Like what you're reading? Sign up for the new JPT Unconventional Insights newsletter to get the latest news to your inbox. |
Proppant buyers insist on the “lowest cost for an appropriate sand.” That assessment was offered by Hayden Gillespie, president and chief operating officer of Black Mountain Sand, one of the mining companies that has driven down sand prices by building sand mines within a couple of hours’ drive from where it is used.
Cheap sand is easy to find in the Permian Basin, where regional sand mines have glutted the market. Nearby suppliers have an unbeatable price advantage over distant mines, which not long ago produced most of the sand used for propping fractures.
Appropriate is harder to define. The rules are changing as customers try new mixes of sand size and find that production data does not support many of the old standards.
In the Eagle Ford, oil companies are using sand size ranges that stretch the traditional API size specifications beyond recognition (Fig. 1). Rather than using old standards such as 40/70 mesh—the biggest grains must fit through a screen of 40 wires per inch, and the smallest cannot go through a screen of 70 wires per inch—they are using 40/140, where minimal sifting is required. Fracturing sand buyers still have needs, but they vary.
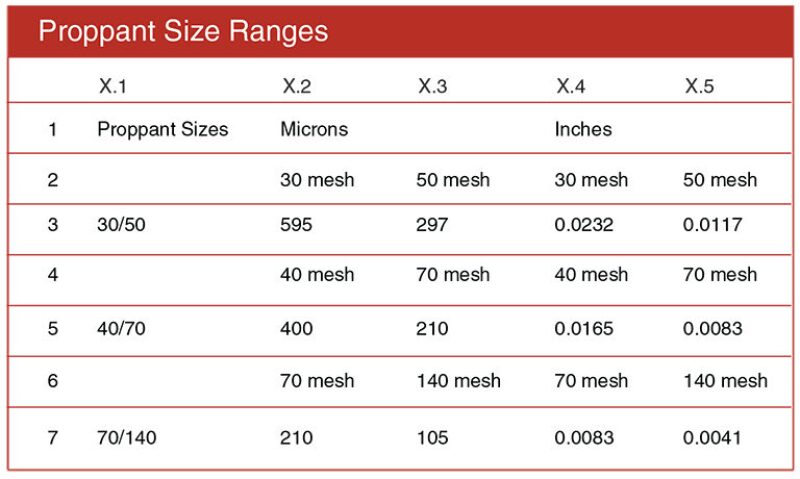
“I believe until all the companies are merged into one there will be different ideas” about how to get the most out of the local geology, said Mike Fleet, executive vice president for mining operations for Vista Proppant and Logistics.
The challenge for proppant suppliers is matching customer desires with the sand they mine.
“Vista has a hand-in-hand relationship with our customers,” Fleet said. The goal is to give them what they need, but “we can only do what mother nature puts in the ground,” he said.
Vista’s biggest mine, which is near Fort Worth, Texas, delivers grains ranging from mid-sized (40/70) to unusually small grains that it calls 200 mesh, via its logistics network to customers in Texas and Oklahoma. Vista also has in-basin mines in the Permian Basin, it is building its first mine in Oklahoma, and it is looking for a location for a mine in the Eagle Ford, said Chris Favors, vice president for business relations at Vista.
In the South Texas play, the competition includes mines selling low-cost options such as 40/140. This product contains most of the finer grain sand dug up from local pits, with processing to remove clay and fine dirt.
The approach is more like the original river sand mined for the first fractures rather than products sold with grains within the strict size limits set by API standards. Gillespie describes his sand as a “coarse 100 mesh.” It mixes some larger grains with 100-mesh sand.
ConocoPhillips has long experience in the Eagle Ford and has done extensive testing there to evaluate completions, including one of the only research projects that collected core samples of fractured rock around a well (URTeC 2670034). Based on its well performance analysis, it is open to offers on new proppant specifications.
When Dave Cramer, senior engineering fellow for ConocoPhillips, asked those in the field about what they are buying, they told him that ConocoPhillips is not specifying particle size ranges of nominal 100-mesh sand for Eagle Ford fracturing treatments. Doing so would increase the cost of that proppant type significantly. Instead, the company is typically accepting whatever is supplied by pumping service vendors. That includes 40/140 mesh sand, 50/140 mesh sand, 70/140 mesh sand, and other variations.
“The Eagle Ford well performance team claims they don’t see enough variability in production among the various sources of nominal 100-mesh sand to warrant securing a particular source or type of sand,” he said.
Opinions about what matters when fracturing vary widely. Given the many variables in wells and completion designs that can alter unconventional well performance, it is hard to prove or disprove the impact of any specific lever on production.
The Best Sand?
So what is the best sand for fracturing? “There is no right answer. It is based on local economics,” said Bob Barree, president of Barree and Associates and a technology fellow for Halliburton since selling his firm and his Gohfer fracture-modeling software. He says companies are looking for the “cheapest local sand.”
Gillespie said that while customers demand data on sand quality, “the changes we’ve seen over time always favor cost reduction.”
Barree recently delivered a technical paper about rules for proppant purchasing at the SPE Hydraulic Fracturing Technology Conference that questioned the value of a handful of rules of thumb (SPE 194382). They included: buying sand based on API standard sizes; not pumping mixes covering a wide range of grain sizes, particularly ones with extremely fine particles that might create blockages; and only using sand with clay and fines cleaned out.
The paper contradicts the widespread assumption that fracturing with larger-diameter proppant is not as effective as finer-grained mixes. Testing done at a prominent industry lab concluded that mixing larger-grained 30/50 mesh with finer 40/70 actually increased the conductivity of the smaller-grained proppant.
The popular notion that proppant made up of finer grains is more effective has dampened demand for larger 30/50 proppant, which once was the most widely used size.
“Nobody really wants it (30/50). There is absolutely no market for it,” said Scott Forbes, vice president Americas cost research for Wood Mackenzie, an energy consulting firm. With more mines producing more proppant, “pricing for finer-grain sand is so low today you cannot make 30/50 cheap enough to get someone to take it.”
Grinding Down Prices
The origins of the regional sand business goes back to the 2014 oil price crash. Oil companies reacted as they always had, demanding and receiving deep discounts from suppliers.
Deeper cost reductions were re-quired. Some companies began buying directly from the mines rather than buying from pressure pumping companies whose margins depended on markups on sand, Forbes said. At the time, he was the supply chain manager for an independent producer in the Permian that he said was among the first to unbundle—buying sand directly from the mine rather than as part of a service contract.
Some large independents, including EOG and Pioneer, went further by investing in local mines. Mining companies began building regional mines, which Gillespie said are generally within 150 miles of fracturing sites in competitive markets.
“There are several disruptive changes under way in the sand and logistics industry right now,” said Jim Wicklund, a managing director for the investment banking firm Stephens Inc.
Last year, direct purchases by operators totaled more than one quarter of the money spent on sand, according to Spear & Associates, he said. Those mines had to develop the infrastructure to deliver to those customers.
“That is definitely disruptive change. And the development of regional lines, in virtually every region, has made its impact as well, but again, really just on improved logistics,” Wicklund said.
The boom in Permian basin mines was a “paradigm shift” for sand suppliers, said Fleet, who compared it with “a gold rush or the dot com boom.” The result has been a supply glut in the most active unconventional play. The growing capacity of mines in the Permian will soon be large enough to, in theory, supply the entire US shale fracturing market, Forbes said. In reality, exporting excess sand to other basins is not an option because of the cost of moving that heavy commodity. “Everybody is looking for cheap local sand. If a mine is not there yet it will be soon,” Forbes said.
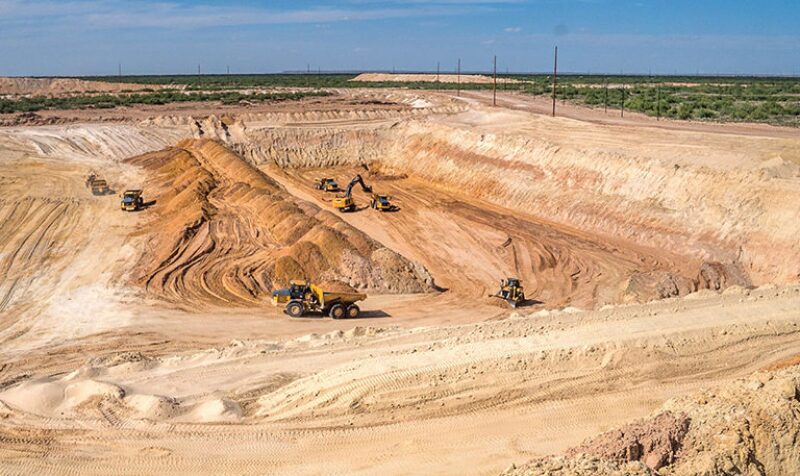
Vigilant Customers
A decade ago, the top selling sand was Northern White—generally large-grained sand from northern US states such as Wisconsin and Minnesota. Buying habits began changing when mines started opening in Texas, including Vista’s mine in Granbury.
Barree said the preference for bigger grains dates back to the days when most completions were done in higher-permeability reservoirs. Those larger openings required larger grains. Customers were comfortable with the quality. When cheaper alternatives hit the Texas market, Gillispie said buyers were interested, but “more vigilant.”
Among the questions raised: Are the locally produced 40/70 mesh grains strong enough to stand up to the crushing weight of the overburden in the deepest Permian shale plays. As with many sand questions, it is not a settled issue. “More testing and understanding is needed for the 40/70,” he said.
“When local mines started selling sand, operators insisted on knowing” what size grains were in this 100 mesh, Gillespie said. “Now people want, on a recurring basis, to know if the quality is staying consistent,” he added. To win over new customers, Black Mountain had to provide third-party tests showing the size distribution of the grains. Texas mines produce mostly fine-grain sands in the 100-mesh range.
Vista is selling an even finer grade called 200 mesh. The ultra-fine grains come out of Vista’s biggest mine in Granbury.
It is successfully reaching out to customers seeking grains with a higher crush strength, including ultra-small ones, and are willing to pay the freight from north Texas, Favors said.
Stretching the Range
Making money in the low-margin sand business requires finding buyers for all of the sand that comes out of the ground.
“The old adage is we want to sell the whole cow,” said Gillespie. Most of the grains in the full-range sand that Black Mountain sells are in the 100-mesh range, but there are also larger grains in the mix. It is described at 40/140 because there are 40/70 mesh grains mixed with those in the 70/140, but not enough of the large grains to make the sifting needed to sell them separately an option.
“If the limit is 70/140, the mine could be throwing away 10% of that. That adds to the waste stream and adds to the cost of the facility,” Gillespie said. Instead they persuaded customers to try a hybrid mix covering the size range of the proppant frequently pumped in the Eagle Ford—100 mesh plus some 40/70 mesh.
Other local suppliers are also selling versions of 40/140 in the Eagle Ford, Forbes said. Feedback on 40/140 has been positive, leading Black Mountain to begin developing a broad mix for the Permian.
“Since the most conductive portion of any fracture is likely to be unpropped open channels or wedges that are proximal to proppant packs or beds, fracture conductivity is probably not greatly impacted by using the smaller, less permeable material,” Cramer said.
“On the flip side, proppant flowback during production can be quite severe when using the smaller proppant as these materials are easily mobilized by the flow through open channels in the fracture,” he said. ConocoPhillips is doing field tests to see if using coarser proppant, such as 40/70 mesh, could limit flowback.
Bigger is Not Bad
The size difference is tiny between the highest-priced proppant—40/70 mesh—and the one mines struggle to sell at deep discounts. To be exact, the largest particles in 30/50 mesh are 0.0067 of an inch bigger than the largest particles in 40/70.
For sellers, that difference looms large. Tony Curcio, national sales manager for Hi-Crush, one of the largest suppliers of proppant, said that 30/50 mesh could go for $20/ton or less at the mine, while 40/70 mesh is selling for twice the price.
Demand for 30/50 is likely to remain low in Texas because few are willing to pay the freight from the northern mines producing most of it. Forbes estimated that moving sand from Wisconsin to the Permian would cost $65/ton. “Even if it (the Wisconsin sand) was free, the cost of shipping it to Texas would be far higher than locally sourced sand.”
Local mines supply more than enough sand for the Permian. While some Northern White is used in the Eagle Ford, Forbes said new mines opening soon will be able to meet local needs.
Rather than building up huge piles of unsold proppant, sand company sales managers are offering deals for 30/50 mesh, packaging it with popular 40/70 mesh to buyers in plays closer to the mines, such as the DJ Basin in Colorado.
A year ago, Barree was asked by Halliburton to find a productive way for an oil company client to use a large volume of 30/50 proppant—he described it as train-cars full in Colorado—purchased in a package deal.
His idea was to test a 50:50 mix of 30/50 and 40/70, creating 30/70 mesh. The blend was compared with 40/70 at Stim-Lab, a Core Labs division whose work is directed by an industry conductivity consortium. When it measured the particle size distribution, it found that the vast majority of the particles were in the 40/70 range (Fig. 2).
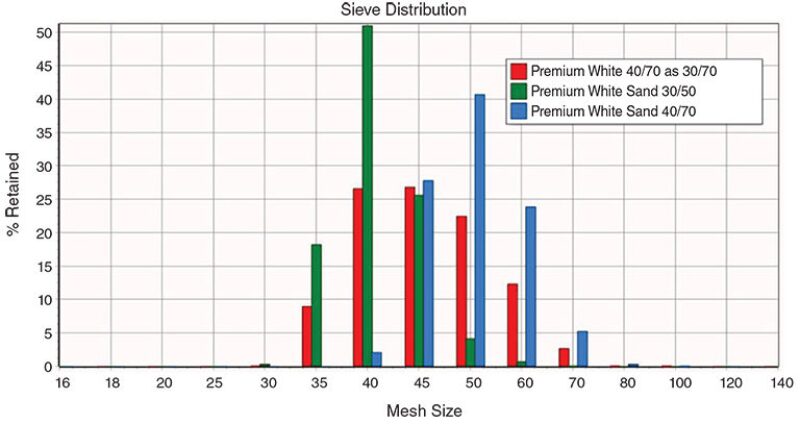
When they ran the standard conductivity tests comparing the 30/70 mix to 40/70, it found that the larger particles improved conductivity. Mixing small and large grains may also provide greater support against the heavy weight of the rock above, Barree said.
In the ground, the difference is far less, but conductivity in the ground is a tiny fraction of what is reported in the lab because labs cannot replicate the obstacles experienced in microscopic fractures.
The bottom line from Barree: “Mixing 30/50 and 40/70 sand may offer a significant advance in price and availability in many basins.”
What is the Distribution?
While some buyers are turning away from traditional size standards, they are asking more questions about the distribution of the grain sizes in the mix. “Customers want to know the sieve distribution. We go through that discussion a lot,” Gillespie said.
API standards set size boundaries, but do not consider the size of the grains in between. A chart from a ConocoPhillips paper (SPE 194329) presented at the hydraulic fracturing conference shows the variations among 100-mesh samples from different suppliers (Fig. 3). In recent years, automated systems originally designed for jobs such as assorting and sizing microorganisms have been adapted for measuring sand sizes.
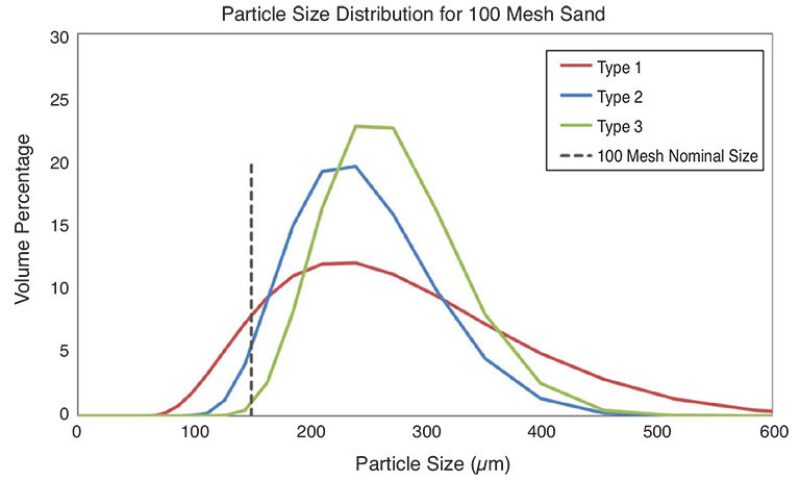
Barree suggested using the mass median particle diameter as a quick indication of the distribution, which correlates with conductivity. This measures the mid-size particle based on a mass-weighted calculation. That means it adjusts the size distribution by taking into account that the mass of big particles make up a far greater part of the mass and volume in a ton of sand than many tiny particles.
“I think the important thing is once you know the median size you can predict how it will behave,” Barree said. “Thousands of conductivity tests have demonstrated a very strong correlation between median particle diameter and conductivity for each specific type of proppant,” the Barree paper said.
He did concede that one rule that he suggested might be suspect must be obeyed. Barree said he was told by Bob Duenckel, vice president of Stim-Lab that, “if you do not wash it and get out the clays and super-fine dirt, that does degrade conductivity.”