When discussing dual-gradient drilling, there is an important distinction between controlling wells and well control.
Controlling wells requires maintaining the balance between preventing influxes that could lead to trouble and exceeding the limit that could push drilling fluids out of the well and into the formation. Well control refers to the hardware, procedures, and training associated with dealing with situations in which an influx has occurred and needs to be quickly stopped before it grows into a bigger problem, and then circulated out of the well.
For companies seeking to win approval from the US Bureau of Safety and Environmental Enforcement (BSEE) to drill the first deepwater well in the US Gulf of Mexico using dual-gradient drilling, questions about well control are critical. Offshore regulators want to be sure that all the new equipment has been thoroughly tested because this is a new way to drill, and the BSEE wants to be sure that it is understood that when it comes to well control, the requirements are not changing.
Chevron and Statoil have been working through a detailed testing program to identify and remedy any potential problems, and they have prepared their crews to safely operate the system and properly respond to any situation.
“The challenge we see at BSEE is that training is huge. It is a whole new way of looking at and thinking about” drilling, said Lance Labiche, chief of BSEE district operations support for the Gulf of Mexico Outer Continental Shelf Region. “When it comes to well control, there are some significant changes with certain systems.”
The dual-gradient designs may improve well control. Flow-measurement capabilities in these closed systems are able to offer earlier warnings than traditional systems as well as quicker ways to apply pressure downhole to stanch an influx. But drillers have had to learn to distinguish between an early warning and normal variations in fluid volumes.
Chevron’s full dual-gradient method should allow heavier mud weights below the seabed, creating a fluid able to halt a well from flowing after the pumps go off, even if the drilling rig is accidentally disconnected from the well.
At that point, the meaning of the phrase restoring full riser margin becomes apparent. The mud column from seabed to bottom of the well has sufficient density of its own to prevent the well from flowing, serving as an effective primary well control barrier. In a conventional well, the mud weight used must be lighter to allow for the added pressure from the riser.
Statoil is adding flow controls to the EC-Drill system that it plans to use to drill the first deepwater well in a high-pressure environment in the Gulf of Mexico. It has added a unit with two shutoff valves, which can be used during pipe connections to maintain the pressure without having to fill the riser to increase pressure, and a second able to close quicker than a BOP in case a rig pump fails, halting circulation and causing an abrupt pressure drop.
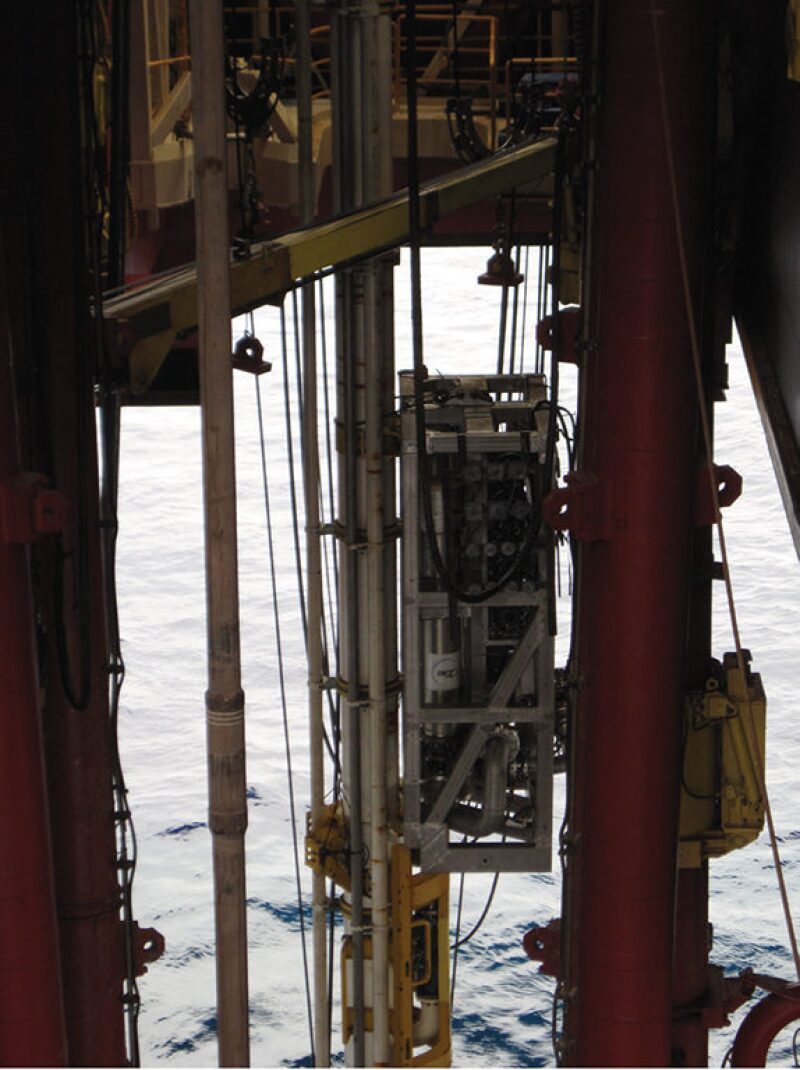
Both valves would block the annular space between the drillpipe and the casing. Their role sounds similar to the job of the annular rams in a BOP. But Statoil officials emphasize these quicker-moving closing devices are not elements of the well control system.
Dual-Gradient Drilling is: “Two or more pressure gradients within selected well sections to manage the well pressure profile.”Conventionally, the Primary Well Barrier is a “single gradient” mud form wellbore to “bell nipple” and this drilling mud exerts a pressure on the formation that is above pore pressure. In “dual gradient” the fluid column is not “uniform”; the fluid column has “two or more” different densities. So, if one is air or gas as in EC-Drill, the mud weight must be heavier if the pressure at the bottom shall be the same. Thereby the “pressure gradient” is altered. Similarly, seawater in the riser is typically much lighter than the drilling mud used in deep water. Roger Stave |
Well control is done by the BOP, which must be closed when there is an indication of a kick. No party seeking to drill using dual gradient in the Gulf of Mexico is saying otherwise. It is a critical point because US regulators make it clear they do not want accumulations of hydrocarbons, particularly natural gas, in the riser. The limit is no more than the small volumes that can flow into the well when pumps are shut off briefly for operations, such as connecting pipes.
When asked during the panel discussion at the Offshore Technology Conference (OTC) if that rule might change if managed-pressure systems were added offshore, Labiche of BSEE said, “We do not see that changing any time soon. As long as we are using a traditional drilling riser, we do not want gas in the riser.”
If gas does appear, standard operating procedures apply. Those include closing off the riser using the annular rams in the BOP, adding mud to increase the pressure and stop the influx, and bleeding off any gas though the choke line.
Managing Differently
The question about gas in risers was raised because the capabilities of managed-pressure systems have inspired some users to reconsider the common wisdom on how to deal with an influx from the formation. They can detect changes in fluid volume of 1 bbl or less, which would never be observed using a conventional system measuring fluid returns on the tanks on a floating rig.
In Brazil, Petrobras has agreed with regulators that when an influx exceeds 2 bbl, it will begin using traditional well control procedures on its deepwater rigs with managed-pressure drilling, said Jose Umberto Arnaud Borges, offshore well project manager exploratory well construction at Petrobras.
An influx would typically need to be about 10 times that large before it would be apparent to crew members on a platform using a system measuring fluid levels in a return tank on a rig in active seas, said Don Hannegan, a strategic manager in drilling hazard mitigation technology development at Weatherford.
The increased awareness of small changes, and the ability to quickly apply backpressure to stop them, is leading some to say there is a better way to react to what managed pressure industry standards refer to as flow anomalies. One of the most vigorous advocates for change is Robert Ziegler, who is head of deepwater drilling technology at Petronas, one of the most active managed-pressure drilling users offshore. The company also drilled a dual-gradient well in deep water, and used its pressure-management capabilities while cementing the casing.
Ziegler advocates using quick detection of relatively small volume influxes. He advocates using the managed-pressure system to quickly add backpressure to stop the influx, and then circulating hydrocarbons from the influx out normally using the separator that removes oil and gas from drilling mud.
This method breaks from the standard procedure for reacting to kicks, which is to shut down the mud pumps to stop the fluid from moving, and then shutting the annulars in the BOP. While that does keep the influx in place, when fluid stops moving the pressure it exerts on the formation drops because it loses the force exerted by friction as it rises in the hole—the equivalent circulation density—at a moment when greater pressure is needed. This reduction of several hundred psi increases the flow rate, he said.
Shutting in the BOP will eventually increase the pressure and stop the inflow, but it takes nearly a minute to close the annular rams in conventional systems, which are not good at accurately detecting small influxes. The initial loss of pressure when the pumps are shut down can allow an influx to grow significantly. “A 5-bbl kick turns into a 60-bbl kick,” Ziegler said, adding that the current standard procedure “is the worst thing you can do” if you need to minimize an influx. He adds that when the fluid stops flowing, it allows gas to be concentrated in a small area, rather than being spread out over a longer distance in a low-density stream that can be removed using standard processing.
The approach is in line with the managed-pressure guidelines from the International Association of Drilling Contractors, Ziegler said. But as managed-pressure systems move into deep water drilling they are undergoing scrutiny.
One of the presentations at OTC discussed the value of using “dynamic control,” which uses managed-pressure hardware to quickly detect and limit an influx and then flow it out at a pace that allows any hydrocarbons to be safely removed. “The benefits added by managed-pressure drilling are not fully understood,” said Oscar Gabaldon, operations manager at Blade Energy Partners who presented the paper. “With small influxes it is safer to circulate them out.”
Based on Ziegler’s research and experience with offshore managed-pressure drilling, an influx from a deepwater well rises slowly through drill mud, if it rises at all, and disperses as it does, making it easier to manage using available equipment.
Operators are researching whether well control should be handled differently using managed-pressure equipment. A recent joint industry project (JIP)—The Controlled Mud Pressure JIP—investigated the ability of the EC-Drill systems to detect small kicks, and also observed how simulated kicks using nitrogen move up a riser, said Roger Stave, senior technology adviser at Enhanced Drilling.
Results are not final, but Stave said the system did show the system could detect influxes of less than a barrel in 10 to 20 seconds. In contrast, in a conventional well, he said it can take several minutes to detect, and only be noticed when there is an increase of 20 bbl or more of fluid in the fluid return tanks.
Given the ability of managed-pressure systems to quickly detect and act on influxes too small to be observed in conventional systems, Stave sees merit in Ziegler’s call for a change in thinking on circulating out kicks. But he recognizes this will take time. “Everyone wants to take it a step at a time and become comfortable where they are,” he said.
US offshore regulators have asked the industry to improve its ability to detect influxes of fluids and gases, which may provide an early warning of a kick that can become a blowout.
The hardware used to manage pressure could be added to help address this concern, said Hannegan of Weatherford. He was involved in developing a kick-detection system that can be quickly installed with minimal rig modification. It would divert fluid returns using a rotating control device within the marine diverter, measured with a Coriolis meter, and the measurements would be adjusted to remove the rising and falling of the sea on a floating rig. That total, when compared with the volume of fluid flowing into the well, could detect relatively small influxes that may be a kick.
“My opinion, based on bits and pieces here and there, is that probably by next year BSEE will be encouraging operators, as they issue permits to drill, to show what form of early kick-loss detection they are using,” he said.