Well cement is placed into the annulus between casing and formation to provide structural support and zonal isolation throughout the well life cycle. Nevertheless, operators in the North Sea have been concerned about the ability of the cement sheath to maintain sealing integrity because of the increasing number of reported failures in mature wells. A new laboratory setup is designed to allow visualization of the development of possible leak paths throughout the cement sheath when exposed to pressure- and temperature-related varying loads.
Experimental Setup
The new laboratory setup presented in this work allows pressurization while maintaining the capability to perform a detailed study of the creation and propagation of cement-sheath failures upon thermal cyclic loads.
The cell is shown in Fig. 1 (above).
The applied formation materials were Saltwash North sandstone and Mancos shale.
Some of the current features of the cell are specified as follows:
- Cell is X-ray transparent.
- Temperature is controlled (from inside the casing) during cement setting and cyclic tests.
- There is independent control of pressure inside casing on cement and confining pressure (around the rock) during cement setting and cyclic tests.
- Maximum pressure is set at approximately 35 bar, while the allowable temperature range is set between −1°C and 150°C.
- All components of the cell can be reused for several test samples.
In particular, the X-ray transparency is important because it allows for visualization of leak paths without the need to release pressure from the cell, or remove the internal test sample for a computed-tomography (CT) scan, or perform the traditional invasive method of cutting the test sample cross section.
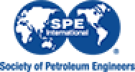