerprinting with MPD
Conclusions
The 8½×9½-in. section of Well SBD-2 presented the operator with a difficult decision that is becoming more common as the industry extends its reach to more-challenging reservoirs: How to balance risk, such as losing an expensive LWD BHA vs. the need to acquire data to understand the downhole conditions. Lessons learned from previous well operations prompted the operator to use the latest technical enablers, such as real-time FPWD pressures, to provide a clearer description of downhole conditions and enable informed decision making.
This article, written by Senior Technology Editor Dennis Denney, contains highlights of paper SPE 156888, “Demonstrating the Value of Integrating FPWD Measurements With Managed-Pressure Drilling To Drill Narrow Mud-Weight Windows Safely in an HP/HT Environment,” by L. Umar, SPE, I. Azian, N. Azree, and A.R.M. Ali, Petronas, and A. Waguih, SPE, F. Rojas, SPE, S. Fey, SPE, B. Subroto, SPE, B. Dow, and G. Garcia, SPE, Schlumberger, prepared for the 2012 SPE/IADC Managed Pressure Drilling and Underbalanced Operations Conference and Exhibition, Milan, Italy, 20–21 March. The paper has not been peer reviewed.