Oilfield testing firm Interface Fluidics says it is one step closer to reinventing the industry’s pressure-volume-temperature (PVT) testing portfolio after the development of a smaller, faster version of yet another laboratory stalwart.
Representing the newest alternative to the slimtube test is the micro-slimtube test.
A conventional slimtube test involves flowing gas through a sand- or glass-bead-packed metal coil that may be 1 to 4 mm wide and some 40 to 80 ft long to see how it mixes and mobilizes oil with samples also inside the tube. The test and subsequent analysis usually take a few months to complete.
For a generation, this has been considered time well spent by anyone preparing to invest millions of dollars to prop up an aged asset through gas-injection-based enhanced oil recovery (EOR).
But the times are changing.
Interface Fluidics’ innovation, which it developed in close partnership with Equinor, measures only about 1.5 in long and generates results in about a week—about 95% sooner than the conventional bench method. The new test also reduces costs by around 75% while using a reservoir fluid sample that’s 99% smaller (10 ml vs. 1 liter).
“It’s the same story over and over again—we’re miniaturizing the big stuff and putting it on a chip,” said Stuart Kinnear, CEO of Interface Fluidics. Founded in 2016, the Calgary-based firm helped introduce microfluidic technology to the oil industry with glass and silicon chips that it calls “reservoir analogues.”
A well-established enabler in the healthcare industry, microfluidic devices of various stripes are routinely used to rapidly screen new drugs or to study how blood cells move through tiny veins and capillaries.
In the upstream industry, Interface Fluidics is part of much smaller group of specialists proving that the devices are also ideal for screening production-enhancing chemicals and to study how oil moves about the tiny pathways of a reservoir rock (SPE 188895).
The firm first showed how this works by replicating reservoir rock samples onto its chips as an alternative to core flood experiments. For oil and gas producers and their chemical providers alike (SPE 189780), the lower-cost devices made it affordable to run dozens of tests to determine how various chemistries affect flow behavior in specific geologies.
An example of the minimum miscibility pressure estimates obtained from the micro-slimtube test. The number of data points generated is about an order of magnitude greater than the conventional technique. Source: Interface Fluidics.
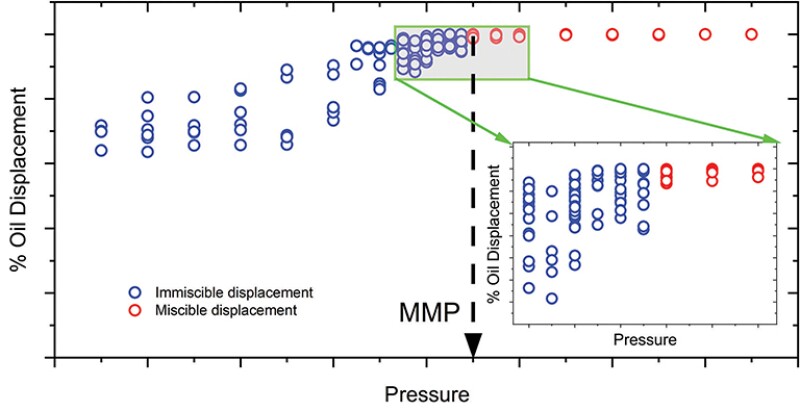
What’s Old Is New Again
Like coreflooding, the next target of disruption for Interface Fluidics has also been used for decades and is a long and expensive process.
Invented in the 1980s, the slimtube test is considered the industry’s most reliable tool for estimating an oil reservoir’s minimum miscibility pressure (MMP). In gas injection EOR projects, acquiring an accurate MMP is nothing short of essential.
This is because the MMP represents the point at which an injected gas, be it CO2, CH4, or something else, will optimally displace the remaining oil inside an oil reservoir.
Inject gas at a pressure above the MMP, and trapped oil droplets will swell out of their pore throats and start flowing en masse toward a wellbore. Lower pressures may still pay out additional barrels, just not ones worth the effort. Dial the pressures up too high though, and profits are needlessly eroded.
Simply put, the closer to the goldilocks zone that operators can get, the more efficient their EOR operation.
Interface Fluidics says its micro-slimtube has made that balancing act far easier—in part because “we have repeatability, whereas the slimtubes don’t,” said Kinnear.
He added that the MMP can change with reservoir drawdown or depending on the purity of the injection gas, further highlighting the advantage of being able to run many iterations to stay ahead of a moving target.
Additionally, Equinor has confirmed through a blind study that the micro-slim tube test delivers more than 10 times the number of measurements as its progenitor, and up to 20-fold, thus eliminating much of the educated guesswork that today’s MMP estimation practices require.
“The new micro-slimtube test will significantly lower the MMP test threshold, especially on the sample volume requirement,” said Camilla Vavik Pedersen, manager of remaining resources recovery at Equinor. She added that the “easily accessible MMP data will reduce the uncertainties” of gas-based EOR projects going forward.
The idea to marry the slimtube concept with a microfluidic device came from Equinor, which in addition to being one of the Interface Fluidics’ biggest clients is also one its biggest investors. Because it is difficult, costly, and often far too ambiguous, the Norwegian oil and gas company has made the development of new rapid-fluid-analysis technologies a top priority.
A chief reason the slimtube has remained the preferred tool for figuring out a reservoir’s MMP is because it is the only one designed to mimic the multi-contact miscibility process when displacing live reservoir fluids with real injection fluids. In other words, it is not a simulation—which makes it about as close to the real thing that petrotechnicals can get their hands on before committing to a multimillion-dollar project.
The importance of this aspect is not lost on Interface Fluidics; to the contrary, it is something the company is trying to seize and improve upon.
“We really are emulating the slimtube on a chip,” emphasized Kinnear. Just like the slimtube, “we have a long serpentine porous media because the important thing to capture in these experiments is the mixing phenomenon between the gas phase and the oil phase.”
Thanks in part to the flexibility of microfluidic chips—named so because they are made in a way similar to that used to make computer chips—it took Interface Fluidics and Equinor only about 12 months to go from the drawing board to building their first validated prototype.
Though industry downturns tend to dampen interest in EOR, Interface Fluidics’ long-term bet is that gas-injection operations will enjoy steady uptake as more oil companies look to store more CO2 underground or reduce their flaring by doing the same with associated gas.
Displacing the Incumbent
Driving the technology company and the operator to develop a new alternative was the fact that the traditional bench method has several significant drawbacks that have limited its usage and even called its reliability into question.
First, there is cost. For their diligence, operators can expect to pay no less than $100,000 for a single slimtube test. A micro-slimtube test is a quarter of this cost.
Second is time. Depending on the complexity and other factors, a conventional slimtube run takes 1 to 2 weeks with the MMP estimation taking between 1 to 4 months. In a micro-slimtube test, the flowing action is over within 15 minutes while a full analysis may take a week to complete.
Third is the aspect of repeatability mentioned earlier. Cleaning the tube out before another run can be made is a process that in itself takes days and may even alter the material inside the tube, introducing some variance from test to test. Each micro-slimtube can be made to match the last and each is used just once.
Then there is the issue of data, or lack thereof. “We will make 40 to 50 measurements in order to come up with your MMP. With a slimtube you get four [measurements],” said Kinnear, adding that with more data come a much smaller margin of error.
Equinor will present a technical paper coauthored with Interface Fluidics at the European Improved Oil Recovery Symposium in April. The focus of the paper will be on the validation of the new technology using live reservoir fluid samples and historical MMP data from three of Equinor’s oil fields.
The firm is also forming a joint industry study that will bring together various operators in an effort to expedite the industrywide acceptance of the micro-slimtube.
As noted in industry literature (SPE 200462), and as is often the case with emerging technologies, oil and gas companies need more experience with the new testing technology before they can embrace it as a replacement for traditional techniques.
Pedersen at Equinor said the technology has “imminent” potential as a standalone test. “However, for the new technology to roll out and broadly replace the conventional slimtube, there is still some way to go,” she said. “Pressure limitation and the capacity to handle entire PVT measurements are the main obstacles to overcome.”
For Further Reading
SPE 200462 Measurement of Minimum Miscibility Pressure: A State of the Art Review by Birol Dindoruk, Shell International; Russell Johns, Pennsylvania State University and EMS Energy Institute; Franklin M. Orr, Stanford University.
SPE 189780 Nano-Particle Surfactant in Hydraulic Fracturing Fluids for Enhanced Post Frac Oil Recovery by Harvey Quintero, Mike Mattucci, Robert Hawkes, Kewei Zhang, and Bill O’Neil, Trican Well Service Ltd.
SPE 188895 Rapid Microfluidic Analysis of Thermal Foam Stability at 250 Degrees Celsius by Bo Bao, Interface Fluidics Ltd.; Aaron Sanders and Ginger Ren, Stepan Co.; Thomas de Haas, Interface Fluidics Ltd.