Occidental: Learning While Drilling Faster
Molly Giltner smiled when she saw a text from a driller saying, “Reduced WOB. Continued to drill to bottom.”
For the senior drilling engineer at Occidental Petroleum, that cryptic note was a sign that a rig-based program providing a flood of data from wired drilling pipe installed on one rig could have a lasting impact on other rigs drilling in the Permian.
Specifically, it was shorthand for how a driller dealt with a problem—the mud motor was stalling while drilling hard, interbedded rock near the bottom of a horizontal well. Occidental drillers and engineers had figured out that it is faster and cheaper to reduce the weight on bit (WOB) than speeding ahead, which increased the risk of a breakdown and time lost for repairs.
The text message arrived after Giltner delivered a talk at the SPE/IADC Drilling Conference and Exhibition in The Hague. The paper topic was about improving drilling performance using downhole data from wired drill pipe and downhole sensors (SPE 194093).
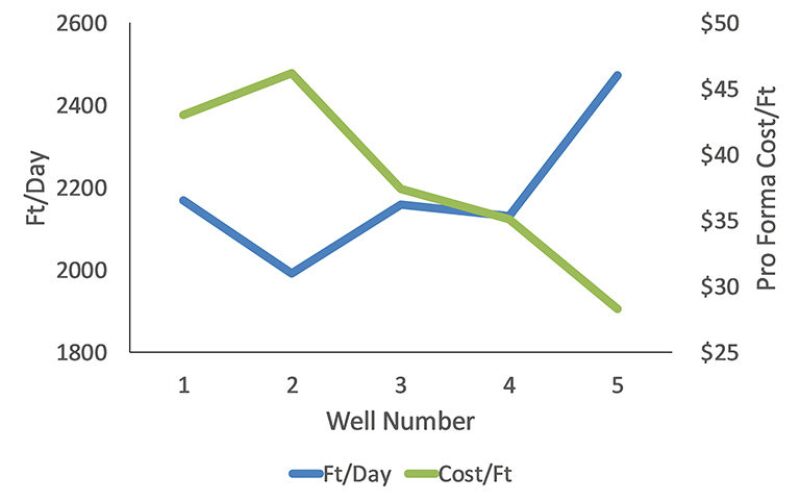
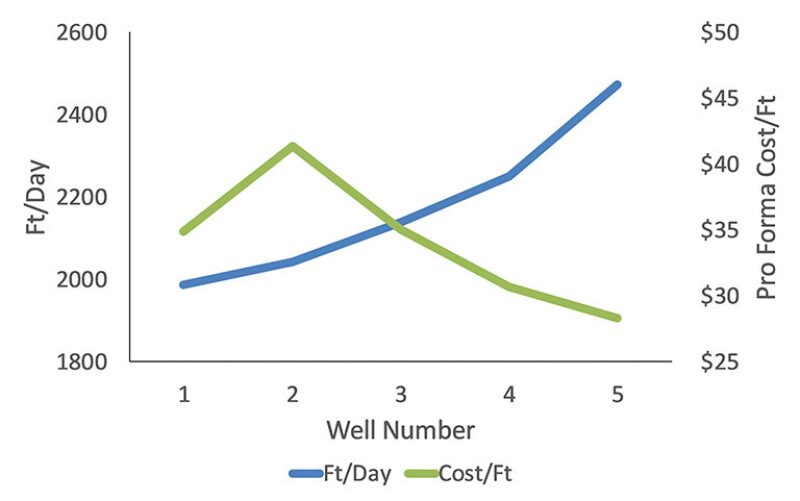
There was no mention of people in the title, but the majority of the talk was on the cooperative method used by teams on drilling rigs to use high-resolution data to figure out how to increase drilling productivity and pass on what was learned.
Wired pipe sending nearly 58,000 bits per second offers a lot clearer view of subsurface reality than mud-pulse telemetry sending 10 bits per second. To justify the cost of that quality, significant performance gains are required.
“If you do not translate that knowledge to the person on the joystick, he doesn’t do anything different, so what have you accomplished?” Giltner said. The data had to be part of a group effort, starting on one drilling rig and spreading to six others.
The hard part was developing and maintaining “a simple and effective way to capture that information and use it” to redesign drilling, she said.
The methods used were not new or unique. Occidental has a program to teach the physics of drilling to key rig personnel, including contractors. It built that process into the industry practice of creating a drilling parameters roadmap.
“It is nothing magic. It was knowledge sharing and an understanding of what you are drilling through,” Giltner said.
The potential value of that flood of data provided “a perfect opportunity to double down on the drilling improvement system” she said.
Focus on the Driller
The payoff was a 25% reduction in the drilling time through an intermediate hole section, and a 33% savings. Those pro forma estimates are based on reduced equipment costs and a lower cost-per-foot calculation using assumed hourly rates and equipment costs.
The focus of the system is on the driller using the available information to find a better way. “Rather than telling them what to do, which means you will do only as well as you did before, they describe what the data means and how to use it, allowing them to use their judgment. They were empowered,” Giltner said.
She described the approach to dealing with a drilling dysfunction: “We will go one way and try the conventional thing to do. Then we go the other way and we understand a lot more quickly.”
For example, drillers had been taught to react to torque oscillations by increasing the revolutions per minute and reducing the WOB. The Occidental rigs, though, found that in a particular section, increasing the WOB reduced the oscillations without having to make changes that slowed drilling. “It was better to not back off from every dysfunction we found,” she said.
The work began on the rig with wired pipe. “What made a difference was starting with a small group that was really into the project and then we brought in others,” she said.
Others joined in without an invitation. “They showcased a 10% rate of penetration gain and that got the attention of others who asked, what you doing? What is working? It snowballs,” Giltner said. The number of rigs involved grew as they saw the results when others learned to “drill smarter.”
Competition motivated others to change. Drillers wanted to be fastest, and company representatives do not want to be associated with mangled drill bits.
While other rig crews did not have the data offered by wired pipe, what was learned about the local problems and how to adjust to deal with them, enabled them in some cases to outperform the wired rig after the data convinced them that they needed to change their habits.
Those rigs had been drilling fast, but stops for repairs added days to the time it took to drill a well. Based on what they learned, they made changes that reduced the time lost and cost of replacing damaged hardware.
The drilling roadmap was used to communicate what was learned. It evolved as they worked to create a concise report documenting and transferring lessons learned as well as the usual information covered in such a report, such as what to expect in the rock ahead.
It also provided advice on the control settings and strategies based on what had been learned, and information related to the current drilling limiter—the focus of the drilling improvement effort.
The goal was to create a constantly updated document used by drillers, drill-site managers, and engineers to identify and record what they observed when drilling problems were encountered. It described the drilling characteristics of intervals ahead allowing drilling teams to focus on specific indicators related to the limiter.
Engineers played an important role of making “sense of all these piles of data we were getting,” helping plan changes for future wells.
“I think constant communication between the rig and the office is key to make sure all parties understand the dysfunctions occurring, or in the absence of dysfunction, opportunities to improve,” Giltner said.
The roadmap is updated after each well so lessons are documented for future reference. Occidental is looking for other ways to share what is learned. “We are working on other systems to efficiently share lessons learned and successful practices and designs across the global drilling community,” she said.
The paper reported on work done a year ago within a group of rigs that is still using wired pipe to go after remaining limiters, Giltner said. “We are targeting higher-hanging fruit,” She explained that, “We are getting away from avoiding failure and moving more toward optimization.”
The second of four JPT stories on drillers leading change.
Leading Drilling Change