“We’re going to the Moon, and we’re going there to stay this time,” has become a NASA mantra as the US competes with other countries, including China and Russia (https://jpt.spe.org/esa-roscosmos-to-mine-oxygen-water-from-moon-rocks-as-nasa-eyes-first-artemis-lunar-mission), to be the first to put humans on the Moon and Mars. The race will rely heavily on using resources available on the planetary bodies—or in-situ resource utilization (ISRU). Chief among these is water, which has been called “the oil of space.”
As NASA prepares for Artemis mission astronauts to land on the Moon in 2024, it will fly at least two preliminary missions to look for water and gather information about the lunar south pole. The Polar Resources Ice-Mining Experiment (PRIME-1) and Volatiles Investigating Polar Exploration Rover (VIPER) missions, which will be launched in late 2022 and 2023, respectively, will be the first missions to study ISRU on another celestial body. They will also mark the first time NASA will robotically sample and analyze for ice from below the surface. And they will use technologies transferred and adapted from oil and gas exploration.
Reconnaissance Missions
Data from nearly 3 decades of lunar orbiter and impactor missions suggest that the Moon’s soils, particularly at its south pole and other regions, could contain hundreds of millions of gallons of water that could eventually be harvested and converted to oxygen, fuel, or drinkable water for human use on the Moon, Mars, and beyond. But, at what concentrations? In what kinds of soils? And is the water in a form that’s accessible?
Most of the information we have about the presence of water-ice on the Moon comes from orbital measurements. The only direct evidence acquired to date came in 2009 from a sensing satellite aboard a spacecraft that was purposely crashed in the Cabeus crater. The material ejected as a result of the impact was analyzed with a spectrometer to reveal the presence of 5.6%±2.9% water-ice by mass. The form, distribution, composition, and quantity of the water-ice remain largely uncertain. The only way to reduce this uncertainty is to obtain ground-truth data by drilling exploratory boreholes in the crater. This will be the purpose of the PRIME-1 and VIPER missions.
PRIME-1 will last a week to 10 days, during which a robot will deploy a drill and mass spectrometer to harvest and preliminarily evaluate moon-ice for quality and regional heights and to determine how much of the ice is lost to a process known as sublimation, wherein the water transforms directly from solid ice into vapor, rather than first going through a liquid phase. In addition to ice, PRIME-1 will gather samples including rock samples to help date the sequence of impact events on the Moon, core tube samples to capture ancient solar wind trapped in regolith layers (unconsolidated, inorganic rocky material), and paired samples of material to characterize the presence of volatiles and to assess geotechnical differences between materials inside and outside permanent shadows. The samples will be returned to Earth and studied to characterize and document the regional geology, including the small, permanently shadowed regions. The data from the mission will help scientists understand how a mobile robot to be used on the subsequent VIPER mission can search for water at the Moon’s pole, and how much water may be available to use as NASA plans to establish a sustainable human presence on the Moon by the end of the decade (Fig. 1).
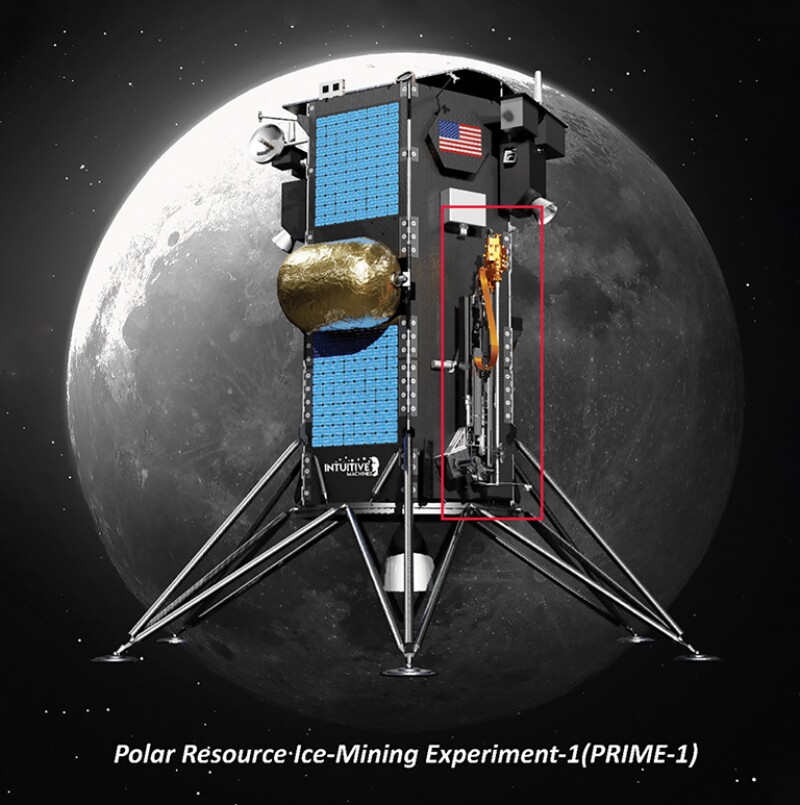
The mission has been compared to collecting core samples in oil and gas exploration.
“PRIME-1 will provide ground-truth for the presence of water and other volatiles up to 3 ft below the surface at a lunar landing site. The insights we gain from drilling where data suggests we may find water will help to validate what we have learned by studying the Moon from orbit as well as inform resource-location models we plan to use on future robotic and eventually crewed missions,” said Jacqueline Quinn, civil and environmental engineer, MSolo Payload PM/PRIME-1 PM.
The VIPER mission at the end of 2022 will last up to 100 days. Its rover, a robotic vehicle about the size of a golf cart, will roam several miles, sampling various layers of regolith and digging up cuttings from those environments to get a close-up view of the location and concentration of water-ice that could eventually be harvested to sustain human life over extended stays. The physical state of the water found will help tell scientists about its origin and history, as well as what is needed to extract it.
Water is considered a “volatile,” meaning it readily evaporates at only moderately warm temperatures. This makes it easier to access in the lunar regolith than nonvolatiles and increases its probability of being extracted for use. The Moon also holds other volatiles such as hydrogen, ammonia, and carbon dioxide, that could serve as resources for human endeavors.
With the data it collects about the amount of water in various environments, VIPER will create resource maps using a process similar to how natural-resource mapping is done on Earth and will rely on the US Geological Survey to help determine locations where water and potentially other accessible materials could be harvested to sustain humans over extended stays.
Drilling in the Lunar Environment
The VIPER mission will mark the first time since the Apollo missions that drilling has been done on the Moon and will be a first for drilling robotically to this depth on another world.
The Regolith and Ice Drill for Exploring New Terrain (TRIDENT) which will be used for both the PRIME-1 and VIPER missions is rotary-percussive, meaning it both spins to cut into the ground and hammers to cut the hard material into fragments for more energy-efficient drilling. According to Honeybee Robotics, which is developing and will supply TRIDENT, it has been specifically designed for early space prospecting efforts to capture and evaluate volatile species, including water, from cryogenic solids located within the top meter of lunar regolith.
Kris Zacny, Honeybee Robotics’ vice president of exploration systems and senior research scientist, who began his career as a petroleum drilling engineer, explained that TRIDENT is being developed using fundamental drilling engineering principles adapted for the lunar environment (Fig. 2).
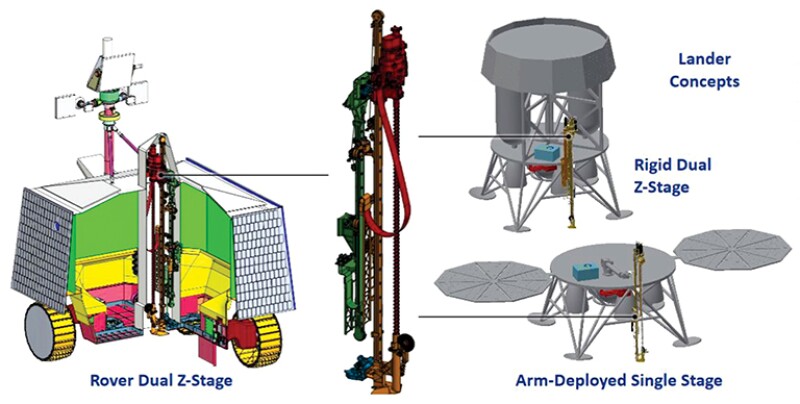
“One thing we learned from the Apollo missions is that the Moon’s regolith is extremely compact,” said Zacny. To drill into this on Earth and into ice as hard as rock, we would typically look at hammer drills, but operations on the Moon must accommodate extremes of both heat and cold and will take place in a vacuum,” said Zacny. “Many traditional hammer drills use the Earth’s atmospheric air for expansion, compression, and percussion. We can’t apply that to the Moon,” he continued. The Moon’s gravity is approximately one-sixth that of Earth, making drilling forces an issue.
Zacny compared the design of the TRIDENT drill to that of a corkscrew used to open bottles of wine. “Instead of pushing down on a bottle opener, we are applying rotation force to drill downward, which reduces weight-on-bit forces,” he explained.
The drill bit at the tip of the long drillstring has carbide cutting teeth. These are harder than steel to maintain their sharpness and are like the cutters on precision drilling or cutting equipment. The tip also carries a temperature sensor to take readings below the surface. Along the length of the drillstring are flutes that transport drill cuttings to surface when the drill is spinning. A rotating brush sweeps the soil sample off the drill and into a chute, forming a neat pile on the ground where the next set of instruments can analyze it.
The drill uses a “bite” sampling approach that captures samples in approximately 10-cm intervals from a depth of up to 1 m and then transfers them to an oven, where the water will bake off and be captured for further use. This allows determination of water content as a function of depth, which is important data for future mining efforts.
“In addition to being a tool for providing samples, TRIDENT is an instrument,” Zacny said. The drill’s integrated 40-W heater and real-time distributed temperature (RTD) sensors will measure downhole temperature and could provide thermal conductivity. These two measurements are needed to determine heat-flow properties of the Moon. The first RTD is in the drill bit and the second is co-located with the heater, approximately 20 cm above the bit.
The drill’s power and penetration rate are used to determine regolith strength. Measuring the strength in combination with input from three mass spectrometers—the mass spectrometer observing lunar operations (MSolo), the neutron spectrometer system (NSS), and the near-infrared volatiles spectrometer system (NIRVSS)—determines the volatile composition and mineralogy of the material. The spectrometers will enable determination of the physical state of the ice, including whether it is mixed with regolith or cemented with regolith grains. The former will lead to low drilling power and the latter to high drilling power, even if water-ice concentration is the same.
TRIDENT will also be able to provide bearing capacity of the top lunar surface from measuring the sinkage of its footpad into the surface, as well as angle of repose from measuring the angle of the cuttings pile.
According to Zacny, TRIDENT’s downhole heater and temperature sensors will pave the way for more advanced downhole technologies that could be developed for future missions. “For example, integrating the NSS and NIRVSS into the auger would change the paradigm of planetary exploration. Instead of bringing a sample to an instrument, we would be bringing an instrument to a sample,” Zacny said.
Learning More, Faster
NASA expects the PRIME-1 mission to begin drilling and gathering information within its first 24 hours of landing on the Moon in late 2022. A year later, when VIPER arrives on the Moon, the MSolo spectrometer will assess gases in the environment after touchdown to understand which ones are truly coming from the lunar surface and which are being introduced by the lander. Once the rover begins operations, MSolo will work in tandem with NIRVSS to evaluate drill cuttings for water-ice and other volatiles.
The NIRVSS spectrometer will be able to tell the nature of the hydrogen in the lunar soil initially detected by the NSS instrument. That hydrogen could belong to water molecules, hydroxyl, or it could exist simply as hydrogen atoms. Any of these forms could be a useful resource for making rocket fuel. NIRVSS will also detect the different types of minerals and ices that might be present in the lunar soil, including frozen carbon dioxide, ammonia, and methane.
Thanks to the Moon’s proximity to Earth, command and control of the VIPER rover will be flexible and near real time. Compared to Mars, where the time from sending a command to seeing the results ranges from 10 to 20 minutes, VIPER’s latency will be 6 to 10 seconds.
Optimizing Operations
The Moon’s environmental conditions and operational limitations create unique operational challenges for lunar drilling missions. Under a NASA early-stage innovation grant, a pattern-recognition algorithm was developed at the Colorado School of Mines to assist the upcoming lunar missions by using the drilling data collected during these missions to characterize subsurface properties in real time. The algorithm development process has been described in earlier SPE papers. At the 2021 SPE/IADC Drilling Conference in March, the authors presented a new paper (SPE 204108) describing an optimization module that works in tandem with the “lunar material characterization while drilling” algorithm to find the optimum rate of penetration and rev/min that will help make operations safer and more reliable while minimizing power consumption. The authors contend that integration of the optimization module to a control system might help deliver closed-loop drilling systems for common day-to-day operations as well as extraterrestrial drilling systems to add value and stability.
In the meantime, Honeybee Robotics has developed a real-time drilling optimization algorithm specifically for the TRIDENT drill and its bit. According to Zacny, the algorithm will prevent getting stuck, reduce the energy required to drill, and optimize operations based on the energy being used.
“Many of the fundamental principles that apply to drilling and mining on Earth also apply to drilling on the Moon and other planetary bodies,” said Zacny. “Rock is rock, wherever it is; you can’t argue with it.”
For Further Reading
SPE/IADC 204108 Evaluating Data-Driven Techniques to Optimize Drilling on the Moon by D. Joshi, A. Eustes, J. Rostami et al., Colorado School of Mines https://doi.org/10.2118/204108-MS
SPE 195803 How Can Drilling Engineers Help Revolutionize Space Transport and Colonize the Solar System: Focusing on Lunar Water-Ice by D. Joshi, A. Eustes, J. Rostami, et al., Colorado School of Mines https://doi.org/10.2118/195803-MS
Challenges and Methods of Drilling on the Moon and Mars IEEE Aerospace Conference Proceedings 2011, by K. Zacny, G. Paulsen, and M. Szczesiak, Honeybee Robotics https://doi.ieeecomputersociety.org/10.1109/AERO.2011.5747261
TRIDENT Drill for VIPER and PRIME1 Missions to the Moon 52nd Lunar and Planetary Science Conference 2021 (LPI Contrib. No. 2548) by K. Zacny, P. Chu1, V. Vendiola et al., Honeybee Robotics https://www.hou.usra.edu/meetings/lpsc2021/pdf/2400.pdf