Over the past few decades, the upstream oil and gas industry has demonstrated marked improvement in safety performance as measured by traditional lagging indicators. This success has been supported by the development of safety management systems, improved training and equipment, as well as numerous guides on the most critical component: safety leadership. Organizations such as the International Association of Oil and Gas Producers (IOGP), Step Change in Safety, and Center for Offshore Safety (COS), to name a few, provide guidance and encourage leadership to actively participate in driving the message and expectations around leadership engagement on safety.
The SPE Technical Report Getting to Zero and Beyond: The Path Forward (March 2018) states that to achieve a culture of perfection, actions must be led from the top. In the context referenced in this article, leaders are those individuals in senior positions who are recognized by their organization as having responsibility for operations and can commit financial resources to reduce risk (the US Federal Aviation Administration would call this person an “accountable executive” per the regulations).
Many leaders commit to the aspiration of no harm to people, but they may need help on the substance and actions that will make a difference. The guidance documents from the organizations and technical report listed above provide sound foundations for messaging, as well as what follows in this article. The authors have had robust experience in safety culture and performance improvement, and where it succeeds or fails.
Start With the Basics
The first thing leaders must do is provide a Statement of Organizational Intent (SOI). An SOI starts with, but goes well beyond, the aspiration of No Harm. The SOI should cover what operational leaders will do to help improve the safety culture. This should be specific to the needs of the organization and include an honest assessment of the current state of safety. It is vital to understand what is going on at the front lines: (a) why are incidents occurring, and (b) what are the trends of the failures. The SOI will move past the superficial view that “incident rates are too high and therefore, we must do better.”
There is a need for more information on performance beyond the traditional lagging indicators of incident rates. A good starting point is adding near misses, observations, and incidents with a high potential for serious outcome. Beyond that, leaders need to identify measures of inputs that make a difference in performance. Traditionally this may have meant something like training hours, but that assumes the training is effective. The measures must include a view of strategic plans and implementation progress.
A means of tracking and verification of progress is needed as well. Senior leadership then must routinely, and personally, follow up on the progress and hold the organization accountable for following through to completion. If not, there can be elements within the organization who will simply wait out the strategies, knowing there is no consequence for lack of participation.
Leaders should also be involved in the review of incident investigations and follow through to closure of corrective actions. Metrics must be in place for timely investigations and reasonable target dates for completion. The leaders should set the expectations that incidents be thoroughly investigated and that the systemic failures are identified and addressed in a timely fashion.
Where organizations do not have a sense of urgency around investigations, a clear signal is sent that safety is only important when we have the time to get to it. If investigations are superficial or incomplete, it sends a message that problems won’t get fixed. If the causes are routinely listed as human error, violations, or complacency, then the organization appears as though there isn’t a willingness to challenge how work is done to look for sustainable improvement.
Leaders must also ensure that there is integrity and transparency in incident reporting and that their response is measured and guided by curiosity around the circumstances, not anger for the event. If reactions to incidents give the organization the feeling that it is better not to report, that is exactly what will happen. If the classification of incidents is strongly challenged and bent to the will of the leader rather than the regulatory or company requirement, it sends the signal that the numbers are more important than the truth or their people.
Another foundational component of the SOI is Hazard Identification and Risk Assessment. Most organizations already have this within their safety management systems. For those who don’t, it must be developed and implemented. For those who do, it needs to be assessed for effectiveness and improvement opportunities. Far too often, one of the common threads found during incident investigations is that employees failed to see the hazard or appropriately assess the risk of harm.
Lead the Improvement and Stay Involved
Strategic planning for safety improvement must be treated no differently from business financial planning with an annual process to assess the state of the company with routine oversight and follow-up. For many companies, the financial process is burdensome and may need to be decoupled from the safety planning cycle to allow for a focused effort from all involved.
The planning cycle must include senior leadership to start. Many leave it up to the safety function to develop plans and have them signed off by senior leaders. If that happens, there is a potential for missed buy-in from the leaders and possible misunderstanding as to why the focus is on particular areas. The plans themselves should be structured to allow local operations to build their own actions, rather than just being told what to do or what the objectives of the year are. Templates can be distributed that include a preface on the current state and identification of potential solutions to problems. Some may, by necessity, be extremely prescriptive so each operation must implement. Others may be higher level that accommodate local conditions and allow for creative solutions.
These plans then should be reviewed and approved by senior leadership. If they are only reviewed and approved locally, or solely by the safety function, it may send the message that senior leadership doesn’t have the time to be involved in the improvement process. Even if that isn’t true, the perception that it isn’t important up the chain can set the plans up for failure. Mid-level and front-line managers, who are self-motivated safety leaders on their own, will create and execute plans and see through to completion because that is who they are, not because someone above them says so. Others will observe the lack of interest from senior leaders and take that as a signal that it is business as usual.
Components of plans may include specific actions around the highest-risk activities as identified either by incidents or assessment of the top risks across the company. They should also include enough latitude for parts of the organization that may not experience the identified hazards to address their own high-risk hazards.
That brings up the next action senior leaders must take: Follow up on the execution of plans on a routine basis. This should include at least routine calls going over the progress and, better yet, site visits to discuss with local management and employees the impact of the plan elements. This will send a strong message throughout the ranks that the plans for improvement have full support from leadership.
Successful Performance Improvement and Culture Change
We need to move beyond showing concern for superficial measures of safety that focus solely on injury rates. In order to show leadership and concern for the well-being of the workforce, leaders must be involved throughout all aspects of performance, including planning for improvement. Following the guidelines above will help leaders positively impact safety performance and culture within their organization.
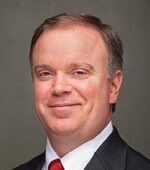
Tom Knode, SPE, is the vice president of industrial safety with Quantum AI. He more than 30 years of experience in HSE, principally in oil and gas, and has worked for Halliburton, Equinor, Kirby Distribution & Services, and vPSI. Knode has been involved in numerous safety performance improvement initiatives and has seen successes and failures and the circumstances contributing to both. He served on the SPE International Board of Directors as the Technical Director for HSE from 2008–2011 and has co-chaired five SPE HSE conferences and several workshops. He has published more than 20 articles focusing on safety leadership, employee engagement, and performance improvement. Knode holds a BS in geology from Texas Christian University and an MS in geology from the University of Texas at Arlington.

David King, SPE, enjoyed 35 years of employment in the oilfield services industry. Retiring from Halliburton after a 32-year career, he then served as CEO of Archer (8,300 employees at the time he joined). While at Halliburton, he was the chief HSE officer as well as the president of the largest division, completion and production, with 2012 revenues of $17.38 billion when he retired. King has served on the board of directors of large and medium-size service companies and operators. He has been directly involved and responsible for safety leadership in his executive roles and has coached other executives and junior leaders on safety from an operational perspective. King holds a BS in civil engineering from The University of Alabama.