The trend of increasing automation and integration of digital work flows continues in all disciplines within the industry. An obvious driver is the increasing digital nature of our world; today’s phones and tablets connected to the cloud perhaps have more computing capabilities than supercomputers from 5 or 10 years ago. Another key driver, arguably the reason why intelligent operations came on the radar of most companies, is being able to improve safety and efficiency in the complex operations that are routinely performed in the oil patch.
The last couple of years, I have highlighted efforts around remote operations of fields, smart wells, and the acquisition and integration of real-time data. This year, I have focused on recent drilling-related papers that highlight how safety and performance can be improved with more intelligent operations.
Paper SPE 208711 discusses a key requirement I see for successful intelligent operations, especially when the operations span disciplines and companies. Having a standard, consistent, and unambiguous lexicon is critical for automation and digital work flows. This paper highlights an effort to spur the standardization of codes across companies to describe drilling, completions, and other well activities. Anybody who has gone through old well files will recognize immediately the value and the need for such standardization of well activity codes.
The other two papers (SPE 208764 and SPE 208784) highlight how automation can lead to increased safety on rigs during operations. Companies are using a combination of cameras, wearables, and other technology to monitor personnel in safety zones on rigs to ensure no one is unknowingly in the wrong spot at the wrong time. A familiar analog to this would be the safety improvements in driving because of collision-avoidance systems in cars (where a combination of technologies including cameras, radar, and lidar are used).
Standardization of Well Activity Codes. Paper SPE 208711 describes the efforts of one operator to standardize well activity reporting codes. A key highlighted improvement is a new coding system that captures both what was done (the typical focus of historical well activity codes) and the broader context on why the activity was performed.
The new codes have enabled more granular tracking of performance metrics and a simplification of reporting. Significantly, the operator has recognized the need for a standardized set of codes across the industry and has donated the codes they have developed to an industrywide open-source environment. I hope this spurs wider adoption and refinement of reporting standards across the industry.
Using Computer Vision To Monitor Safety Zones and Automate Drillpipe Tallies. Paper SPE 208764 highlights how digitalization can result in safer operations and improved accuracy through the automation of manual tasks. The paper discusses a computer vision system coupled with a neural network model that detects if any personnel are within a restricted pipe-delivery red zone at an unsafe time and sets off an audible warning alarm.
The paper also describes how the use of multiple cameras on different levels of the mast automates the measurement and tallying of the drillpipe being run into the hole. Both these aspects have enhanced existing processes (such as the use of buffer zones and barricades and the manual counting of drill pipe) to further improve safety and accuracy. This article in JPT might also be of interest.
Automatic Kick Detection and Dynamic Well Monitoring. Paper SPE 208784 discusses how to reduce the time gap between when drilling operators detect a kick and when they activate the blowout preventers (BOPs). The paper identifies accurate positioning of the drillstring before activating BOPs as a critical step that affects the time gap. The paper describes an architecture that allows automation of the space-out operation and achieves quick and accurate positioning of the tool joint with minimum movement of the drillstring. A critical enabler that the authors describe is being aware in real time of the depth of each tool joint in the wellbore.
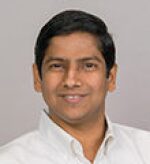
Keshav Narayanan, SPE, is a principal reservoir engineer with BHP in the Houston office. He has more than 24 years of experience in reservoir management, optimization of reservoir performance, and reserves estimation. Narayanan has worked on a variety of greenfield and brownfield projects in the US, Europe, and the Middle East. He holds a BS degree in chemical engineering from the Indian Institute of Technology, Madras, and an MS degree in petroleum engineering from The University of Texas at Austin. In addition to serving on the JPT Editorial Review Board, Narayanan also serves on program subcommittees for SPE’s 2022 Annual Technical Conference and Exhibition. He can be reached at www.linkedin.com/in/keshav-narayanan-328576.