It would be an oversimplification to say that during the initial push to deep water in the mid-1990s, no one knew how long these fields would produce. Armed with 20 years’ worth of hindsight and steadily advancing technology, it is clear that many of these early discoveries will produce beyond their anticipated design life.
This is especially true in a low-priced oil market. It makes sense to keep a known producer producing, as opposed to taking on the cost and risk associated with new exploration and development.
The key to extending the life of floating production units (FPUs), as with anything production-related, is to accomplish what needs to be done safely, economically, and without shutting in the wells. Fortunately, as reservoir and development technologies have advanced, so have intervention methods. As an added bonus, a better understanding of materials interaction and improved monitoring tools allow newly installed systems the capability to outlive original equipment.
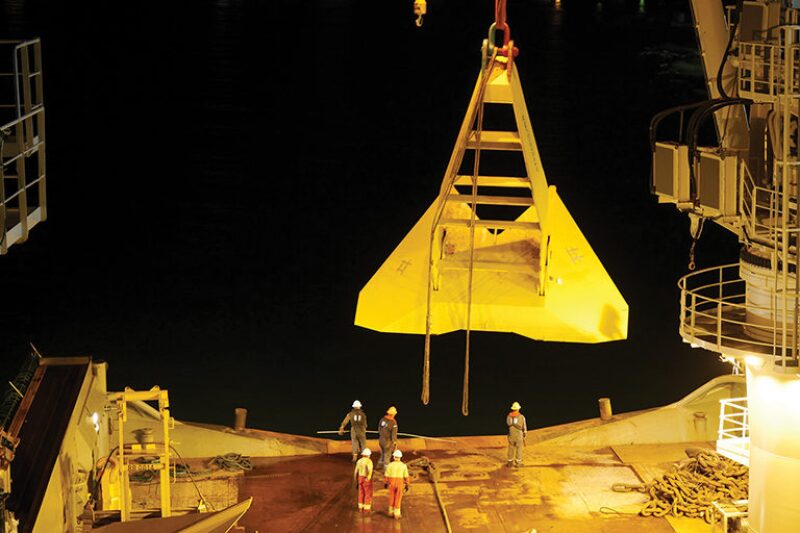
Although deepwater mooring systems are designed with redundancies in place, it is not unheard of for one, or even two, lines in a system to part without the operator’s knowledge, said Rizwan Sheikh, senior metocean engineer at BMT Scientific Marine Services.
With the loss of one mooring line, an FPU on an overdesigned mooring system may simply drift over to a new equilibrium. As long as this new location is within the station-keeping parameters of the vessel, the failure may go undiagnosed.
Many top-moored systems can still hold an FPU on station with multiple line failures. The problem is that if these lines fail without the operator’s knowledge, then any subsequent failure could lead to an unzipping, or total failure, of the system.
Bull's Eye Positioning
Strain gauges and other sensors are designed to monitor line tension and would report a parting of a mooring line as a sudden drop in tension; however, these gauges are prone to failure over time and can be difficult to access for maintenance and repair. Also, since many of the older, first-generation FPUs did not have monitoring systems installed, the production vessels rely on their watch circle to ensure that they are remaining on station.
The watch circle, a sort of bull's eye, uses GPS readings to tell the FPU how close it is to the optimum position for its riser system. There are excursion limits for these systems and, beyond that, what is considered the design limit.
If the vessel strays outside the “design offset of the system,” it may be necessary to shut in some or all of the wells. It also indicates a problem with the mooring system.
However, Sheikh said the watch circle gives the operator too little information, too late. By the time a vessel drifts out of its watch circle, there is already a serious problem with the mooring system. Because of the redundant design and the generous size of the watch circle, a vessel can be operating with one or two failed mooring lines and still be well within its design offset.
TLP Tendon-Based Mooring
Intecsea’s floating systems business unit focuses much of its brownfield and life extension work on FPUs. Jim Yu, global subject matter expert of tendons and risers at Intecsea, said the company is working with several oil companies on tension leg platforms (TLPs) and semisubmersibles in the US Gulf of Mexico, although most of the FPUs have not yet reached their design life.
TLPs are unique among deepwater platforms because they rely on rigid steel “tendons” to keep them on station. These tendons have a protective coating and are equipped with anodes to protect them from the corrosive environment. The tendons are also outfitted with fairings or strakes to resist vortex-induced vibration (VIV) during the installation stage.
Although one of the TLPs has a number of years left on its design life, the operator plans to use the structure as a hub facility for many more years. To ensure the integrity of the FPU, the operator brought in Intecsea to evaluate the condition of the platform and provide a prediction of its remaining service life.
The inspection and refurbish plan for the tendons and the top-tension riser was then developed.
Bill Greiner, manager of the naval architecture department at Intecsea, said that while it makes economic sense to perform this type of maintenance on a TLP, the tendons are not designed to be changed out, except in a case of failure. Replacing any of the tendons would be uneconomical, which emphasizes the importance of regular inspection and maintenance of these facilities.
Regulatory Oversight
As with other FPU mooring systems, the process begins with contacting the contractor that built and installed the tendon system. This makes available the original engineering and design plans to Intecsea. In some projects, the company is the original engineering firm that designed the FPU.
This type of life extension program requires regulatory approval, although there are no clear-cut regulations in place for such work. Instead, the company performs the engineering work and assists the operators in preparing and presenting operation plans to the appropriate regulatory body for approval based on the specifics of the platform.
Typically, the US Bureau of Safety and Environmental Enforcement (BSEE) has oversight. The US Coast Guard (USCG) is also involved in the review process of the FPU. A third party verification analysis is typically included in the operator’s plan.
As part of the plan submitted to BSEE and USCG, Intecsea prepares an inspection plan for the tendons and riser to identify any weak links in the system. As with conventional mooring systems, some of the TLP tendon components present a challenge to visual inspection. In other cases, more advanced technology is required in addition to visual inspection. Yu said the use of acoustic and ultrasonic equipment is required for identifying possible cracks, corrosion, or other damage to the tendons. Also, it is important to detect problems with the coating and cathodic protection.
Mooring Repair Plans
The permanent mooring lines are commonly in need of updating and replacement on older FPUs. The assessment, repair, and/or replacement of these lines can be costly if not properly planned.
Kent Longridge, a chief engineer at InterMoor, said cost is one of the reasons why contractors emphasize the importance of a mooring repair plan (MRP) to their customers. If the mooring contractor is involved with the planning process early, then the savings can be substantial.
To create an MRP, companies that supply mooring and installation technology such as InterMoor first look at the as-built mooring configuration to determine which components make up the mooring system and to identify which equipment is available on the FPU for the repairs.
Based on the as-built specifications, the contractors design an MRP that includes procedures for offshore operations and the identification of long lead-time mooring components and installation aids.
A working knowledge of regional ports and harbors and the installation vessels in the area enables the identification of installation vessels with the capabilities to do the work. The contractor also identifies bases of operation (i.e., for equipment storage, maintenance, staging, and mobilization) and estimates cost and scheduling.
Understanding the as-built configuration and the operational functionality of the on-vessel mooring equipment is essential. For example, most production facilities include mooring winches that are installed on the topsides. Winches that were originally used to wind up or pay out the mooring lines during installation may be useful in completing repairs and replacements. However, in cases in which the winch may have been set 20 years earlier, the equipment may no longer be operational. Making use of on-board mooring equipment is just one way of streamlining the replacement operation.
Access to installation vessels and equipment is another key component of an MRP. Typically, anchor handling vessels can be used for this work and are more cost-effective than contracting a dedicated installation vessel with more capacity and capability.
Locating and securing equipment storage and maintenance space for spare mooring components saves time, especially in remote regions. Dedicated storage facilities allow the operator to preorder the necessary materials and house them in one location. This avoids the cost and delays of acquiring and importing long lead-time parts and equipment.
A viable base of operations should be identified. In selecting a location, the depth of the channel and adequate space for staging of equipment are key factors. It is also important to have adequate crane capacity for handling the mooring systems and components, and local transport vessels or barges for mobilization to form a contingency plan.
Mooring systems are designed with built-in redundancy and should outlast the design life of the production facilities. This feature makes it relatively easy to manage the timing of a refurbishment program to maximize savings and minimize disruption on the platform.
Mooring Inspections
An area of growing interest among operators is mooring integrity management. Visual in-place inspection of off-vessel mooring components using a remotely operated vehicle (ROV) is an aspect of integrity management.
The expertise required in examining and assessing the condition of the mooring components is also critical. The accurate documentation and record keeping of videos, pictures, and results is essential for the comparisons of results from previous and future inspections.
A potential issue with in-situ inspections of mooring systems is the possibility that the inspection itself may affect the condition of the components. For example, an ROV is dispatched to photograph mooring lines in the water column, but many of the critical components on the seabed have become covered with silt and mud. The only way to expose the buried section is to tension the mooring line, which may increase its fatigue.
Likewise, mooring components situated near the oxygenated waters of the splash zone may become covered in rust or marine growth such as barnacles.
The splash zone is the area immediately above and below the mean water level in which the platform is installed. Tides cause the water level to rise and fall, alternately wetting and drying the exposed metal of legs and risers.
The soft and hard marine growth can be blasted off with high-pressure water jets mounted on an ROV; however, this action exposes fresh steel to the corrosive seawater, possibly inducing more corrosion.
Vortex-Induced Vibration
TLP tendons have their own challenges. Marine growth buildup may interfere with the view and inspection of tendons, and the performance of fairings or strakes which protect against VIV also may be affected by the buildup.
“Historically, industry has not done a good job of maintaining VIV equipment,” Yu said.
If the marine growth is soft, it can be removed by an ROV using high-pressure water jets. Hard growths, such as barnacles, may develop over time and are more difficult to remove. In this case, it is often necessary to replace the fairings or strakes to meet the platform's extended service life.
Most of this maintenance can be conducted using an offshore service vessel and an ROV. If a top-tensioned riser needs to be pulled, a workover rig is required.
Generally, a life extension project lasts from 1 to 2 years. Although these facilities are typically designed for a life of 20 years, often the original design carries certain design margins that potentially allow the service life to be extended from an additional 7 to 15 years with an inspection and maintenance program.
While inspection programs can identify damage and extend the life of an FPU, Alaa Mansour, a marine engineering manager at Intecsea, said the collection and analysis of the platform’s field history may identify existing fatigue damage and thus predict the most likely areas for failures.
Something as simple as a tension monitoring system can be used to log fatigue events throughout the life of the facility. Even during a single extreme event, much of the fatigue life in these systems can be spent, Mansour said.
Still, many FPUs either do not have such a system, or do not collect data on a reliable basis. Reaching out to operators and reviewing this data in advance of the design life of a facility can save money and help avoid the shutting in of operations for maintenance.
Response Learning System
Another solution that is just coming on the market relies on a mathematical model to evaluate the condition of a mooring system. Companies such as BMT use metocean data, the vessel’s GPS location, motions, heading, and draft to predict FPU movement. Deviation of the FPU’s actual movement from its predicted location indicates a problem.
Sheikh of BMT said the topside-based response learning system concept is simple, but the math behind it is complex. To begin with, a baseline inspection is conducted to ensure that the station-keeping systems are working properly.
It requires several months to “train” the model's algorithms to the actual motion of a given vessel. But, given time, Sheikh said the system can predict where the vessel should be within a few meters. Even a slight deviation from the predicted location may indicate a problem with the mooring system.
The key to the predictive algorithm is how the vessel responds to the sea states. The more field data available to the model, the more accurate the resulting prediction.
Sheikh compared the vessel’s response to sea states to that of a buoy. If the sea state is known and the vessel’s response is observed, it is possible to predict its response in other situations.
Although not yet applied in the field, these observations may shorten the lead time required to get such a model in place and provide a detailed history of how the FPU reacts to changing weather and seas.
While it may work by itself for older vessels, the modeling program may also complement a mooring management system that includes physical sensors such as strain gauges. Sheikh explained that the software provides an overall picture of where the vessel should be positioned, and the strain gauges and other monitoring equipment describe the condition of individual mooring lines.
The Bottom Line
If the on- and off-vessel mooring components are properly maintained, monitored, and inspected, it is possible to qualitatively evaluate a mooring system’s remaining service life and plan accordingly. Mooring repair plans enable a cost-effective solution for the repair and replacement of mooring components.
This approach enables operators to realize the value in establishing a maintenance program as part of a broader, life extension effort for their aging FPUs. Such was the case with ExxonMobil’s Zafiro Producer, for which InterMoor did the mooring replacement work.
The Zafiro Producer is a floating, production, storage, and offloading vessel that began production in the Zafiro field offshore Equatorial Guinea in 1996. A converted oil tanker, the vessel has a 12-point mooring system made up of chain and jacketed, spiral-strand wire rope.
Longridge said InterMoor used the existing equipment to remove and inspect each of the mooring lines one at a time. After inspection, it was found that nine lines needed replacement. Also, two of the Stevpris Mk6 anchors were replaced with updated models.
The whole project, part of a broader refurbishment, took only 4 weeks to complete and was accomplished without interruption of production operations on the vessel. The work was conducted using vessels already on site, and there were no accidents or injuries.
For Further Reading
OTC 25449 Serpentina FPSO Mooring Integrity Issues and System Replacement: Unique Fast Track Approach by S. Bhattacharjee, ExxonMobil Production Co.; S.M. Majhi, Granherne-KBR; D. Smith, ExxonMobil Upstream Research Co.; and R. Garrity, Delmar Systems

William Furlow is the senior manager of business development at SPE.