The first curable resin-coated proppant (RCP), which Fairmount Santrol introduced 40 years ago, has helped oil and gas operators solve costly proppant flowback problems. And the many phenolic novolac RCPs that the company has developed since then have become industry work-horse products. Their polymeric coatings are based on phenolic novolacs (phenol formaldehyde resin) crosslinked by the use of Hexamethylenetetramine (Hexa) as the curing agent.
When general concerns arose recently about phenolic novolac RCPs potentially leaching chemicals during handling and downhole pumping, the company undertook to research to gain a full understanding of the subject. One of the specific objectives was to critically address environmental concerns about the potential leaching of free formaldehyde and phenol (Pangilinan et al. 2016) into fracturing fluids or inside propped fractures downhole from phenolic novolac RCPs.
Preliminary qualitative testing showed low levels of leachants from company-specific phenolic novolac RCPs. However, to become certain, an in-depth quantitative study was initiated to further investigate potential chemical leaching under simulated downhole conditions.
The overall scope of the study was to investigate a couple of representative RCP samples from the company’s product portfolio in connection with product safety and environmental impact by analyzing: the total level of leachants and quantifying any potential leaching of free formaldehyde (a hazardous chemical) and/or free phenol.
As part of the test matrix (Horadam et al. 2018), two phenolic novolac RCPs (one curable RCP-C and one precured RCP-PC) were compared with two polyurethane (PU) RCPs that are commercially available from other suppliers.
The vast majority of commercially available RCPs are based on phenolic novolac chemistry, and to a lesser degree, on polyurethane chemistry. The test temperatures for this study were selected to include a low bottomhole temperature (BHT), typical in a Permian Basin well and a high BHT representative of wells in Oklahoma, the south-Texas Eagle Ford Shale, and the Bakken Shale.
Each experiment ran for 7 days at two representative temperatures (150 °F and 250 °F) and three pH conditions: pH=3 (acidic), pH=7 (neutral) and pH=10 (alkaline) in glass pressure bottles to ascertain if these RCPs were likely to leach chemicals into the environment. To study the worst-case scenario, the tests were conducted at an RCP loading level of 8 lbm of proppant added (PPA) to one gallon of fracturing fluid, which is three to four times higher than the typical RCP loading level used in downhole pump operations.
Total Leachant Level, Potential Free Formaldehyde Leaching
After chemically exposing the four RCPs under the previously stated conditions, company scientists analyzed the supernatant aqueous fluids from the leachates by using proton-nuclear magnetic resonance (1H NMR), an advanced analytical technique capable of elucidating chemical structures at the molecular level. A “water suppression” pulsed NMR technique was adopted to mitigate the effect of the intense proton signal because of water, which would allow the quantitative identification of the various organic leachants in solution.
The NMR analysis of the leachates (Fig. 1) proved that there was no free formaldehyde present in its pure or its hydrated form (such as methylene glycol) in the tested phenolic novolac RCPs.
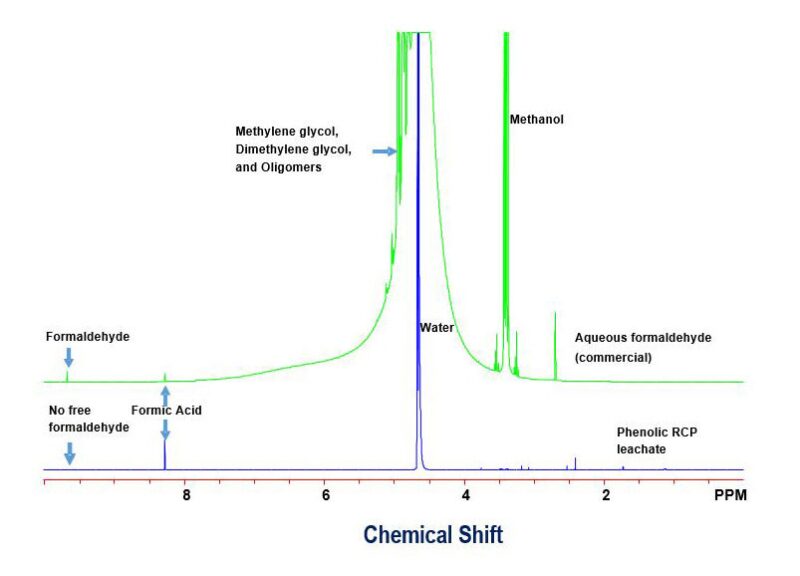
This is shown by the lack of a free formaldehyde peak around 9.7 ppm in the NMR spectrum (blue line) of the phenolic novolac RCP sample. It should be noted that there were only tiny amounts of formic acid, as a byproduct, as shown at 8.3 ppm (blue line NMR spectrum).
The finding that there is no free formaldehyde in the company’s phenolic novolac RCPs is of critical significance to exploration and production, oilfield services, and transportation companies and important for the environment. The permissible exposure limit (PEL) and short-term exposure limit (SEL) for free formaldehyde are 0.75 ppm and 2.0 ppm, respectively, according to OSHA regulations (OSHA 20007b 29 CFR 1910.1048).
The major conclusions from the NMR analysis are:
1. At 150 °F exposure test temperature, the company’s curable and precured phenolic novolac RCPs showed very low total leachant levels, measuring at 0.08% by weight. The commercially available PU RCPs showed leachants up to 0.15% by weight.
2. At 250 °F exposure test temperature, the company’s phenolic novolac RCPs showed a negligible level of total leachants, below 0.06% by weight. The PU RCPs showed leachant levels between 0.20% and 0.35% by weight. Fig. 2 provides a summary of the comparative leachability study of the phenolic novolac RCPs versus PU RCPs (PU1 and PU2) tested at 250 oF. The total leached material from each RCP has been averaged over the three pH conditions, as it was observed that the extent of RCP leaching was relatively insensitive to the pH levels used in this study.
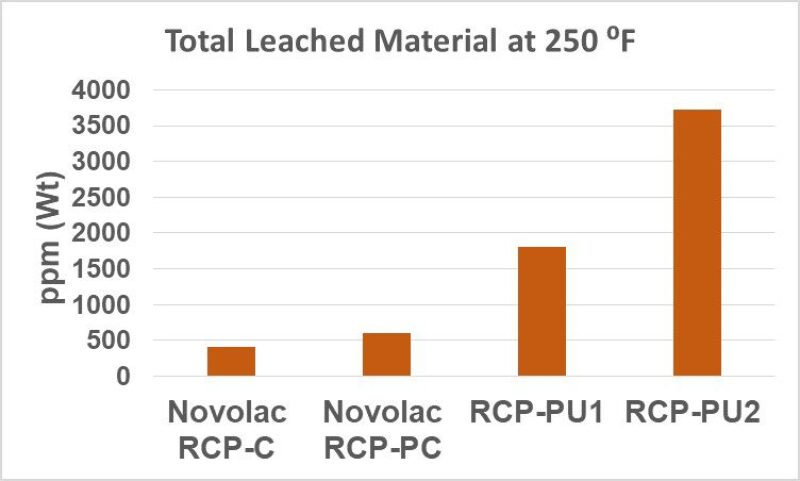
3. The NMR analysis showed that the phenolic novolac RCPs, whether curable or procured, are demonstrably more stable in higher downhole temperature conditions than polyurethane RCPs.
4. The polyurethane RCPs start to degrade at higher temperatures.
Free Phenol Analysis
To investigate the phenolic novolac RCP samples specifically for potential leaching of free phenol, the leachates of these samples were tested by using the highly sensitive ultraviolet-visible (UV/Vis) spectrophotometry. It was demonstrated that the concentrations of phenolics in the leachates, including free phenol from the phenolic novolac RCPs were well below the detectable limits of this technique (< 1 ppm).
The UV/Vis spectrophotometric analysis results of phenolics and potentially free phenol in the aqueous leachates of the company’s phenolic novolac RCPs are shown in Table 1. Phenolics were present in less than detectable amounts (< 1 ppm) in the aqueous leachates of the phenolic novolac RCPs (both precured and curable, entries 1–6 in the table). Free phenol, if any, is expected to be at an even smaller fraction of the 1 ppm of total phenolics, which can be potentially detected with this sensitive test.
These findings are of great significance because these tests were conducted on the phenolic novolac RCPs at a much higher than normal proppant loading level (~ 8 PPA) to enhance the detectability of leaching species.
TABLE 1—SPECTROPHOTOMETRIC ANALYSIS OF PHENOLIC COMPOUNDS IN THE AQUEOUS LEACHATES GENERATED FROM COMPANY-SPECIFIC PHENOLIC NOVOLAC RESIN-COATED PROPPANTS | ||
---|---|---|
Entry | Leachate, loading level (Conditions: 250 oF, 7 days) | Total Phenolics concentration (mg/L or ppm) |
1 | RCP-C (curable), 100g/100 ml pH 3 solution | <1* |
2 | RCP-C (curable), 100g/100 ml pH 7 solution | <1* |
3 | RCP-C (curable), 100g/100 ml pH 10 solution | <1* |
4 | RCP-PC (pre-cured), 100g/100 ml pH 3 solution | <1* |
5 | RCP-PC (pre-cured), 100g/100 ml pH 7 solution | <1* |
6 | RCP-PC (pre-cured), 100g/100 ml pH 10 solution | <1* |
* Below the detectable limits of the technique.
Conclusions
By employing highly sensitive and sophisticated analytical techniques (1H NMR and UV/Vis), the following have been demonstrated:
There is no leaching of free formaldehyde or free phenol from the company’s phenolic novolac RCPs.
The company’s phenolic novolac RCPs were demonstrated to be environmentally safe for use at low and high temperatures within a wide pH range of 3–10.
Commercially available polyurethane-based proppants offered by other suppliers showed high levels of leachants at higher temperatures.
Acknowledgement
The authors gratefully acknowledge the contributions of William Horadam, Moustafa Aboushabana, Tuan Tran, Kanth Josyula, and Vinay Mehta towards the success of this project.
References
Horadam, W., Venkat, N., and Tran, T. et al. 2018. Leaching Studies on Novolac Resin-Coated Proppants—Performance, Stability, Product Safety, and Environmental Health Considerations. Journal of Applied Polymer Science 135 (8): 45845. https://doi.org/10.1002/app.45845
OSHA 20007b 29 CFR 1910.1048. Formaldehyde. 2011. Washington, DC. Occupational Safety and Health Administration.
Pangilinan, K. D., De Leon, A. C., and Advincula, R. C. 2016. Polymers for Proppants Used in Hydraulic Fracturing. J. Petrol. Sci. Eng. 145: 154–160. https://doi.org/10.1016/j.petrol.2016.03.022