In the realm of enabling technologies, multiphase flow modeling has proven to be one of the most important to the oil and gas industry. Without it, nearly all subsea wells would be too costly or dangerous to develop. While working to fine-tune its offshore capabilities, developers are also busy expanding the technology’s application areas to include shale field development, hydrate remediation, and heavy oil extraction.
In the 1960s, when the industry began studying how to model multiphase flow, which is the science of how liquid and gas interact inside wellbores and pipelines, little was known about the complex physics involved. Back then, an engineer’s ability to predict flow behavior was strictly limited to what could be observed at the wellhead.
Over the years, the industry invented devices that could accurately calculate flow rates, velocities, and volume fractions, along with downhole temperatures and pressures. Armed with these tools, engineers and scientists had the measurements they needed to marry computational science and fluid dynamics. More than anything else, this advancement is what has allowed offshore operators to extend their reach beyond the shallow-water fields and into those thousands of feet deep.
“What we have done is to make it possible for the industry to live with the complex multiphase flow problems that face them on a daily basis,” said James Brill, a multiphase flow expert who recently retired as a research professor of petroleum engineering at the University of Tulsa. “When the industry first moved offshore, they were afraid to go with multiphase flow pipelines because they did not know what was happening inside of them, or what kind of facilities they would have to have at the outlet end in order to handle the fluctuating rivals of gas and liquid.”
In lieu of a complete understanding of multiphase flow, Mack Shippen, a product champion for one of Schlumberger’s top multiphase modeling programs, said early offshore explorers were forced to make conservative design decisions when building a production platform.
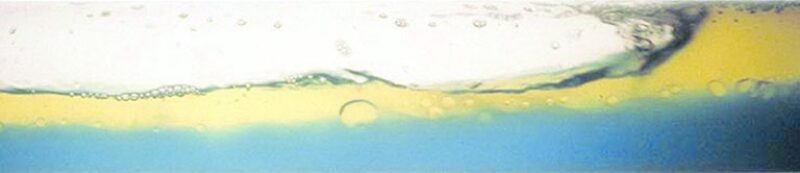
That meant using larger than needed processing equipment and pipelines to compensate for what they did not know about the behavior of the multiphase flow. “So yes, you had a safe design but you did not have one that in today’s world would be economic,” he said, explaining that, “if it is overdesigned, then essentially money has been wasted on equipment that is more than what is necessary.” If an operator can reduce the diameter of a subsea pipeline by just 1 in. or 2 in., “the difference can be on the scale of millions of dollars in capital investment,” he said.
On the other hand, Shippen, who is also involved in the scientific research of multiphase flow with universities in the United States and the United Kingdom, said there have been offshore projects where companies selected separation equipment, pumps, and compressors that were undersized, which prevented them from realizing the field’s potential production volume and value.
Modeling the Shale Revolution
One of the new directions for multiphase flow modeling appears to be into the prolific shale fields of Texas, North Dakota, and beyond. With this technology, producers could better manage their shale fields that are developed at a much faster pace than conventional reservoirs. In the US, tens of thousands of new shale wells have been brought on line each of the past few years.
A downside of the shale operators’ continuous efforts to reduce the time it takes to drill and complete the wells, is that it has in many cases outpaced their transportation network’s ability to move the product. Oftentimes, when a well comes on stream, the pressure from it and neighboring wells can be too much for the pipeline network to handle.
“If you are bringing on newer, stronger wells, then you may have to choke those back to allow the older wells to produce,” which can prevent the field’s overall production from increasing, Shippen said.
With Schlumberger’s steady-state multiphase flow simulator, Pipesim, Shippen said operators are able to identify the pipeline bottlenecks on a computer screen and then relieve them by using a precise calculation that shows how much production needs to be choked back from new wells. This allows the operator to ensure the optimization of production throughout the production network.
Steady-state models produce a snapshot in time of a proposed or operating production system based on different design scenarios. The technology enables companies to plan for the life of a field before they invest much capital and then manage it once it is online.
“When operators are looking at designing production systems, and this includes the well itself and essentially the entire flow path from the reservoir, they need to be designed to ensure the production system is able to deliver what the reservoir is capable of producing,” explained Shippen.
In many shale fields, operators control only the wells and not the transportation network, which is often why pipeline capacity increases at a slower rate than production growth. So Shippen suggested that steady-state modeling could be used between the operator and a midstream company to accurately predict the future line needs of the field before the bottlenecks form.
Many unconventional shale oil wells must go on pump a year or so after first production and steady-state modeling can be used for these events as well. Schlumberger has developed Pipesim to allow producers to compare the wellbore hydraulics of different artificial lift systems and determine the one likely to offer the best performance for a particular well, which may sometimes include multiple options.
“We are seeing cases where different lift systems are used at different points in the life of a well,” Shippen said. “For example, you may use an electrical submersible pump (ESP) that can be operated with a variable speed drive for a certain range of production, and when the production declines to the lower end of that range, oftentimes that ESP is replaced with a rod pump.”
The Mother of Flow Assurance
The non-Newtonian phenomena involved in multiphase flow can render many people in the industry a bit glassy-eyed. And even for petroleum engineers, well-versed in advanced mathematics, multiphase flow modeling can be a bit of a mystery. “Much of it is beyond the scope of what you can teach in an undergraduate class in petroleum engineering. It is too complicated,” said James Brill, a recently retired research professor from the University of Tulsa.
Nevertheless, as younger engineers are tasked with managing complex oil and gas fields reaching deeper into the cold oceans and involving the tying together of multiple wellstreams into a single pipeline, he believes it is more important than ever that they have a greater understanding of the theories and technologies in use today.
Brill and a former graduate student-turned-professor at the University of Kuwait are trying to simplify the topic for the next crop of undergraduate engineering students with a new textbook on multiphase flow and flow assurance in oil and gas production. The book is being published by SPE and will debut at the Annual Technical Conference and Exhibition in Houston in September.
Borrowing a phrase from a colleague at Chevron, Brill said he wants production engineers to realize that “multiphase flow is the mother science of flow assurance. You really cannot address the flow assurance issue unless you have a pretty good knowledge of how multiphase flow works in pipes.”
Plenty of Room for Improvement
One area for general improvement with the modeling and simulation of large unconventional developments involves the behavior of fluids entering the wellstream. Brill said that many current models he has worked with are “not that good” when it comes to predicting production in unconventional wells. Part of the problem is that for most of the 50-year history of multiphase flow modeling technology, when it comes to wellbores, developers have focused largely on vertical and directional holes.
While fluid behavior in a conventional vertical well has been understood and studied for some time, unconventional wells and their long lateral sections present different conditions that have not been scrutinized for nearly as long. As liquid and gas enter a lateral section, which are a mile or more in length in many cases, the temperature can remain about the same while the flow rates increase with each perforated section from the toe of the well to the heel.
Once the liquids and gases reach the vertical section, Brill explained, they begin to behave as they would in a conventional well, where temperatures and pressures begin to drop as fluids make their way to the surface. Tying this series of events together is what researchers still need time to perfect. “We know what has to be done, but you have to have some experimental data to know that the models are working properly,” Brill said, adding that, “We are not there yet.”
On the other side of the spectrum is heavy oil. The issue with modeling the production of this type of crude is that the process is so different from conventional light oil production. Heavy oil wells involve smaller volumetric flow rates, higher pressure drops, and different flow patterns because of the high viscosity, and a significantly more difficult separation process.
“You use the models developed for lighter oils and try to get them to work on heavy oils and it does not take long before you realize that there are some significant problems involved,” Brill said. “The flow patterns look different, there is less gas trapped in liquid slugs, and the fluids are what we quite often call non-Newtonian in behavior.”
The upside for developers to invest their time and money in heavy oil modeling is the large amount of reserves found all over the world. When reliable modeling technology is developed for heavy oil, Brill said it would be a very welcomed development for its producers.
New Kid on the Modeling Block
Before he founded his startup multiphase flow modeling company, Pipe Fractional Flow, Anand Nagoo teamed up with his professors at the University of Texas at Austin to build from the ground up an entirely new multiphase flow model. The program, which shares the name of the company PipeFractionalFlow, began as a research project more than 7 years ago when Nagoo was an undergraduate student studying simple-to-compute analytical multiphase flow principles that could connect and unify past and current observations. The program is in the final stages of being commercialized and will be available later this year for use by companies.
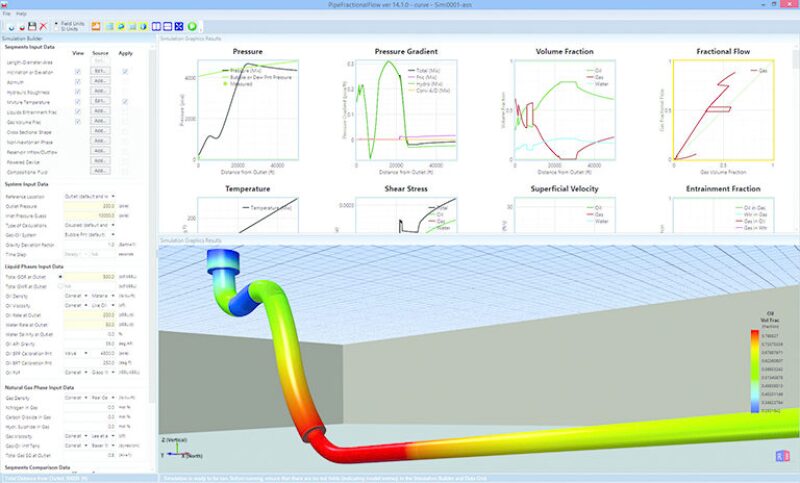
His quest to develop a new multiphase flow theory began with the analytical fractional flow theory used in reservoir modeling, based largely on basic laws of physics. Applying this highly tested theory to a pipe made perfect sense to Nagoo. “The media does not matter, what matters is the conservation laws that you are imposing on the media,” he said. “The conservation of mass, momentum, and energy.”
Nagoo then set out on a research mission to study the multiphase flow theories produced by various industries including mining, chemical, nuclear power, geothermal, aerospace, and of course, petroleum production. After forming a theory, Nagoo said he validated it against published control experiments from these industries. The outcome of the effort is the world’s largest searchable database of published data relating to multiphase flow modeling, which he named Anna.
Unlike previous work in multiphase flow modeling, Nagoo said his development efforts focused on how to simplify and connect the forces and concepts involved with flow vs. breaking each apart, which complicates the existing models. “What we were doing differently was we were looking not at the individual specific problems, such as bubble flow or stratified flow,” he said. “We were looking at the interrelationships between phenomena, the connectivity between different things.”
The resulting body of work, he said, represents the first unified analytical and mathematical theory of multiphase flow. Called pipe fractional flow theory, Nagoo said it has been tested and validated using recent data and data dating back to the 1940s.
A special application area for PipeFractionalFlow involves well planning for horizontal wells. Nagoo believes his program will be the first of its kind to enable companies to make informed decisions on wellbore trajectory for shale drilling. He said one of the biggest problems with other multiphase flow models is their inability to tell a driller or a petroleum engineer what degree of inclination or declination should be for the horizontal section of an unconventional well, otherwise known as drilling toe-up or toe-down.
What is missing in the most popularly used models, he said, is the accountability for the role that frictional pressure and volume fraction play in a horizontal well section that trends downward. Nagoo said he compared his model with others and then used empirical evidence from the field, industry reports, and published lab data to confirm his finding that his model worked better in this regard.
“It just takes a very slight downward decline for the gas to be held up and a very sharp change in your volume fraction gradient, and therefore, your pressure gradient,” he said. “A slightly inclined phenomena in multiphase flow directly impacts the production capability of horizontal wells in the real world via the sole effect of inclination.”
The modeling program has found that under certain conditions it only takes 0.2° to 0.5° of sloping in a horizontal well to alter the holdup behavior of fluids and create a choke point, Nagoo said. He noted that the key to solving this problem will be getting oil and gas companies to open up the lines of communication between the various disciplines of unconventional field development and integrate more modeling into well design to improve well performance.
“How you decide to drill your wells has a profound effect on the rest of the events that are to follow, namely, completions and production, and then artificial lift down the road,” he said. “That is not how we as industry work now; we are compartmentalized and partitioned.”
Hydrates are Hard
At the Colorado School of Mines, researchers are in the early stages of developing a new multiphase flow modeling specifically designed to understand the effect of the formation of gas hydrates on multiphase flow in production lines. Hydrates are essentially bits of frozen water that contain light gases such as methane, ethane, propane, or carbon dioxide. They not only constrain flow; if they build up too much, they put a pipeline at risk of rupturing.
“[Hydrate formation] is the main issue that all offshore companies deal with on a daily basis, but as they go into even harsher environments, it will of course be more prominent,” said Amadeu Sum, an associate professor and the leader of this research project. “If you are going to live with hydrates, you need to know how they are forming, where they are, how much you have, and how they are affecting the flow,” he said.
To live with the problem thus far the industry has developed numerous technologies to remediate hydrate formation inside flowlines and pipelines, such as pipe insulation and expensive hydrate-inhibiting chemicals. But Sum said that there has been less emphasis placed on developing models to figure out the nature of hydrate formation, which happens in nearly all subsea flowlines and places onshore such as Alaska, where much of the production comes from north of the Arctic Circle. The simple reason hydrate modeling has not been a major focus for multiphase modeling research because it is very complex and hard to do.
Sum compared hydrate modeling with modeling sand in pipes, which has been successfully done, to illustrate why it is so difficult. “Hydrates are quite different from sand, especially in terms of the density and in that hydrates aggregate, whereas sand will just either remain dispersed in the fluid or depending on the flow rate, settle,” he said. In other words, where sand can flow through a production system or form small deposits, hydrates can form and accumulate at a much higher and, therefore, dangerous rate.
To take the research further, Sum said he is working to establish a first-of-its-kind experimental laboratory that can test his team’s multiphase flow and hydrate models at the same time. He said he knows of no lab in the world that currently can do both in the same experiment. The current research is partially funded by a hydrate consortium at the Colorado School of Mines; Sum said more funding will be needed to continue the progress. Details of the research project will be presented at the Offshore Technology Conference in Houston in May.