As the pace of exploration and production activity accelerates and the cost of drilling, evaluating, and completing wells continues to rise in complex deepwater and unconventional plays, operators are seeking new logging-while-drilling (LWD) tools that offer real-time measurements comparable to proven wireline logging technologies. Obtaining continuous high-quality data during drilling operations can dramatically improve safety and reduce nonproductive time (NPT) by enhancing an understanding of geomechanical conditions and mitigating uncertainty in borehole stability.
Advanced LWD systems give engineers “eyes down the hole” long before they would normally deploy traditional logging tools. This enables the value of real-time decision making, reduces logging risks, and guarantees data acquisition in challenging wells.
In response to continued advances in LWD technology over the past decade, oil and gas companies are increasingly demanding access to robust real-time and recorded compressional and shear sonic data in both fast and slow formations. In costly deepwater wells, such data can enhance geomechanical models, improve wellbore stability monitoring and pore pressure prediction, and provide sonic-to-seismic tie-in, thereby minimizing drilling hazards and uncertainties in well placement and casing positioning. In high-tier horizontal wells in tight gas and unconventional shale plays, having reliable compressional and shear acoustic data while drilling can improve rock mechanics, fracture detection and characterization, perforation design, and hydraulic fracture optimization.
SonicScope Technology
To meet these growing industry needs, Schlumberger released the SonicScope multipole sonic-while-drilling technology (Fig. 1) as part of its suite of expert drilling and measurement services. This new LWD solution is unique in four ways.
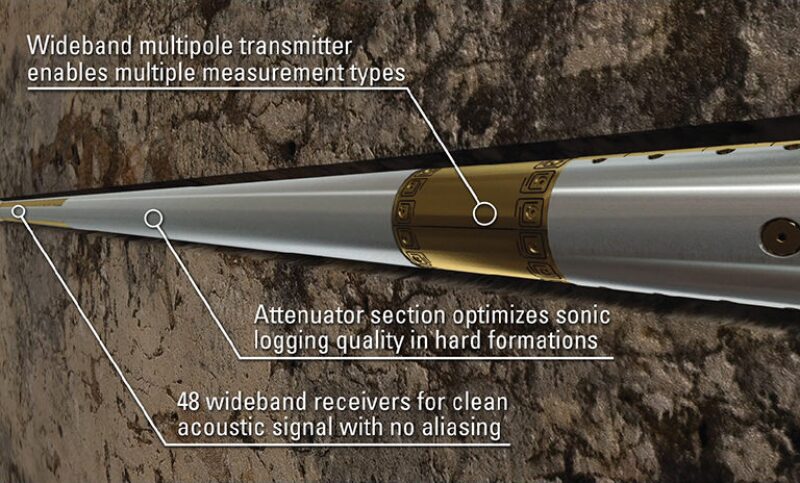
- Currently it is the industry’s only sonic-while-drilling solution that combines three distinct firing modes in a single tool (Fig. 2): low-frequency monopole for Stoneley acquisition, high-frequency monopole to extract compressional data in all formations and shear slowness data in fast formations, and wideband-frequency quadrupole to extract shear slowness data in slow formations.
- As the only tool that provides a dedicated module for the acquisition of Stoneley borehole wave forms while drilling, it provides high-quality acoustic data for fracture evaluation and fluid mobility analysis before washouts can develop.
- With more than 35 patents related to this technology, it incorporates innovative acoustic processing techniques for both downhole and surface algorithms, which were developed to compute reliable real-time compressional and shear data without prior knowledge of formation characteristics, and without affecting rate of penetration (ROP).
- The new sonic-while-drilling tool includes 48 receivers with the tightest interspacing in the industry (Fig. 3)—just 4 in. of separation between receivers. This arrangement provides superior acoustic sampling for reliable and robust measurements even in noisy environments.
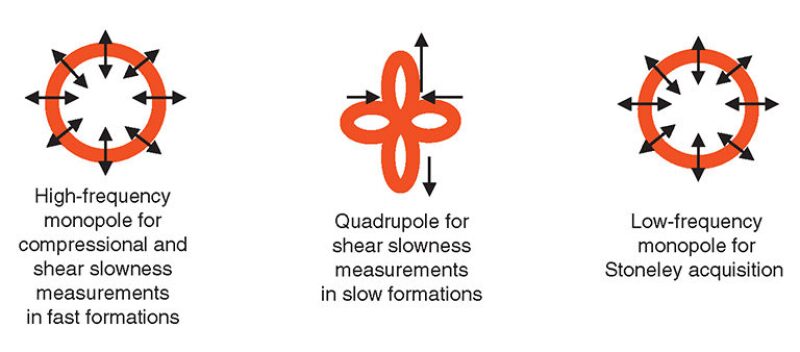
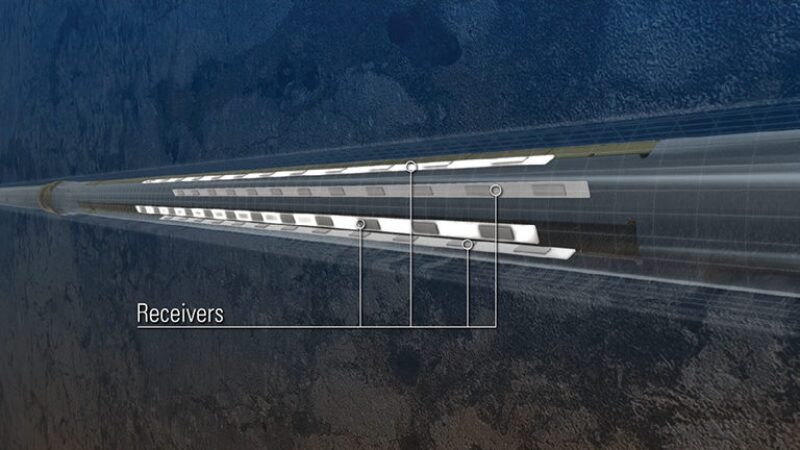
Development and Field Testing
Prior to development of multipole sonic-while-drilling technology, the physics of monopole LWD tools could only provide compressional and fast shear measurements in fast formations in which shear travel time or slowness (1/velocity) is greater than mud slowness. In slow formations, where shear slowness is lower than mud slowness, wireline sonic tools had to be run after drilling the well using dipole physics sensitive enough to measure slow shear. For LWD applications, a multipole tool that did not suffer the limitations of monopole physics had to be developed. Drawing on the acoustic structure and processing design of its proven wireline sonic scanning platform, Schlumberger developed new quadrupole technology using four different arrays set 90° apart.
The technology was tested on approximately 100 wells in a variety of drilling environments for many different operators around the world, initially in deepwater wells, then in tight gas reservoir shale plays and other challenging environments. Deploying multipole sonic while drilling in a wide range of settings with different technical objectives led to improved hardware and enhanced capabilities prior to commercialization, including the following:
- Addition of higher downhole computation power, providing real-time measurements at any logging speed while drilling, tripping, or washing down
- Incorporation of flexible downlink commands
- Development of self-diagnostics for automatic downhole recovery
- Ability to operate the system with or without battery, as required
- Addition of a standby mode accessible by downlink at any time, extending memory and battery life
Technical Description and Deployment
The new multipole sonic-while-drilling solution delivers robust and reliable compressional and shear slowness data in almost any environment without affecting logging speed. Extra downhole computation power made available in the commercial tool enables the use of advanced algorithms, which provide more complex processing and allow sonic acquisition while drilling, reaming, tripping in, or pulling out of the hole at up to 1,800 ft/hr.
Acquisition process. The new technology offers considerable acquisition flexibility. Sonic logging can be controlled through mud pulses or wired drillpipe, powered by a measurement-while-drilling (MWD) turbine, and runs with or without batteries. As a result, sonic while drilling is suitable for a variety of concurrent rig activities. Typically, an integrated MWD platform sends real-time fast formation compressional and shear slowness measurements to the surface using mud-pulse telemetry. Bit size and mud type are the only inputs necessary to create robust real-time logs from downhole processing; no prior knowledge of formation characteristics is needed and minimal human interaction is required. Full slowness time (ST) projection and pumps-off station measurements are sent to the surface to provide critical quality control data for pore pressure monitoring and wellbore stability evaluation. Where possible, deploying a remote connectivity and collaboration system allows engineers at any remote location to access real-time acoustic data for continuous monitoring and timely decision making. Multipole data is also recorded for further analysis and enhanced processing.
Transmitter, attenuator, and receivers. The tool includes four orthogonal broadband transmitters (Fig. 4) that can be driven independently to excite borehole monopole and quadrupole modes over a frequency band of 1 to 20 kHz. Transmitters are sensors that, with electric power, vibrate to create an output pressure, which generates sound waves with rich frequency content. To improve the signal while drilling, stacking is performed after exciting the borehole multiple times. In addition to high-frequency monopole, low-frequency Stoneley, and wideband-frequency multipole modes for compressional and shear slowness measurements regardless of mud type, the technology also provides a while-tripping, fast-logging mode for multipass analysis and top-of-cement detection.
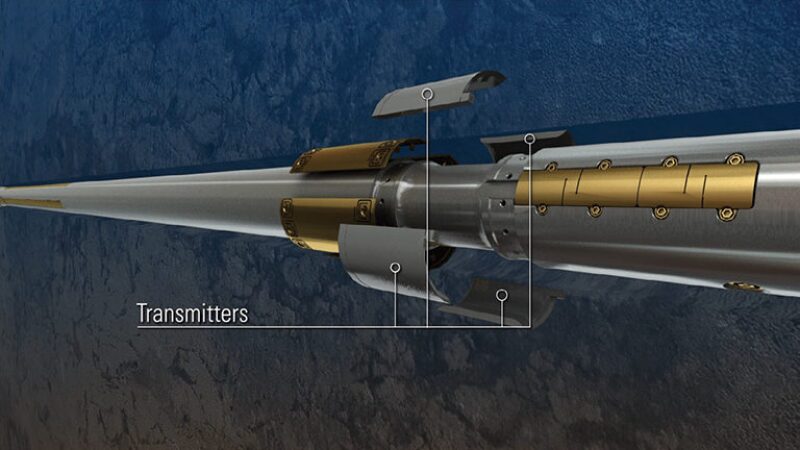
In fast formations, higher noise levels and propagation of acoustic waves through the tool itself—especially through a rigid drill collar—can make sonic LWD acquisition challenging. Therefore, the new system includes an optimized attenuator section that enables the removal of collar arrivals by a dedicated processing technique during real-time operations.
The multipole sonic-while-drilling tool also has four orthogonal receiver arrays with 12 receiver stations each. These 48 wideband receivers digitize high-quality waveforms directly at the sensors to produce an unperturbed acoustic signal. The 4-in. inter-receiver spacing prevents aliasing of any kind.
Two monopole modes. To extract compressional data in all formations and shear data in fast formations, the four transmitters excite the monopole mode at a high frequency equally in all directions. Waves propagate in the formation along the borehole, interacting at high frequency. After each individual excitation, the 48 receivers reconstruct the monopole propagation at each of the 12 stations and stack them to improve the signal-to-noise ratio. Then a slowness-time-coherence computation is made downhole. For each increment of time, different slopes, equivalent to different slownesses, are scanned to identify a coherent arrival, which is likely to represent consistent formation arrivals across the receiver array. All data on coherent arrivals is sent to the surface for real-time decision making.
To extract information about open, permeable fractures, the four transmitters excite the Stoneley monopole mode at a low frequency with the same pressure in all directions. Stoneley waves propagate along the borehole. When they encounter an open permeable fracture that crosses the well, they slow down and create an acoustic reflection from the fracture. When the receiver array passes by the open fracture, a chevron pattern appears in the waveforms (Fig. 5), which is analyzed with a forward modeling technique to provide information on the fracture.

Multipole mode. To extract shear data in slow formations, transmitters excite the quadrupole mode by reversing the polarity from quadrant to quadrant. Again, the waveforms recorded at the 48 receivers are combined to reconstruct the quadrupole propagation at each of the 12 stations, and are stacked after each borehole excitation. While drilling, the same acquisition sequence is performed at preprogrammed intervals. All data is recorded in downhole memory for further processing. Once the tool returns to the surface, the set of waveform data is recovered and, at each recorded depth, the frequency response is extracted and used to invert for the shear slowness value with a unique processing technique including the tool presence effects. The final shear value for each depth is combined with compressional slowness data to provide complete information for sonic formation evaluation.
Data quality compared with wireline. Advanced system design and new processing algorithms provide high-quality multipole data comparable to wireline sonic reference logs, even in highly damaged and unstable formations. In a fast formation, monopole compressional and shear data showed excellent agreement with wireline acoustic monopole measurements over a 1,000‑ft interval (Fig. 6). In a slow formation, monopole compressional and quadrupole shear slowness data also showed good agreement with wireline monopole compressional and dipole shear data over a 1,000-ft interval. This is quite remarkable because LWD and wireline logs are not recorded at the same time or under exactly the same borehole conditions. In addition, for Stoneley applications, the monopole Stoneley measurement has been extended to very low frequencies that were previously impossible to measure with monopole sonic-while-drilling technology.
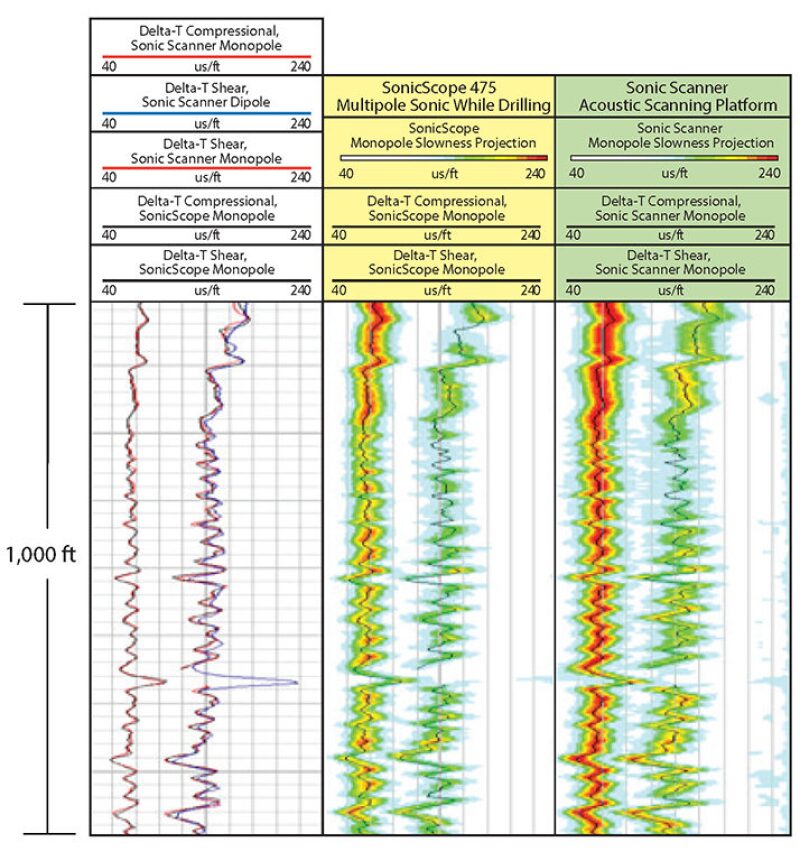
Applications and Case Studies
Multipole sonic-while-drilling technology has been used for a variety of different applications, plays, and technical objectives. In general, high-quality acoustic measurements have proven effective in reducing drilling risk and cost, developing more effective mud management programs, evaluating formations and characterizing reservoirs, ensuring accurate seismic positioning, and optimizing completion design to enhance production.
Formation evaluation. Applications of robust sonic-while-drilling data for formation evaluation include determination of the ratio of compressional to shear wave velocity (Vp/Vs) in any formation, quantitative assessment of rock mechanics, sanding analysis for completion and fracture design, and detection of hydrocarbons. In geological and geophysical applications, this data helps identify complex lithologies and provides porosity measurements without requiring a radioactive source. This is especially useful in carbonate reservoirs in which sonic-while-drilling data responds only to interconnected—rather than vuggy—porosity.
Deepwater wells. In costly deepwater wells, reliable compressional and shear data improves the understanding of complex geomechanical issues, real-time pore pressure monitoring, and wellbore stability surveillance. By providing geomechanical information independent of formation temperature and salinity that affect other methods, engineers can adjust mud weight properly to mitigate the risk of kicks and other drilling hazards. In addition, real-time measurements enable operators to minimize uncertainty related to seismic interpretation and casing positioning. For example, sonic-while-drilling data can be used to update the predrilling velocity-to-pressure transform. Combining sonic with formation pressure-while-drilling information can reduce uncertainty in a pore pressure prediction model. As a result, operators can significantly reduce well costs either by extending casing depths or possibly eliminating an entire casing section.
Unconventional plays. In unconventional plays—shales and tight gas reservoirs—shear sonic data enables operators to evaluate rock strength, while Stoneley data can detect fractures. The Stoneley borehole waveform is highly sensitive to fracture permeability and aperture. By inverting fracture aperture and fluid mobility using a forward modeling technique, it is possible to identify fracture locations and determine whether they are open, permeable, and capable of conducting flow. In water-based mud, Stoneley fracture analysis can be combined with high-resolution while-drilling image logs to completely describe the fracture network. Combining shear measurements with Stoneley, engineers can optimize packer placement for completions, and determine where the rock is more suitable for efficient hydraulic fracturing.
Fracture identification. Even in conventional plays, Stoneley fracture identification can prove critical in designing better completions. In one offshore region, for example, the operator needed to locate and seal fractures that were stealing hydrocarbons produced below them and preventing flow from otherwise productive wells.
Horizontal wellbores. Robust and reliable multipole sonic-while-drilling measurements are essential in any environment in which conventional wireline tools may be time consuming and difficult to deploy. One example would be highly deviated or horizontal wellbores or when the trajectory or stability of the hole makes it unwise or technically impossible.
Case study 1: Unconventional play. During field testing of the new technology, an operator drilling a horizontal well in a tight formation decided to acquire high-quality compressional and shear data to assist in identifying the sweet spot while drilling, and to optimize the hydraulic fracture completion design. Robust, real-time data provided both sonic porosity and geomechanics information during drilling operations. By correlating sonic while drilling with advanced bed boundary imaging, the operator was able to clearly define and stay within the zone of highest reservoir quality while mitigating shock and vibration, thus improving the ROP by 20% and maximizing ultimate productivity.
Case study 2: Offshore development. OMV Petrom of Romania began producing from fields in the Black Sea in 1987. However, the company had been unable to achieve more than about 115 BOEPD per well in the low-permeability carbonate shelf formations found there. In 2009 and 2010, Petrom deployed the new multipole sonic-while-drilling system along with advanced directional drilling tools, complementary LWD technologies, and multistage hydraulic fracturing in two new horizontal wells with longer drain sections than before.
The first wellbore was approximately 4,600 ft long. Stoneley waveforms and other acoustic measurements enabled the operator to isolate open, permeable fractures and larger-scale faults, select appropriate fracturing stages, and identify optimal packer positioning for hydraulic fracture completions. As a result, production increased to a peak of more than 1,000 BOEPD before stabilizing at levels up to 750 BOEPD per well, achieving enormous gains in value for the high-cost offshore environment.
Current and Future Plans
Following the commercialization of the 8¼-in. multipole sonic-while-drilling tool for large boreholes, the industry now has the service available in hole sizes ranging from 10½-in. to 17½-in, together with the already commercial 4¾-in. tool that can be used in hole sizes of 5⅝-in. to 8-in. Further development and field testing of multipole sonic-while-drilling tools are currently under way for the full range of hole sizes. Having the same advanced alternatives for all hole sizes will meet additional industry needs, both in unconventional plays and in shallower sections of offshore and deepwater wells, in which challenging geomechanical issues often occur.
The future deployment of different hole sizes also comes in parallel with the more advanced answer products, such as cement evaluation, that are necessary industrywide.