Diagnostic fracture injection tests (DFITs) have gained widespread usage in the evaluation of unconventional reservoirs. In typical field operations, pressure is measured at the wellhead, not at the bottom of the hole. The bottomhole pressure (BHP) is obtained by adding a constant hydrostatic head of the water column to the wellhead pressure (WHP) at each timestep. One can question the soundness of this practice because of significant changes in temperature that occur in the wellbore, leading to changes in density and compressibility throughout the fluid column.
×
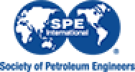
Continue Reading with SPE Membership
SPE Members: Please sign in at the top of the page for access to this member-exclusive content. If you are not a member and you find JPT content valuable, we encourage you to become a part of the SPE member community to gain full access.