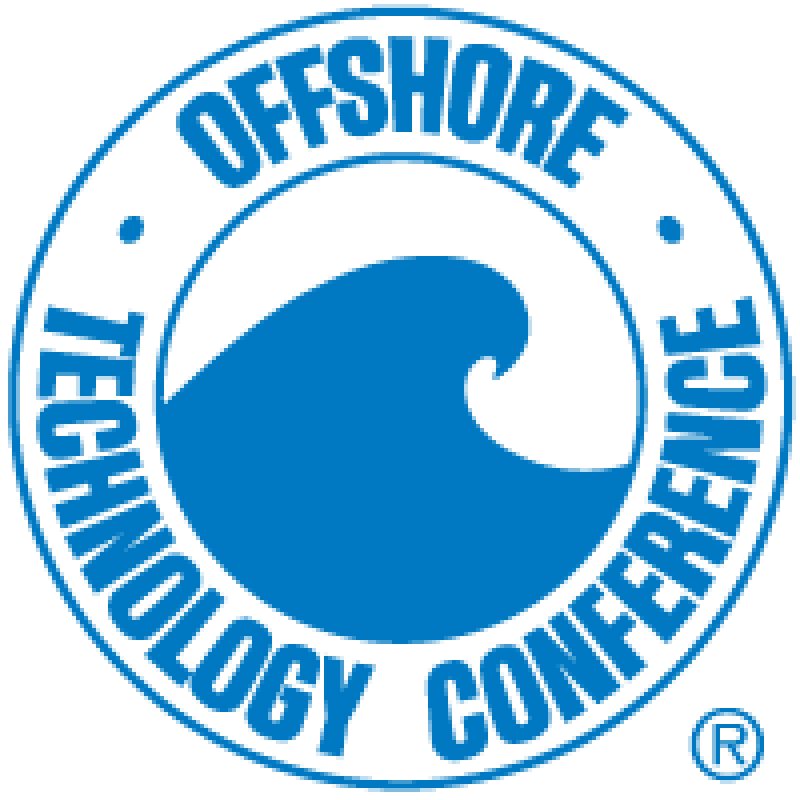
Moving oil/water separation equipment from platforms to the seabed looks inevitable, but based on the current rate of adoption it could take forever.
Out of the 5,000 wells with subsea completion, only five have used some variety of separation, whether it is separating water from oil, gas from liquids, or treating seawater before it is injected into a reservoir.
A panel at the 2016 Offshore Technology Conference in Houston made the case for why separators are a far better option in deep water than lifting water a mile or more, processing it, and pumping back down to the bottom for injection into the ground.
“It is going to happen," said Jeff Jones, senior subsea systems consultant for ExxonMobil. “We will get back to it.”
Jones referred to subsea separation in the past tense because it has been a while since the five projects, or by his count eight of them including some smaller units used for pilots, have gone into service.
“It is not as dead as you think,” said Don Underwood, director of subsea processing for FMC Technologies. “We are in a world where, perhaps, operators cannot go forward with greenfield projects,” but still need to find a way to add production to make up for declines in older wells.
As for what will turn the inevitable technology into a practical option, the one word answer is cost. Statoil, which has been a major supporter of moving operations subsea has said a 50% cost cut is needed, while Petrobras has put that number at 30%, he said.
“There has been significant movement in that direction," Underwood said. "For one, prices have been lowered dramatically,” while the designs have shifted from huge units to “lower cost compact technologies” that can be added as a cheaper alternative to drilling.
“Drilling these wells will be so expensive, but tying back to existing hosts would help us squeeze every last barrel we have,” Jones said, noting that drilling costs represent 50%-80% of the cost of offshore projects.
So far the company’s only experience with subsea separation is as a partner with Total on its Pazflor project off West Africa, which is operated by Total. There, gas is removed from the oil to ease lifting. But Jones said the technology could be used on its developments off Newfoundland to increase the output from tie backs—eliminating the need to build lines to carry both water and oil as well as reducing flow assurance issues—and processing seawater used for injections to enhance production.
Removing the water and disposing it saves the cost of lifting water, which is then pumped back down to the bottom to be injected into the formation. As fields age, and when the water cut far exceeds the oil, operators must either expand processing capacity on the platform or live with limited output.
“Adding a pump is sometimes not the most efficient answer, but it is easier,” Jones said, noting that the comfort factor exceeded the energy required to pump water to the surface, process it, and send it back down.
Turning subsea separation into a tool used as widely as pumps will require executives to show their support for doing something new, and make it clear that project managers are not risking their career if they choose to use subsea processing.
The heightened attention on the risk of using subsea processes may be adding to the complexity, which is an obstacle to adoption. One of the toughest challenges is removing sand from the production stream because it can shorten the life of these devices. But that could introduce the complexity-driven risks.
“If a pump can, in theory, fail because of sand, we create a sand system that is 10 times more complicated than the pump,” said Rune Fantoft, chief executive officer of Fjords Processing, a Norwegian firm working on separation. While he recognized the need for improved equipment to deal with such problems, he pointed out the methods are likely to be drawn from what is now down above the surface.
FMC has addressed one of the problems nagging subsea operators—the hard-to-separate emulsions of water and oil which stymie processes—with its InLine ElectroCoalescer, which earned it an OTC Spotlight on New Technology Award on Monday. The device uses electrical currents to cause oil to form droplets that can be easily removed from water. It's not a new idea, but it is a compact solution to emulsions, which separation methods using forces such as gravity cannot solve.
“You cannot depend on separation for that,” Underwood said. “Emulsions could take days to break down on their own.”
The industry needs to create other compact, standard models which can be added as needed to increase processing capacity, according to the panel. But, so far, the experience of the five projects shows subsea processing methods work.
“It can be optimized. There are many things we can do,” Fantoft said. “But for most applications where there is a good value proposition the technology is there."
Stephen Rassenfoss is the Emerging Technology Senior Editor for the Journal of Petroleum Technology.