The authors’ objective is to provide robust completion strategies for the Middle East’s high-pressure/high-temperature (HP/HT) gas wells, focusing on well-testing operations that require extreme solutions for solids separation, fluid recovery, sour service, and efficient well cleanup. This study evaluates flowback operations across various well-cleanup scenarios. It introduces a cleanup and flowback-testing approach incorporating advanced solids separation technology, portability, equipment automation, improved metallurgy, and enhanced operational safety standards.
Description of Current System
Emergency Shutdown Valve (ESD). The fluid mixture from both the wellbore and reservoir flows into the production tubing, proceeding through the production wellhead’s flow wing valve and subsequently through a 10,000-psig ESD valve. Mounted atop the flow wing valve, the ESD valve is hydraulically actuated and protects the downstream facility infrastructure.
Sand Management System (SMS). The SMS effectively segregates solid particles from the production fluids and consists of two primary modules: the desander vessel (primary stage) and the wellhead filter (secondary stage) (Fig.
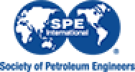