With the availability of operational magnetic-flux-leakage (MFL) -measurement devices, operators are now able to see many previously undetectable coiled-tubing (CT) defects as they occur and advance. CT operators can now understand the circumstances that caused these defects, the conditions that worsen them, and the methods that can prevent their progress. This work will present an object-oriented tracking system that allows CT operators to monitor defects as they evolve over time.
Introduction
For many years, an integral part of pipe management has been nondestructive-evaluation (NDE) inspections of CT strings. These inspections exist to complement the use of theoretical-fatigue-life (TFL) tracking and mitigation of pipe failures. It is possible to track fatigue, imperfections, and anomalies during the job. These data should be used to optimize pipe management further in field locations. Despite its availability, the practice of conducting real-time NDE by use of MFL principles during job execution has been quite rare. Because NDE tools are becoming increasingly robust and reliable, this technology can now be used at the wellsite during CT jobs and thus data can be analyzed in real time. Sites in Alaska, for instance, run NDE devices in CT-drilling operations, and implement the findings into their pipe-management practices.
Object-Oriented Tracking System
CT damage can occur by many mechanisms, the most common of which is mechanical damage caused by surface equipment. Reactive or erosive fluids can wash out the coil internally, corrosion can occur during storage, and material abrasion can be experienced as the CT moves across the production tubing. Finally, fatigue occurs every time the CT passes off the reel and over the gooseneck. Of all these mechanisms, the only one with an operational tracking system in place is fatigue. However, with continuous MFL monitoring, the operator can see these additional damages clearly. In tracking these damages, one can determine their type and can characterize, quantify, and even repair them.
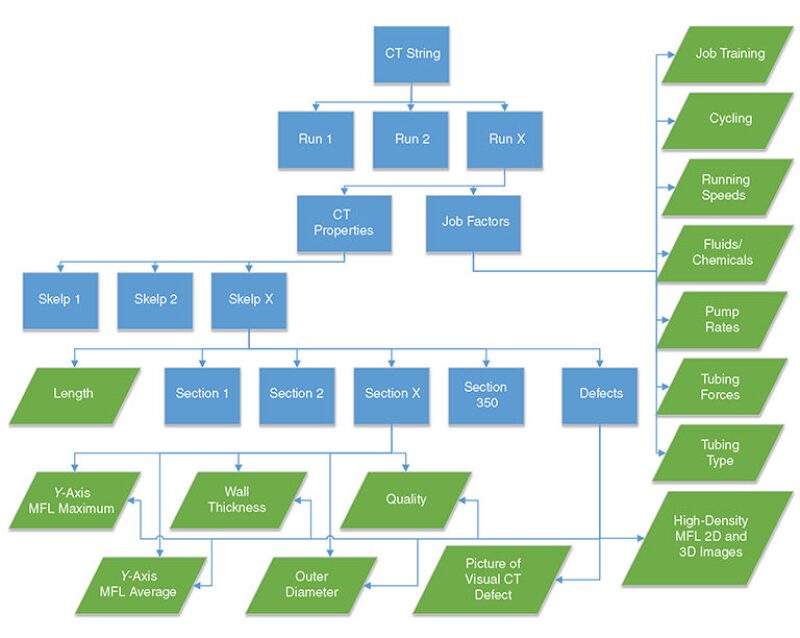
The philosophy of an object-oriented tracking system (Fig. 1 above) is to divide the lengthy CT and its damages into a definite number of sections, and to track each section individually. Isolated flaws are tracked in the same manner. The damage can then be observed as it progresses, and pipe-management decisions can be made on the basis of these observations.
There are several challenges associated with this system. First, understanding which section of the CT is being measured is impossible with simple depth control. The CT is in a constant state of change as it is elongated and trimmed throughout its life. In the manufacturing process, the CT begins as a flat steel strip, also known as a skelp. The edges of these skelps are sheared at a fixed angle and then welded together before being milled into a tube; these welds are known as bias welds. The developed system uses the bias welds to separate the CT into sections—its skelps. Once the skelps can be identified, each can be separated into a certain number of equal sections so as to acquire a direct comparison and can be tracked on that basis. This way, the same piece of CT metal is being compared on every run, regardless of the depth at which it crosses the gooseneck. These sections are referred to here as “objects,” and parameters such as wall thickness, outer diameter, ovality, and MFL response are tracked for each object.
Second, certain defects are difficult to quantify with typical CT parameters: wall thickness, outer diameter, and ovality, for example. Metallurgical anomalies such as bias welds may not display a change in wall thickness at all. Fortunately, almost all of these anomalies exhibit an MFL response, and with the corresponding high-density MFL images, these can be characterized. Once their physical position on the coil can be ascertained, these anomalies can be tracked as individual objects as well by correlation with the location of the bias welds.
The final challenge is to magnify this tracking system. While it is easy to characterize the damage and defects in a particular CT string in a single run, adjusting a fieldwide pipe-management strategy requires a streamlined tracking system.
Bias-Weld Correlation
Bias welds are used in the manufacturing process of a CT string. Bias welds have a very recognizable MFL signature because of their fixed 45° angle, so these can be observed on almost every run. As long as the distance between bias welds can be tracked, then the MFL data can be correlated to each skelp and tracked positively regardless of changes in the CT. In this way, the system is able to isolate a single defect even if its apparent position moves by thousands of feet. The defect-tracking system therefore records each defect and the properties of each definite section of pipe, identified by a percentage of the distance along a particular skelp.
Defect Tracking
Many defects can be discovered throughout the entirety of a lengthy CT string. Many defects, mainly in larger pipes, cannot be tolerated because of the high stress concentration and will lead to failure in a short period of time, bringing losses and reputation issues. These defects can be tracked and identified by their MFL signature. A particular signal that will be identified from the beginning is a bias weld. Bearing in mind the length of the CT string, there could be several bias welds present. Knowing the location of each bias weld will confirm the current location of additional imperfections on the CT.
Though defects can be formed during manufacture, many are formed because of operational job factors. Taking this into account, the systematic defect-tracking system includes these factors for each run into a well—in other words, per job the CT string performs. The job factors tracked for each run include well name, wellbore-tubing type, job type, fluids pumped during the job, and start and end time. The well name is tracked so that the operator can correlate each run to a particular well. The well name corresponds with a well schematic and directional survey that includes the type of wellbore the CT string has encountered. It is important to know how deviated the wellbore is, or will be in the case of drilling, in order to gain knowledge of ever-changing CT fatigue.
Other important characteristics tracked by this system include the amount of CT trimmed, when it was trimmed, and the runs that correspond with each CT string length. Knowledge of where each imperfection and anomaly should be located on the CT string is vital in monitoring their progressions. The tracking system has a built-in calculation that predicts where each defect is currently located while executing continual operations. This includes each bias weld and all monitored defects. With this addition, the operator will notice an anomaly and can confirm whether it is new or pre-existing, monitoring all types easily.
When an anomaly is observed, it is tracked in the object-oriented system also. This portion of the system tracks characteristics pertaining to the anomaly itself. First, the run number is tracked in order to determine when the defect was first seen and when it was seen thereafter. This run number also correlates to the well name, job type, and fluids pumped, all of which must be understood when monitoring an imperfection in the CT. The depth of the anomaly when first noticed is tracked, which enables calculation of its current depth as the CT continues to perform jobs.
The spooling direction of the CT when the anomaly is detected is tracked also. This enables the operator to further determine the root causes of the defects. Furthermore, the high-density MFL images relate to the spooling direction and can be analyzed to characterize each imperfection. The MFL reading of the anomaly is one of the more important factors tracked by this system. The reading is the maximum MFL amplitude given off by the imperfection at the time it is seen. Monitoring this reading over time will allow the operator to determine the intensity of the defect and its effect on the CT string’s lifespan.
Finally, the inclusion of pump rate in the tracking system is significant for several reasons. Tracking pump rate will also enable the operator to determine the root causes of the anomaly. Moreover, the pump rate and corresponding circulating pressure seen by the CT can affect the overall characteristics of the coil—namely, the wall thickness, outer diameter, and ovality. The effects that the pump rate has on these characteristics need to be monitored to determine the root causes further, and to make conclusive decisions on the specific results of the anomaly when detected. All of these characteristics are monitored further in the material-parameter tracking to make defined overall decisions regarding the defects themselves, and regarding the CT string as a whole.
Material-Parameter Tracking
Certain parameters of critical importance to pipe integrity must be tracked across the coil. For instance, a CT string could be slowly washing out internally without the operator’s knowledge and without creating any isolated defects. This is why the object-oriented tracking system monitors these parameters across the length of each skelp. Changes can be correlated to certain job parameters, and solutions can be created on the basis of the data.
In Alaska, the tracking system’s first application was a 2⅜-in. wireline-enabled CT string. This string was used for an outstanding 51 runs without failure while having its integrity constantly monitored. In this case, the skelps were divided into 350 sections. Although more than 1,500 ft of coil was trimmed throughout the life of the string and approximately 155 ft of CT elongation was experienced, the MFL tool was able to identify the bias welds well enough to correlate the data against the skelps. The only way to compare material directly between runs is to correlate the skelps from the bias welds and normalize their lengths.
In comparing all runs, the small variations can be explained by the different circulating pressures experienced during the job; however, the outer diameter was well within specifications throughout the string’s life.
There was a sharp decrease seen in wall thickness at the end of the string’s life. This is believed to be the result of a combination of corrosion and erosion from fluids pumped during operations; the outer diameter did not suffer such a decrease. Most pinholes that occur in Alaska CT-drilling operations are the result of internal washouts from the corrosive drilling mud.
It is important to note that the tiny features in wall-thickness and outer--diameter variation were consistent across the majority of the runs, despite the fact that this skelp elongated approximately 3% and lost more than 1,500 ft from the downhole end (from trimming pipe). This is a testament to the accuracy of the MFL tool used and the quality of the analytical methods applied. Having a consistent wall-thickness measurement could allow the CT-drilling operator to catch these pinholes before they occur. This was never possible before, because wall-thickness assessment was realistically only possible with point ultrasonic measurements.
This article, written by JPT Technology Editor Chris Carpenter, contains highlights of paper SPE 168303, “Optimizing Pipe Management With a New Approach to Coiled-Tubing-Integrity Monitoring,” by Michelle Torregrossa, SPE, Liam Zsolt, SPE, and Mirjam Zwanenburg, SPE, Schlumberger, prepared for the 2014 SPE/ICoTA Coiled Tubing and Well Intervention Conference and Exhibition, The Woodlands, Texas, USA, 25–26 March. The paper has not been peer reviewed.