More precise measurement can create a dilemma.
One example is the precise fluid flow measurements used to control managed pressure drilling (MPD) systems.
By measuring differences as small as 1 bbl in the drilling fluid flowing out of a well compared to what flowed in, these closed well designs are able to quickly adjust the downhole pressure to manage an influx, or drilling fluid loss.
MPD has allowed development of difficult formations, particularly in Southeast Asia, where conventional drilling methods would have taken far longer for many wells, if they could have been drilled at all, in unpredictable carbonate formations prone to massive fluid losses. One MPD advocate, Peter Aird, a drilling consultant who is founder of Kingdom Drilling Services, said MPD should stand for “makes problems disappear.”
The dilemma is a result of regulations prohibiting offshore drillers in the US from “knowingly” taking a kick. The rule was written back when the smallest kick that a driller could knowingly have taken was roughly 10 times larger than what an MPD system can accurately measure.
Drillers have been trained to react to kicks, which can be a warning sign of a potentially bigger surge of oil or natural gas to come, by resorting to traditional well control methods, beginning with using the blowout preventer (BOP) to shut in the well below the riser. That approach is costly, time consuming, and can damage the well, forcing the operator to abandon a section of the hole.
The dilemma is not just a product of regulation. For managed pressure systems to work efficiently, thorough training is required so drillers understand a method that requires them to think differently. Often MPD systems are brought in relatively late in project planning, leaving little time to get workers comfortable with the process, said Robert Ziegler, president of RZI Deepwater, a drilling consulting firm.
“The problem for early MPD operators is the driller sees 1 bbl of extra flow and because that could mean there is gas in the marine riser, the reaction is to go to well control rather than circulating it out” while drilling ahead, said Paul Sonnemann, vice president of technology for Safekick, a company that designs and builds equipment and software used for MPD.
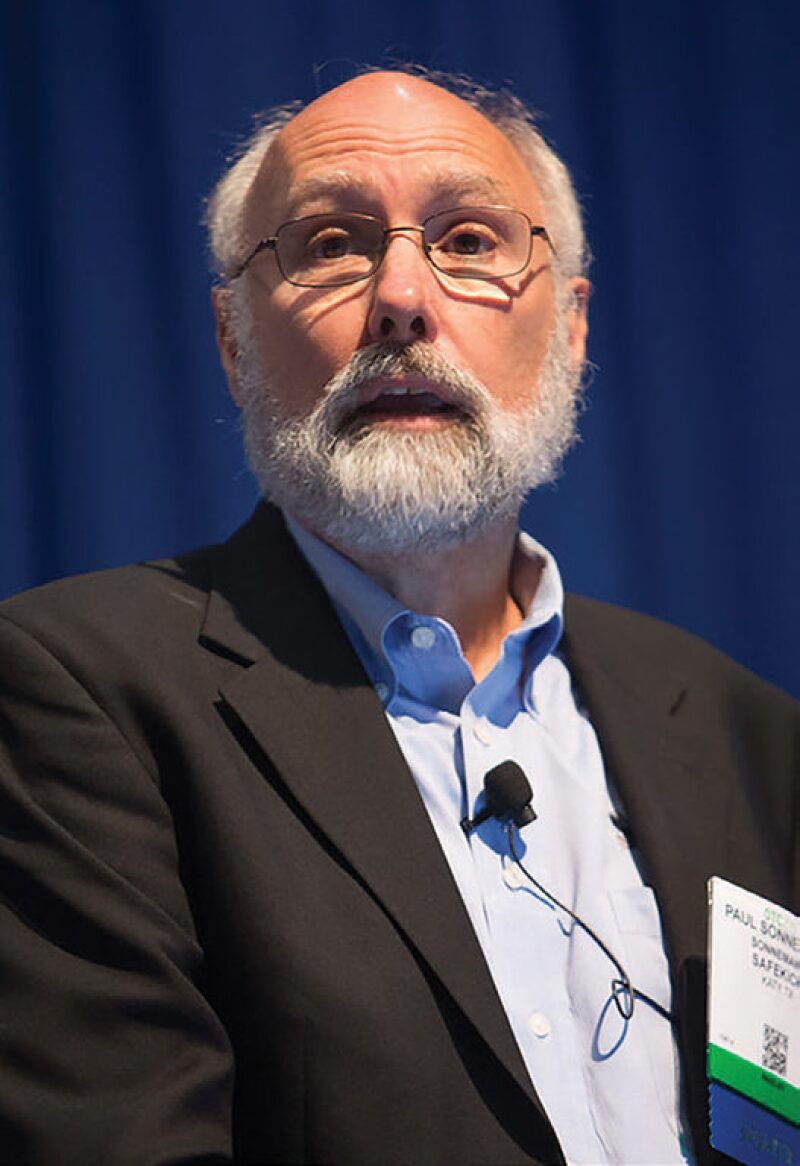
He made that comment during a panel discussion on managing gas in the riser with eight managed pressure drilling experts at the 2015 Offshore Technology Conference, all of whom are working to spread the use of various forms of MPD. While changes in fluid levels may be due to influxes of oil, water, and/or natural gas, the biggest safety concern is gas.
For MPD to live up to its full potential in the US, regulators and operators will have to answer the question: If gas is allowed into the riser, what is the best way to handle it? Sonnemann said, “If you do not think that through now, you will not get the benefit of MPD.”
He and the other panelists recognized the risks posed by gas. If not properly controlled, the hydrocarbon that is in a liquid state as it enters the riser can expand enormously if it reaches atmospheric pressure, with results ranging from disturbing incidents where mud shoots out of the riser onto the drilling floor up to deadly accidents.
For drilling to be done more efficiently and safely using MPD, those who have used the method say the regulations and training will need to be adjusted to take advantage of the ability of these systems to detect small variations in fluid flows and to quickly stop an influx by adjusting the pressure downhole while continuing to drill.
That requires accepting that a small amount of gas or oil that may have come into the well during a small kick—quantities too small to be noticed in a conventional system—will travel up the riser. MPD experts say that if the system is working normally, those influxes are no larger than what flows into a well now when the mud pumps are shut off during connections, reducing the weight of the mud used to stop fluid influxes.
An MPD system, using Coriolis meters and mud tank measurements, can reliably detect differences as small as 1 to 2 bbl. The minimum difference in a mud tank measure that can be relied on to detect an influx, ranges from 10 bbl to 25 bbl. It is hard to pinpoint the average margin of error on mud tanks. Estimates vary based on sea conditions, the measurement system, the diligence of those doing the measurements, and the source of the estimate.
Knowing there has been a small influx, though, requires drillers to make a decision. “Before MPD, we knew we could have a 5 to 10 bbl kick, but because we could not detect it, we felt OK,” Sonnemann, said, adding, “Now we can have 1 to 2 bbl [kick] and we are terrified.”
Managing Gas
The makeup of the OTC panel showed the range of managed pressure methods being introduced in the US Gulf of Mexico. Two of the companies represented on the panel, Chevron and Statoil, are working closely with regulators to introduce a version of MPD called dual-gradient drilling in the US Gulf of Mexico. Each method manages well flows differently and will require different regulations. For example, Chevron pumps all the returning drilling fluids out of the riser at the seafloor and up a separate pipe to the surface, so gas should not get into the riser.
One scheduled panel member from Marathon oil was unable to attend because he was working on a company project to install the most widely used managed pressure method, which applies back pressure by capping the top of the riser.
Companies moving to MPD are looking for a safer, more efficient way to drill wells where the window between the pressure needed to control the well and the level that could damage the wellbore is really narrow. When drilled using conventional methods these often are beset by long delays and cost overruns.
“We’ve pretty much already drilled the easy offshore prospects, and are now having to drill in ultradeepwater in the Gulf of Mexico,” said Don Hannegan, an MPD pioneer in charge of strategic technology development-MPD at Weatherford Secure Drilling Services. Similar challenges are found in other offshore basins. “I am convinced that by the end of this decade, perhaps as much as 40% of deepwater wells globally will be drilled with one or a combination of the variations of MPD.”
While the US Bureau of Safety and Environment Enforcement (BSEE) has not commented on MPD regulation, those involved with applying these methods say the offshore regulator has been quietly asking for information about MPD.
Safety is the top priority for BSEE, which is looking for ways to better detect and respond to kicks using conventional drilling methods, said Dan Fraser, an industrial safety expert from Argonne National Laboratory who is advising BSEE on well control issues. During a presentation at the 2014 SPE Annual Technical Conference and Exhibition on the need for better industrywide data on kicks and response time, he said that a “closed system would be a big win.”
In a paper (SPE 173153) delivered at this year’s SPE/IADC Drilling Conference and Exhibition in London, Fraser said MPD is able to detect smaller kicks faster, and “could reasonably reduce the overall number of kicks by as much as half. MPD can be viewed as a kick ‘inhibiting’ technology.”
But Fraser emphasized he does not speak for BSEE, which is doing its own evaluation of MPD and kick detection methods. The drilling method has been used elsewhere in the world, but the efforts in the Gulf of Mexico stand out because the water and the wells there are deep and demanding. Also, the area has often been a proving ground for ideas that have spread elsewhere.
“There are contractors on three continents with plans to make [riser control] modifications. Most of the deepwater industry in the future will include some kind of riser-top device,” Ziegler said.
He was referring to rotating control devices and annular shutoff valves that are used singly or together. They are often part of MPD systems, but can be used in other ways. They are not well control devices, like a BOP, but they can allow a driller to more precisely control a well while drilling.
“In most systems applying a little backpressure calms everything down,” said Colin Leach, president of Mulberry Well Systems, a drilling consulting firm. The options include bottling up the riser to give drilling teams time to figure out how to best deal with a large gas influx.
Introducing a new system for managed pressure drilling raises fundamental questions about how hydrocarbons behave in a well during drilling. Sonnemann co-chairs an ad hoc work group within the International Association of Drilling Contractors (IADC) on natural gas in risers, which is gathering information on how gas behaves in a riser and what to do if it gets in there.
What the group has learned so far challenges widely held views about gas behavior in enclosed risers, showing “reality is much better than our wildest imagination,” he said. Though the reality includes perils, they are often poorly understood, Sonnemann said, adding, “We need to improve our ability to realistically quantify even worst-case situations and learn how to best react to them.”
An Old Problem
While no driller wants hydrocarbons in the riser, it is not surprising to find them there. “In the deepwater Gulf of Mexico, there is likely to be oil with a small amount of associated gas in the returning drilling mud,” Leach said.
This becomes more likely in a one-mile long marine riser. As the water gets deeper, the riser represents more of the wellbore, increasing the chance there is gas in it, Sonnemann said.
One possible source is unexpected gas pockets encountered during drilling. Another is the small influxes that are a regular occurrence during connections. When connecting drilling pipe, the pumps are turned off, reducing the effective pressure applied by the moving mud, often allowing a kick. In a deepwater well, the time required for the drilling fluid to travel down to the bottom of the hole and back is so long that several connections may have occurred before it returns.
When asked at the 2014 OTC about whether having some gas in a riser is acceptable, Lance Labiche, then chief of BSEE’s district operations support section for the Gulf of Mexico Outer Continental Shelf Region, said that US regulators did not want to see gas in the riser, except for small quantities of connection gas.
For MPD drillers, that narrow exception does not resolve the dilemma, because the influx during a typical connection on a conventional well are below what a driller could observe using mud-tank measurements on rigs bobbing in the ocean. Managed pressure systems can reduce connection influxes by adding pressure to offset the impact of a pump shutoff.
Resolving the dilemma is not a current priority for operators seeking permission from US regulators to use MPD. For now those companies are focused on demonstrating to regulators that their systems work as safely and effectively as promised.
That strategy may mean they will be resorting to traditional well control methods for small kicks, which will significantly reduce the efficiency of a device designed to safely manage pressures without stopping.
The goal is to convince regulators that MPD methods are safer than conventional methods, even if a small influx is detected while drilling ahead.
The IADC has offered guidance for MPD operations, including a quick reference matrix for drillers visually sorting influxes into three categories, color-coded from green to red like a stoplight. The suggested responses range from a normal variation that can be addressed by adding backpressure, to a kick requiring traditional well control, Ziegler said.
It is a simple grid based on an estimate of the size of the influx, which is an amount that can be a matter of debate among drilling consultants. “The stuff that people have to figure out is not the MPD matrix. It is how to calculate the values to put into the MPD matrix,” Sonnemann said.
The green level is typically a variation of less than 5 bbl, which is a miniscule percentage of all the drilling fluid in a well and riser, Ziegler said. Interpreting whether a fluid flow change is a kick requiring well control, or just the normal variation in a column stretching out for miles, requires an understanding of the well, going back to the baseline well properties predicted during well planning.
With accurate flowmeters measuring fluid flowing in and out of a well, “we are able to pick up every hiccup” in the well, Leach said. “With modeling you can decide what the significant values are.” Those estimates provide a benchmark for drillers to decide if a flow rate change is out of the ordinary at that place in the well.