Thirty years after Piper Alpha and the subsequent Cullen Inquiry into the disaster, which made 106 recommendations accepted by the oil and gas industry, safety remains a priority and a concern.
In recent years, operators and the supply chain have worked in a relatively constrained, low-cost environment. The dramatic shift to producing hydrocarbons at lower cost, with fewer people, while transitioning to a more environmentally friendly and sustainable energy future is well under way and will undoubtedly have impacts long into the future.
Business leaders and workers must take responsibility for increased investment in healthy, safe working practices and work closely with regulators globally to manage risk. Regulators remain vigilant toward major accident hazard management (MAHM). They are watching for gaps in safety-related skills that may potentially arise and lead to a higher incidence of major accidents in an industry cautiously stabilizing after the downturn.
Knowledge loss, from the enforced mass departure of an aging and skilled workforce within the industry, is a concern as highlighted by a recent report from an industry/government working group in Norway, which reviewed offshore health, safety, and environmental (HSE) performance. It commented that although the level of HSE offshore Norway was high, safety challenges have risen in the pas few years.1
Plugging the Skills and Knowledge Gap
New research has revealed that recruitment is firmly back on the agenda after 4 years of consistent reductions, spurred by cost-efficiency measures. According to A Test of Resilience, DNV GL’s ninth annual report on the outlook for the oil and gas industry, more than a third (34%) of the 791 senior professionals surveyed expect to grow their workforce in 2019—more than three times as many respondents than 4 years ago (10%). Over a third (39%) also expect to increase the use of contractors this year.
However, skills shortages and an aging workforce have resurfaced as a major concern. The issue takes joint second place as a perceived barrier to growth, alongside the oil price and the state of the global economy. Competitive pressure is viewed as the greatest challenge. The study also found a leap of 20 percentage points over the past 2 years in the number of respondents looking to increase or maintain investment in training and competence, up from 65% in 2017 to 88% for the year ahead.
Technologies are part of the answer to ease this generational knowledge transition, but operators are also expanding management processes for MAHM. Formalizing the recording of historical or crucial job-specific information and capturing, sharing, and using information from experienced professionals can promote safe operations in the global oil and gas industry. In the long term, this strategy is also highly cost effective.
Too often, knowledge is lost as an unintended consequence of activity such as mergers, acquisitions, and industry redundancies or job losses. Over-reliance on specialist supply chain companies or expensive subcontracted expertise can also leave noticeable gaps.
Strategies to mitigate the risk of knowledge loss in oil and gas can be borrowed from other industries with major, long-standing plant facilities such as the nuclear and steel industries. This safeguards against the potential loss of safety-critical knowledge if staff move within the industry or leave it.
Knowledge loss does not have to be accepted. Other industries have shown ways this can be retained, notably by building mechanisms for knowledge retention into the safety management system. This creates continual processes that are more effective, thus saving costs and downtime associated with re-acquiring knowledge and reducing incidents.
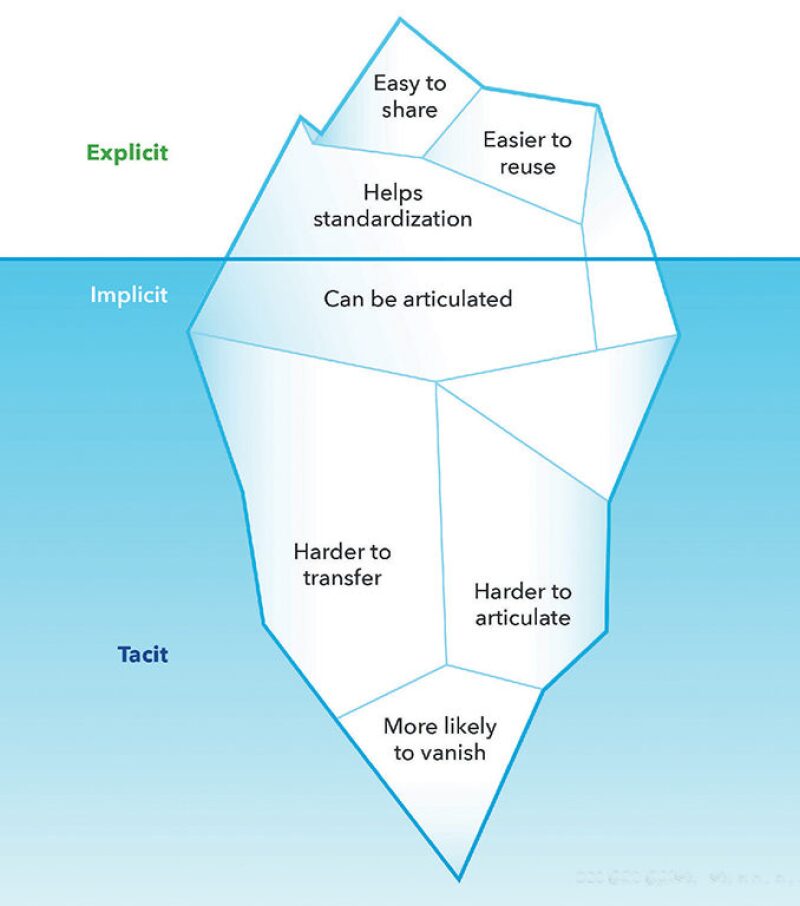
Reprioritizing Knowledge Management
The value of safety knowledge transfer is beginning to become clearer and is now being considered more at the boardroom level and filtering to the worksite. Working with industry over many decades, specialists from DNV GL have found that accidents usually happen when there are complex interactions between people and plant.
Therefore, the oil and gas industry promotes the use of rigorous systems to check for weaknesses in both elements. We have observed that while risk management processes to enhance safety are important, people can be ignorant of the risk.
In what remains a high-risk industry, the cost of overlooking—or worse, ignoring—a safety hazard is potentially high in terms of human lives, financial, and reputational consequences. The knowledge risk challenge that we face can be simplified through early-warning systems and shutdown safeguards that advanced technologies offer. However, the human factor in safety control is key to designing better solutions and implementing them globally. Without the buy-in of management and workers, the technologies and processes cannot succeed.
Connected World, Global Solution
The International Association of Oil and Gas Producers (IOGP) has found that among 45 reporting member companies operating in 104 countries, the number of fatal incidents per year rose from 29 to 30 between 2016 and 2017.2 IOGP’s analysis showed that at least 87% of the fatal incidents involved breaches of its own longstanding Life-Saving Rules and that many such fatalities are preventable.
A special DNV GL report, The state of safety: the outlook for the oil and gas industry in 2018, reaffirms concerns over safety spending in the sector.3 The industry should always retain a healthy sense of unease over safety. It would be dangerous to assume that safety is under complete control anywhere in a rapidly changing industry. Through these studies, we recognize that in mature basins, knowledge of design, non-routine issues, and asset-specific knowledge is usually only fully understood by a few people.
This information is not readily accessible to others who may need it, including people in safety-specific roles. Knowledge can be lost in many ways but, in some cases, the simple knowledge that such documentation or resources even exist is not known by staff. A robust approach involves identifying knowledge risk, evaluating it, capturing and transferring knowledge into an accessible form, sharing it, and, most important, re-using it.
We can visualize knowledge as an iceberg with a small part of its bulk—the easy-to-get, explicit knowledge held in documents, images, and reports—visible above the water, and the vast majority, the tacit knowledge held in the heads of people, submerged.
In safety-critical environments, all relevant knowledge, information, and data should ideally be easily available and understandable when and where needed and not be out of date, incomplete, and dispersed as is commonly the case.
References
- Helse, arbeidsmiljø og sikkerhet i petroleumsvirksomheten, Rapport fra partssammensatt arbeidsgruppe, Oslo, Norway, January 2018
- Safety performance indicators 2017 data, IOGP, June 2018
- The state of safety: the outlook for the oil and gas industry in 2018, DNV GL, May 2018
![]() | Michael Kelleher is principal consultant, Knowledge Management Competence Centre, DNV GL, and has specialized in knowledge management and organizational learning for 30 years. He has also served as a visiting professor at Nottingham Trent University, a director of Learning Futures Ltd., and general secretary of the European Consortium for the Learning Organisation. He has BSc and PhD degrees from the University of Bath. |