The careful planning and successful execution of a multistage-fracture-stimulation completion in one of the first horizontal wells (KZN-F) drilled in the Amin formation in north central Oman instigated a step change in initial production rate and long-term deliverability from this tight-gas-sandstone reservoir. The operator and service company worked as a team, modeling the fracturing program after North American practices.
Introduction
Most of the natural gas in the Amin formation is locked up in low-permeability, extremely hard sandstone formations in very deep reservoirs. Drilling times of 3 to 4 months are typical for vertical wells, and fracture stimulation is necessary.
BP acquired the concession from the Sultanate of Oman in 2007 to engage in an appraisal of the block (shown in Fig. 1). Following appraisal, a full field-development license may be granted to develop the block. The objective of the appraisal project is to evaluate the delivery potential of gaseous hydrocarbons from four reservoirs: Barik, Miqrat, Amin, and Buah. There were two wells drilled by BP that tested the Amin formation in the field before this investigation. The KZN-C well was stimulated with a conventional crosslinked-gel fracture treatment, and the KZN-E Amin well was stimulated by use of a hybrid technique. The only other fracturing technique that had not yet been introduced to the Amin formation was a high-rate water fracture (HRWF), also known as a slickwater fracture. This technology, widely used in North America, had originally been planned for use in the Amin reservoir and had already been used successfully in the Miqrat reservoir.
Pumping and chemical costs are lower for an HRWF than for crosslinked-gel fracture treatments.

Challenges and Solutions
Zone Selection. Six target intervals were selected for flow testing in the KZN-F well, with the goal of evaluating the efficacy of different reservoir-access and stimulation technologies, as well as determining which formation conditions would contribute to flow. These intervals were identified by use of a combination of mud logs, conventional openhole logging, and a microimaging log. Gamma-ray, resistivity, and porosity logs were used to differentiate zones in the Amin reservoir that might present more-promising targets. The microimaging log proved to be valuable for identifying fractures in the reservoir that could be targeted for stimulation. Fractures were categorized as faults, natural fractures (cemented or uncemented), or drilling-induced fractures on the basis of their appearance on the log. Fig. 2 illustrates some of the data available from the microimaging log used to target key wellbore objectives.
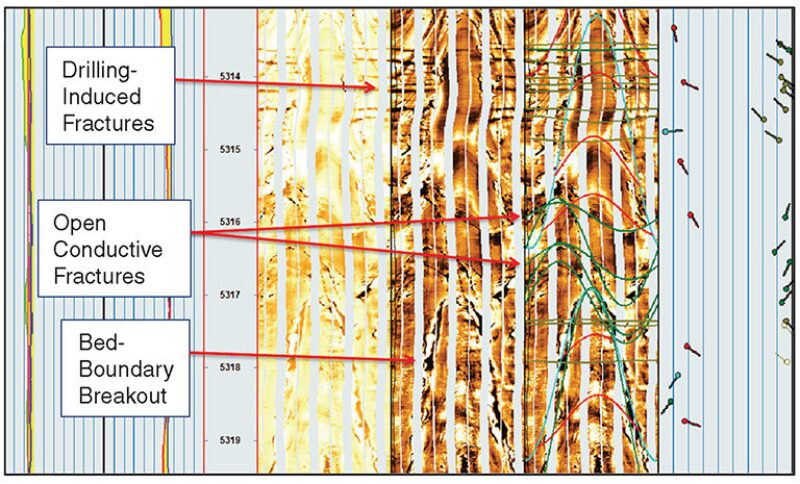
Reservoir Access for Stimulation. The liner was cemented in place with five fracture sleeves preinstalled to provide multiple access points for possible stimulation. These were conventional fracture sleeves designed to be operated in either uncemented or cemented completions using a ball to shift the sleeve to an open position for stimulation. However, in this case, a backup method for operation was used, implementing a shifting tool, run on coiled tubing (CT), to activate the ports. These sleeves were placed in approximate positions in the liner to target zones with increased evidence of fracturing. Overall, three reservoir-access technologies were planned for this well: sliding sleeve, explosive-jet (shaped-charge) perforating, and abrasive-jet perforating.
Fracture Interference. One of the objectives in drilling a horizontal well, especially in low-permeability reservoirs, is to facilitate conducting multiple transverse-fracture stimulations along the lateral section. However, each fracture may be subject to fracture interference.
In the KZN-F well, because there were other considerations used to select the perforations, perforation clusters were spaced in a single fracture interval between 27 and 53 m apart, depending on the interest of the zone. The overall interval of each fracture stage was approximately 100 m, simulating typical North American operations.
At every fracture interval planned with multiple sets of perforations, HRWF treatments were executed successfully. The actual perforation set that does eventually fracture within a given fracture interval may be influenced strongly by reservoir quality at that particular depth (e.g., by the stress or fracture gradient at different perforation clusters within a given interval). This tends to support the theory that multiple sets of fractures are unlikely in a fracture interval if that length is less than the fracture height.
Wellbore Access. Both CT and electric-line-tractor technologies were evaluated in the KZN-FH2 well after considering which options for achieving wellbore access were practically and financially feasible.
CT intervention is already well-known as a robust method of conducting intervention operations. This method holds advantages such as rapid mobilization and rig up/rig down, live-well intervention, and the ability to perform nearly all intervention services except real-time electric logging. The disadvantages of this method are depth accuracy, which is especially important during the appraisal phase of a project, and high daily costs.
Electric-line tractors use two to six drive sections, operated by electrical power from the surface, to move the tractor into the wellbore. Perforating, logging, and setting bridge plugs can be performed with an electric-line tractor while being monitored from the surface. This method has the advantage of excellent depth correlation, but it has limited ability to put significant force downhole, and it is also very expensive. The electric-line-tractor method was shown to have the best ability to perforate and set plugs at the preferred depth, but leftover fracture sand in the tubulars caused several major delays during the operation. In electric-line-tractor operation, the cause of the problem is the downhole force limitation of the tool.
Zone Isolation. There are two conventional methods that industry adopts in a cemented-liner completion in a horizontal well to achieve zone isolation: sand plugs and bridge plugs. In North America, the most common method used today for isolation in cemented completions is bridge plugs run with pump-down guns. A bridge-plug method for zone isolation was planned for KZN-F to avoid intervention delays while running the electric-line-tractor. Six bridge plugs were set inside the wellbore. All of them demonstrated the ability to withstand fracturing pressures during operation. Apart from six that set perfectly, two more bridge plugs were not run successfully. One bridge plug was set while running in the hole, which required a milling operation. A second plug was accidentally set in the riser before running in the hole. Analysis of that event determined that the tension on the gripper elements was too low, which probably contributed to setting the first bridge plug accidentally.
Depth Accuracy. Compared with CT, an electric-line tractor offers much better control of depth accuracy. The operator can perforate, log, or place bridge plugs with excellent accuracy with a tractor. Furthermore, a tractor-set bridge plug provides excellent depth correlation for CT operations. If the bridge plug can be placed using electric-line measurement, the CT can tag that plug with reasonable accuracy. This was demonstrated in the abrasive-jet perforations in Stage 4, which were on depth within 0.5 m on the basis of the known depth of the previously tractor-set bridge plug.
Technology-Comparison Results
In North America, evaluating the optimum system to use by a trial-and-error approach would involve trialing technologies in several wells. However, to shorten this process, several comparisons were made in KZN‑F, which included fracturing technique, proppant treatment volume, and reservoir-access technique.
Fracturing Technique. To maximize the stimulation treatment, a technique that would maximize fracture half-length, but would attempt to limit the height growth, would be optimal for this formation. The potential for uncontrolled height growth would most likely accompany a conventional crosslinked-gel fracture treatment, so a hybrid fracturing technique or an HRWF has appeal. A hybrid fracture, in this application, refers to the use of a linear pad stage, whereas the proppant-carrier fluid is a fully crosslinked polymer gel. An HRWF refers to treatment using water and friction reducer; proppant-carrying capacity highly depends on the pumping rate and is not considered to be a significant contributor to flow conductivity.
There were six fracture treatments performed along the horizontal wellbore: one using a crosslink-gel fracture (Stage 1), one using a hybrid technique (Stage 5), and the rest using HRWF technology (Stages 2 through 4 and Stage 6). From a production standpoint, the HRWFs performed significantly better than the crosslinked-gel fractures, producing 12 MMscf/D vs. 0.5 MMscf/D.
Treatment Volume. Measuring proppant volume per net pay zone could give an indication of fracture conductivity. In the KZN-FH2 horizontal well, which has the same formation properties along the majority of the horizontal wellbore, sensitivity to proppant volume can be compared between Stage 2 and Stage 3 fractures. Stage 2 was treated with 287,600 lbm of proppant, while Stage 3 received 196,600 lbm of proppant. Both were stimulated with an HRWF technique. Following a commingled-flow test, multiphase production logging showed that there was no additional production achieved by using larger proppant mass. Stage 3 did have many more clusters of natural fractures to target, as well as the interval with 50 bbl of mud lost while drilling. Furthermore, Stage 6 produced approximately the same gas rate as Stage 2 despite having zero proppant used throughout the job.
Reservoir-Access/Perforation Technique. Three different access or perforation techniques were compared in KZN-FH2: cemented fracture sleeves, explosive-jet perforating, and abrasive-jet perforating. Explosive-jet perforating demonstrated superiority to cemented fracture sleeves when Stage 1 and Stage 3 were compared. Assuming the same magnitude of tortuosity per stage, Stage 1 had a total near-wellbore (NWB) friction pressure of 2,400 psi at 36.5 bbl/min after acid-wash treatment. This compares with Stage 3, which had total NWB friction pressure of 2,200 psi at 64.5 bbl/min after shooting only four sets of perforations, demonstrating a 28-bbl/min increase in injection rate at the same NWB friction pressure.
Stage 3 and Stage 4 were intended to compare explosive-jet and abrasive-jet perforation techniques. Both of the stages used four sets of perforations. There might be a slight advantage with abrasive jetting, in that it is more likely to cut a slot or elongated oval shape instead of a hole. In any event, Stage 4 measured NWB friction pressure of 2,250 psi at 73.2 bbl/min, which is approximately the same NWB friction pressure value as Stage 3, but with a further 9-bbl/min increase in rate. Depth control was much better for Stage 4 because the nozzle was landed on a bridge plug set just below the target interval by an electric-line tractor.
This article, written by JPT Technology Editor Chris Carpenter, contains highlights of paper SPE 164008, “Adopting North American, Multistage Fracturing and Horizontal Completion Technologies Starts To Unlock the Amin Tight Gas Formation in the Sultanate of Oman,” by Robert Clark, SPE, BP, and Kevin Mullen, SPE, and Stevanus Kurniadi, Schlumberger, prepared for the 2013 SPE Middle East Unconventional Gas Conference and Exhibition, Muscat, Oman, 28–30 January. The paper has not been peer reviewed.