In the past, most wells have been drilled using conventional methods, but the landscape is changing as economic pressures have forced the drilling industry to refocus. Attention is at an all-time high on technologies that deliver operational efficiency and improve safety. Operators, drilling contractors, and service companies have gone through exhaustive measures to reduce cost, refine efficiency, optimize asset performance, and maximize returns. The recently introduced Schlumberger Managed-Pressure Drilling Integrated Solution offers a significant impact in all of these areas.
Managed-pressure drilling (MPD) is an adaptive drilling process used to precisely control the annular pressure profile throughout the wellbore. In conventional drilling, the system is open to the atmosphere. However, with MPD, a closed-loop circulation system is created. The closed-loop system is the key element, as it enables control of the annular pressure profile through the application of surface pressure.
MPD can dramatically improve operational efficiency through the reduction of nonproductive time associated with influxes, mud losses, and stuck-pipe events. The closed-loop system improves safety by providing an increased awareness of pressure state in the well and facilitates a much higher level of control with quicker response.
The MPD drilling technique has been around for many years on land but is relatively new to deep water, as the needed technologies have only become available in the past 5 to 7 years.
While manual chokes have been the principal form of control of MPD operations since the technique was introduced, it has been noted that the consistency and repeatability of manual methods is only as good as the choke operator’s skill and the level of experience and teamwork between the driller and the choke operator. For this reason, automated MPD was introduced, and a solution now exists that addresses the many challenges associated with MPD operations.
A Shifting Business Case
Historically, MPD components have been owned and leased through various service companies. Operators have called out multiple providers to deliver the kit and execute the service.
Deepwater MPD requires substantial planning and financial investment, which has typically recurred with each call-out. On top of that has been the need to coordinate multiple service providers to work with the drilling contractor so that the system is properly integrated.
Given these requirements, operators have tended not to use the technique unless the well or hole section they are planning cannot be drilled without it. For the most part, MPD in deep water has been a contingency solution rather than a standard practice.
It is difficult to build a reasonable business case around a contingency solution or a call-out service that requires such significant investment and has multiple variables at stake. Additionally, service companies must charge a premium to ensure a sufficient return on their investment.
In all, the business model for applying deepwater MPD has proved inefficient for customers and providers, and a highly valuable technology has sat on the shelf. As long as the system utilization remains low, end-user costs will remain extremely high.
For MPD to reach its full potential in the deepwater market, the business case must change. The key to achieving that is to recognize all of its benefits and increase its utilization.
Closed-loop drilling not only delivers value in navigating the pressure profile of narrow-margin wells, but has proved its benefits in all phases of drilling, including risk mitigation and safety. It can be successfully applied in any deepwater well and should become a standard practice for drilling all high-profile wells.
However, closed-loop drilling cannot become a standard practice as long as all capital investment is on the service provider. Many operators and drilling contractors recognize this, and there are indications that a change is underway. Operators are increasingly calling out MPD enablement as a requirement in new contracts, and interest from deepwater drilling contractors has flourished even in a depressed market.
The new business model is for drilling contractors to own the equipment. This enables higher utilization as equipment becomes part of the standard rig offering, and the consumer capitalizes on all benefits of the system. As the trend continues, so will the shift from conventional to closed-loop drilling.
In parallel to this shift, more options have become available on land and in the deepwater market. On land, MPD has been a more sustainable call-out service, as the equipment footprint is smaller and more mobile. But relative to other call-out services, it remains challenging. While some drilling contractors are seeing the advantages of incorporating MPD into their rigs, the economics of doing so have been difficult to justify. However, an alternate deployment model could lower these barriers.
Mobile MPD
The @balance Xpress mobile MPD package from M-I SWACO, a Schlumberger company, is able to minimize connection points and installation time to improve rig-up and commissioning. The package is trailer-mounted and designed to reduce service delivery cost through higher asset utilization and by eliminating the need for a crane to move the mud gas separator from the horizontal to the vertical position (Fig. 1 above).
From Reservoir to Flare Stack
Schlumberger has made a significant impact in the deepwater market by introducing the industry’s first complete, reservoir-to-flare-stack deepwater MPD system exclusively developed, built, and delivered by an original equipment manufacturer. Customers can benefit greatly when MPD design, engineering, manufacturing, system integration, well engineering, and onsite well delivery services are provided by a single supplier.
The system includes an integrated riser joint (rotating control device, slimline annular blowout preventer, and flow spool) that is currently the shortest and lightest available on the market. Its reduced size and weight allows the joint to be picked up and deployed as a single lift, which saves time and improves operational safety.
The integrated solution includes a single control unit with all integrated riser-joint functionality and all surface manifolds controlled from a single human-machine interface. Transition from conventional drilling to closed-loop drilling, to riser gas handling, or well control can occur in an extremely efficient manner. This provides a considerable improvement in overall operating efficiency, user friendliness, and equipment footprint over other systems available in the market.
The number of service personnel required to operate and maintain the system has also been reduced with a focus on lowering the total cost of ownership.
Delivering the Technology
Schlumberger has delivered two fully integrated deepwater MPD systems into the field and completed the installation and commissioning. The system was tested on a warm-stacked floating rig and the performance was successful (Fig. 2).
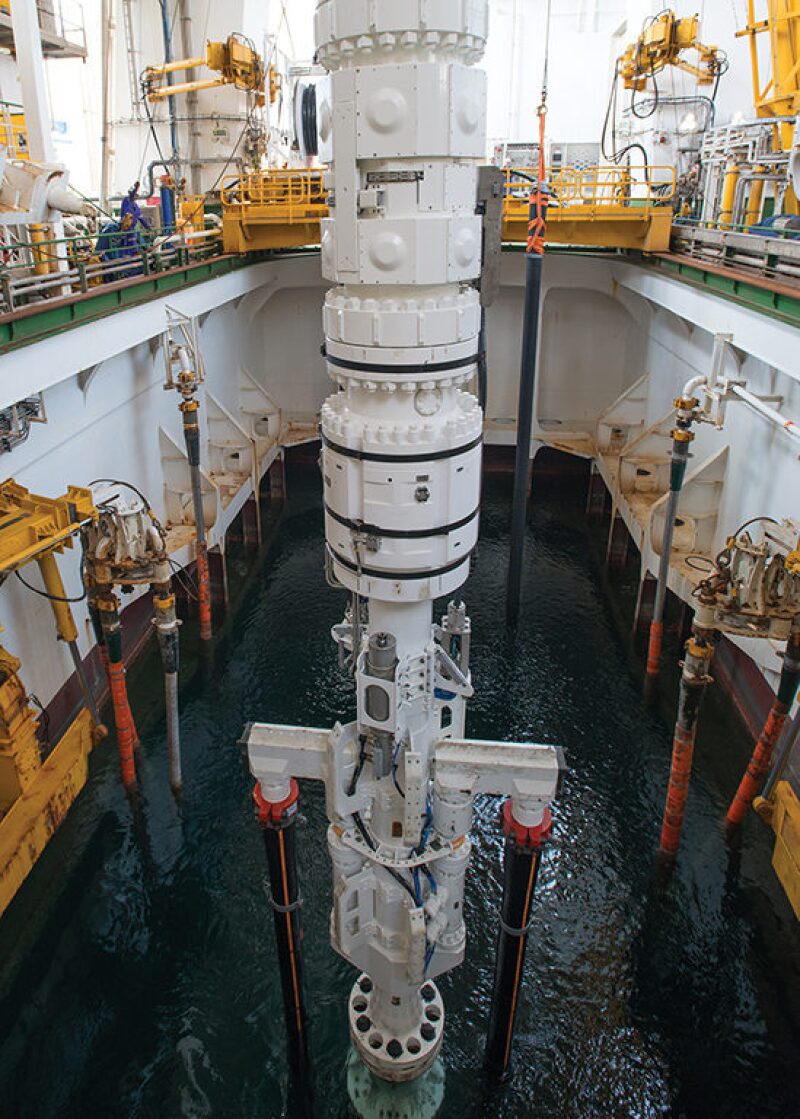
The testing provided an opportunity to capture lessons learned and assign actions to enhance operational performance before the package was used on a live well. Roles and responsibilities between all parties were clearly understood from the time the equipment was being built and through the planning stage for its deployment, rigsite commissioning, and MPD service execution.
All Parties Must Be Aligned
It is vital that each player—operator, drilling contractor, and service company—understand its role in successfully expanding the availability and deployment of closed-loop drilling in the market. All parties must be aligned and work together for closed-loop drilling to become the standard.
As operators continue to embrace the technology, drilling contractors will continue to equip their rigs, and service companies will continue to develop and support the technology. Once rigs become equipped with closed-loop systems, utilization will naturally increase as MPD becomes the new way to drill.
Although MPD originated as a solution for “undrillable” wells, recent technology developments to improve drilling efficiency and enhance safety are driving the technique increasingly into the mainstream for onshore and offshore operations.