Cyclic gas injection combined with modern technologies such as horizontal drilling and hydraulic fracturing has achieved promising results in low-permeability formations. This paper focuses on the effects of injected-gas composition and fracture properties on oil recovery, concluding that cyclic gas injection in hydraulically fractured shale oil reservoirs is feasible for improving oil production substantially over primary production.
Introduction
Cyclic gas injection is an effective and quick-responding enhanced-oil-recovery (EOR) method in intensely naturally fractured or hydraulically fractured reservoirs. The short payout is a characteristic that should attract industry’s interest in investing in these types of projects. Recent studies showed that cyclic gas injection could be a viable method to improve the oil recovery in shale oil reservoirs, but those studies were performed on the basis of black-oil models without detailed analysis of the phase behavior of the reservoir-oil/injected-gas system. The reliability of using the black-oil model to simulate the cycling of gas/condensate reservoirs is questionable because the two-component description may not be able to represent the active compositional phenomena adequately. This paper describes the use of an equation-of-state (EOS) approach to model the phase behavior of the oil and injected-solvent system.
Description of Models
The reservoir-fluid-composition data are from the published data of the fifth SPE comparative solution project, which aimed to illustrate the comparison of results between a four-component black-oil miscible-flood simulator and a fully compositional reservoir-simulation model.
Minimum-Miscibility-Pressure (MMP) Determination
Local displacement efficiency by gas or solvent injection is closely dependent on the MMP. Most gas- or solvent-injection cases operate in a regime in which true miscibility is not achieved; however, high recoveries still could be attained. The analytical method for MMP determination focused on finding the key crossover tie-lines for a dispersion-free displacement when one of the key tie lines becomes a critical-tie line (a tie-line of zero length). This paper shows the use of a cell-to-cell simulation method to determine the MMP of the given solvent composition and reservoir fluids. The pseudoternary diagram is generated from the calculations to study the vaporization or extraction process and interprets MMP as 3,440 psi. The multiple-contact miscibility occurs at approximately 3,400 psi, and a very small increase in recovery is observed at higher pressures. A slimtube simulation model also was developed that has good agreement with the MMP calculated by the tie-line method.
A swelling test was simulated by varying the proportions of injection gas mixed with original reservoir oil. The initial reservoir pressure is 6,425 psi, which is far above the bubblepoint pressure of 2,302 psi. When carbon dioxide (CO2) dissolves in oil, the liquid volume will expand. With the increasing injection percentage of CO2, the saturation pressure decreases and easily reaches first-contact miscibility with the equilibrium-reservoir-oil mixture. CO2 is a favorable alternative injection fluid for implementing oil-recovery processes because CO2 has the advantage of extracting or vaporizing some hydrocarbon components when it comes into contact with reservoir oils.
Because of the complex propagation of induced hydraulic fractures in shale gas reservoirs associated with the interaction with pre-existing fissures or natural fractures, it has been suggested that modeling the complex fracture network be classified into the following three categories:
- Planar hydraulic fractures provide the dominant conductive flow path to the wellbore if the injected proppant is concentrated mainly in the single hydraulic fracture.
- Planar hydraulic fractures act as the primary flow path to the wellbore supplemented by the natural fracture if there is a slight amount of fracturing-fluid leakage.
- The natural-fracture network dominates the flow path in the gas reservoirs if the proppant is distributed evenly in the entire fracture network.
According to the classifications of stimulated reservoirs, the reservoir simulation in this paper is separated into the following two stages:
- Investigate the cyclic-gas-injection EOR in only naturally fractured shale oil reservoirs.
- Investigate the huff ’n’ puff EOR in hydraulically stimulated shale oil reservoirs combined with natural fractures.
Simulation Results and Discussion
A dual-permeability model was used to simulate the natural-fracture network. The dual-permeability model allows communication between matrices of adjacent gridblocks in addition to the expected interblock fracture-to-fracture flows and the matrix-to-fracture fluid flow. The natural-fracture network is assumed to be contained within an orthogonal system of continuous, uniformly spaced, and constant-width fractures.
The reservoir model used 80 gridblocks of 50×50 ft to simulate a unit fracture network. This study examined the effect of grid refinement on oil recovery by performing a series of numerical sensitivity calculations. Using 4×20×1 2D gridblocks produces results similar to those of the far-more-refined 10×50×1 gridblocks, which is good enough to eliminate the error caused by numerical dispersion. From these results, the authors concluded that a 4×20-grid-discretization dual-permeability model was able to model the rapidly varying pressure in the fractures properly.
A comparison was made of the oil recovery for the four-component model and that for a fully compositional model for the scenario in which the average reservoir pressure was maintained well above the original saturation pressure and in the vicinity of MMP. Although the black-oil model gives results close to those of the compositional model, the black-oil model lacks the ability to consider the mass transfer between injected solvent and reservoir oil. Vaporizing/condensing gas-drive processes control the development of miscibility in gas displacement in which gas extracts intermediate-molecular-weight hydrocarbon components from oil, and oil may take up components from the gas phase. For an immiscible condition, the black-oil model gives lower oil recovery compared with the compositional model because the black-oil model cannot carry condensable liquids in the gaseous phase.
Reducing fracture spacing from 200 to 50 ft would result in an almost six-fold increase in the cumulative-oil-recovery factor. Results show that natural-fracture spacing has a significant effect on EOR. The complex fracture network is critical to well productivity in shale reservoirs because it maximizes fracture-surface contact area with the shale through both size and fracture density. The well-production performance in shale oil reservoirs is strongly dependent upon the fracture complexity. If the fracture density exceeds a certain point in the fracture network, the addition of hydraulic fractures would not improve oil recovery significantly.
CO2 Huff ’n’ Puff
CO2 is believed to be a favorable alternative injection fluid for implementing EOR projects. The oil recovery shown in Fig. 1 (above) is based on control of maximum allowed bottomhole injection pressure because the well’s maximum injection rate is set purposely at a high value that cannot be maintained.
The results shown in Fig. 1 indicate that natural-fracture density is the dominant factor that dictates reservoir drainage area and well performance; increasing fracture permeability with hydraulic fracturing has a diminishing effect on EOR when natural-fracture conductivity reaches a certain value. The conductivity requirements for cyclic gas injection to enhanced recovery in a 0.0001-md case are not as critical as fracture spacing is. Fig. 1 shows that reducing the natural-fracture spacing from 200 to 50 ft results in a 50% increase in oil production, more than is provided by induced fractures. However, it is important to note that the model assumes that the conductivity of the natural fractures is constant at 4 md-ft. In the field, without hydraulic fracturing, the conductivity of natural fractures is not likely to reach 4 md-ft. More importantly, natural-fracture-network properties (conductivity, density, size) are highly dependent on hydraulic fracturing.
When reservoir pressure is above the MMP (2,300 psi), CO2 flood will form a miscible displacement. Because of the constraint set up for the producing well (flowing bottomhole pressure no less than 2,500 psi), the CO2 huff ’n’ puff process will be fully miscible. As cyclic CO2 injection continues through 20 cycles, there is an increasing amount of CO2 retained in the oil phase. This loss of CO2 to the oil-production cycle is actually a form of geological storage because CO2 will be contained within the reservoir. Increasing the amount of CO2 dissolved in the oil results in reduction of oil viscosity from the initial 0.295 to 0.08 cp, which allows the oil to flow more easily toward the production well. The CO2-cycling process can be repeated several times, but the oil-recovery efficiency decreases with the number of cycles (Fig. 2). Cyclic CO2 stimulation can be useful in recovering shale oil when polymer flooding is not a good candidate in shale rocks. It is important to determine what injection time in each cycle would be most efficient. Longer injection time will allow the reservoir pressure to continue increasing, but it cannot exceed the maximum allowed bottomhole injection pressure of 7,000 psi. On the other hand, it will result in loss of production time during the injection period. Oil will be pushed away from the fractures by long injection times, making it more difficult to produce back.
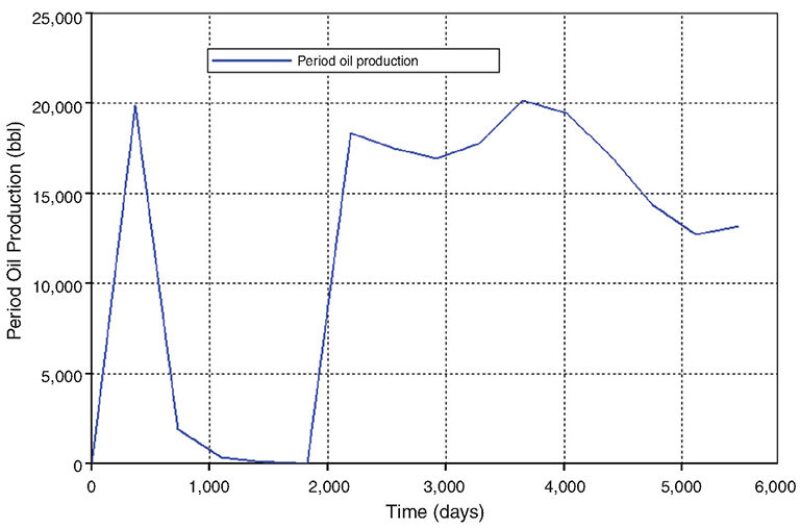
Summary
The objective of this paper is to evaluate the response of cyclic gas injection as an EOR method in intensely naturally fractured and hydraulically fractured reservoirs by use of a compositional model. The compositional model was compared with a generated black-oil model to show that they give similar results in the case of average reservoir pressure maintained above MMP by gas injection to repressure the reservoir. Detailed reservoir black-oil and gas/condensate pressure/volume/temperature characterization analysis was performed to illustrate the lean-gas-injection and CO2-injection mechanisms. A series of slimtube simulations was performed to study the interaction of injected solvent with reservoir oil. Miscible- and immiscible-gasflooding performances were compared by keeping the injection pore volume the same for each case. When injection-solvent enrichment exceeds a certain value, miscible displacement can happen at a lower pressure than with pure-solvent injection. Enriched solvent and CO2 achieved miscible displacement by a small amount of pore volume injected. In this case, they performed better than pure solvent and C1 because it is difficult for C1 to develop miscible displacement with reservoir oil at low pressure.
The effect of fracture spacing on oil recovery was investigated in this paper. Simulation results indicate that smaller fracture spacing is constructive to improving oil recovery in shale oil reservoirs. The primary decision when designing fracture treatments in shale oil reservoirs is to exploit fracture complexity. The role of hydraulic fracturing should be maintained because high pressures from hydraulic fracturing may cause slip in the natural fractures, increasing their conductivity. As cyclic CO2 injection continues in 20 cycles, there is an increasing amount of CO2 dissolved in the oil, resulting in oil viscosity decreasing from an initial 0.295 to 0.08 cp, which allows the oil to flow more easily toward the production well. The CO2-cycling process can be repeated several times, but the oil-recovery efficiency decreases with the number of cycles.
This article, written by Special Publications Editor Adam Wilson, contains highlights of paper SPE 169069, “Compositional Modeling of EOR Process in Shale Oil Reservoirs Stimulated by Cyclic Gas Injection,” by Tao Wan, Xingbang Meng, James J. Sheng, SPE, and Marshall Watson, SPE, Texas Tech University, prepared for the 2014 SPE Improved Oil Recovery Symposium, Tulsa, 12–16 April. The paper has not been peer reviewed.