This paper presents an overview of the challenges of using traditional synthesis gas reforming methods for efficient gas-to-liquids (GTL) conversion. A second objective is to show how newly emerging reformer technologies, such as those based on plasma or catalytic partial oxidation, will provide significant improvements. A case also will be made for how these new technologies, when paired with a high-efficiency Fischer-Tropsch (FT) process, provide a profitable alternative to the environmentally damaging, and wasteful, practice of flaring or venting associated gas.
Introduction
Given the limitations of footprint, weight, safety, cost, and other factors for platform operations, the use of the FT process for flared-gas conversion to liquids is challenging. This study shows that the best process uses a catalytic partial-oxidation reformer, a unique wax-free FT catalyst, and an advanced FT reactor to meet all platform criteria while cutting traditional capital expenditures (Capex) and operational expenditures (Opex) in half.
Criteria for Platform Operations
The following criteria were considered for the selection of equipment on a platform:
- Small footprint (space limitations)
- Low weight (weight limitations)
- Low pressure (safety considerations)
- High gas hourly space velocity (GHSV) (to enable small reactors)
- Low pressure drop at high GHSV (reactor shape)
- High gas conversion (process efficiency)
- High gas selectivity to carbon monoxide (process efficiency)
- No water needed (simplicity)
- No pure oxygen needed (platform requirement for safety)
- No feed-gas preheat needed (simplicity)
- No reformer tail-gas heat exchanger needed (simplicity)
At the heart of the list are footprint, weight, and safety.
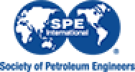