Accidental detonation of a perforating gun at surface can have catastrophic consequences. To decrease risks, layers of procedural controls have been implemented to reduce the inadvertent application of power caused by human error, stray voltage, or the presence of radio frequency (RF) energy. Explosives handling procedures and controls, such as locking out the firing panel and acquisition system, are used to mitigate the human error risk.
Mitigating RF risks requires establishing RF-free exclusion zones, with all RF transmissions shut down. Exclusion zones are effective, but adhering to them relies on strict procedural controls. With increased industry and personal reliance on RF transmitters, such as cellular phones, RF silence is becoming more difficult to achieve. Although RF-immune initiators were introduced more than 20 years ago to allow wellsite operations to continue without RF silence imposed, their complex initiation technologies require high power levels, which improve the safety margin to stray voltage but significantly reduce overall system reliability.
Perforating has always been a hands-on operation that relies on supervisor experience. Over the last decade, perforating reliability has continued to improve as service companies and operators have implemented detailed training programs, procedural checklists, and advanced hardware. However, these reliability improvements have begun to plateau, acting as an impetus to develop new perforating systems that would be more effective than procedural controls in addressing the main causes of perforating misruns: damaged or improper wiring, mechanical seal failures, and initiator malfunctions.
Plug-In Design With Built-In Safety
With a focus on resolving these issues, Schlumberger developed the Tempo instrumented docking perforating gun system—the industry’s first perforating system that fully integrates a plug-in gun with real-time advanced downhole measurements for monitoring and confirming operations to mitigate risk while increasing safety, reliability, and efficiency (Fig. 1 above). Created for all environments, the system uses modularized initiators combined with RF filtering mechanisms and an addressable switch to provide an enhanced level of safety to operations.
Proprietary docking components are the key element of the gun system’s plug-in design. They streamline assembly and eliminate the major cause of perforating misfires: technique-sensitive crimping and wiring. The initiator can be plugged into a perforating gun by using simple mechanical and electrical connections without requiring complicated assembly. The new system eliminates all complex field wiring connections and crimping, which simplifies the arming process that has a direct impact on both wellsite efficiency and reliability.
The new system incorporates an addressable switch with circuits as redundant protection barriers to eliminate any single-point failures. RF filtering mechanisms in the design cover a wide range of RF sources, including those typical to oilfield wellsites on both land and offshore. The combination of an addressable switch, multiple protection barriers and filtering makes it possible to arm the guns in advance of operations at the wellsite, off the critical path for perforating operations. The design’s electrostatic discharge protection is tested to 25 kV, stray voltage rating to 40 V, and no-fire voltage to 600 V. Bringing these design features together mitigates all the major causes of unintentional detonations.
With its engineered controls, the gun system provides the highest level of safety in compliance with API RP 67 Group 2 specifications. RF protection has been verified by an independent third-party organization. As a result, RF silence requirements are eliminated in almost all use cases, and both single and selective guns can be armed in advance of wellsite operations, which erases the rig time associated with arming for conventional gun systems. Regardless of when arming is conducted, it takes significantly less time than conventional systems to further improve operational safety and efficiency.
The gun design is streamlined with compact firing heads and adapters and fewer seals. This reduces the overall assembly length to maximize the usable gun string length and the explosive load that can be deployed. The firing heads and adapters are not only designed to reduce length but also to eliminate arming ports, which are a major contributor to seal failures and leak paths. Approximately 1 ft of assembly length is saved for each selective gun in a string compared with conventional systems, which provides a major benefit in increasing the explosive payload while keeping gun string lengths within operational boundaries. Additionally, the number of seals has been reduced from nine to five for a single gun with a savings of two additional seals for each selective gun.
Performance Confirmed by Measurement Capabilities
The advanced perforating measurements capability of the new gun system delivers a complete suite of real-time, simultaneously acquired data that are critical for verifying and optimizing perforating design and execution. Incorporation of this ruggedized measurement technology in the gun string is new to the industry, obtaining pressure, temperature, casing collar locator, and gamma ray before, during, and after perforating without the need for a shock absorber in the compact design (Fig. 2).
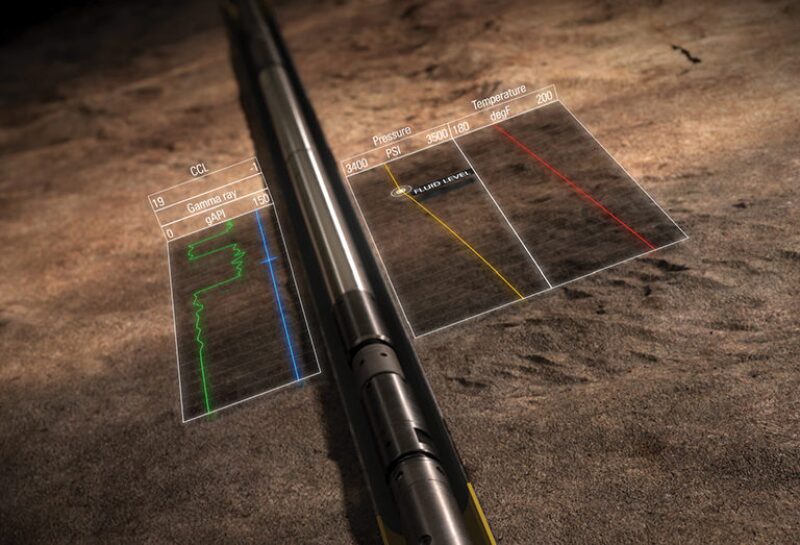
For dynamic underbalance perforating, postperforating treatment, and propellant treatments, the system measures the dynamic pressure and peak shock for each gun fired and transmits the data within seconds after firing each gun. These data enable validation and effectiveness of productivity treatments as well as gun shock modeling to optimize future operations.
Case Studies
Perforating a well poses numerous operational and safety risks. By integrating a plug-in gun design with an RF-protected initiator and real-time advanced downhole measurements, the new system effectively delivers major improvements in efficiency, reliability, and wellsite safety in addition to providing certainty by monitoring the well’s dynamic underbalance while creating clean perforations that boost reservoir productivity.
In Egypt, an operator employed the system to improve the efficiency of multizone perforating operations in deep wells in the Western Desert. When conventional perforating gun systems were used, significant operational time was required to assemble and arm the guns, and the integrity of the armed systems could not always be verified until they were conveyed to perforating depth. In these deep land wells, any connection failures that could not be diagnosed until the guns were at depth caused lengthy downtime to remedy. In addition, retrieving live guns posed safety risks to personnel.
The system both streamlined deployment and supported operational safety. The compact system enables running up to 40 guns for selective initiation to efficiently perforate multiple reservoir zones with a maximized explosives payload in a single trip. The plug-in design simplifies the arming process to increase safety and reliability by eliminating the variability introduced by the wellsite crimping and wiring necessary for conventional systems. Onboard diagnostics check the system’s integrity at surface, and a confirmation check can then be conducted once the guns are at least 200 ft below ground level instead of requiring the perforating guns to be at target depth.
The operator completed 11 perforating runs, with two selective runs. The plug-in design delivered considerable time savings, including reducing arming time by more than half and providing RF protection that allowed simultaneous wellsite operations.