This paper presents information regarding the installation of intelligent-well completions (IWCs) in the Lula and Sapinhoá fields of the Santos basin presalt cluster (SBPSC). The technology is intended to improve reservoir-management capability by using remotely operated flow-control valves and real-time pressure and temperature monitoring for each perforated interval, corresponding to different reservoir zones. The benefits are obtained at the expense of additional challenges for well engineering because well-completion design becomes more complex and overall associated risks increase.
Introduction
The area known as the presalt cluster in the Santos basin is located in ultradeep waters, between 1900 and 2400 m, approximately 290 km from Rio de Janeiro in southeast Brazil. Fig. 1 (above) shows the main blocks of the presalt cluster currently in the appraisal-plan or production-development phases.
The first areas selected for production development were Tupi (BM-S-11 Block) and Guará (BM-S-9 block), which now are known as the Lula and Sapinhoá fields. Initially, extended well tests were performed in these areas to gather information and test some of the technologies that would be applied on further developments.
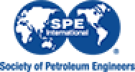